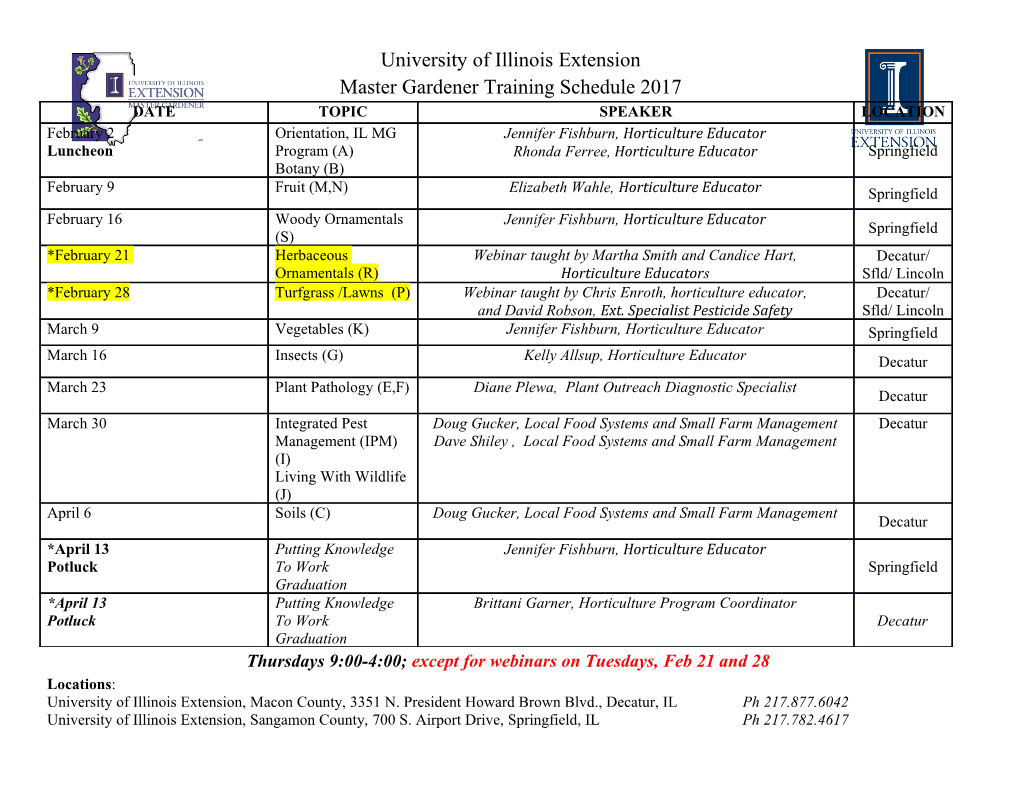
OUTLOOK GRAPHENE don’t all buy $5,000 suits. A lot of the time a $300 suit is all you need to wear,” says James Tour, an organic chemist who specializes in nanotechnol- ogy at Rice University in Houston, Texas. But for materials scientists allured by graphene’s extraor- dinary potential in electronics and optics it is the $5,000 suit — or high-quality graphene – that they strive to produce on a large scale. EXFOLIATING GRAPHITE For at least a century, researchers have been producing stacks of thin carbon platelets by pulling graphite apart into its constituent layers. (A description of a suspension of small graphite flakes was published in 1907, for example). But these days manufacturers, alert to graphene’s potential, produce consistently thinner platelets. UNIVERSITY OF SINGAPORE NATIONAL PHYSICS DEPT., GROUP, OZYILMAZ Graphite’s layers are very close-knit, so acids are used to oxidise the material to graphite oxide, lay- ers of which are more easily separated to form graphene oxide. Chemical reduction of graphene oxide leaves graphene platelets crumpled in a solution, or as a powder: a process first reported in 1961 by German chemist Hanns-Peter Boehm, who called his product ‘thinnest carbon films’. It PRODUCTION is this method — with proprietary modifica- tions — that companies such as Vorbeck Mate- rials, in Jessup, Maryland; Angstron Materials in Dayton, Ohio; and XG Sciences in Lansing, Beyond sticky tape Michigan, still use to produce large quantities of graphene. Researchers constantly invent twists in the technique: in 2011, Chao Gao at Zhejiang Flecks of graphene are easy to make. But producing sheets University in Hangzhou, China, reported spin- of pristine, electronics-quality material is another matter. ning a concentrated solution of graphene oxide flakes into fibres several metres in length, which could then be chemically reduced to filaments of BY RICHARD VAN NOORDEN perfect single sheets. The platelets are typically pure graphene1. rough stacks of 5 to 10 carbon layers riddled with Angstron scientists have found a way to pro- nlike many hi-tech materials, graphene is defects, and begrimed with other chemicals. Yet duce graphene without the harsh acid treatment so simple to make that anyone can pro- they still have the attributes that make graphene of the graphite oxide route. They disperse pieces duce it at home. First, press adhesive tape so appealing: they’re lightweight, strong, have of graphite in water and surfactant, and use ultra- Uonto a chunk of graphite and pull: this peels off a a large surface area and conduct electricity and sound to peel off layers of carbon: a more pristine thin flake of grey-black carbon. Then repeatedly heat. It’s already possible to buy dozens of differ- graphene as fewer chemicals are involved in its stick the carbon-covered tape against itself and ent grades of graphene made this way as powders production. Andrea Ferrari, professor of nano- peel away: the carbon flake breaks up further into or in solution. Developing applications range technology at the University of Cambridge, UK, thin, faint fragments, each hundreds of microme- from conductive inks and fillers in composites, to who has worked on solutions of graphene for tres across. After a few rounds of this, some flakes battery electrodes and electrochemical sensors. ink-jet printing, reckons this method might be have been whittled away to single-atom thickness For more demanding electronics, however, useful in electronics that do not need the highest — a fleck of graphene. researchers need much purer graphene in large quality graphene, such as touch screens, ‘smart All in all, it is a pleasingly artisanal way to sheets — millimetres or centimetres in diameter. windows’ that can adjust light levels when a volt- make a remarkable material. The graphene is The aim is to grow theoretically perfect graphene: age is applied, or conductive fabrics that might high quality, too: it was on similar products that a hexagonal, honeycomb carbon lattice with not carry signals from iPods, for example, or heart Manchester University physicists Andre Geim a single atom out of place. In practice, a real car- monitors. and Kostya Novoselov measured extraordinary bon lattice is strained by defects, polluted by 5- or electron-transport properties in 2004 — experi- 7-membered rings, its edge is ragged, and it sits GROWING GRAPHENE ments for which they won the 2010 Nobel Prize on a substrate that interferes with its properties. To make larger, higher-quality sheets of gra- in Physics. “You can make several square milli- These imperfections impair conductivity and phene, researchers are growing the material as metres with a couple of hours’ work,” says Peter other electronic properties. Whether that matters a single-layer carbon film on top of another Blake, cofounder of Manchester-based Graphene in practice depends on the purpose: transparent surface, a technique known as chemical vapour Industries, which sells such flakes to researchers conducting films in touch screens, for example, deposition. This isn’t new either: ‘monolayer for £500–1000 (US$780–1550) each. need not be as conductive as those in solar cells. graphite films’, or graphene, were made this But one can’t mass produce graphene with Large carbon sheets and small imperfect way in the 1970s. Typically, a mixture of meth- sticky tape. To do this, researchers use chemicals carbon platelets are such contrasting forms of ane and hydrogen gas is passed across a sheet to split graphite into graphene platelets by the graphene that they could almost be considered of copper in a furnace at 800-1000°C, and a tonne. Unfortunately, with speed and volume different materials. In fact, each version has its single carbon layer forms atop the copper; comes variable quality: few of these platelets are merits, depending on cost and application. “We chemical processing can remove the copper S32 | NATURE | VOL 483 | 15 MARCH 2012 © 2012 Macmillan Publishers Limited. All rights reserved GRAPHENE OUTLOOK GROWING GRAPHENE FILMS Researchers make large (centimetre-scale) graphene lms by depositing carbon atoms from a vapour onto a copper surface. Roll-to-roll processing then transfers the graphene lm from copper to another substrate. Polymer support H2 CH4 Graphene Released polymer support Graphene on copper foil Acidic bath Target substrate Copper foil Graphene on polymer support Graphene on target Copper foil is heated to 800-1000°C in a Adhesive 'thermal release' tape The copper is eaten away in a On heating to 90-120°C, the furnace, where hydrogen (H2) and methane is attached on top of the plastic bath lled with etchant adhesive tape unsticks, leaving gas (CH4) are piped through. Carbon atoms graphene, by applying pressure (such as ammonium persulfate, the graphene clinging to a grow as graphene lm on top of the copper. between heavy rollers. a bleaching agent and oxidant). target substrate. and deposit the graphene on a more useful Science and Technology in South Korea, prom- Institute of Technology in Atlanta takes a dif- substrate material, such as silicon dioxide (see ises a similar process that works at just above ferent tack: growing graphene ribbons directly ‘Growing Graphene Films’). Tour says a labo- room temperature4. in place on a substrate. He heats silicon carbide ratory using a US$10,000 setup can make gra- Even a graphene film grown on a surface is far — a compound of silicon and carbon that has phene sheets a few square centimetres in size. from perfect. The film forms when micrometre- been mass-produced for over a century — to And while methane is the standard reactant, sized patches of hexagonally-arrayed carbon 1,600°C, and the silicon atoms on top escape, any carbon source will do: Tour has even put atoms — each cluster a tiny fragment of graphene leaving carbon behind. To grow graphene rib- cockroach legs on top of copper and produced — sprout simultaneously from various points on bons exactly as required, de Heer notches a step a thin graphene film. the substrate. The clusters never stitch together into the silicon carbide; the graphene grows A more sophisticated version of this approach perfectly, so the final graphene sheet looks like a preferentially on the sidewall6. yields graphene on an impressive scale. In 2010, patchwork quilt of carbon, with kinks of 5- and The best graphene ribbons developed so far researchers at Sungkyunkwan University in 7-membered rings where each patch joins with are those grown molecule by molecule. Chem- Suwon, South Korea, made transparent graphene the next. The largest single perfect graphene ist Klaus Müllen’s team at the Max-Planck Insti- films up to 76 cm across by depositing carbon patch ever created is reported by nanotechnolo- tute for Polymer Research in Mainz, Germany, atoms onto copper and etching the copper away2. gist Rodney Ruoff at The University of Texas at make flawless ribbons via chemical reactions Electronics giant Samsung wants to use a reel-to- Austin, together with scientists at Texas Instru- between molecules based on hexagonal rings reel version of this technique to produce graphene ments in Dallas, who grew individual clusters up — each molecule chosen to produce an atomi- film on a continuous roll — although Seungmin to 0.5 millimetres on a side5. cally precise graphene lattice when they fuse Cho, principal research engineer at subsidiary in long chains7. Müllen says his team can now Samsung Techwin in Gyeongnam, South Korea, FROM SHEETS TO RIBBONS make perfect graphene ribbons. The catch: they says for now the company is concentrating on Graphene film conducts electrons so well, it are only a few hundred nanometres long. De making high-quality single sheets. is hard to block their flow — a problem if one Heer envisages using similar chemistry to grow Materials scientists are working on ways to lift wants to use graphene in a transistor to control thin semi-conducting electronic interconnects the graphene off the copper plate and onto insu- electrical current.
Details
-
File Typepdf
-
Upload Time-
-
Content LanguagesEnglish
-
Upload UserAnonymous/Not logged-in
-
File Pages2 Page
-
File Size-