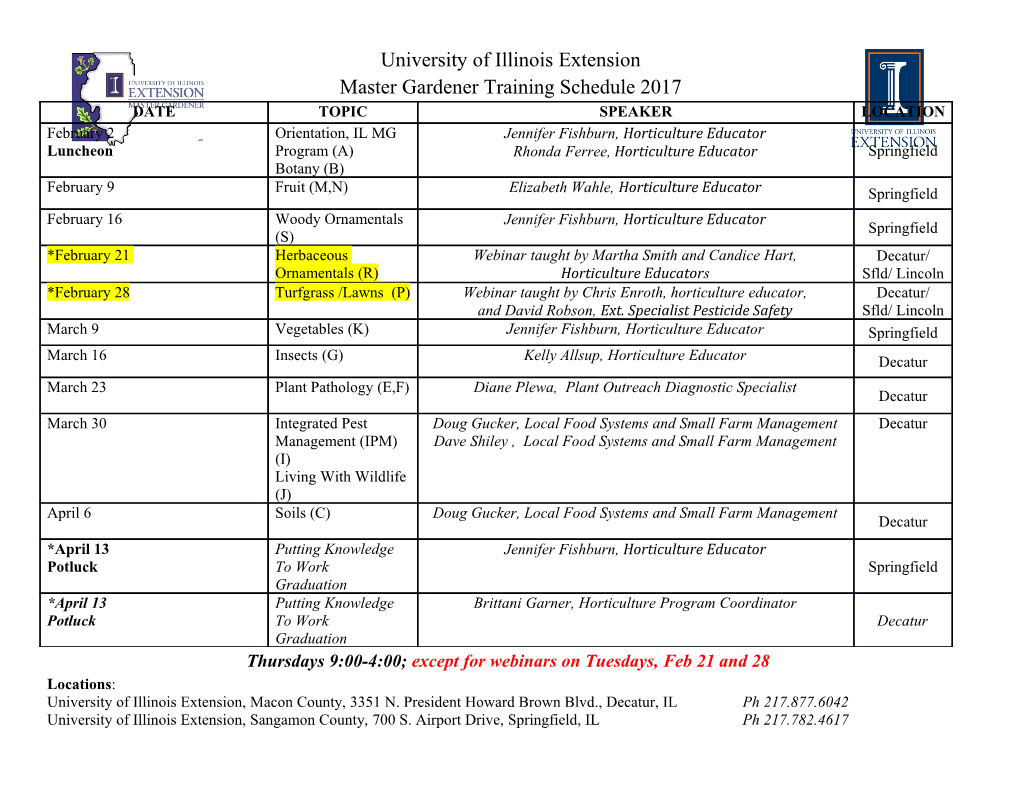
Transactions on the Built Environment vol 29, © 1997 WIT Press, www.witpress.com, ISSN 1743-3509 RELIABILITY-BASED FATIGUE INSPECTION PLANNING OF FIXED OFFSHORE STRUCTURES Luis Volnei Sudati Sagrilo, Edison Castro Prates de Lima, COPPE/UFRJ Carlos Cunha Dias Henriques, Sergio Guillermo Hormazabal Rodriguez, PETROBRAS S.A. Abstract -This paper proposes the practical application of a reliability-based procedure for fatigue inspection planning of fixed offshore structures. This procedure is based on a simplified probabilistic crack growth model for welded tubular joints available in the literature, which encompasses fracture mechanics and S-N curves and uses the results of the original fatigue design. Current techniques for reliability updating are implemented to re-evaluate the fatigue failure probability after inspection campaigns. Target reliability values are defined to be compatible with the simplicity of the procedure. Actual applications illustrate the inspection costs reduction that can be obtained. INTRODUCTION Fatigue is an important limit state in the design and operation of steel offshore structures. The fatigue design is usually based on Miner's rule and S-N curves but alternatively a fracture mechanics approach can be employed. There are several uncertainties concerning its evaluation. In-service inspections, using nondestructive tests, are planned and performed in order to assure an adequate safety level and to gather more information about the fatigue process. Fatigue inspection results can be basically summarized in detection or no detection of cracks. Until recently, fatigue inspection planning was based mainly on engineering judgment and usually the results of previous inspections were not accounted for the next ones. However, since the structural reliability analysis has become a practical and widely spread tool this situation has changed. Transactions on the Built Environment vol 29, © 1997 WIT Press, www.witpress.com, ISSN 1743-3509 316 Offshore Engineering Some important works on probabilistic inspection planning of offshore structures have been published recently*'*'***. These works take into account inspections results and show that it is possible to establish a rational fatigue inspection planning. Relevant practical results of probabilistic inspection planning can be seen also in Ref [11]. Most of these works employ a reliability method in connection with a fatigue crack growth model, based on linear fracture mechanics, to evaluate and update the probability of getting a through- thickness crack at any time during the field service life of the structure. Inspections are indicated whenever this probability fails above a target value. This target must be established taking into account several issues such as consequence of failure, cost of repair and so on. Since this task is not straightforward, this topic has not been clearly defined. As a matter of fact this target should be stated by standard codes, but up to now there are few ones covering this topic. This paper focus on practical inspection planning of fixed offshore structures using a probabilistic approach. It describes the theoretical topics employed in the development of a reliability-based procedure for fatigue inspection planning of fixed offshore structures and illustrates its practical utilization. This procedure uses a probabilistic mixed fracture mechanics/S-N model for crack growth in welded tubular joints proposed in Ref. [15] and FORM* to compute and update after inspections the probability of fatigue failure and its associated reliability index. Due to some approximations involved in the crack growth model and uncertainties in statistical data, these results and the target values are seen as qualitative indicators of reliability in the practical inspection scheduling process of individual tubular joints. Actual applications show the possible inspection costs reduction that can be obtained FATIGUE ANALYSIS Fatigue analysis can be performed basically by two methods™. 1) Miner's rule and S-N curves (S-N model); 2) Fracture Mechanics (FM model). Traditionally, the fatigue design of welded offshore structures has been based on S-N model while the FM model has been most used in the maintenance of such structures. These two models and their equivalence will be briefly presented below. S-N Model The S-N model uses the well-known S-N curves which are obtained from fatigue experiments of tubular joints. An S-N curve is given by N(S) = KS- (S>S,) (1) Transactions on the Built Environment vol 29, © 1997 WIT Press, www.witpress.com, ISSN 1743-3509 Offshore Engineering 3 1 7 where N(S) is the number of cycles to failure under constant amplitude loading S, K and m are material parameters, and So is a threshold level below which no fatigue damage is developed. For design purposes, generally, a characteristic S- N curve is defined by assuming m as a constant and setting K as the mean value of experiments minus two standard deviations^. The Miner's law for fatigue damage is defined as (S,>S.) (2) where N is the number of stress cycles in a reference period of time TR and D is the fatigue damage accumulation. Assuming that fatigue failure occurs when D reaches an amount A, the fatigue design life TL is given by T -31A ?L- o (3) In this procedure the stresses correspond to the local hot spot stresses, which are computed by multiplying the nominal stresses Sn, obtained from a global deterministic or stochastic structural dynamic analysis of the structure, by the stress concentration factor SCF. The SCF is obtained from standard parametric formulas or through a finite element analysis of the joint. The fatigue design life can thus be rewritten as AI — (4) I(Sn,SCF)- Fracture Mechanics Model The most employed FM model is the Paris-Erdogan crack growth equation defined by da - = C(AK(a)f = c(Y(a)S V^)" (AK(a) > AK,) (5) where a is the crack size ( in this paper it will refer to the crack depth only), n is the number of stress cycles, C and m are material parameters, K(a) is the stress intensity factor obtained from linear elastic fracture mechanics, Y(a) is the geometry function, S is the stress amplitude and AKo is a threshold below which no crack develops. Considering the mean frequency of long term stress cycles process equal to v, the integration of Equation (5) gives Transactions on the Built Environment vol 29, © 1997 WIT Press, www.witpress.com, ISSN 1743-3509 3 1 8 Offshore Engineering (6) where ao is the initial crack size, a is the crack size associated to time in service T and E[ ] is used to express the mean or expected value. The geometry function employed in this work corresponds to one that has been frequently used in offshore fatigue reliability analysis*'": Y(a) = 1 1.08 - 0.?Q I! 1.0 + 1.24expf- 22./-11 + 3.17expf- 357^-llj (7) where a is the crack depth and t is the tube wall thickness. The FM model can be employed whenever one needs to know the time interval for a crack to grow until a certain size. When using FM model for fatigue design purposes, similarly to S-N model, m is taken as a constant and C as a characteristic value^ (mean value of experiments minus two standard deviations). The fatigue design life is calculated from Equation (6) as the time in service until a critical crack size ac is reached. Usually fatigue failures of tubular joints are defined by a through-thickness crack and in this case the critical crack size ac is the tube wall thickness. Equivalence between FM and S-N Models A simplified calibration between the FM and S-N models can be obtained by assuming that the fatigue design life predicted by S-N model is the same as the time to obtain a through-thickness crack and the exponent m is the same in both models*'^'". By this calibration it is possible to show that the time in service T(a) for a crack to grow from ao to a is given by^ where TL is the fatigue life computed by Equation (4) and the function \P(x) for a particular value x = b is given by In this paper this calibrated model is identified as mixed FM/S-N model. Transactions on the Built Environment vol 29, © 1997 WIT Press, www.witpress.com, ISSN 1743-3509 Offshore Engineering 3 1 9 PROBABILISTIC FATIGUE ANALYSIS As pointed out in detail in so many works*'**'**, there are several uncertainties associated to the parameters of S-N and FM models. The rational way to address the effect of this uncertainties in the fatigue analysis is through structural reliability methods. For this purpose, a failure function or limit state function G(X) must be established in such a way that it indicates a failure state whenever G(X) < 0.0 and a safe state otherwise. X stands for a vector including all random variables considered in the analysis. Probabilistic approaches have been developed for S-N, FM and mixed FM/S-N fatigue analysis models. As the S-N model does not take into account any parameter related to inspection results, i.e., detection or no detection of cracks, its probabilistic approach has been mainly used in the development of standard codes for fatigue design™. On the other hand, FM probabilistic model has been widely used to develop rational fatigue inspection planning of offshore structures considering results of previous inspections*'^'*. The probabilistic mixed FM/ S-N model can be used for fatigue design criteria development*'^ or for probabilistic fatigue inspection planning**. Although some simplifications, the mixed FM/S-N model is attractive for practical purposes since it encompasses fatigue design and fatigue crack growth at same time. For this reason this model has been used in this work and it will be briefly explained in what follows.
Details
-
File Typepdf
-
Upload Time-
-
Content LanguagesEnglish
-
Upload UserAnonymous/Not logged-in
-
File Pages13 Page
-
File Size-