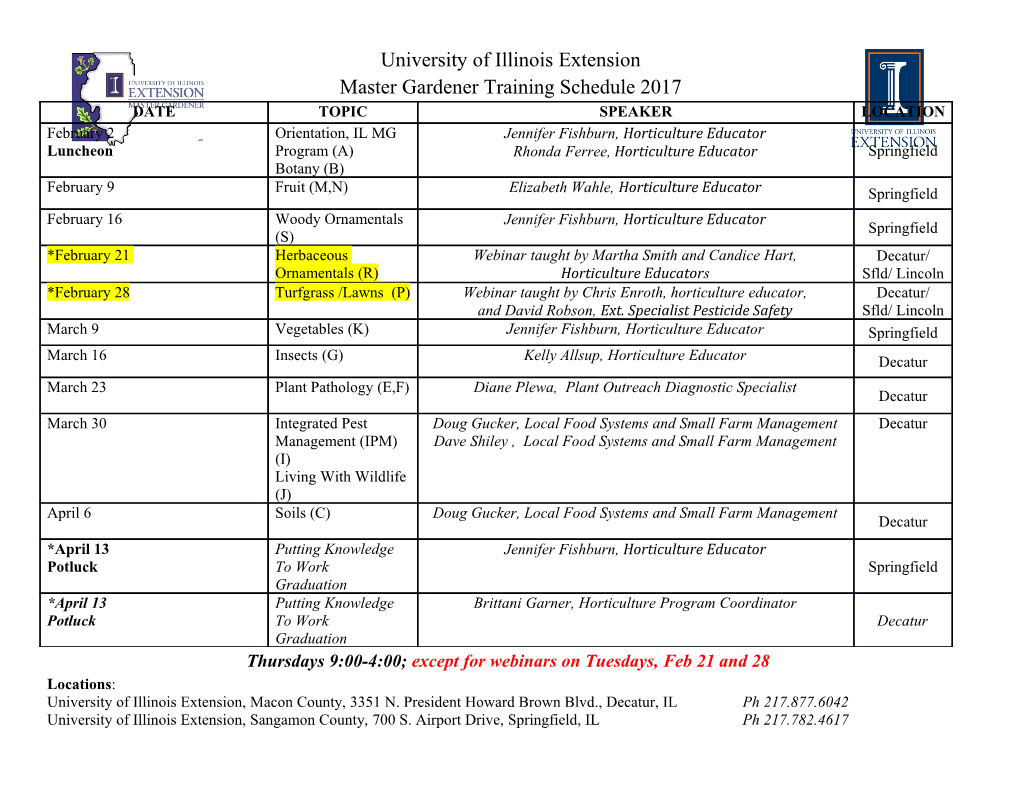
Graduate Theses, Dissertations, and Problem Reports 2012 Coal Liquefaction Process Development Christopher L. Yurchick West Virginia University Follow this and additional works at: https://researchrepository.wvu.edu/etd Recommended Citation Yurchick, Christopher L., "Coal Liquefaction Process Development" (2012). Graduate Theses, Dissertations, and Problem Reports. 4943. https://researchrepository.wvu.edu/etd/4943 This Dissertation is protected by copyright and/or related rights. It has been brought to you by the The Research Repository @ WVU with permission from the rights-holder(s). You are free to use this Dissertation in any way that is permitted by the copyright and related rights legislation that applies to your use. For other uses you must obtain permission from the rights-holder(s) directly, unless additional rights are indicated by a Creative Commons license in the record and/ or on the work itself. This Dissertation has been accepted for inclusion in WVU Graduate Theses, Dissertations, and Problem Reports collection by an authorized administrator of The Research Repository @ WVU. For more information, please contact [email protected]. Coal Liquefaction Process Development Christopher L. Yurchick Dissertation submitted to the College of Engineering and Mineral Resources at West Virginia University in partial fulfillment of the requirements for the degree of Doctor of Philosophy in Chemical Engineering Alfred Stiller, Ph.D., Chair Christopher J. Bise, Ph.D. Eung H. Cho, Ph.D. Rakesh K. Gupta, Ph.D. Eric Johnson, Ph.D. Department of Chemical Engineering Morgantown, West Virginia 2012 Keywords: Coal Liquefaction; Pitch; Coke; Centrifugation; Distillation; Process Development Copyright 2012 Christopher L. Yurchick ABSTRACT Coal Liquefaction Process Development Christopher L. Yurchick The traditional method of liquefying coal operates at extreme conditions consisting of hydrogen pressures of over 2000 pounds per square inch and temperatures of over 450°C. The elevated hydrogen pressure is necessary to hydrogenate the reaction mixture and liquefy the coal molecules. As a result, the processing equipment is very expensive and safety is a major concern. The coal liquefaction process invented at West Virginia University does not use hydrogen overpressure and operates below 500 pounds per square inch. The WVU process has produced 4500 pounds of cleaned de-ashed coal extract referred to as centrate. The centrate was processed into coal tar binder pitch by Koppers Inc. and finally into electrodes for the steel industry by GrafTech International Ltd. The electrodes were tested and passed all of the commercialization tests. Quantex, a Canadian company, licensed the technology from the university in 2007 with the intention of commercializing the process. However, the process had several deficiencies to overcome before it could be economically viable and move towards commercialization. The centrifuge system removes ash and other solid materials from the mixture after the coal has been liquefied. In the process existing in 2007, the centrifuge residue, or tails, contains only 20% by weight of the ash material with the remaining 80% consisting of valuable products or unreacted coal. Without first increasing the efficiency of ash removal from the coal either before or after the liquefaction reaction, the process cannot be economically viable and is unable to be commercialized. Another drawback of the original process is the reaction and centrifuge systems were not designed or operated to produce reliable mass balance results. The reaction system was redesigned and constructed incorporating the previously redesigned centrifugation system to produce clean, de-ashed centrate and other products from the raw materials. A vacuum distillation system was designed and constructed that produces quality pitches and condensed liquid volatiles from the clean, de-ashed centrate produced from coal in the previous reaction step. The coking system was designed and constructed to process the coal derived pitches into commercial grade coke and additional condensed volatiles. Each of the three operating systems produces reliable and repeatable mass closure results for individual experiments. All of the products can be collected and samples taken for further analytical analysis. A complete mass balance analysis for the overall process was performed from the raw material through the products produced. The end products were subjected to and passed testing for commercial standards. The potential for commercialization has been enhanced by this research and the technology now can be properly analyzed. iv Dedicated to my beautiful wife Rebecca, whose love and support made this work possible. Also dedicated to my late grandfather Stanley Gawlik for all of the knowledge, love, and support that he provided during my childhood. v ACKNOWLEDGEMENTS I would like his express my greatest appreciation to my research advisor, mentor, and friend Dr. Alfred Stiller. He did, in fact, teach me how to observe amongst many other things. He also provided me with the tools to do work that I love for the rest of my life. I would like to thank the members of my committee which includes Dr. Christopher J. Bise, Dr. Eung H. Cho, Dr. Eric Johnson, and Dr. Rakesh K. Gupta who is also the chairman of the Chemical Engineering Department for their guidance and patience. Furthermore, I would like to thank Dr. Charter Stinespring for all of his assistance. I would like to thank everyone in the Carbon Products group along with the individuals that assisted me in the construction and operation of the processes contained in this dissertation. This would include Elliot Kennel, Terry Ryan, Jeremy Hardinger, and Femi Olajide. I would particularly like to thank Tony Golden and Benson Njoroge who helped with the construction and operation of each system for this research. Furthermore, I would like to thank Jim Hall and Cliff Judy with their help in construction the systems. I would like to thank Norm Caplin and Coal Innovations for providing the ability to perform research at their facility in Stoystown, PA. I would like to thank the Chemical Engineering Department, the Carbon Products group, and Quantex Energy for the financial support to construction the necessary systems. Finally, I would like to thank all of my family and friends who provided love, support, and encouragement throughout the years. vi vii DISCLAIMER The document is not only a dissertation for the requirements of a Doctoral degree, it is also a legal document for the Technology Transfer division of West Virginia University since this is a licensed process. Therefore, it contains all of the information in great detail so that the legalities of ownership and property rights can be distinctly discerned. viii TABLE OF CONTENTS ABSTRACT ............................................................................................................................. iii ACKNOWLEDGEMENTS....................................................................................................... vi DISCLAIMER ........................................................................................................................ viii TABLE OF CONTENTS .......................................................................................................... ix LIST OF FIGURES .................................................................................................................xvi LIST OF TABLES .................................................................................................................... xx CHAPTER I: INTRODUCTION ................................................................................................1 1.1 History of the Carbon Products Group .....................................................................................1 1.2 Statement of the Problem ........................................................................................................6 1.3 Proposed Research ..................................................................................................................7 1.4 Research Objectives ................................................................................................................9 1.4.1 Primary Objectives ............................................................................................................ 10 1.4.2 Secondary Objectives ........................................................................................................ 12 1.4.3 External de-ashing process secondary objectives ............................................................... 13 1.4.4 Internal de-ashing process secondary objectives ............................................................... 15 1.4.5 Reaction process secondary objectives............................................................................... 15 1.4.6 Vacuum distillation process secondary objectives: ............................................................. 16 1.4.7 Coking process secondary objectives: ................................................................................ 17 1.5 Accomplishing the Objectives ............................................................................................... 17 1.6 State of the Processes When This Research Began ................................................................ 19 1.6.1 Summary 19 1.6.2 Pre-reaction De-ashing of Sub-bituminous Coal ................................................................ 20 1.6.3 The
Details
-
File Typepdf
-
Upload Time-
-
Content LanguagesEnglish
-
Upload UserAnonymous/Not logged-in
-
File Pages380 Page
-
File Size-