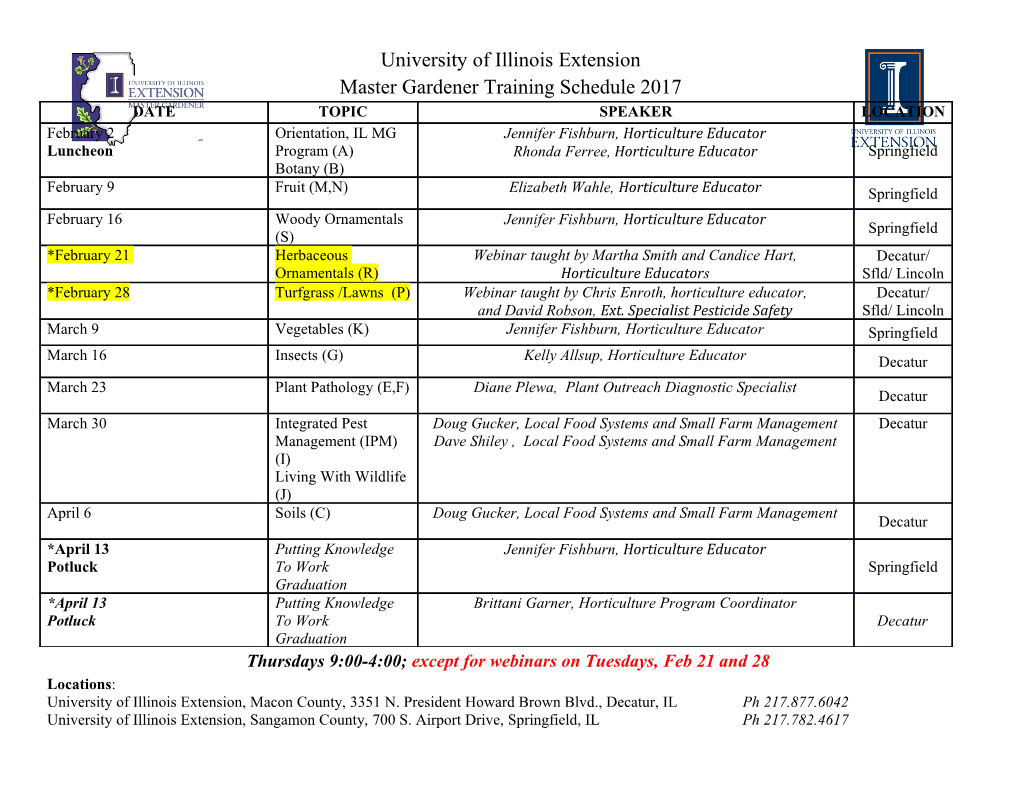
i i -1 • .1 a WQ» QSQ80-OOP30 EVALUATION ^"^ — 1 OF 1 n CHLORSNE/C^SLGRiDE BASED PROCESSES OBES FIWAL REPORT ?3 Tf «3 G? THS 7- '1 V, CfiERGV, KSfiESMSD RESOURCES, CAMA0A OSS FILE NUIS3ER : 15SQ23«0«-9130 DSS CONTRACT SERIAL KUKESB : OSCSMXKSO ••••'I P CANMET PROJECT NUMBER : 3S5-102 CANMET SGtENTiF.'C AUTHORITY : aiR. W.A, GOW 1 i i PROJECT NO. 9309 MINERALS DIVISION EVALUATION OF CHLORINE' OSIDE 8ASED PROCESSES FOR t yjJUM ORES Work on this project was conducted under the auspices of the Canada Centre for Mineral and Energy Technology, Department of Energy, Mines and Resources, Canada. ISS File Number 15 SQ 23440-9-9130 DSS Contract Serial Number OSOSO-00030 CANMET Process Number 335-102 CANMET Scientific Authority Mr. W.A. GOM , - - , . I II-M. I AI. Project No. 9309 CE Lummus November 1980 Minerals Division LU^MUS IHDEX 1.0 INTRODUCTION 2.0 OBJECTIVES OF STUDY 3.0 SUMMARY 4.0 CONCLUSIONS AND RECOK-SENDATIONS 5.0 STUDY CRITERIA 6.0 PROCESS FOR LOW GRADE ORE 6.1 Description 6.2 Basis for Capital Cost Estimate €.3 Capital Cost Estimate 6.5 Sunjaary of Operatihq Cost Estimate I • g.6 Detailed Operating Cost Estimate 6.7 Discussion 7.0 PROCESS FOR HIGH GRADE ORE 7.1 Description 7.2 Basis for Capital Cost Estimate 7.3 Capital Cost Estimate 7.4 Basis for Operating Cost Estimate 7.5 Summary of Operating Cost Estimate 7.6 Detailed Operating Cost Estimate 7.7 Discussion APPENDIX I Drawings M LUMMU3 1.0 INTRODUCTION The CE Lunwus Minerals Division was cosraissioned by The Department of Supply and Services to evaluate "Chlorine/Chloride Based Processes for Uranium Ores". The processes are designed to resove substantially all radioactive constituents from the ores to render the waste products harmless. CE Luse-us Minerals Division engineers followed the general outline contained 1n their proposal Ho. 8-981S. Experimental work carried out at the CANKET laboratories of the Department of Energy, Nines and Resources in Ottawa was used as a basis for the evaluation. At a meeting between CASKET engineers and scientists and Lunraus engineers on May 27, 1980 agreement was reached on the processes to be Investigated and CAHKET provided Lunsmis with technical literature and laboratory data. Two processes ware selected, one for a typical low grada ore (2 1b. U30g/ton ore) and one for a high grade ore (fO lbs UiQa oer tan). For the Iwi ersfe ora 5 hv&ochlcric 8cid leaching process was chosen. Tor high grads ere, a more coraplex process. Including gasecas chiorinatica, s?as selected. A second seating was held to present Lurssus1 preliminary process flew diagrams and to incorporate consents frasi CANHET scientists and engineers. Hhen the process flow diagrams were completed, they were used to generate major equipment specifications, utility diagrams and plot plans for esch process. Capital cost estimates were compiled from Information obtained from vendors for the specified equipment. The building cost estimates and the piping, electrical and instrumentation costs were developed from the plant layout. A more detailed description of the basis for the capital cost estimates Is given in Sections 6.2 and 7.2. Utility diagrams and mass balances were used for estimating utilities and consumables. A more detailed description of the basis for the operating cost estimates 1s given in Sections 6.4 and 7.4. LUMMUS 2.0 OBJECTIVES OF STUDY Concern over add drainage and radionucleide dissolution problems associated with uranium tailings disposal has preempted Investigations into improved methods of Isolating uranium, thorium and radium from tailings. Several processes to overcome these problems and produce tailings more suitable for disposal have been proposed. The primary purpose of this study MSS to develop order of magnitude capital and operating costs for two processes now being considered by CAHMET to reduce the radioactive content of mill tailings. The cost information is Intended to assist CANHET 1n selecting areas deserving further study. LUMMUS 3.0 SUGARY An evaluation of the capital and operating costs of two plants using chlorine/chlorida technology to produce yellowcake from uranium ores has been made. The results are given below: Ore Grade Low High 1)305 Content of Ore, lbs/ton 2.0 50 Ore Input, tons/day 5.200 200 H^OQ Production: lbs/day 10,000 10,000 lbs/year 3,300,000 3,300,000 Process Used Hydrochloric Chlorination Acid Leach and Hydrochloric Acid Leach Direct Capital Cost $ 138,800.000 67,000,000 Direct Capital Cost, A? aa ?n •sn Direct Operating Cost: S/year 22,540,000 14,050,000 S/ton ore 13.13 213.00 i S/lb U308 6.83 4.26 ^SHI IM LUMMUS 4.0 CONCLUSIONS AND RECOMMEHDATIOSS 4.1 Low Grade Or3 It hss been demonstrated that the hydrochloric acid leaching process will extract uranium, thorium and radium to meet the environmental criteria of 15 picocuries (pCi) per gran in the leach residue wastes. Sulphuric acid 1s required to regenerate hydrochloric acid from spent leach liquor. For ores containing pyrite, the sulphuric add can be produced on site by floating the pyrite and roasting it. By removing the pyrite, formation of sulphuric acid 1n the tailings 1s prevented and long term lime treatment of tailings effluents 1s not necessary. High extraction of uranium, in the order of 98%, 1s possible. Before considsring a conmercial hydrochloric acid leach plant for low grade uranium ores it would be necessary to operate an integrated fi-ilnf" n'i ant 4*n HpkuaJ/in ali W ** * "~" """" a cost estimate. In order to achieve a wall designed pilot plant and minimize unnecessary expenditures during the pilot stags it is reconffiended that semi-continuous coordinated bench scale tests be carried out. These should include the following process segments: 1. Hydrochloric acid leaching of pyrite flotation tailings and roaster residue. 2. Solvent extraction of uranium; precipitation, dewatering and drying of yellowcake. 3. Solvent extraction of thorium" from uranium raffinate; precipitation, dewatering and drying of thorium oxalate. 4. Extraction of radium by two-stage 1on exchange. 5. Regeneration of hydrochloric add with sulphuric acid. Grinding, pyrite flotation and roasting can be carried out separately to provide feed for the leaching circuit. 4.2 High Grade Ore The chlorination process has the potential to substantially decrease radium levels in tailings wastes. 4.0 CONCLUSIONS ASP RECOMMENDATIONS 4.2 High Grade Ore - Continued However, at the time this study was initiated, it had not been demonstrated 1n the laboratory that radium levels in the tailings waste could be reduced to a level approaching the desired standard of 15 picocuries per gram. Uranium extraction 1s quite high and In the order of 98%. Capital and operating costs for the process, based on costs per ton of ore, are quite high. Costs might be reduced substantially by preconcentratton, for example, by radioactive sorting, screening, flotation, gravity concentration or a combination of these. Ths chlori nation process has not been completely tested in the laboratory. It is rsccssnended that bench scale test work be continued. Tha crimary objective o? continuous usavk should ht. to increase radiua extraction. This objective might be achieved by: 1. Adjusting chlorination conditions, preferably in a fluid bed, rather than static reactor. 2. Grinding the calcine product prior to leaching to overcome possible.sintering effects. 3. Higher concentration of hydrochloric acioi in leaching and/or pressure leaching at higher temperatures. The process could be simplified 1f all the uranium were recovered In the chiorination gas product. This would eliminate the uranium recovery section in the chlorination residue leaching circuit. If satisfactory radium extraction is achieved, test work should also be carried out in other areas which have not been adequately investigated, including the following: 1. Chlorfne regeneration and recovery 2. Arsenic separation 3. Caustic leaching of oxide residues. Evaluation of these test results would be necessary before considering a pilot plant program. LUMMUS 5.0 STUDY CRITERIA The following criteria were used as a basis for evaluation of the selected processes: 1. Radium to be extracted fn s form suitable; for long term storage. Tailings radioactivity objective: Lew grade ore: 15 picocuries par gram (pC1/g) High grade ore: as low as practically possible. 2. Thorium extraction to be as high as practically possible on ores containing thorium. 3. High uranium extraction, preferably about 98X. 4. Minimum effect on the environment from toxic and undesirable elements 1n the ore, or Introduced in the process, e.g. sulphuric acid, nitrate, chloride and arsenic. 5. Safe working environment achievable.in the plant. 6. Proven unit processes to b-a used as far as possible. 10 7. Optimum energy utilization. ft. Minimum capital and operating costs within the restraints of other criteria. For study purposes, the following ore analyses were assumed: Analysis, % Elejnent Low Grade High Grade U308 0.1 2.5 Th 0.44 0.01 Ra 350 pC1/g 6,000 pCI/g Fe 3.5 3.6 Si 39 27 S 3.0 1.2 As 4.0 The low grade analysis is typical of Elliot Lake ores. The high grade analysis is more or less *.ypical of Saskatchewan ores; however, these show wide variations in mineral coraposition. %,fc .; • Most high grade ores 1n Saskatchewan contain Insignificant concentrations of thorium. Therefore, thorium removal has not been inciuoed in the process for high grade ore. ^ LLMMUS 6.0 PROCESS FOR LOW GRADE ORE (0.1X U3O8) 6.1 Process Description A general process flow diagram for the low grade ore 1s shown on [Yawing No. SKD-9309-001C0-2 in the Appendix. The hydrochloric acid leaching process for low grade uranium ores 1s a combination of the following process steps: 1.
Details
-
File Typepdf
-
Upload Time-
-
Content LanguagesEnglish
-
Upload UserAnonymous/Not logged-in
-
File Pages43 Page
-
File Size-