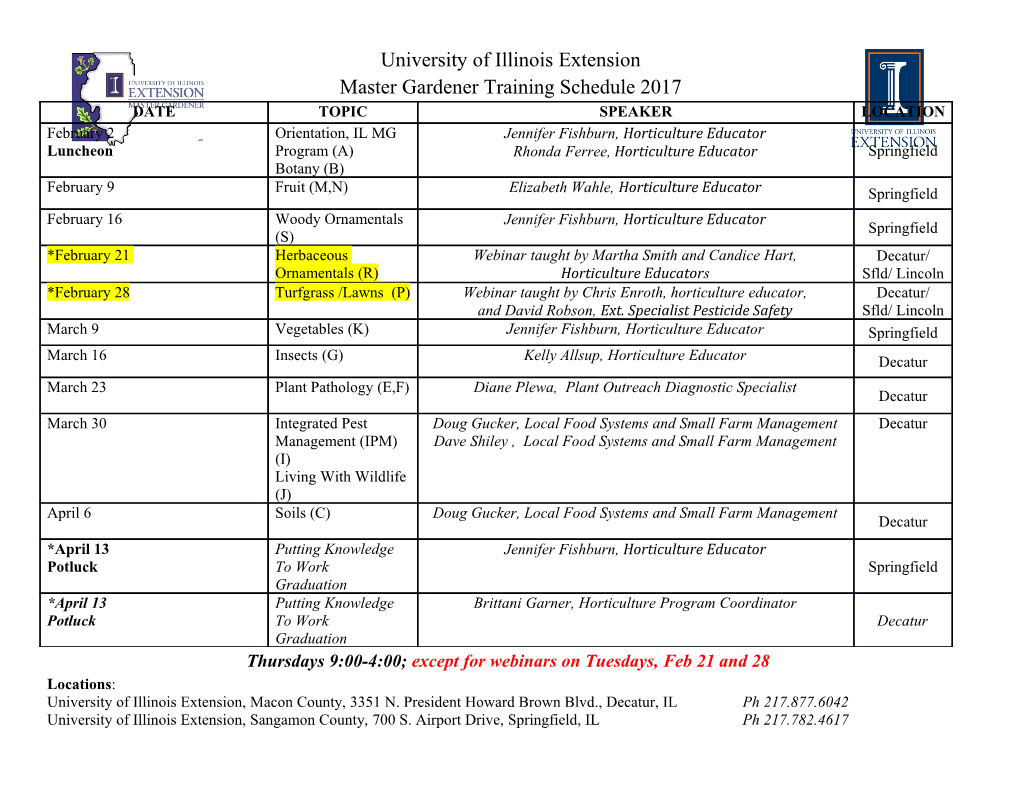
Politecnico di Torino Department of Mechanical and Aerospace Engineering Ph.D. degree in Mechanical Engineering Design and development of prognostic and health management system for fly-by-wire primary flight control electrohydraulic servoactuators Candidate: Andrea Mornacchi Thesis advisor: Prof. G. Jacazio Thesis submitted in 2016 Allegato n.6 COMMISSIONE GIUDICATRICE ll dott. Andrea MORNACCHI ha discusso in data ha discusso in data 29 aprile 2016 presso il Dipartimento di lngegneria Meccanica e Aerospaziale del Politecnico di Torino la tesidi Dottorato avente il seguente titolo: Design and development of prognostic and health management system for fly-by- wire primary fly control electrohydraulic servoactuators Le ricerche oggetto della tesi sono eccellente livello. Le metodologie appaiono molto buone. I risultati sono interessanti ed analizzati con elevato senso critico. Nel colloquio il candidato dimostra ottima conoscenza delle problematiche trattate. La Commissione unanime giudica estremamente positivo il lavoro svolto e propone che al dott. Andrea MORNAGCH| venga conferito il titolo di Dottore di Ricerca Data, 29 aprile 2016 Prof. Carlo Ferraresi (Presidente) Prof. Stefano Beretta (Componente) Prof. Enrico Ravina (Segretario) iii Prediction is very difficult, especially if it’s about the future. Nils Bohr Abstract Electro-Hydraulic Servo Actuators (EHSA) is the principal technology used for primary flight control in new aircrafts and legacy platforms. The devel- opment of Prognostic and Health Management technologies and their appli- cation to EHSA systems is of great interest in both the aerospace industry and the air fleet operators. This Ph.D. thesis is the results of research activity focused on the devel- opment of a PHM system for servovalve of fly-by-wire primary flight EHSA. One of the key features of the research is the implementation of a PHM sys- tem without the addition of new sensors, taking advantage of sensing and information already available. This choice allows extending the PHM capa- bility to the EHSAs of legacy platforms and not only to new aircrafts. The enabling technologies borrow from the area of Bayesian estimation theory and specifically particle filtering and the information acquired from EHSA during pre-flight check is processed by appropriate algorithms in order to obtain relevant features, detect the degradation and estimate the Remaining Useful Life (RUL). The results are evaluated through appropriate metrics in order to assess the performance and effectiveness of the implemented PHM system. The major objective of this contribution is to develop an innovative fault diagnosis and failure prognosis framework for critical aircraft components that integrates effectively mathematically rigorous and validated signal pro- cessing, feature extraction, diagnostic and prognostic algorithms with novel uncertainty representation and management tools in a platform that is com- putationally efficient and ready to be transitioned on-board an aircraft. Keywords: Prognostics and Health Management (PHM), Condition Based Maintenance (CBM), fly-by-wire primary flight control, ElectroHydraulic ServoValve (EHSV) vii Contents 1 Introduction to PHM 1 1.1 Historical perspective . .2 1.2 Prognostics and health management . .4 1.3 Automatic diagnostic . .7 1.3.1 Requirements and performance metrics . .8 1.3.2 Alarm bounds approach . 10 1.3.3 Data-based approach . 11 1.3.4 Data-driven approach . 13 1.3.5 Model-based approach . 15 1.4 Prediction of residual useful life . 18 1.4.1 Requirements and performance metrics . 19 1.4.2 Model-based approach . 21 1.4.3 Probability-based approach . 23 1.4.4 Data-driven approach . 24 1.5 PHM for flight control actuators . 25 2 Reference servoactuator 29 2.1 Flight control system overview . 30 2.1.1 Primary flight control systems . 32 2.1.2 High lift control systems . 33 2.2 Boeing 777 flaperon EHSAs . 34 2.2.1 Hydraulic manifold . 35 2.2.2 ElectroHydraulic Servovalve . 37 3 Servovalve degradations 39 3.1 Selected degradations . 40 3.2 Reduction magnetomotive force . 41 3.3 Contamination of nozzles and filter . 42 3.4 Yield feedback spring . 43 3.5 Feedback spring backlash . 44 3.6 Friction force variation . 45 ix x Contents 3.7 Radial gap increase . 45 4 Mathematical model 47 4.1 Model structure . 48 4.2 Actuator . 50 4.2.1 Coulomb friction . 53 4.2.2 Actuator stoke limits . 56 4.3 Servovalve . 57 4.3.1 Discharge coefficient . 70 4.4 Surface . 71 4.5 Controller . 72 4.6 Position transducer . 74 4.7 Aerodynamic force . 74 4.8 Oil Properties . 75 5 Mathematical model validation 79 5.1 Test Bench . 80 5.2 Open loop tests . 82 5.3 Close loop tests . 84 5.4 Validation results . 85 6 PHM strategy 87 6.1 Available information . 88 6.2 Adopted strategy . 89 6.2.1 Implemented command . 91 6.3 PHM algorithm . 94 6.4 Operative scenario . 96 7 Features extraction 99 7.1 Extracted features . 100 7.1.1 Position features . 101 7.1.2 Current features . 103 7.2 Influence of operative conditions . 105 7.2.1 Fluid parameters . 106 7.2.2 Noise and environmental disturbances . 117 7.3 Influence of manufacturing tolerances . 120 7.4 Features evaluation . 123 7.4.1 Reduction magnetomotive force . 124 7.4.2 Contamination of nozzles . 126 7.4.3 Variation of the stiffness of the feedback spring . 130 Contents xi 7.4.4 Increase of the backlash between spool and feedback spring . 132 7.4.5 Variation of the friction force between spool and sleeve 133 7.4.6 Increase of the radial gap . 136 7.4.7 Summary . 138 8 Fault diagnosis 141 8.1 Fault diagnosis requirements . 142 8.2 Fault diagnosis techniques . 143 8.3 Alarm bounds approach . 144 8.3.1 Results overview . 150 8.3.2 Summary . 163 8.4 Probability Density Function approach . 164 8.4.1 Detection with PDF from real-data . 165 8.4.2 Detection with PDF from particle filter . 167 8.4.3 Result overview . 170 8.4.4 Summary . 181 8.5 Summary . 184 9 Fault classification 187 9.1 Classification technique . 187 9.2 Classification of the first degradation . 189 9.3 Classification of additional degradations . 193 9.4 Summary . 197 10 Residual useful life estimation 199 10.1 RUL estimation technique . 200 10.2 Degradation model fitting . 201 10.3 RUL estimation . 203 10.4 Results overview . 206 10.5 Evaluation . 209 10.6 Summary . 213 11 Conclusion 215 11.1 Summary . 215 11.2 Future developments . 217 A Random pattern generator 219 Bibliography 223 List of Figures 1.1 An integrate PHM approach . .5 1.2 PHM cycle . .5 1.3 ISO 13374-1 processing model . .8 1.4 Alarm bounds . 10 1.5 Neural network example . 12 1.6 Neural network decision regions . 13 1.7 Detection using PDF comparison . 15 1.8 Prognosis technical approaches . 19 1.9 Prognosis result example . 20 1.10 PHM system proposed by Byington et al . 26 2.1 Position of the three principal axes . 30 2.2 The fly-by wire EHSA and its interactions . 32 2.3 Layout of the primary controls of Boeing 777 ......... 33 2.4 Boeing 777 flaperon . 34 2.5 Flaperon scheme . 35 2.6 Flaperon manifold scheme . 36 2.7 EHSV scheme . 37 3.1 Selected degradations . 41 3.2 Nozzle clogging . 43 3.3 Yield feedback spring . 43 3.4 Feedback spring backlash . 44 3.5 Friction force variation . 45 3.6 Radial gap increase . 46 4.1 Mathematical model layers . 49 4.2 EHSA model scheme . 50 4.3 Actuator lumped model . 50 4.4 Rod free body diagram . 52 4.5 Sleeve free body diagram . 53 xiii xiv List of Figures 4.6 Actuator seals . 54 4.7 Coulomb friction . 56 4.8 Stroke limits - saturation signal . 56 4.9 Stroke limits - subsystem . 57 4.10 Model EHSV scheme . 58 4.11 Torque motor equivalent circuit . 58 4.12 Distribution of air-gaps . 61 4.13 Flapper free body diagram . 65 4.14 Spool free body diagram ..
Details
-
File Typepdf
-
Upload Time-
-
Content LanguagesEnglish
-
Upload UserAnonymous/Not logged-in
-
File Pages249 Page
-
File Size-