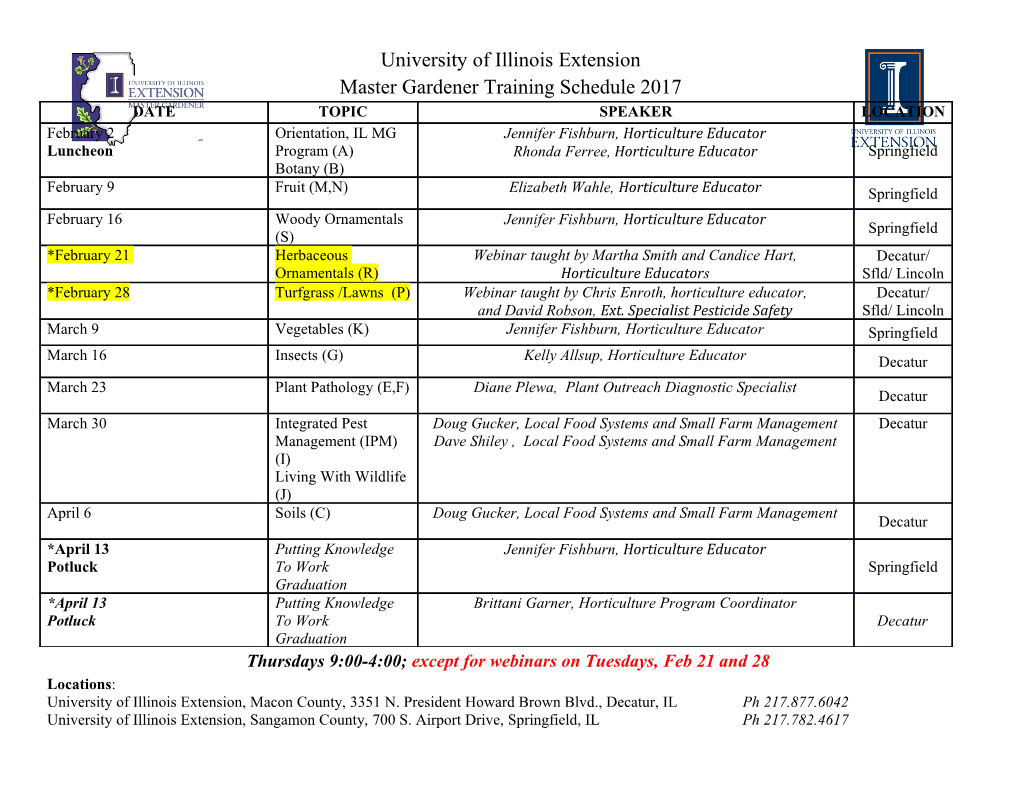
Fall 2013 Selecting a DC Motor Matthew Stephan Henry Michigan State University College of Engineering Fall 2013 P a g e | 1 I. Abstract The purpose of this paper is to provide analysis on the process of selecting a DC motor. It will give thorough descriptions of the principle operations of DC motors. By better understanding how this type of product works, the process of finding a motor should become simplified. Comparisons and contrasts will be given for many motor features aiding this process. The application note should provide clarity on what type of characteristics to look for and how to better make motor selection decisions. P a g e | 2 II. Keywords Armature – the component of the motor that produces power. It can be located on either the stator or the rotor. BLDC – brush-less direct current Brush – mechanism that conducts current in between moving parts and stationary wires. Brushed Permanent Magnet Motor - contains permanent magnets inside, which eliminates the need for external field current. This design allows a smaller, lighter, and energy-efficient Brush Motor. Brushed Series Wound Motor - speed varies automatically with the load, increasing as the load decreases. Brushed Shunt Wound Motor - run at constant speed regardless of the load. Commutator – mechanism which reverses the direction of current in certain electric motors. Direct Current – electrical charge constantly flows in the same direction. Opposite of an alternating current, where current periodically switches direction. Electrical Power – electric circuits transferring electrical power at a given rate. IPM – Internal Permanent Magnet PWM – Pulse Width Modulation Rotor – rotating device in an electric motor which rotates about the Brush DC Motor generating torque among the rotor’s axis. Stator – the part of the Brush DC Motor that is stationary. Torque – the ability of a force to rotate a given object about an axis or fulcrum. P a g e | 3 Table of Contents I. Abstract ........................................................................................................................ 1 II. Keywords ................................................................................................................. 2 III. Introduction .............................................................................................................. 4 IV. Motor Design ........................................................................................................... 4 a. What is a DC motor? ................................................................................................... 4 b. Brushed vs. Brushless DC Motors ............................................................................... 5 c. Hall Effect Sensors vs. Back EMF .............................................................................. 6 d. MCU Based Design vs. Standalone Solution .............................................................. 8 e. Commutation Methods .............................................................................................. 11 V. Conclusions ............................................................................................................ 12 VI. References .............................................................................................................. 13 P a g e | 4 III. Introduction The goal of this application note is to allow the reader to make better decisions when researching the type of motor to select for a project. I will begin by providing a description of what a DC motor is and comparing Brushed versus Brushless DC motors. From there I will go into specific features of motors for example their sensor capabilities, micro-controller use, and commutation method. I will also provide examples of motor applications. Finally, I will end with a conclusion of what steps to take with the provided information. Usually, a motor selection involves many more factors than are presented here. This method, however, provides the designer with a starting point for the selection of motors for a particular set of design options. IV. Motor Design a. What is a DC motor? Motors are seen everywhere in the world today. Almost every mechanical movement seen in your daily life is caused thanks to some type of AC or DC motor. A DC motor is a mechanically commutated electric motor powered from “direct current” hence the “DC”. There are many types of DC motor architectures but I will explain the basic type of motor you will see in typical daily applications. These motors are comprised of six main components; permanent magnets called the stator, a spinning armature called a rotor, an axle, a commutator, field magnets, and brushes (optional) [1]. The motor uses magnetism to create rotational motion and spin the axle. By connecting a battery, current is allowed to flow which will generate an electric field. This is then placed within another external electric field that is constantly “flipping” directions causing the rotation. When power is applied, the polarities of the energized winding and the stator magnets are misaligned, and the rotor will rotate to try and get aligned with the stator's field magnets [2]. The rotation reverses the direction of current through the rotor winding, leading to a P a g e | 5 "flip" of the rotor's magnetic field, driving it to continue rotating. The simplest form of this is done with only 2 poles, however there can be many more poles in application. It is possible to have many different connections of the field and armature winding which provides for diverse speed/torque characteristics. Many motors have feedback sensors which provide information on the performance characteristics. These and other features will be described in the following sections. All of these choices must be factored when choosing what type of motor to use. b. Brushed vs. Brushless DC Motors There are two main types of DC motors. The first and increasingly popular choice today, is a Brushless DC motor. This type of motor has permanent magnets in the rotor and stationary electrical current coil magnets on the housing of the motor to act as the stator. You may then use a motor controller to convert the DC input power to output AC. A brushed motor on the other hand generates torque directly from DC power supplied to the motor by using internal commutation, stationary magnets and rotating electrical magnets [3]. Some advantages of brushed versus brushless are seen in the table of Figure 1 below. Advantages Disadvantages Brushed Cheaper initial cost Brushes eventually wear out Older/ Easier to Find Sparking/Electrical Noise due to making/breaking connections Simple Construction - No controller necessary Brushes Limit Maximum speed of motor Quick Application Harder to cool with internal, centered electromagnet Limit to # of poles possible Less Reliable Brushless Better Speed vs Torque Characteristics Higher Start-up Cost Saves money over time Can become difficult to operate with motor controller Less Maintenance/More Reliable Most drivers slow BLDC motors by applying reverse current Noiseless Operation Nearly as much power is used to stop the motor as to start it Better Speed Ranges Figure 1 – Advantages of Brushed vs. Brushless DC Motors P a g e | 6 c. Hall Effect Sensors vs. Back EMF Another important feature of DC motors is the ability to generate feedback. These sensors provide information on the current, position, speed and direction of a rotating motor. This is a very useful tool to ensure that you are providing the correct amount of torque and speed to your circuit. The two main methods for providing this feedback are Hall-Effect Sensors and Back EMF. Hall Effect sensors are easier to implement and require the least amount of effort for the user. The sensors main purpose is to convey information about the rotor’s position at any instance in time. This is done via the Hall Effect which basically states that there will be a voltage difference between sides of a conductor when an electrical current passes through. If the magnetic field is known, the hall voltage can be measured to determine the distance from the conductor. This effect is what allows us to determine the position. A graph of the Hall Effect with 120° angle separation in operation is seen below in Figure 2. Figure 2 – Hall Effect Commutation Drive Voltage P a g e | 7 This table represents the state of the high-side and low-side MOSFETs of the half-bridge amplifiers for all three phases during trapezoidal commutation [4]. When the sensors read the speed, position, etc… you can then send them to the controller which will adjust these readings to achieve the desired parameters. The back electro-magnetic-force (EMF) method on the other hand, does not require any additional sensors. This implementation however, is much more complicated and has to overcome several issues. This method is achieved by obtaining the speed and position of the motor directly from the voltage at the motor windings. This back EMF is created when the motor’s armature turns, which creates an electrical pulse that is sensed as a voltage through a resistor. The amplitude of the EMF signal increases with the speed of the armature rotation. The back EMF voltage can either produce a sine or trapezoidal waveform which is then sensed at the motor’s winding and typically converted into a digital square wave by a comparator circuit [5]. You can then use a microcontroller to calculate the motor position and phase relationship from these generated square waves. Comparisons of the Hall Effect Sensor vs. Back
Details
-
File Typepdf
-
Upload Time-
-
Content LanguagesEnglish
-
Upload UserAnonymous/Not logged-in
-
File Pages14 Page
-
File Size-