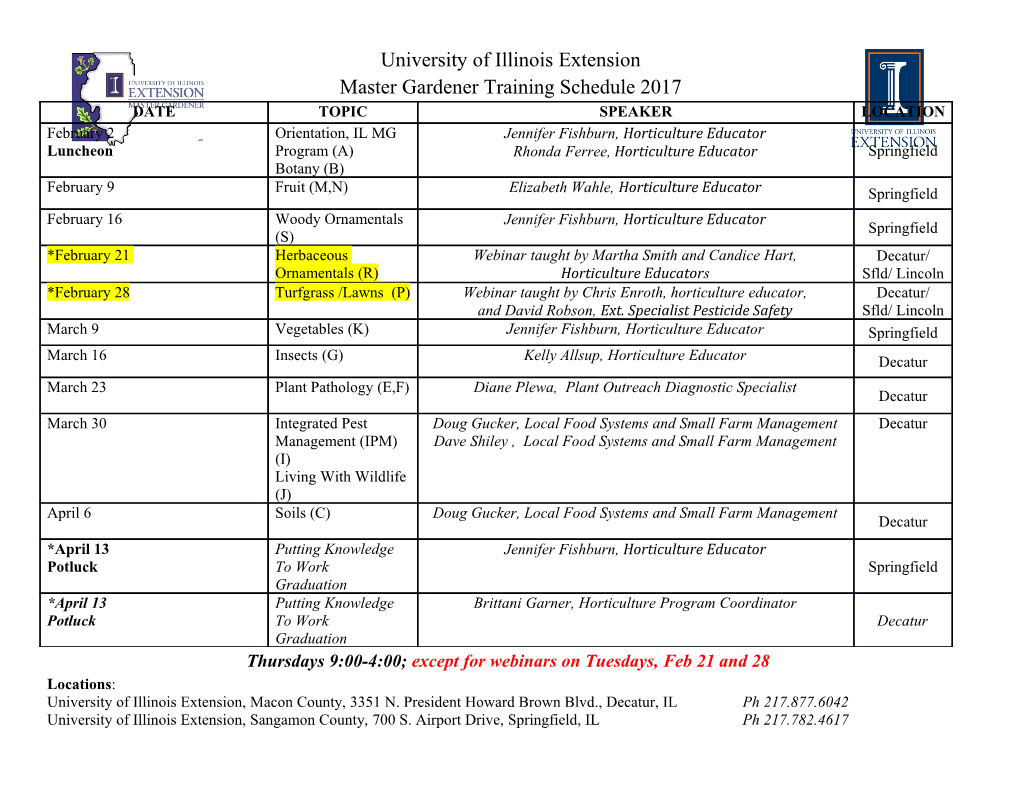
AJAX REPRINT No. 182 An Introduction to SALT BATH HEAT TREATING by Q. D. Mehrkam V. P. Research 8 Development AJAX ELECTRIC COMPANY Philadelphia, Pa. Reprinted from TOOLING & PRODUCTION Magazine, June & July, 1967 Figure 1 Rate of hearing curve shows the time required to heat a part of given dimensions. Part I Salt bath heat treating WHEN WORK is fully immersed ening) to the quench operation. into a salt bath furnace, no air Conduction heating. When the can contact it. Steel scaling, oxi- by Q. D. Mehrkam work is immersed, heat is trans- dation and decarburization can be V. P. Research & Development ferred by direct contact with a avoided. It is common to process AJAX ELECTRIC CO. heating medium of high capacity. low, medium, and high-carbon Philadelphia, Pa. This is 4 to 6 times faster than steels in the same medium without possible in radiation or convection surface carburization or decarburi- type methods. For example, the zation. This is particularly advan- time required to heat a part of tageous for a variety of batch-type given dimensions, at 1500°F,* the heat treating work. A thick salt rate of heating is approximately film adhering to the surface serves as protection which continues when the work is removed and *All temperatures in this discussion are transferred (in the case of hard- Fahrenheit. Immersing metals, ceramics, or plastics in a molten salt makes possible unique characteristics. 5 min/in of thickness or ¼ the time bath’s composition consists of one Design features or more salts, nitrates, chlorides, required in radiation type equip- Furnace size and shape can be carbonates, cyanides, caustics, or ment, see Fig. 1. almost anything desired. One de- additives in small amounts. The Automatic preheat. Upon immer- sign uses a metal pot for temper- additives can be sulphates, fluo- sion into molten salt, a frozen salt atures up to 1750°. With this rides, etc. cocoon forms around the part. arrangement, electrodes must Heat is transferred between Layer thickness and the time re- enter from the top and are usually work and molten salt by conduc- quired to melt it depend upon size located along the back wall free of tion. The salt lends itself to either and shape of the part, bath oper- o the work area, see Fig. 2. All ex- heating or cooling within a 300 ating temperature and salt melting o ternal walls are heavily insulated to 2400 range, as required. Com- point. As a result, the work is sub- and radiation losses from surfaces patible salt mixtures are selected jected to an automatic preheat are minimized by a suitable cover. with proper operating ranges and which prevents excessive heat The metal pot in this type furnace often are formulated to meet spe- shock and distortion damage of is used whenever salts contain cific temp-range requirements. cracking. Furthermore, heat is appreciable amounts of cyanides, transferred to the work over its carbonates, and caustic soda, or for entire surface uniformly. One side Operating principle low temperature applications using will not heat faster than the other. nitrates and nitrites. As the part gradually heats to the The electrode furnace generates A different type furnace is pre- salt’s melting point, the cocoon direct heat in salt by using its re- ferred for higher temperature o o melts leaving only the molten salt sistance to current passage. Salts, applications in the 1200 to 2400 while insulators in the solid state, contacting the work. It is impossi- range. The pot is of interlocking ble for the work to be higher or are excellent high-resistance con- ceramic tile. Electrodes are re- lower than the bath’s temperature ductors in the molten state. Poten- placed without costly downtime. tial is applied to the molten salt control. The tile is merely raised, the old by use of heavy electrode bars. electrodes removed, the new or Buoyancy. An important property These are connected to the sec- rebuilt electrodes installed, and the in molten salt is molten salt ondary of special multiple voltage tile replaced. weight; it may be 2 to 3 times that air cooled transformers. Electrodes A third type furnace, radically of water. Thus the piece’s im- are located in a recessed area of different from those above, is pri- mersed weight is appreciably de- the bath and cause salt circulation marily intended for cooling rather creased 25 to 35 per cent of the by electromagnetic forces when than heating. The isothermal original. This helps- hold work energized. A strong magnetic field quench furnace is for martemper- distortion to absolute minimum. is created between electrodes when ing, austempering and isothermal located close together. heat treating operations (of which Using Maxwell’s Law, this field Furnace development there are many hundreds). This will cause salt particles between About 30 years ago, the first im- electrodes to move downward in portant salt bath furnace installa- a whirlpool fashion. This electro- tion was made in this country. dynamic circulation assures abso- Since then they’ve gained wide lute temperature uniformity recognition and the number has through the bath and eliminates grown-not only in number but in danger of undesirable differentials. size and capacity. The 5000 in use today range in size to 43 ft L x 20 ft D x 8 ft W. In use, the unit con- tains 300,000 lbs of salt. Many operate with connected loads over Figure 2 Ajax Type H Furnace has a metal 2500 km. pot with electrodes entering from The furnace has a ceramic or the top. This type furnace is pre- metal container filled with molten ferred for cyanide hardening, car- salt. The work can be immersed burizing, descaling, desanding, and for either heating or cooling. The cleaning. is used for diffusing carbon and small amounts of nitrogen into steel surfaces. It will alter physi- cal properties of the surface by materially increasing strength and wear resistance. Liquid carburiz- ing is done in baths, operating at 1450o to 1750o. All carburizing steel grades, carbon and/or alloy, may be liquid carburized with case depths of 0.005" to 0.250". A uni- form carburization rate is con- trolled by maintaining sodium cyanide concentration-the source of carbon and nitrogen, see Fig. 3. Salt samples are removed from the bath daily, and are analyzed for cyanide content. Replenish- ment salt is then added to main- tain cyanide content at the re- quired operating level. Since cy- anide oxidizes in contact with air at these temperatures, the bath operates with a carbonaceous scum cover which serves two purposes: 1) It reduces radiation losses by 50 per cent or more-thus saving power; and, 2) it reduces cyanide oxidation. It’s interesting to note, a car- burizing bath doesn’t fluctuate chemically-radically or rapidly.’ It normally consists of a carbonate, chloride and cyanide mixture. With cyanide oxidation, carbonate is formed and this requires periodic dilution by adding fresh salt. Pro- prietary salt replenishments are available in varying concentra- tions of the above chemicals, to maintain proper chemical balance. Generally, it is only necessary to Figure 3 maintain the sodium cyanide oper- Carburizing curve shows time penetration needed to get desired care depth at various furnace temperatures. ating level. For example, the carbonate con- type furnace will always have a the work into the nitrate-nitrite, a centration in a deep case carburiz- metal port heated by either resist- separating chamber continuously ing bath should not exceed 30 to ance heaters or gas fired immer- clarifies the bath. Chloride salts 35 per cent with a sodium cyanide sion tubes. The external pot sur- settle to the chamber bottom and content of 8 to 12 per cent. Other- face is frequently finned and air are removed periodically. This wise, carburizing potential or the under pressure is circulated type furnace normally operates bath’s ability to do it is adversely o around the outside to extract heat. within 400 to 750 . affected. A higher cyanide con- Both heating and cooling cycles By eliminating pumps, separat- tent will also account for greater are automatically controlled to ing chamber and cooling chamber, breakdown to carbonate. If drag- maintain a constant and uniform the furnace can also be used for out losses on the work surface are o ±10 temperature. heating applications with in the low, it may be necessary to bail a o For quenching, salt must be range of 400 to 1100 . It can be portion of the bath each day to properly agitated. This is done heated by either resistance heaters maintain proper chemical balance with a propeller driven pump or gas-fired immersion tubes. by adding fresh salt. As we point which forces the molten nitrate- out above, chemical change is not nitrite salt through the quench rapid and considerable variation Applications header. Whenever high temper- can exist without affecting carbon ature chloride salts are carried by Liquid carburizing. This method potential. ure of its effect on the steel sur- Rectifiers incorporating silicon bath quench achieved a consist- face being treated. A more con- carbide, metallic silicon and silica ently higher uniform hardness lev- clusive examination is made by are commonly used effectively and el than obtainable by air cooling. processing steel test coupons, then will carry contamination to the Surface scaling is eliminated examining the surface hardness furnace bottom as sludge. This can since there is no contact with air using micro-hardness or superfi- be removed by desludging tools. while cooling through the oxidiz- cial hardness testers or microscop- While this rectification method is ing and scaling temperature range. ically examining a cross section. effective, it’s a disagreeable task.
Details
-
File Typepdf
-
Upload Time-
-
Content LanguagesEnglish
-
Upload UserAnonymous/Not logged-in
-
File Pages12 Page
-
File Size-