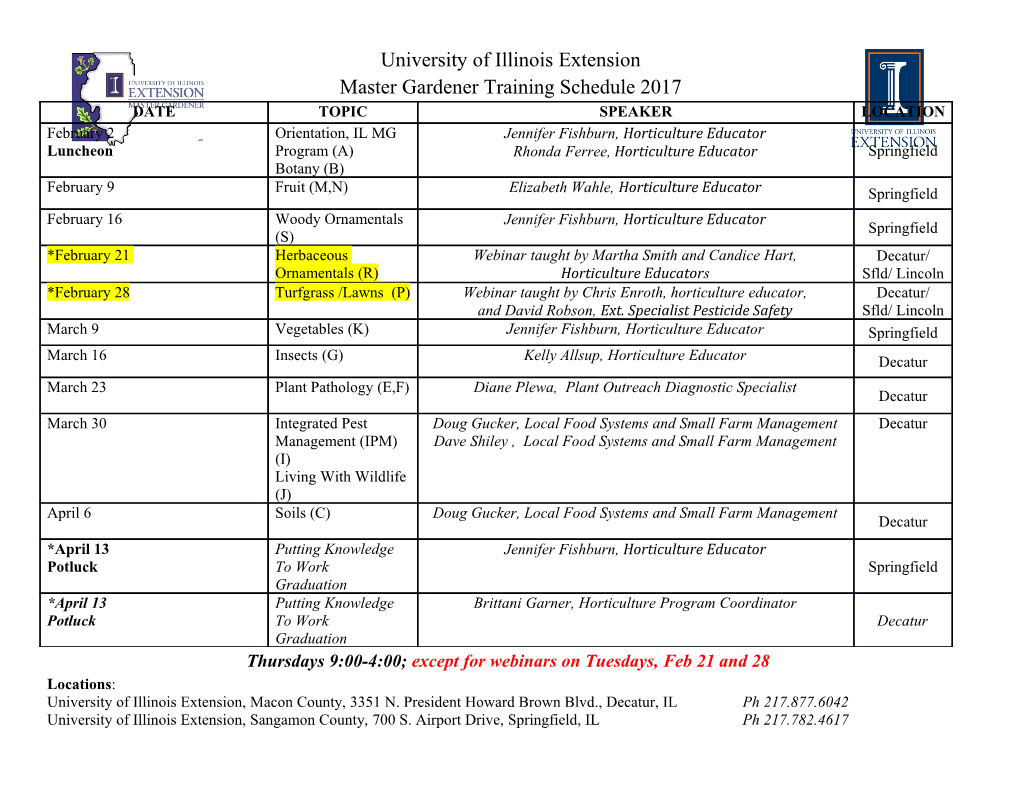
Advances in the Development of the Discrete Element Method for Excavation Processes C. A. Labra E. Oñate J. Rojek Monograph CIMNE Nº-132, September 2012 Advances in the Development of the Discrete Element Method for Excavation Processes C. A. Labra E. Oñate J. Rojek Monograph CIMNE Nº-132, September 2012 International Center for Numerical Methods in Engineering Gran Capitán s/n, 08034 Barcelona, Spain INTERNATIONAL CENTER FOR NUMERICAL METHODS IN ENGINEERING Edificio C1, Campus Norte UPC Gran Capitán s/n 08034 Barcelona, Spain www.cimne.com First edition: September 2012 ADVANCES IN THE DEVELOPMENT OF THE DISCRETE ELEMENT METHOD FOR EXCAVATION PROCESSES Monograph CIMNE M132 The authors ISBN: 978-84-940243-5-1 Depósito legal: B-27595-2012 To my parents... Acknowledgements This research was partially supported by project SAFECON of the European Research Council (ERC). Abstract Modelling of granular materials, soils and rocks has been a challenging topic of investigation for decades. Classical continuum mechanics has been used to idealize soils and rocks, and numerical solution techniques such as finite element method (FEM) has been used to model these materials. Considering the idealization of the material, continuum mechanics allows the analysis of phenomena with discontinuous nature such as fracture in rock or soil via damage models. However, in more complex processes like rock milling or crushing, this kind of models are usually not suitable. Discrete models are more appropriate for problems with multiple discontinuities and particulate materials. The discrete element method (DEM) has been gaining popularity in analysis of granular materials, soils and rocks. Many aspects of this method still require more profound investigation. This work presents new developments of the discrete element method improving efficiency and accuracy of modelling of rock-like materials, especially in excavation processes. All the numerical algorithms has been implemented in an in-house software, which was then used to run numerical examples. The basic formulation of DEM with linear elastic-perfectly brittle contact model is presented. The main difference with other models found in the literature is the consideration of global stiffness and strength parameters that are constants in the whole model. The result of a simulations is strongly related with the configuration of the particle assembly used. Particle assemblies should be sufficiently compact and ensure the isotropy to reproduce the physical properties of the modelled material. This work presents a novel technique for the generation of highly dense particle assemblies in arbitrary geometries, satisfying all the requirements for accurate discrete element simulations. One of the key issues in the use of the DEM is the estimation of the contact model parameters. A methodology is proposed for the estimation of the contact model parameters yielding required macroscopic properties of the material. The relationships between the contact model parameters and the mechanical properties of brittle materials, as well as the influence of the particles assembly configuration on the macroscopic ii properties, are analysed. A major difficulty in the application of the DEM to real engineering problems is the high computational cost in simulation involving a large number of particles. The most common way to solve this is the use of parallel computing techniques, where multiple processors are used. As an alternative, a coupling scheme between DEM and the finite element method (FEM) is proposed in the work. Within the hybrid DEM/FEM model, DEM is only used in the region of the domain where it provides an advantage over a continuum-based approach, as the FEM. The coupling is dynamically adapted, starting with the whole domain discretized with FEM. During the simulation, in the regions where a high stress level are found, a change of modelling method from continuum FEM to the discrete DEM is employed. Finally, all the developments are applied to the simulation of a real excavation process. An analysis of the rock cutting process with TBM disc cutters is performed, where DEM and the DEM/FEM coupling technique presents an important advantage over other simulation techniques. Table of Contents 1 Introduction1 1.1 Motivation and objectives...........................1 1.2 Outline......................................3 2 The discrete element method5 2.1 Equations of motion..............................5 2.2 Contact forces..................................6 2.2.1 Normal contact force..........................7 2.2.2 Tangential frictional contact......................9 2.3 Constitutive models............................... 10 2.4 Background damping.............................. 13 2.5 Time integration scheme............................ 14 2.6 Numerical stability............................... 15 3 Discretization of the media 17 3.1 Overview of available approaches....................... 17 3.1.1 Constructive algorithms........................ 18 3.1.2 Dynamic algorithms.......................... 19 3.1.3 Collective rearrangement techniques.................. 19 3.2 The proposed algorithm............................ 20 3.2.1 Internal contacts............................ 21 3.2.2 Treatment of boundaries........................ 22 3.2.3 Treatment of particle overlapping................... 25 3.2.4 Initial generation of the media..................... 27 3.3 Characterization of the generated package.................. 28 3.3.1 Average radius............................. 28 3.3.2 Porosity................................. 29 3.3.3 Coordination number.......................... 29 3.3.4 Fabric tensor.............................. 30 iv Table of Contents 3.4 Analysis of the packing algorithm....................... 32 4 Estimation of the discrete element parameters 39 4.1 Micro-macro relationship............................ 40 4.2 Micromechanical analysis............................ 41 4.2.1 Inter-particle contact law........................ 42 4.2.2 Average stress and average strain tensors............... 42 4.2.3 Kinematic localization assumption.................. 44 4.2.4 Numerical analysis........................... 47 4.3 Dimensional analysis.............................. 49 4.3.1 Elastic constants for two-dimensional case.............. 52 4.3.2 Elastic constants for three-dimensional case............. 56 4.3.3 Compressive and tensile strengths for two-dimensional case..... 59 4.3.4 Compressive and tensile strengths for three-dimensional case.... 68 4.3.5 Improving dimensionless number with micromechanics....... 79 4.4 Parameter estimation.............................. 83 4.4.1 Parameter estimation for two-dimensional case............ 85 4.4.2 Parameters estimation for three-dimensional case.......... 89 5 Coupling scheme with the finite element method 95 5.1 The finite element method........................... 95 5.1.1 Non-linear transient dynamic formulation............... 96 5.1.2 Finite element discretization...................... 98 5.1.3 General discrete/finite element dynamic formulation......... 100 5.2 Coupling scheme................................ 101 5.2.1 Kinematic constraints......................... 104 5.2.2 Example: Wave propagation...................... 107 5.2.3 Example: Mixed-mode bending beam with a notch......... 108 5.3 Adaptivity of the coupling definition..................... 112 5.3.1 Transition from finite elements to discrete elements......... 114 5.3.2 Projection of kinematic variables................... 115 5.3.3 Example: Mixed-mode bending beam with a notch solved with the adaptive DEM/FEM coupling scheme................. 119 5.3.4 Example: 3D three point bending beam............... 123 6 Modelling of rock cutting process 129 6.1 Linear cutting test with disc cutters...................... 130 6.2 Discretization of the linear cutting test model................ 133 Table of Contents v 6.2.1 Disc cutters selection and discretization............... 133 6.2.2 Rock material sample......................... 135 6.2.3 Cutting process parameters...................... 138 6.3 Cutting forces prediction models........................ 139 6.3.1 Colorado school of mines model.................... 140 6.4 Numerical results and comparisons...................... 141 6.4.1 Unrelieved rock specimen....................... 142 6.4.2 Relieved rock specimen......................... 161 7 Summary and conclusions 171 A Micromechanical stress tensor 175 A.1 Stress tensor in terms of external forces.................... 175 A.2 Stress tensor in terms of internal forces.................... 176 A.3 Average stress tensor.............................. 177 B Micromechanical strain tensor 179 B.1 Geometrical micro-variables.......................... 179 B.2 Strain tensor.................................. 181 List of Figures 2.1 Decomposition of the contact force into the normal and tangential components....................................7 2.2 Rheological model of the contact........................7 2.3 Friction force vs. relative tangential displacement...............9 2.4 Force-displacement behaviour in the linear elastic perfectly brittle model with bonded contacts.............................. 13 3.1 Local neighbourhood of a particle in the interior of the domain....... 20 3.2 Minimization of the distance in a small assembly of cylindrical particles.. 22 3.3 Boundary treatment in the exterior zone of the domain........... 23 3.4 Dense assembly of discs with and without the boundary treatment for a square domain.................................
Details
-
File Typepdf
-
Upload Time-
-
Content LanguagesEnglish
-
Upload UserAnonymous/Not logged-in
-
File Pages213 Page
-
File Size-