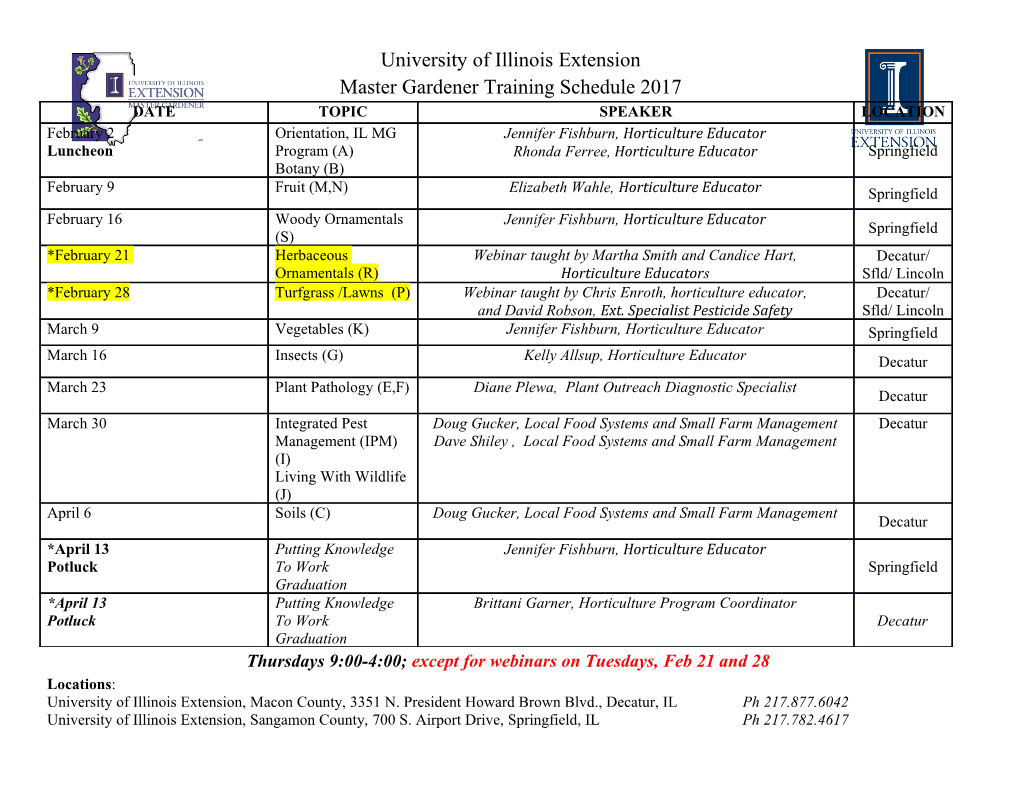
DESIGN OF A DUAL-EXPANDER AEROSPIKE NOZZLE ROCKET ENGINE by ERIC STEPHEN MCVAY RICHARD D. BRANAM, COMMITTEE CHAIR JOHN BAKER PATRICK R. LECLAIR A THESIS Submitted in partial fulfillment of the requirements for the degree of Master of Science in the Department of Aerospace Engineering and Mechanics in the Graduate School of The University of Alabama TUSCALOOSA, ALABAMA 2016 Copyright Eric Stephen McVay 2016 ALL RIGHTS RESERVED ABSTRACT The University of Alabama’s Aerospace Engineering and Mechanics Department is developing a computational dual-expander aerospike nozzle (DEAN) upper stage rocket engine to demonstrate the engine’s performance capabilities and to establish a model by which the DEAN can be built. This research expands the base model developed by the Air Force Institute of Technology to more accurately represent the physics involved in both the fluid flow and geometrical properties of the engine. The DEAN engine was modeled using NASA’s Numerical Propulsion System Simulation (NPSS) and Chemical Equilibrium with Applications (CEA) software. The methodology implemented in this research was validated by modeling the RL- 10A-3-3A upper stage engine in NPSS and comparing resulting outputs with NASA’s ROCket Engine Transient Simulator (ROCETS) analysis. The DEAN uses liquid oxygen and liquid hydrogen as its propellant and is being designed to produce a thrust of 30,000 [lbf] and a specific impulse of at least 465.5 [s], at an oxidizer-to-fuel ratio of 5.88, while also remaining within the size envelope of the RL-10B-2 upper stage engine. The performance and size objectives were established to meet the National Aeronautics and Space Administration’s (NASA) Advanced Upper Stage Engine Program (AUSEP) need for an upper stage rocket engine to replace the aging RL-10 series engines that have been in production since the 1960s. Results indicate that optimal performance for the feasible solution space examined in this research occurs at an expansion ratio of 30, a throat area of 23 [in2], and a characteristic length, L*, of 90 [in]. The optimal DEAN design point was ii shown to achieve a thrust of more than 5,000 [lbf] greater than the RL-10B-2, a Isp of 1.8 [s] greater, and a significantly reduced size envelope. iii LIST OF ABBREVIATIONS AND SYMBOLS a = cooling channel half-spacing �!! = speed of sound of H2 �!! = speed of sound of O2 A = cross-sectional area Ac = chamber area !! = chamber contraction ratio !! Ae = nozzle exit area Aphys = annular flow area At = throat area AR = cooling channel aspect ratio b = width of cross-sectional area c = effective exhaust velocity c* = characteristic velocity �!" = chamber ratio coefficient �! = nozzle truncation factor �! = heat capacity of the fluid Cd = discharge coefficient CF = thrust coefficient CEA = Chemical Equilibrium with Applications iv CET93 = Chemical Equilibrium with Transport Properties CV = cooling volume d = depth of cross-sectional area dhyd = hydraulic diameter D = diameter Dc = chamber diameter DEAN = dual-expander aerospike nozzle f = Darcy friction factor FPT = fluid property table g0 = gravity constant Δh = change in enthalpy h = enthalpy h = cooling channel height hgr = hot gas heat transfer coefficient, Bartz equation hl = liquid heat transfer coefficient, Colburn equation �! = pump head pressure rise Isp = specific impulse k = thermal conductivity K = loss-factor L = length L* = characteristic length Lc = chamber length Le = engine length v Ln = nozzle length LOX = liquid oxygen LH2 = liquid hydrogen LCH4 = liquid methane LRPS = liquid rocket propulsion system m = mass mf = final mass mo = initial mass � = mass flow rate � = molar mass M = Mach number Me = exit Mach number n = number of channels NASA = National Aeronautics and Space Administration NIST = National Institute of Standards and Technology NPSS = Numerical Propulsion System Simulation O/F = oxidizer-to-fuel ratio ΔP = pressure drop Pa = ambient pressure Pc = chamber pressure Pe = exit pressure Pe/Pc = pressure ratio �!" = turbine inlet pressure vi �!" = turbine discharge pressure �!,!" = turbine pressure ratio � = heat flow rate � = gas constant Re = Reynolds number ROCCID = ROCket Combustor Interactive Design ROCETS = ROCket Engine Transient Simulator RTE = Rocket Thermal Evaluation rc = chamber radius rt = throat radius SA = surface area SRPS = solid rocket propulsion system t = cooling channel-combustion chamber wall thickness T = temperature TDK = Two-Dimensional Kinetics �! = total temperature Tc = combustion temperature T/W = thrust-to-weight ratio ΔV = change in velocity v = velocity Ve = exhaust velocity Vc = chamber volume w = cooling channel half-width vii x = axial position y = surface contour equation α = nozzle half-angle ε = expansion ratio γc = ratio of specific heats of combustion in chamber ηP = pump efficiency factor ηT = turbine efficiency factor λ = nozzle efficiency factor µ = absolute viscosity �! = Bartz equation correction factor �!"#$ = Colburn equation correction factor for tube radius of curvature ρ = density viii ACKNOWLEDGMENTS I would first like to express my sincere appreciation to Dr. Richard Branam, my research advisor and committee chair, for his guidance, encouragement, and support throughout this research. I would like to thank Dr. John Baker for sitting on my research committee and, more importantly, for reestablishing the astronautics coursework and research foundations within the Aerospace Engineering and Mechanics department. Thank you to Dr. Patrick LeClair for sitting on my research committee and for being patient with my constant questions regarding relativity, physics, and metaphysics. Thanks to Dylan Stapp, my research colleague and lab mate, for the wise words and support throughout this endeavor – “coffee is my working fluid.” I would like to thank The University of Alabama Graduate School for providing me the Graduate Council Fellowship, which allowed me to pursue my master’s degree and complete this research. Finally, a special thank you to my beautiful wife Allyssa – your love, support, and sacrifice has been the glue for our family over these past five years; I cannot wait to continue our journey together. ix CONTENTS ABSTRACT ................................................................................................................................... ii LIST OF ABBREVIATIONS AND SYMBOLS ........................................................................... iv ACKNOWLEDGMENTS .............................................................................................................. ix LIST OF TABLES ...................................................................................................................... xiii LIST OF FIGURES ...................................................................................................................... xiv I. INTRODUCTION ........................................................................................................................ 1 I.1 Motivation .............................................................................................................................. 3 I.2 Research Objectives ............................................................................................................... 5 II. BACKGROUND ........................................................................................................................ 8 II.1 Current Upper Stage Rocket Engines ................................................................................... 8 II.2 Rocket Engine Thermodynamic Cycles ............................................................................... 9 II.3 Rocket Engine and Nozzle Performance ............................................................................ 14 II.4 Rocket Engine Components ................................................................................................ 16 A. Propellant Feed System ................................................................................................. 17 B. Turbomachinery ............................................................................................................. 19 C. Injector ........................................................................................................................... 23 D. Combustion Chamber .................................................................................................... 27 E. Cooling Jacket ................................................................................................................ 32 II.5 Dual Expander Aerospike Nozzle ....................................................................................... 39 II.6 Previous DEAN Research ................................................................................................... 41 x A. David F. Martin, AFIT .................................................................................................. 42 B. Joseph R. Simmons, AFIT ............................................................................................. 42 C. Joshua N. Hall, AFIT ..................................................................................................... 43 D. Michael D. Moen, AFIT ................................................................................................ 43 III. METHODOLOGY .................................................................................................................. 44 III.1 Numerical Propulsion System Simulation (NPSS) ..........................................................
Details
-
File Typepdf
-
Upload Time-
-
Content LanguagesEnglish
-
Upload UserAnonymous/Not logged-in
-
File Pages129 Page
-
File Size-