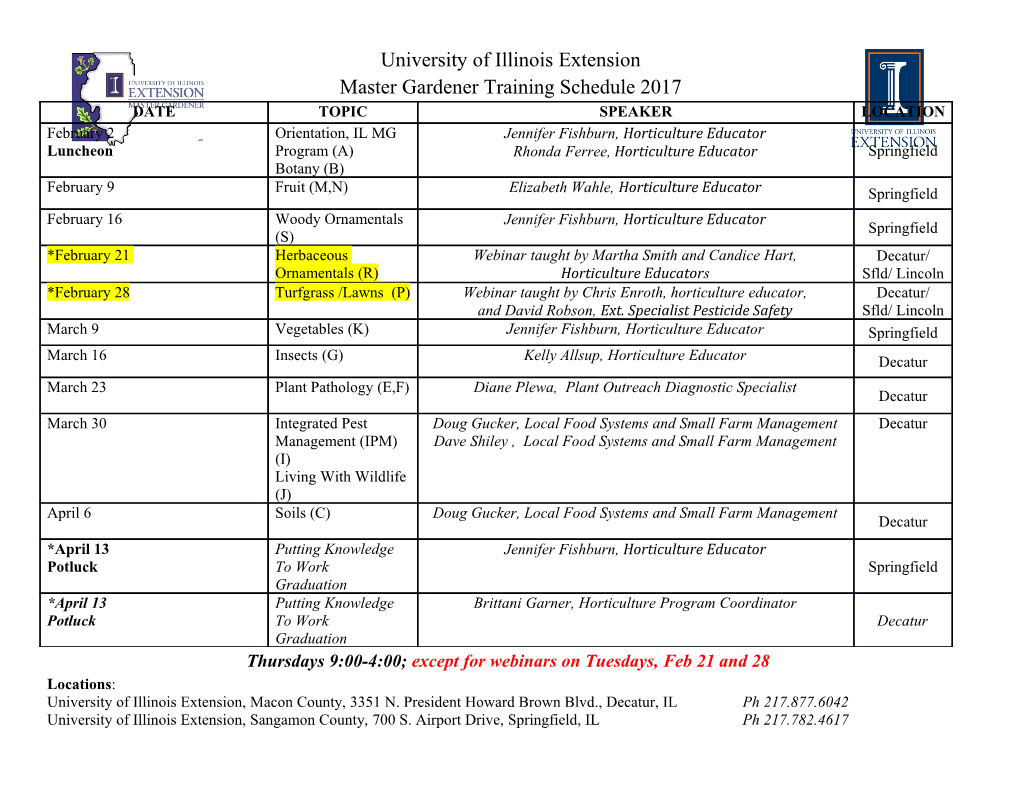
1 April 5, 2011, Madison WI CSWEA Education Seminar Key elements and bottlenecks of the membrane bioreactor (MBR) process for advanced wastewater treatment Prof. TorOve Leiknes TorOve Leiknes 2 Outline: - Brief introduction to the history of MBRs - Market potentials and development – Global / Europe - Challenges and bottlenecks in MBR systems - Where is research heading today? - Future perspectives… 3 Looking into membrane technology: Suspended matter MF Macromolecules UF Sugars' Divalent salts NF Dissociated acids Monovalent salts Fluks RO Undissociated acids Trykk Water RO – rejection of ions/solutes MF Conventional filtration (< 20 Å pore size) UF NF NF – rejection of ions/solutes RO (< 20 – 600 Å) UF – defined by MWCO (10-1000 Å) Angstroms 1 10 102 103 104 105 106 MF – colloidal suspensions Microns 10-4 10-3 10-2 10-1 1 10 102 (0.02 – 10 μm) Ionic Macromolecular Micron Fine range range particle particle 4 AS Wastewater Sludge applications: treatment RO GAC Recarbonation Air stripping 2. Process optimization Pre-treatment AS Sand filter MF/UF RO 1. For tertiary treatment Sludge treatment Pre-treatment MBR AS MF/UF RO RO Sludge Sludge treatment treatment 4. Membrane bioreactors 3. Replace conventional treatment 5. ……… ? 5 Steps on the way to MBR….. Application distinction: Municipal / industrial End of 1960’s: - UF: for municipal wastewater, sludge separation in AS (1969) 1970’s and 1980’s: - MF/UF of industrial wastewater (f.ex. textile industry, oily wastewater, separation of metals, organic compounds) - In connection with separation in anaerobe digestion 1990’s: - Membrane bioreactor concepts 6 MBR breakthrough… 1989: Prototype of current MBR solutions, Yamamoto et.al. • Flux: ~ 3-9 LMH • Sludge: 10-11 kg/m3 • TMP: ΔP ~ 1.33 bar • Energy: 0.007 kWh/m3 • Treatment efficiencies: - 93 - 95% COD - 94 - 99% TOC - no SS 7 Why the interest in MBRs? (Gander et al., 2000) 8 What has happened…..? ……… what is to be expected? Yamamoto, 2009 9 What drives MBRs R&D? Global water markets: $350 - $375 billion • municipal sector ∼ $225 billion, • industrial segment ∼ $110 billion, • residential market ∼ $25 billion 160 Water Wastewater 140 120 • Total value - 224 billion € 100 - AAGR 16-20% 80 60 • Drinking water Billion EURO Billion 40 – doubling of market value 20 • Wastewater largest segment 0 1998 1999 2000 2005 2015 – 43 % growth rate 10 Market drivers Investigations of market trends have highlighted: “The driving factor for the growth of this market is waster stress…” • need to recycle and reuse wastewater • stricter environmental regulations worldwide • new applications in the industry and new developments • biosolids management and energy recovery • sustainable wastewater management 11 Global trends 12 Anticipated growth rates Stipulated average annual growth rates Large regional difference China and Middle East key future markets Annual growth Region (% / year) N. America 15 % Middle East 25 % Europe 10 % Asia Pacific 10 % China 20 % Japan 10 % Total 20 % 13 Examples of large MBR projects Capacity WWTP name Location Commissioning (m3/d) Jumeirah Golf Estates Dubai 2010 220 000 Palm Jebel Ali Dubai 2010 220 000 Brightwater USA 2010 144 000 Jebel Ali Free Zone Dubai 2007 140 000 International City Dubai 2007 110 000 Guangzhou China 2010 100 000 Kunyu River China 2007 100 000 Johns Creek USA 2007 93 500 Beixiaohe China 2007 80 000 Al-Ansab Oman 2006 78 000 Peoria USA 2007 75 700 Lusail Qatar 2007 60 200 Qinghe China 2007 60 000 Syndial Italy 2007 47 300 14 European trends 65 new refs/year Total Municipal in Europe About 2 millions e.p (0.5% population) 45 new refs/year 30 new refs/year (Lesjean et.al. 2009) 15 MBRs, a proven technology! • Competitive for tertiary treatment requirements • BAT for wastewater reuse / recycling Large scale installations MBR Retrofitting / upgrading Package plants 16 Comparison of CAS - MBR Investment cost, new and retrofitted WWTPs 1989 - 2006 2000 1800 CAS 1600 CAS with tertiary treatment 1400 MBR Cost function (all WWTPs) 1200 Investment costs 1000 800 600 Specific cost, EUR per PE 400 200 0 0 10 20 30 40 50 60 70 80 90 100 Treatment Capacity, MLD Erftverband, Germany, 2009 Energy consumption 17 MBR in a nutshell 18 If only membranes were membranes…. 19 If only bacteria were bacteria…. Filamentous Protozoa Nematodes Rotifers 20 Key elements of the MBR process Feed characteristics Membrane module Composition of feed Membrane characteristics Main “bottlenecks”: Treatment requirements - pore size / surface properties - Nutrient removal Module configuration - End use of treated water - Geometry / dimensions Operatingparameters • Fouling / sludging • Aeration (biology & Biological process Membrane process membrane) Biomass characteristics: Membrane fouling: - Floc structure - reversible / irreversible • Operation / monitoring - EPS (free/bound) Clogging: Bulk characteristics: - membrane channels • Complete process - viscosity - aeration system configuration • Energy demands Aeration • Costs – market Aerobic phase Air scouring Mass transfer Cleaning acceptance Operatingparameters Retention times: Flux / TMP - Hydraulic (HRT) Hydraulics Fouling - Solids (SRT) Cleaning 21 Fowled membranes……??? 22 Bottleneck - 1: Clogging Fouling of membrane channels and aeration systems; → increased aeration? → improved modules design? → improved pretreatment? “Improved” aeration = € 23 Impact of improving sludging • Pretreatment • Improved module design • Operating conditions Before After 24 Trends in aeration demands: Energy for: - pumping - aeration (biology / membranes) Consequence: → design of aerators → module designs → operating modes (GE Zenon) 25 Bottleneck – 2: Aeration in MBRs: • Membrane module operation – air scouring • Bioprocess operation – oxygen for aerobic degradation Pre-treated Anoxic Aerobic wastewater Permeate Sludge recirculation Air • Coarse bubbles - membrane operation • Fine bubbles - bioprocess operation 26 Biological vs. membrane operation Biological needs: Membrane needs: • Objective: • Objective: • Oxygen transfer for aerobic • Generate crossflow hydrodynamic degradation conditions • Practice: • Generate high shear stress on • Fine bubble diffusers surface • Challenge: • Remove deposition on membrane • Change in fluid viscosity surface • Poorer masstransfer • Practice: efficiencies, more energy • Continuous aeration for air scouring • High operating costs • Intermittent aeration (on/off cycles) • Change in biomass • Relaxation techniques (no production characteristics? during aeration) • Challenge: • High specific aeration demands • High operating costs 27 Aeration for aerobic biological processes: - Same fundamental Monod kinetics apply - Process must be designed for oxygen necessary to degrade both organic matter and to convert NH4 to NO2/NO3 as required - Determines oxygen transfer rate (OTR) Challenge: - Parameters in OTR equation affected by high SS concentrations - Particularly viscosity and the α-factor - Correlations have been proposed where µ is viscosity (kg/(m s)) x is the correlation exponential MBR: MLSS of 12 g/L → α-value of 0.6 CAS: MLSS of 3-5 g/L → α-value of 0.8 Consequence → higher aeration demand 28 Is the biomass different in an MBR? Floc size Boimass denisty EPS density Oxidation tank Large Frequently loose Lower Medium Small Membrane Large Compact and Higher Medium dense FISH analysis: • using general phylogenetic probes • using probes for specific functional groups (IBET, Portugal – EUROMBRA project) Beta-proteobacteria Gamma-proteobacteria Alpha-proteobacteria other Bacteria other Bacteria other Bacteria FISH probes targeting Alpha-, Beta- and Gamma-proteobacteria covered ≈ 60-75% 29 Bottleneck - 3: Fouling control / mitigation MBR foulants • polysaccharides • proteins • colloids • filterability Challenges: • Understand interaction biology – membranes • Identify major foulants • Strategies for fouling mitigation and control • Optimize operating conditions for minimal fouling • Cleaning of fouled control 30 Main mechanisms and types of membrane fouling 1. Membrane resistance: RM 4/6 2. Adsorption / scaling: RF 5 - reversible / irreversible 3 3. Pore blocking / plugging: RP 4. Cake formation: RC - dead-end operation 1 5. Concentration polarization: RG - formation of gel-layer 2 6. Biofouling – biofilm/EPS: RB ∆P = RR=++++mFCG R R R ... J ' RPm +Φ⋅∆ 31 Illustration of fouling development by particles: Clean membranes Start phase; → cake formation 32 - Fouling of MBRs - “Types” of fouling, how it behaves 33 • How does bio-fouling (biofilm growth / EPS) behave on the membrane surface? - Study biofilm growth - Study fouling development - CLSM analysis of biofouling - Characterization - green: signal from the membrane - red: fluorescent light from the lectin WGA, bound to the polysaccharides N- acetyl-glucosamine in the biofilm 34 Understanding MBR fouling and mitigation: Fundamentals of membrane fouling • EPS issues; polysaccharides vs. proteins, colloids? Data acquisition, monitoring techniques • Online monitoring systems • Fouling control and SMP sensor • DFU – filtration characterization unit • Advanced control systems (VITO) Modeling • Biological models • Sludge production models • CFD modeling and process development 35 Bottleneck - 4: sustainable flux, operation costs Flux = f( hydraulics, aeration, module design, operating mode, feed) → increased crossflow conditions (aeration) → module designs and choice of membrane material → backwash/relaxation, cleaning strategies/protocols → monitoring/analysis of feed Module geometry and aeration: • Bi-phasic CFD model for
Details
-
File Typepdf
-
Upload Time-
-
Content LanguagesEnglish
-
Upload UserAnonymous/Not logged-in
-
File Pages54 Page
-
File Size-