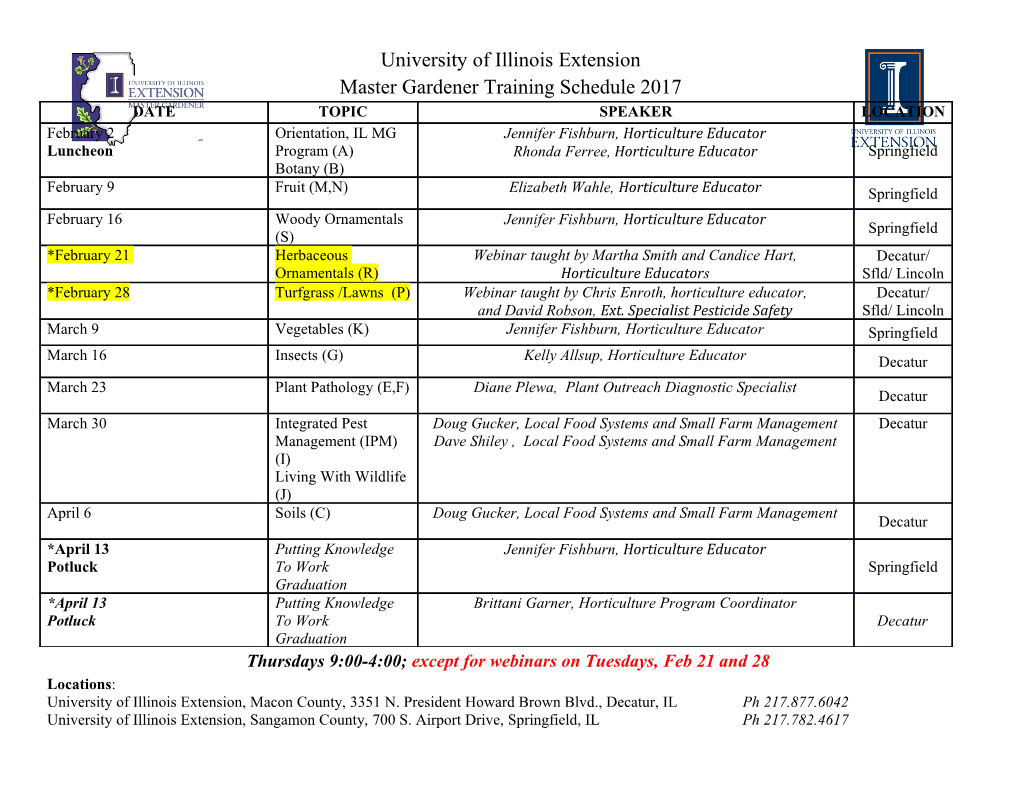
Six Sigma reduces candy defects for a UK food manufacturer • Recently, a UK-based producer of cough drops tested the effectiveness of the DMAIC approach for cutting manufacturing costs. Tools and Techniques for Quality • Using the DMAIC approach, the company saved £290,000 • The company also reduced its scrap rate from 1 in every 5 cough drops to 1 Control and Improvement in 10,000 or more. Chapter 3 • More importantly the organization now has a much Better understanding of the impact of variation. 2 – 1 2 – 2 Chance and Introduction AssignaBle Causes of The Control Chart Quality Variation Implementing SPC in a The Rest of the Quality Improvement An Application of SPC Learning OBjectives Magnificent Seven Program 1. Understand chance and assignaBle causes of variaBility in a process 2. Explain the statistical Basis of the Shewhart control chart Applications of SPC & 3. Understand the Basic process improvement tools of SPC: the histogram or stem - Quality Improvement and-leaf plot, the check sheet, the Pareto chart, the cause-and-effect diagram, the Tools in Transactional defect concentration diagram, the scatter diagram, and the control chart and Service 4. Explain how sensitizing rules and pattern recognition are used in conjunction with Discussion topics Businesses control charts 2 – 3 2 – 4 1 Introduction Statistical Process Control (SPC) § SPC is one of the greatest technological developments of the § A process must Be capaBle of operating with little variaBility twentieth century Because around the target or nominal dimensions of the product’s quality § it is Based on sound underlying principles, characteristics in order to meet or exceed customer expectations. § is easy to use, § SPC is a powerful collection of proBlem-solving tools useful in § has significant impact, and achieving process stability and improving capability through the § can Be applied to any process. reduction of variaBility. § Its seven major tools are § A process is an organized sequence of activities that produces an § Histogram or stem-and-leaf plot output (product or service) that adds value to the organization. § Check sheet § Pareto chart § While we traditionally think of SPC as Being applied to § Cause-and-effect diagram manufacturing processes, it can really Be applied to any kind of § Defect concentration diagram process including service processes. § Scatter diagram § Control chart 2 – 5 2 – 6 SPC Chance and § “The Magnificent Seven” are an important part of SPC But they Introduction AssignaBle Causes of The Control Chart comprise only the technical aspects. Quality Variation § The proper deployment of SPC helps create an environment in which all individuals in an organization seek continuous Implementing SPC in a improvement in quality and productivity. The Rest of the Quality Improvement An Application of SPC Magnificent Seven Program § This environment is Best developed when management Becomes involved in the process. Applications of SPC & Quality Improvement Tools in Transactional and Service Discussion topics Businesses 2 – 7 2 – 8 2 Chance and AssignaBle Causes of Chance and AssignaBle Causes of Quality Variation Quality Variation § In any production process, regardless of how well designed or § Other kinds of variaBility in key quality characteristics usually carefully maintained it is, a certain amount of inherent or natural arises from three sources: variaBility will always exist. § Improperly adjusted or controlled machines, § This natural variaBility or “Background Noise” is the cumulative effect of § Operator errors, or many small, essentially unavoidaBle causes. § Defective raw material. § In the framework of statistical quality control, this natural variaBility is often called a “staBle system of chance causes.” § Such variaBility is generally large when compared to the background noise, and it usually represents an unacceptable level § A process that is operating with only chance causes of variation of process performance. present is said to be in statistical control. § These sources of variaBility that are not part of the chance cause pattern are referred to as assignable causes of variation. § A process that is operating in the presence of assignaBle causes is said to Be an out-of-control process. 2 – 9 2 – 10 Chance and AssignaBle Causes of Quality Variation The terminology “chance” and “assignaBle causes” was developed By Shewhart. Today, some writers use the terminology “common cause” instead of “chance cause” and “special cause” instead of “assignaBle cause”. 2 – 11 2 – 12 3 SPC Chance and § A major oBjective of statistical process control is to quickly detect Introduction AssignaBle Causes of The Control Chart the occurrence of assignaBle causes of process shifts so that Quality Variation investigation of the process and corrective action may Be undertaken before many nonconforming units are manufactured. Implementing SPC in a § The control chart is an on-line process-monitoring technique The Rest of the Quality Improvement An Application of SPC Magnificent Seven widely used for this purpose. Program § Control charts may also Be used § To estimate the parameters of a production process, and, through this Applications of SPC & information, to determine process capaBility. Quality Improvement Tools in Transactional § To provide information useful in improving the process. and Service § To reduce variaBility as much as possiBle. Discussion topics Businesses 2 – 13 2 – 14 The Control Chart The Control Chart § The control chart is a graphical display of a quality characteristic § A point that plots outside of the control limits is interpreted as that has Been measured or evidence that the process is out of control, and investigation and computed from a sample versus the sample numBer or time. corrective action are required to find and eliminate the assignable cause or causes responsiBle for this Behavior. § The chart contains a center line that represents the average value § Even if all the points plot inside the control limits, if they Behave of the quality characteristic corresponding to the in-control in a systematic or non-random manner, then this could Be an state. indication that the process is out of control. § Two other horizontal lines, called § If 18 of the last 20 points plotted aBove the center line But Below the upper the upper control limit (UCL) and control limit and only two of these points plotted Below the center line But the lower control limit (LCL), are also shown on the chart. These aBove the lower control limit, we would Be very suspicious that something control limits are chosen so that if was wrong. the process is in control, nearly all § If the process is in control, all the plotted points should have an essentially of the sample points will fall between them. random pattern. 2 – 15 2 – 16 4 Control Chart Example Control Chart § In semiconductor § manufacturing, an important Every hour a sample of five wafers is taken, the average flow faBrication step is width is computed, and plotted on the chart. photolithography. x=1.5 microns, σ=0.15 microns, n=5 § The developing process is typically followed By a hard σ = σ =0.15/ 5=0.0671 bake process to increase resist x n adherence and etch resistance. § If the process is in control with a mean flow width of 1.5 microns § An important quality § Using Central Limit Theorem, is approximately normally distriButed, we x characteristic in hard Bake is the would expect 100(1-α)% of the sample means to fall Between flow width of the resist x 1.5 + Zα/2(0.0671) and 1.5 - Zα/2(0.0671) § Suppose that the flow width can § Choose Z =3 be controlled at a mean of 1.5 α/2 microns, and it is known that § Therefore, UCL=1.5 + 3(0.0671) = 1.7013 & LCL = 1.5 - 3(0.0671) = 1.2987 the standard deviation of flow width is 0.15 microns. 2 – 17 2 – 18 Control Chart § The width of the control limits is inversely proportional to the sample size n for a given multiple of sigma. § Choosing the control limits is equivalent to setting up the critical region for testing the hypothesis Three Sigma Control Chart H0: μ = 1.5 H1: μ ≠ 1.5 where � = 0.15 (known) The “Sigma” in the three sigma control chart refers to the § Essentially, the control chart tests this hypothesis repeatedly at standard deviation of the statistic plotted on the chart (i.e. ), σ different points in time. x not the standard deviation of the quality characteristics. σ x 2 – 19 2 – 20 5 Control Chart Shewhart Control Chart Note that “sigma” refers to the standard deviation of the § This general theory of control charts was first proposed By Walter σ statistic plotted on the chart (i.e., ), not the standard x A. Shewhart deviation of the quality characteristic. § � - sample statistic that measures some quality characteristic of interest § μ� – mean of � § �� – standard deviation of � § L – “distance” of the control limits from the center line, expressed in standard deviation units. 2 – 21 2 – 22 Process Improvement using Control Out-Of-Control-Action plan (OCAP) Chart § Most processes do not operate § Developing an effective system for corrective action is an in a state of statistical control. essential component of an effective SPC implementation. § Consequently, the routine and attentive use of control charts § A very important part of the corrective action process associated will identify assignaBle causes. If with control chart usage is the OCAP. these causes can Be eliminated from the process, variaBility will § An OCAP be reduced and the process will § is a flow chart or text-based description of the sequence of activities that be improved. must take place following the occurrence of an activating event. § The control chart will only § consists of checkpoints, which are potential assignable causes, and detect assignable causes. terminators, which are actions taken to resolve the out-of-control Management, operator, and condition, preferaBly By eliminating the assignaBle cause. engineering action will usually § Is a living document in the sense that it will Be modified over time as more be necessary to eliminate the knowledge and understanding of the process is gained.
Details
-
File Typepdf
-
Upload Time-
-
Content LanguagesEnglish
-
Upload UserAnonymous/Not logged-in
-
File Pages20 Page
-
File Size-