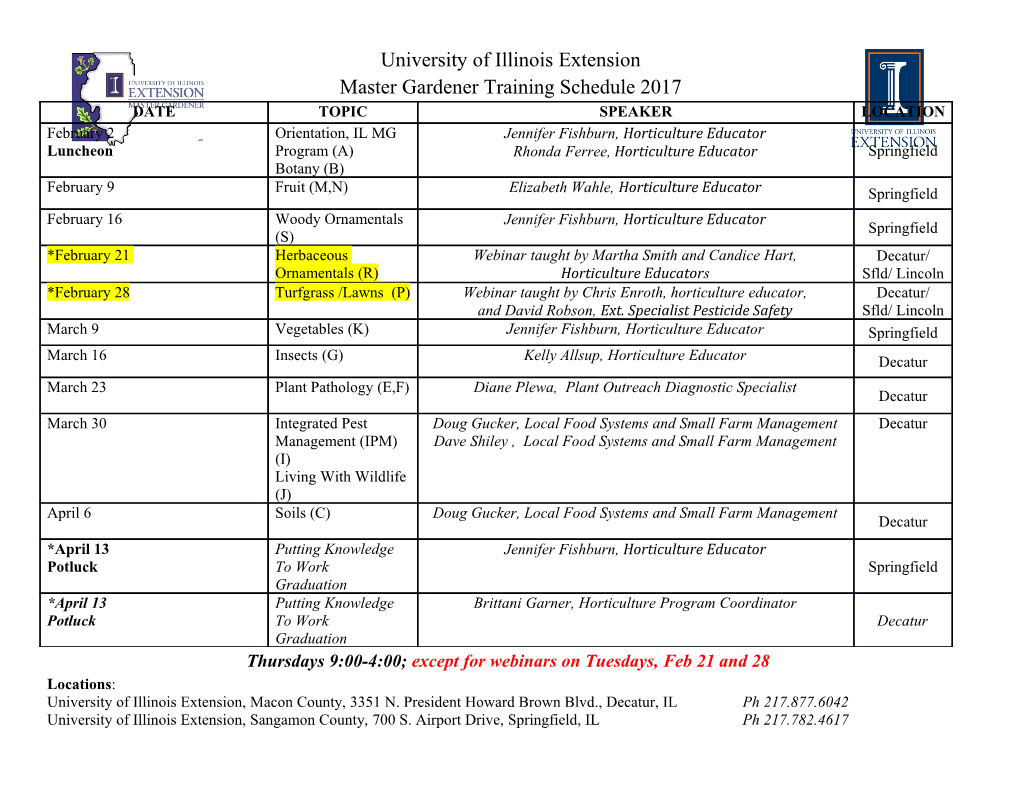
Mukt Shabd Journal ISSN NO : 2347-3150 CFD Analysis of Four Stroke Engine Inlet Valve and Exhaust Valve Manifold System Gopi Satyasai Kumar1 1 Research Scholar, Department of Mechanical Engineering, Godavari Institute of Engineering & Technology, Andhra Pradesh, India. M Bala Krishna2 2 Sr. Assistant Professor, Department of Mechanical Engineering, Godavari Institute of Engineering & Technology, Andhra Pradesh, India. ABSTRACT: The design and manufacture of Internal Combustion (IC) Engines is under significant pressure for improvement. The next generation of engines needs to be compact, light, powerful, and flexible, yet produce less pollution and use less fuel. Innovative engine designs will be needed to meet these competing requirements. The time scales of the intake air flow, fuel injection, liquid vaporization, turbulent mixing, species transport, chemistry, and pollutant formation all overlap, and need to be considered simultaneously. Computational Fluid Dynamics (CFD) has emerged as a useful tool in understanding the fluid dynamics of IC Engines for design purposes.Fluid flow dynamics inside an engine combustion cylinder plays an important role for air-fuel mixture preparation. IC Engine model is developed using CATIAV5R20 tool. The model is then imported to Finite Element solver tool. ANSYS I.C Engine is used for post processing the results. Insight provided by CFD analysis helps guide the geometry design of parts, such as ports, valves, and pistons; as well as engine parameters like valve timing and fuel injection. Using CFD results, the flow phenomena can be visualized on 3D geometry and analysed numerically, providing tremendous insight into the complex interactions that occur inside the engine. This allows you to compare different designs and quantify the trade-offs such as soot v/s NOx, swirl v/s tumble and impact on turbulence production, combustion efficiency v/s pollutant formation, which helps determine optimal designs. In this paper the In cylinder cold flow CFD simulation of four stroke petrol engine using hybrid approach of ANSYS fluent. The simulation is carried out using parameter and journal files which is symmetry geometry.The flow dynamics inside the cylinder for different minimum valve lift is studied using FEA. Dynamic motion is visualized and velocity magnitude is plotted for different crank angle from 0° to 720°. Finally velocities and crank angles for various valve lifts are compared. KEYWORDS: Engine, inlet valve, Exhaust valve, Exhaust manifold, ANSYS fluent. condition needed for the fuel injection during the INTRODUCTION compression stroke. An internal combustion engine (ICE) is a heat CFD can be very well applied for analyzing any engine where the combustion of a fuel occurs with particular process. It can also be used for the an oxidizer (usually air) in a combustion modification of the existing engine design or can chamber that is an integral part of the working fluid also be employed for a new design of an engine. It is flow circuit. In an internal combustion engine the hoped that it may be benefitted in understanding the expansion of the high temperature and high-pressure application of CFD for fluid flow analysis of engine gases produced by combustion apply direct force to inlet and exhaust manifolds. some component of the engine. The force is applied The exception to this is the flows in the typically to piston, cylinder and valves. corners and small crevices of the combustion This force moves the component over a chamber where the close distance of the walls distance, transforming chemical energy into useful diminished out turbulence. Heat transfer, mechanical energy. In diesel engine of these four evaporation, mixing and combustion rates all processes, the intake and compression stroke is one increase as engine speed increases. This increases of the most important processes which influences the time rate of fuel evaporation, the mixing of the the pattern of air flow structure coming inside fuel vapor and air as well as combustion process. As cylinder during intake stroke and generates the a result of the high velocity inside the internal combustion engine (ICE) , in cylinder flows are Volume IX, Issue VII, JULY/2020 Page No : 1269 Mukttypically Shabd turbulent Journal. In today’s world, major with maximum speed of 1500 ISSNrpm is NO taken : 2347-3150 for the objectives of engine designers are to achieve the analysis. The load and performance test is twin goals of best performance and lowest possible conducted. From the experiment back pressure and emission levels. To maximize the mass of air exhaust temperatures are measured. The mass flow inducted into the cylinder during the suction stroke, rate and velocities are calculated. Flow through the the intake manifold design, which plays an exhaust manifold is analyzed using commercially important role, has to be optimized. The design available software with mass flow rate and pressure becomes more complex in case of a multi cylinder as boundary conditions. engine as air has to be distributed equally in all the cylinders. Hence, configuration of manifold Vivekananda Navadagi and geometry becomes an important criterion for the SiddaveerSangamad [4] they analyzed the flow of engine design. exhaust gas from two different modified exhaust manifold with the help of Computational fluid LITERATURE REVIEW dynamics. To achieve the optimal geometry for the low back pressure they have analyzed two different PL. S. Muthaiah [1], He has analyzed the exhaust manifold, base geometry exhaust manifold exhaust manifold in order to reduce the backpressure and the modified geometry exhaust manifold. In the and also to increase the particulate matter filtration. base model of the exhaust manifold the outlet is at He has modified the different exhaust manifold by side of the first inlet where as in the modified model varying the size of the conical area of the exhaust of the exhaust manifold the outlet is at the centre of manifold and varying the size of the grid wire mesh the exhaust manifold. Analysis has been done for the packed throughout the exhaust manifold. When size two different exhaust manifolds. The results were of the grid mesh packed decreased the backpressure compared for the two models and it is found that the increases which leads to lower the performance of modified model gives low back pressure in the engine due to more fuel consumption and hence comparison with other base model which ensures the low volumetric efficiency. When size of the grid improvement in the efficiency of the engine. mesh packed increased the backpressure decreases The flow distribution in the exhaust the filtration of the particulate matter also reduces manifold channels would be highly dependent on the which will not satisfy the standards of the pollution header shape and the flow rate. Jafar M Hassan [5] control. Computational fluid dynamics is used for had analyzed the performance of the manifolds with the study of the exhaust manifold and best possible a tapered longitudinal section. The length of the design of the exhaust manifold with minimum manifold for this study was 127 cm while the backpressure and maximum particulate matter manifold diameter was 10.16 cm. Authors had used filtration efficiency is suggested. the numerical simulations (CFD) for this research work. The flow conditions corresponding to Re = K.S. Umesh, V.K. Pravin and K. 10x104, 15x104 and 20x104 were considered. The Rajagopal [2] In this work eight different models of results were analyzed in terms of uniformity exhaust manifold were designed and analyzed to coefficient. Based on their CFD simulation results, improve the fuel efficiency by lowering the they had concluded that the tapered header backpressure and also by changing the position of configuration provides better flow distribution as the outlet of the exhaust manifold and varying the compared to the header with circular cross-section. bend length. The eight different modified models are M.Usan[6] had applied a multi-disciplinary short bend centre exit (SBCE), short bend side exit optimization approach for the exhaust system, (SBSE), long bend center exit (LBCE), long bend exhaust manifold and catalytic converter, in highly side exit (LBSE), short bend center exit with reducer integrated concurrent engineering software ( SBCER), short bend side exit with reducer framework. They had considered four-cylinder 1.4 (SBSER), long bend centre exit with reducer litre engine as a baseline model. The optimization (LBCER), long bend side exit with contained four major modules – Geometry, reducer(LBSER).After analysis they included that Structural, Cost and Fluid Dynamics – and the the exhaust manifold with long bend centre exit with relevant software for each module was applied. 1- reducer (LBCER), gives the highest overall dimensional transient CFD simulations were carried performance. out using AVL BOOST with the engine torque and catalytic converter inlet temperature over the engine Kulalet al.(2013) [3]work comprehensively rpm were being estimated. analyzes eight different models of exhaust manifold HessamedinNaemi[7] had employed and concluded the best possible design for least fuel numerical simulations (CFD methods) for estimating consumption. CFD is the current trend on the flow loss coefficient in manifolds. The flow inlet automotive field in reducing the cost effect for and exit was model using ‘mass-flow-inlet’ and analysis of various models on the basis of fluid flow. ‘pressure-outlet’ boundary conditions, with the A multi-cylinder Maruti - Suzuki Wagon-R engine Volume IX, Issue VII, JULY/2020 Page No : 1270 Muktconsideration Shabd Journal that the flow was compressible. The Internal combustion enginesISSN areNO quite : 2347-3150 different results from different turbulence models – standard from external combustion engines, such k-ε, standard k-ω, SpalartAllmaras model and RNG as steam or Stirling engines, in which the energy is k-ε model – were compared in terms of flow loss delivered to a working fluid not consisting of, mixed coefficient against the experimental data. Based on with, or contaminated by combustion products.
Details
-
File Typepdf
-
Upload Time-
-
Content LanguagesEnglish
-
Upload UserAnonymous/Not logged-in
-
File Pages13 Page
-
File Size-