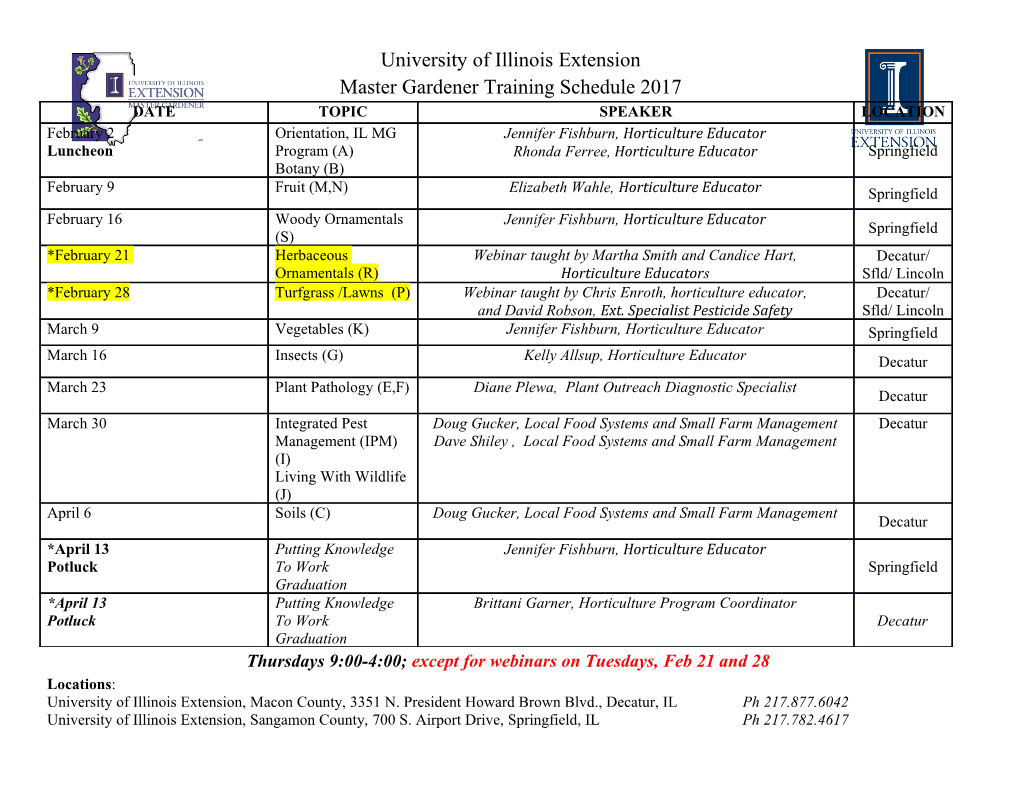
2,798,878 Jnited States Patent Office Patented July 9, 1957 2 weeks; and, finally, the method must be safe from the hazard of-explosion. One of the objects of the invention is to provide a 2,798,878 method of oxidizing graphite to graphitic oxide with the PREPARATION OF GRAPHITIC ACID production of a high quality product of low carbon-to Williaria S. Hummers, Jr., Detroit, Mich., assignor to Na oxygen ratio. tional Lead Company, New York, N. Y., a corporation Another object of the invention is to provide a method of New Jersey of preparing graphitic oxide in a hazard-free manner with a processing time of one or two hours, or less. No Drawing. Application July 19, 1954, 0. Another object of the invention is to provide a method Seria No. 444,400 of preparing graphitic oxide in high yield, with a favor ably low consumption of oxidizing agents. 16 Claims. (C. 260-348) Another object of the invention is to provide a method of preparing graphitic oxide with materials which are This invention relates to the preparation of graphitic 5 relatively cheap, available, and readily handled. oxide from graphite, and more particularly is concerned Other objects of the invention will appear as the de with an improved method of carrying out the oxidation scription thereof proceeds. In accordance with the invention, the starting material, step involved. which is a graphitic substance which may be graphite, Graphitic oxide, sometimes known as graphitic acid, 20 has been known for almost a century, and is an important and is preferably a high grade of synthetic or natural material for experimental studies in electrode processes graphite, such as Ceylon graphite, is treated with a water of colloidal properties of materials related to humic acids, free mixture of concentrated sulphuric acid and an an in inorganic structural chemistry, and the like. Graphitic hydrous nitrate compound of the class of nitric acid, so dium nitrate, potassium nitrate, barium nitrate, and other oxide has also been suggested for use as a lubricant. It 25 inorganic anhydrous nitrate salts, together with an an was first prepared by Brodie in 1859 (Phil. Trans. 149, hydrous permanganate such as potassium permanganate. 249 (1859)) by repeated treatment of Ceylon graphite with an oxidation mixture consisting of potassium chlo Sodium permanganate may be used if anhydrous but this rate and fuming nitric acid. Since then, many other salt is hygroscopic so that potassium permanganate is preferred. The temperature for the reaction is preferably procedures have been devised for forming graphitic 30 Oxide, nearly all dependent upon strong oxidizing mix about 35 C., but may be as high as 45° C. and as low as tures containing one or more concentrated acids and ox 25 C. to 30° C. Above 45 C. the overall yields tend idizing materials. The methods most commonly used at to be low because of oxidation to carbon dioxide, and the present time are the original Brodie synthesis and below about 30° C. the reaction proceeds unduly slowly. one described by Staudenmaier, in which the graphite is However, the temperature may rise considerably higher oxidized in concentrated sulphuric and nitric acids with 35 than 45° C. upon the initial addition of permanganate, potassium chlorate. Even recent workers in the field but if heat transfer in the system is good, and the quantity Such as Hofmann (Z. anorg. allg. Chem. 234 4, 311 of permanganate initially added is small, then such tran sient temperatures of even as high as 70° C. do no (1937)), and Hamdi (Koll.-Beih. 54 563 (1943)), used harm, the system rapidly coming back to the preferred the Staudenmaier process, in which concentrated sul 40 phuric acid and concentrated (63%) nitric acid are range. mixed together with graphite to be oxidized and over a The nature of the product obtained can be quickly period of a week the requisite amount of potassium chlo checked by pouring some of the acid oxidizing mixture rate is added slowly and carefully with cooling, and with containing the graphitic oxide into a large excess of water removal of chlorine dioxide evolved with an inert gas and observing the color produced. Conversions too such as carbon dioxide or nitrogen. This Staudenmair 45 low to be of any practical use, as well as no conversion Hofmann-Hamdi method uses more than 10 grams of at all, give a black suspension. The suspension becomes potassium chlorate for each gram of graphite treated and "r dark green at carbon-to-oxygen ratios of about 3.0 to explosion is a constant hazard. 3.4, and these are usable products for some uses. When There are all stages of oxidation from pure graphite the oxidation has proceeded to a carbon-to-oxygen ratio to pure graphitic oxide, and the efficacy of an oxidation 50 of about 2.8 to 3.0 the color is light green. At lower method may be judged by the proportion of graphitic carbon-to-oxygen ratios the color is yellowish green, be oxide in the product, or more accurately, of the carbon coming bright yellow at the lowest carbon-to-oxygen to-oxygen ratio of the product. Even with a method ratios obtainable of about 2.05 to 2.4. which is efficacious in producing a product of low car A number of oxidizing treatments illustrative of prior bon-to-oxygen ratio (which for good samples of graphitic 55 and other methods, and a number of oxidizing treatments oxide should lie between 2.1 and 2.9), if such a method illustrative of the oxidation process of the present inven is to be useful, it must result in a minimum of wastage tion are given in the tabulation which follows. Where of graphite by oxidation to carbon dioxide. (Overall the carbon-to-oxygen ratio of the product obtained was yields in many preparative methods are very low.) determined by analytical procedures the ratio is given. Moreover, the method must not be wasteful of oxidizing 60 agents, particularly when commercial use of the graphitic Where this was not done, the color of the product deter oxide produced is contemplated; the method must permit mined as noted above gives a clear indication of the ex preparation in a matter of hours rather than days or even tent and therefore the success of the oxidizing process. - 2,798,878 3 4. TABLE Basis : gram graphite Run ml. Other Ingredients . Mesh of Temp., Color HSO Graphite C. 15 1g. Na2Cr2O7--------------------------- --325 30 Black. 15 4 g. Na2Cr2O7--------------------------- -325 ... 30. D0. 15 3.g. KMnO4, 15 ml. 70% HNO3---------- -325 30 O0, 20 1.g. KClO3, 10 ml, 70% HNO3--------- 200-325 0-60 Dark Green. 30 3.g. KMnO4, 3g. NaNO3---------------- 200-325 30 Do. 30, 3 g. KMnO, 1. g. NaNO3---------...--- 200-325 45 Green. 22-33g. KMnO, kg. NaNO3- 325 45 Bright Yellow 22-23.g. KMnO4, 1g. NaNO3- 200-325 45 Yellow. 22-33 g. KMnO4, 0.5 g. NaNO3 --325 45 Do. 22-23.g. KMnO, 0.5 g. NaNO3. -325 35 Bright Yellow. 22, 3 g. KMnO, 0.5 g. NaNO3 ... -325 35 D0. 22-33 g. KMnO, 1.0g. furning HNO3-------- -325 45 Light Green. 22% 3g. KMnO, 1.0 g. BaNO3--------------- -325 45 Yellow, 203 g. KMnO, 3.0 g, furning FINO3-...----- -325 45 Do. In Table I, run D, represents the conventional Stau denmaier-Hofmann-Hamdi procedure. It will be noted about one-twentieth to one-fiftieth should be anhydrous that while a product of satisfactory carbon-to-oxygen 20 nitrate for optimum results. : ratio was obtained, two weeks or 336 hours were taken. The graphitic oxide is recovered from the acid oxidizing The temperature range shown indicates the fluctuation bath in known fashions, the most commonly used method occurring, the oxidizing liquid heating up when chlorate being that of diluting the reaction product mixture with is added bit being cooled down whenever the temperature several volumes of water and recovering the graphitic 25 oxide by decantation, centrifuging, dialyzing out the acids, gets too high. Run C shows an attempt at making gra and salts, and the like. Such methods will not be de phitic oxide, using potassium permanganate and ordinary scribed in detail herein since they are adequately covered 70% nitric acid. Even a twenty-four hour oxidation at in the chemical literature, 30° C. failed to produce anything more than a black The present process is particularly favorably adapted color. Runs A and B show the use of sodium chromate in a sulphuric acid bath where even a seventy-two hour 30 for continuous oxidation, in view of the short oxidation oxidation failed to proceed beyond the black stage. time of some thirty minutes. Thus, a continuous flow of in complete contrast to runs A, B, C, and D, the re the acid oxidizing mixture together with the graphite can mainder of the runs, E through N inclusive, show pro be maintained in coils immersed in a bath at the selected cedures in accordance with the invention wherein con temperature, for example 35° C., the rate of flow being centrated sulphuric acid was used together with potassium 35 such that the transit time is approximately thirty minutes. permanganate and an anhydrous nitrate which in most The oxidized product is recovered from the mixture at the cases was sodium nitrate, but barium nitrate and funning end of this time, and the sulphuric acid can be recovered nitric acid, were used as well. In all cases, green to in accordance with conventional methods, concentrated yellow products were obtained of excellent carbon-to and reused.
Details
-
File Typepdf
-
Upload Time-
-
Content LanguagesEnglish
-
Upload UserAnonymous/Not logged-in
-
File Pages3 Page
-
File Size-