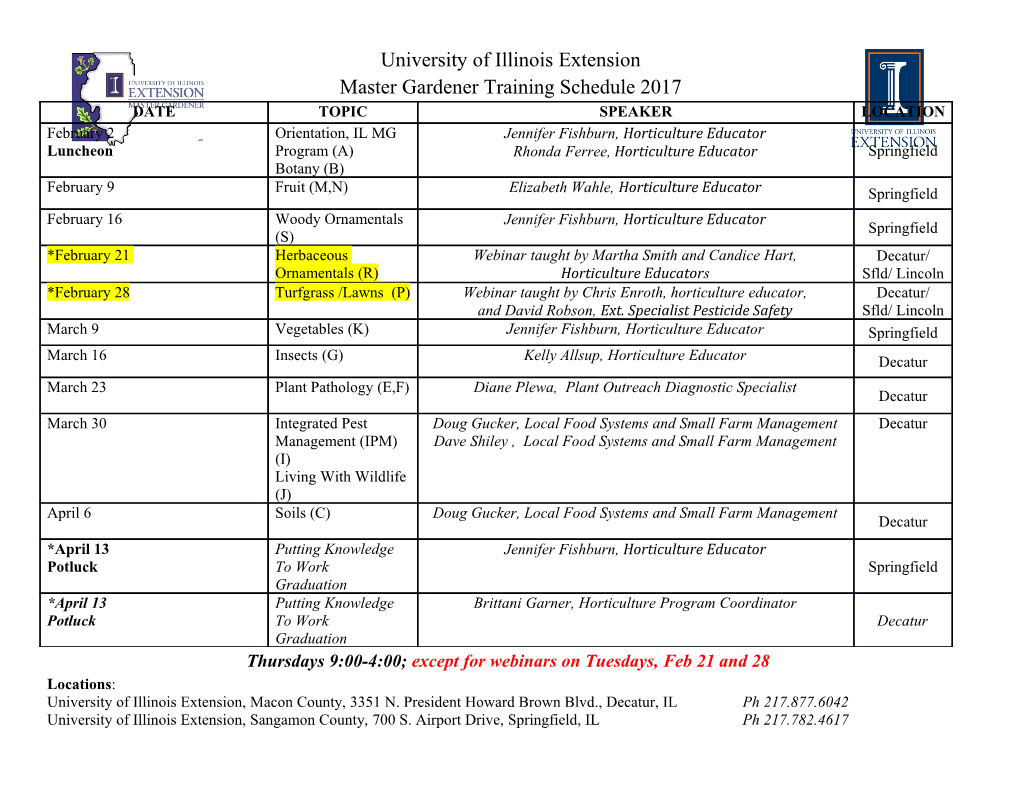
THE AMERICAN SOCIETY OF MECHANICAL ENGINEERS 345 E 47th SL, New York, N.Y. 10017 96-GT-244 The Society shall not be responsible for statements or opinions advanced in papers or discussion at meetings of the Society or of its Divisions or Sections, or printed in its publications. Ditetcion Is printed only if the paper is published in an ASME Journal. Authorization to photocopy • material for internal or personal use under circumstance not falling within the fair use provisions of the Copyright Act is granted by ASME to libraries and other users registered with the Copyright Clearance Center (CCC) Transactional Rearming Service provided that the base fee of $0.30 per page is paid directly to the CCC, 27 Congress Street, Salem MA 01970. Requests for special pennistion or bulk mproduzlion shoukt be ad- dressed to the ASME Technical Publishing Department. Copyright 0 1996 by ASME All Rights Reserved Printed In U.S.A. Downloaded from http://asmedigitalcollection.asme.org/GT/proceedings-pdf/GT1996/78736/V002T02A006/2406937/v002t02a006-96-gt-244.pdf by guest on 30 September 2021 INLET AND NOZZLE TECHNOLOGY FOR 21ST CENTURY FIGHTER AIRCRAFT Marvin C. Gridley 111111111111,111111 111111 Steven H. Walker Wright Laboratory IMJFIMA Bldg 450 2645 Fifth Street Suite 7 Wright-Patterson AFB, OH 45433-7913 USA ABSTRACT more flexible, to perform a variety of missions to counter changing The focus of propulsion integration technology in the 21st threats. century will be economy. USAF inlet and nozzle technology goals Specifically, two propulsion integration technologies that offer translate into 50% weight reduction and 25% acquisition cost the potential for lower cost and more survivable aircraft systems while reduction metrics for new aircraft system. Innovative technology to maintaining today's performance levels are advanced compact inlet enable these reductions over current state-of-the-art systems in weight systems and fluidically controlled exhaust nozzles. Large cost and and cost is required. For inlet systems, compact diffusers that reduce weight benefits can be attained using compact inlets, reducing volume system volume by 50% will demand fewer parts and improved and weight of the aircraft system. Fluidic thrust vectoring and/or aerodynamic performance. Exhaust systems will be fixed with fewer fluidic area control of exhaust nozzles can meet nozzle performance parts, requiring a technology like fluidics, for example, to provide area requirements while reducing parts count leading to lower cost and control and thrust vectoring capabilities. Cooperative programs for lower weight exhaust nozzles. These reductions in inlet and nozzle both inlet and nozzle systems are in place to insure that technologies cost and weighi translate into large life cycle cost savings at an aircraft required to meet weight and cost reduction goals are matured by the systems level. year 2000. • INLET SYSTEM INTEGRATION INTRODUCTION Historically, the threat to USAF aircraft has dictated that inlet Technology Goals technology advances in propulsion integration be oriented towards Traditionally, the figure of merit for aircraft inlet systems has increasing performance. Changes in the global political climate and been performance. Previous operational inlet designs maximized total the resulting impact on national economic priorities have shifted the pressure recovery and minimized distortion at the engine face, and emphasis away from performance to economy. Next generation minimized overall frontal observables. Current budgetary realities aircraft must have lower life cycle cost, be more reliable, perform have caused a shift in the technology development approach to center more and varied missions, and have longer life. Further, multi-service around maintaining current levels of inlet system aerodynamic variants will be encouraged as a way to cut costs. performance at a reduced life cycle cost and/or increased aircraft Propulsion integration technologies are key to attaining system utility. goals of lower cost, Fthil&S, and increased utility. Simplicity in Current USAF inlet technology development has the following integration should lead to lower cost through greater configuration goals for the year 2000: freedom and internal aircraft packaging flexibility, satisfying multi- • decrease inlet weight and volume by 50% from current service requirements. baseline Performance remains an important issue, however. Global technology development will mean more and more potential threats • maintain or increase current inlet performance levels with technologically advanced weapons systems. Therefore, the next The baseline inlet system is the current state-of-the-art in inlet generation aircraft will, at a minimum, be required to perform at system technology: a caret inlet aperture with a long, serpentine current system levels. Additionally, future aircraft systems must be Presented at the International Gas Turbine and Aexoengine Congress at Exhibition Birmingham, UK — June 10-13, 1996 subsonic diffuser, similar to the design pictured in Figure 1. This cowl, an inlet can be made "diverterless" for Mach numbers up to = design provides for high aerodynamic performance and survivability 2.0. throughout the tactical fighter envelope. Surface Downloaded from http://asmedigitalcollection.asme.org/GT/proceedings-pdf/GT1996/78736/V002T02A006/2406937/v002t02a006-96-gt-244.pdf by guest on 30 September 2021 ftAe NEW 16 1 FFOMi NEW `~ Yrtual Bump amavaw — – Conical~ Conei Leading Edge Shock ,_.0 on Shock Figure 3 - Bump Compression Surface Figure t - Caret Inlet System This methodology was used to design inlets in the USAF Wright Background Laboratory Management of Advanced Inlet Boundary Layers (MAIBL) program. The objective of MAIBL was to develop design Historically, inlet complexity has increased with the maximum criteria for advanced inlet boundary layer control (BLC) systems. Mach capability of the aircraft , Figure 2. Traditional inlet Several different boundary layer control techniques were tested in the performance enhancement techniques such as variable geometry, MAIBL program, including shaping (e.g., the bump compression boundary layer diverters , bypass systems , and bleed have been surface), flush and pitot boundary layer diverters , wall jets, and porous incorporated to achieve the levels of performance required for high Aerodynamic performance was determined performance aircraft. and slot bleed systems . using CFD and subscale testing . Results shown in Figure 4 indicate B.L. Sides Camp B.L. Variable Bypass that the inlet BLC methods studied could provide adequate Divarttt Spliatt Surlace Bleed Gear System aerodynamic performance for advanced fighter applications. Plela F-89 ..;>?:¢,::'3 Subsonic sn Fe.s.hsul0..e FSA '4h1'EYtio1 t6e.:'u. e.eR F-101 F-102 ;0$1,?.~ a9u„g: k Mach F-16 ..0?,6;.}$:&. 1.2.2.0 F-18 F-104 ACIS 170 F.105 . ".y.: . 13 xq~ F-10fi F4 .o a Mach F-14 2.0-2.2 R.aesn YF-23 ,..Yob . Rs e.s e.r MASS FLOW RATIO, YFR - AO/AL :. F-111 .T.Ft"A:r.;9r ;;oi3Y::.:: e>:.:..'WA 'rs's'.o:.,..„ia`Y.':.:.. Mark 2.5 Figure 4 - MAIBL Performance Results, M = 1.9, a = 0 0 Figure 2 - Inlet Complexity with Max Mach Number In the NASA/McDonnell Douglas Performance Study for Inlet Recent advances in inlet design methodology, namely Installations (PSII) program, a conceptual design trade study was computational fluid dynamics (CFD) techniques, have allowed inlet performed to determine the impact of inlets incorporating design designers more insight into inlet and diffuser flowfields. This features for survivability on inlet performance , weight, and cost for alleviates some traditional geometric constraints and allows inlet fighter and attack aircraft (Bingaman , 1992). The trade studies used designers and aircraft configurators greater flexibility . For example, ( ) Quality Function Deployment (QFD) techniques to prioritize issues inlets for certain applications may now be designed without diverters and select the optimum air induction system configuration for each of or bleed systems along with much more compact subsonic diffusers. two notional aircraft : a multi-role lightweight fighter and an advanced One of the most promising techniques for inlet design is medium attack bomber . The QFD scores were driven by performance, illustrated in Figure 3 . In this technique (also used in hypersonic observables, weight, and cost. Figure 5 shows the air induction applications), a "bump" shaped, waverider compression surface is system configuration for the selected optimum multi -role lightweight defined by streamlines emanating from the intersection of a plane fighter. Figure 6 illustrates trade study results which led to the which passes through the shock wave resulting off a cone placed in a selection of this configuration as optimum . The multi-role lightweight supersonic flow field . The resulting pressure gradient on the bump fighter air induction system chosen received the highest QFD ranking, surface pushes the low energy boundary layer outboard. By and also resulted in the lowest cost air induction system with the combining this type of compression surface with a properly designed lowest increase in air vehicle TOGW. • survivability • aerodynamic performance With these priorities set, the technical groundrules for the ACIS program are as follows: 1) The inlet system must be fixed geometry. As seen in Figure 7, Downloaded from http://asmedigitalcollection.asme.org/GT/proceedings-pdf/GT1996/78736/V002T02A006/2406937/v002t02a006-96-gt-244.pdf by guest on 30 September
Details
-
File Typepdf
-
Upload Time-
-
Content LanguagesEnglish
-
Upload UserAnonymous/Not logged-in
-
File Pages8 Page
-
File Size-