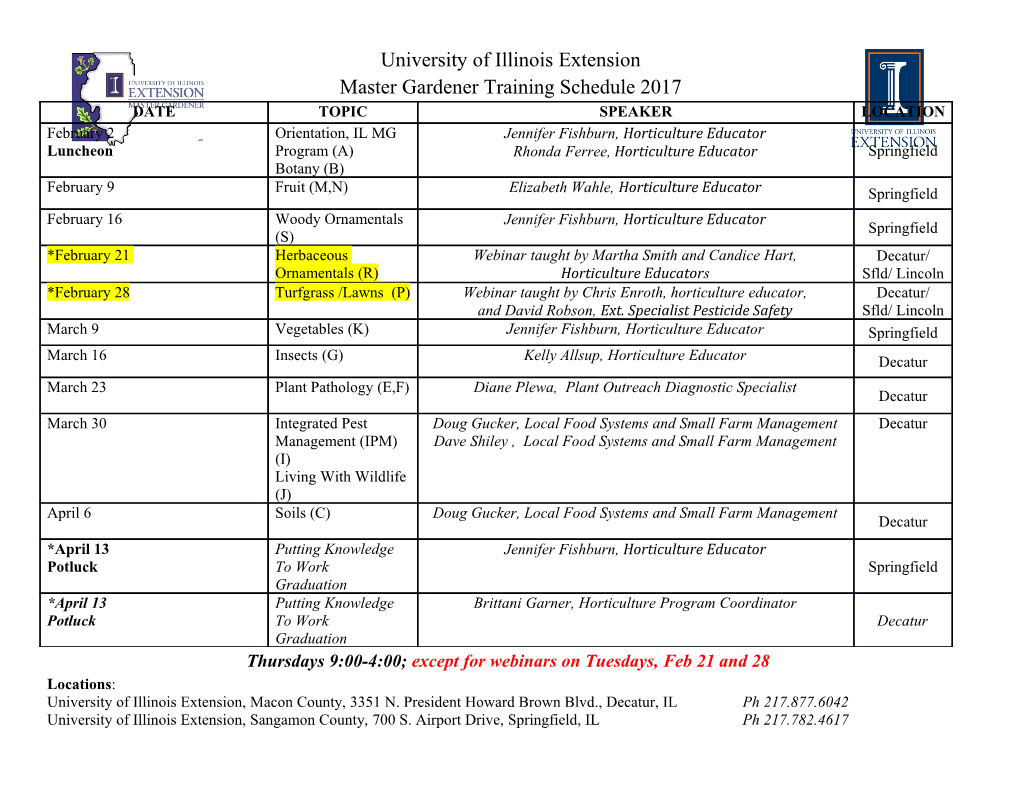
Sensors Industrial Switches and Safety Technology Products WARNER ELECTRIC Sensors, Industrial Switches and Safety Technology Products Warner Electric has many years of experience in applying sensors in motion control applications. Warner Electric’s broad range of innovative and technologically advanced product range offers our customers the exact solution to satisfy their sensing applications. Our full product range is available through more than 800 distributor locations, throughout the United States, Canada and Mexico. Local Sales Support is provided by a well trained sales force that is backed up by Application Engineering providing immediate technical support. Non-Contact Sensors Photoelectric Sensors Ultrasonic Sensors Inductive Proximity Sensors Capacitive Sensors Magnetic Sensors Industrial Switches Limit Switches Foot Switches Cable Pull Switches Safety Technology Products Safety Interlocks Approvals and Certification Cable Pull Switches Each model is individually identified with its own certification. Coded Magnetic Monitoring Systems Documentation is available upon request. ©2004 Warner Electric, Inc. For Application Assistance Call 1-800-451-8279 or Fax 1-815-389-6678 Contents Standard Sensor Products Choosing the Correct Sensor . 2 Photoelectric Sensors Identification Code . .3 OR20 Series . .4 OR90 Series . .5 MCS-144 / 159 / 165 . .6 MCS-500 Series . .7 Compact Series . .8 OT18 Series . .9 MCS-638 Series . .11 Ultrasonic Sensors Identification Code . .12 With Analog Output . .13 With Isolated Solid State Relay Outputs . .15 Inductive Proximity Sensors Identification Code . .17 4mm / M4 / M5 / M8 / M12 / M18 / M30 Voltage 10-30 DC, Integral Cable . .18 M8 / M12 / M18 / M30. Voltage 10-30 DC, Quick Disconnect . .20 M12 / M18 / M30. Voltage AC, Integral Cable and Quick Disconnect . .22 Capacitive Sensors Identification Code . .17 M12 / M18 / M30 / M32 / 34mm dia Integral Cable and Quick Disconnect. Voltage DC and AC. .24 Magnetic Sensors . .26 Sensor Controls MCS 149 / 680 Series . .28 Thermoplastic Limit Switches Body Styles Ti2 / Bi / I88 / ENK . .29 Metal Limit Switches Body Style ENM2 . .37 Foot Switches Single, Two and Three Pedal . .39 Safety Technology Products Safety Position Interlocks SKT / SKI Body Style . .42 SK / SKC Body Style . .44 Important Safety Warning... GC Body Style . .45 The Non Contact sensors described in this Safety Hinge Switch . .46 catalog do NOT include the self-checking I88 Style Interlocks . .53 redundant circuitry necessary to allow them Solenoid Locking to be used in personnel safety applications. SLK Spring and Magnetic Lock (Plastic Housing) . .54 A sensor failure or malfunction can result in SLM Spring and Magnetic Lock (Metal Housing) . .55 either an energized or a de-energized output condition. Coded Magnetic Monitoring Systems Never use these non contact products as MUZ 602 / 202 . .56 sensing devices for personnel protection. Coded Magnet Sensors . .57 Their use as safety devices may create an Cable Pull Switches unsafe condition which could lead to serious Single . .58 bodily injury or death. Two Directional to 250 ft. .60 Glossary of Terms . .61 Index to Part Numbers . .62 1 For Application Assistance Call 1-800-451-8279 or Fax 1-815-389-6678 Choosing the correct sensor for your application Many situations have developed that have 2 – What is the environment? AC circuits generally come in two types, resulted in the loss of valuable production solid state and electromechanical relays. hours, due to not enough time being taken Consider the surrounding and working Finally remember, any problems or to choose the correct sensor for the conditions, steam coolant, metal surfaces, questions, call Sensor Application Support application. temperature both high and low, all can for help. These situations can be avoided if each influence the performance of the sensor. application is systematically approached in Ensure not only that the sensor can detect the following manner. the target cleanly and clearly, but how it will be able to withstand maintenance and Which sensor? wash–down situations. APPLICATION ASSISTANCE Sensing variables/least to most affected Four basic questions should be asked: relating to ambient conditions. CALL Magnetic 1-800-451-8279 1 – What are you sensing? Inductive Proximity Photoelectric – Through-Beam FAX 2 – What is the environment? Ultrasonic – Proximity Photoelectric – Convergent Beam 1-815-389-6678 3 – What is your input voltage? Photoelectric – Retroreflective Photoelectric – Background Suppression Photoelectric – Diffuse Reflective 4 – What are you controlling? Capacitive Proximity 3 – What is your input 1 – What are you sensing? voltage? It is extremely important to know what the material is you are sensing as the material A large factor relating to the exact sensor or relates directly to the type of sensor chosen. sensor system you might eventually choose. A lot of the smaller type sensors need to At this stage, it is also relevant to consider have power supplies in order that the cor- what distance away from the target would rect stable D.C. voltage is available. suit your application best. Eventually this question may not be needed The final information required is to know the to be taken into account as more and more size and shape. sensors are becoming available in a multi- To give a general guideline, the following voltage AC/DC format, 12-265 AC/DC. chart gives an indication of each type of sensor relating to sensing distances. 4 – What are you controlling? Range/longest to shortest Always examine the type of output required Photoelectric – Through-Beam and its capability to drive the external Photoelectric – Retroreflective circuitry. Ultrasonic – Proximity The most common problem when dealing Photoelectric – Diffuse Reflective with D.C. output circuits relates to “sourcing” Photoelectric – Background Suppression or “sinking” PNP or NPN. Photoelectric – Convergent Beam Always determine the answer to this question prior to any purchase by examining Photoelectric – Fiber Optics the specification of the control or counter Magnetic system you are interfacing with, to ensure Capacitive Proximity compatibility. Inductive Proximity 2 For Application Assistance Call 1-800-451-8279 or Fax 1-815-389-6678 Photoelectric Photoelectric Identification Codes 1. 2. 3. 4. 5. 6. 7. 8. 9. 10. 11. 12. 13. 14. 15. 16. 17. 18. 19. + Applications Example: O M 12RT—DHTP—020 0 —CL 1 O = Photoelectric Sensor 9 Output function 13-16 Sensing distance • Jam detection and prevention A = Complementary LA/DA Sensing distance specifications 2 M = Metric metal housing • Empty line detection (light activated/ are always indicated by 4 digits T = Metric thermoplastic dark activated) – mm: without decimal point • Counting housing D = Dark activated (DA) – m: with decimal point R = Rectangular design • Sorting by size, color or surface H = Light activated (LA) e.g. 06.0 = 6 m Z = Cylindrical design • Automatic routing O = No output (through- e.g. 15.0 = 15 m • Feed control 3/4 Specification of housing beam transmitter) e.g. 0500 = 500 mm dimensions P = Selectable LA/DA 17 Dash • Hopper level control e.g. 12 = M12 (light activated/ • Color mark registration 18 = M18 dark activated) 18 Connection type 20 = 20 series X = Customer-specified A = Screw termination • Edge guiding 90 = 90 series output B = Plug with screw • Web break detection terminals 5/6 ES = Through-beam sensor 10 Output type C = Cable (standard C = 2 m • Positioning (Complete set) A = Analog output or length in m) EE = Through-beam, N = NAMUR • Cut-off control S = Plug-in connector receiver only O = No output • Filling SE = Through-beam, Q = Triac 19 Options • Folding and wrapping transmitter only R = Relay C = Control/diagnostic input • Batch counting LC = Fiber optic control S = Others D = LED for output indication (sensor with fiber T = Transistor E = Adjustable sensitivity • Missing part detection optics connection) Y = Thyristor F = Diagnostic circuit with RH = Diffuse reflective sensor output and LED for • Correct count 11 N = NPN transistor output with background indicator (switched to negative) • Open flap detection suppression G = LED for output mode, P = PNP transistor output • Ejected part detection RS = Retroreflective sensor supply voltage and beam (switched to positive) RT = Diffuse reflective sensor control indication • Incorrect closure G = Push/Pull FF = Convergent beam sensor, H = LED for supply voltage S = Through-beam light • Door control fixed focus and output mode source PR = Print registration sensor indication • Sizing U = Switch selectable PS = Polarized retro sensor L = LED for output indicator NPN/PNP T = Adjustable timer circuit 7 Dash 2 = 2-wire output V = LED for operating voltage MCS-627 3 = 3-wire output 8 Voltage type indication 4 = 4-wire output A=AC X = Customer-specific D=DC 12 Dash options M = Multivoltage, AC/DC, UC Z = Fixed timer MCS-627 P = Programmable voltage (AC or DC) Truck Height Control A long range through-beam sensor was Diffuse positioned at a height just below the over- Reflective hanging roof and a couple of feet in front, so Sensor the breaking of the beam would activate an output wired to an alarm alerting the driver to stop. Retroreflector MCS-638 Color Mark Shrink wrap film Sensor Bag Cutting Machine Object Detection Basically, with this being a specialized By placing a diffuse reflective type under- application, there is only one solution and neath the conveyor and looking up through product selection, and that is the MCS 638 the rollers, a safe sensing
Details
-
File Typepdf
-
Upload Time-
-
Content LanguagesEnglish
-
Upload UserAnonymous/Not logged-in
-
File Pages68 Page
-
File Size-