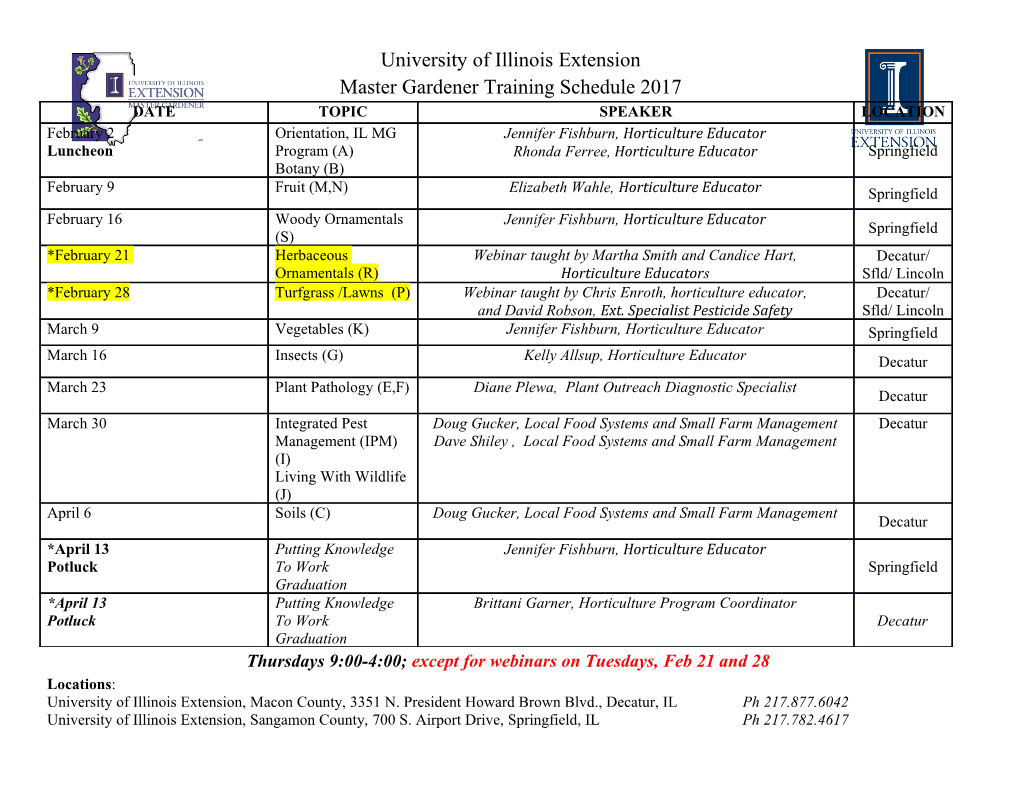
United States Office of Water EPA 832-F-00-022 Environmental Protection Washington, D.C. September 2000 Agency Wastewater Technology Fact Sheet Dechlorination DESCRIPTION or total combined chlorine residual remaining after chlorination. Typically, dechlorination is Dechlorination is the process of removing residual accomplished by adding sulfur dioxide or sulfite chlorine from disinfected wastewater prior to salts (i.e., sodium sulfite, sodium bisulfite, or discharge into the environment. Sulfur dioxide is sodium metabisulfite). Carbon adsorption is also an most commonly used for dechlorination and is the effective dechlorination method, but is expensive major focus of this fact sheet. Some dechlorination compared to other methods. Carbon adsorption is alternatives include carbon adsorption, sodium usually implemented when total dechlorination is metabisulfite, sodium bisulfite, and hydrogen desired. peroxide. Sodium metabisulfite and sodium bisulfite are mainly used in small facilities because Specific design criteria and monitoring these materials are more difficult to control requirements for a particular region are determined compared to sulfur dioxide. Hydrogen peroxide is by the state regulatory agency. Typically, the not frequently used because it is dangerous to treatment plant’s National Pollutant Discharge handle (WEF, 1996). Elimination System (NPDES) permit limits effluent chlorine residual and toxicity. Currently, many APPLICABILITY permits require very low or “non-detect” chlorine residuals, making dechlorination critical. Chlorination has been used widely to disinfect wastewater prior to discharge since passage of the One important alternative to dechlorination is to 1972 Federal Water Pollution Control Act achieve disinfection without the use of chlorine. (WPCA), (Finger et al., 1985). In the first years Other means of disinfection, such as ozone or following the WPCA, disinfected wastewater with ultraviolet disinfection, have also become significant levels of residual chlorine was routinely increasingly prevalent (U.S. EPA, 1986; Blatchley, discharged into the receiving waters. It became E.R. III, et al., 1996). clear, however, that residual chlorine is toxic to many kinds of aquatic life (see, for example, ADVANTAGES AND DISADVANTAGES Mattice and Zittel, 1976, and Brungs, 1973). Moreover, the reaction of chlorine with organic Advantages materials in the water formed carcinogenic trihalomethanes and organochlorines (WEF and • Protects aquatic life from toxic effects of ASCE, 1991). As a result, dechlorination was residual chlorine. instituted to remove residual chlorine from wastewater prior to discharge into sensitive aquatic • Prevents formation of harmful chlorinated waters. compounds in drinking water through reaction of residual chlorine with water- Dechlorination minimizes the effect of potentially born organic materials. toxic disinfection byproducts by removing the free -2 -2 - + Disadvantages (1) SO3 + HOCl ÿ SO4 + Cl + H -2 -2 - + • Chemical dechlorination can be difficult to (2) SO3 + NH2Cl + H20 ÿ SO4 + Cl + NH4 control when near zero levels of residual chlorine are required. Since free chlorine and inorganic chloramines react rapidly with S(IV) (Helz, 1998), a short contact • Significant overdosing of sulfite can lead to time of one to five minutes is considered to be sulfate formation, suppressed dissolved sufficient; nevertheless, complete blending at the oxygen content, and lower pH of the point of application is essential for effective finished effluent. dechlorination (WEF and ASCE, 1992). DESIGN CRITERIA Proper dosage is critical to produce a non- detectable chlorine residual. On a mass basis, 0.9 Chemistry of Dechlorination by Sulfonation parts sulfur dioxide (or 1.46 parts NaHSO3 or 1.34 parts Na2S2O5) is required to dechlorinate 1.0 part Sulfur dioxide (SO2) is a corrosive, nonflammable residual chlorine. In practice, approximately a one- gas with a characteristic pungent odor. At to-one ratio is used (WEF, 1996). Dosing in excess atmospheric temperature and pressure, it is a must be avoided because excess sulfite can react colorless vapor. When compressed and cooled, it with dissolved oxygen (four parts sulfite to one part forms a colorless liquid. Sulfur dioxide is supplied oxygen) in the wastewater to produce sulfates, as liquefied gas under pressure in 100 or 150 pound potentially leading to reduced dissolved oxygen containers and one-ton cylinders. As an alternative concentrations and low pH levels in the finished to sulfur dioxide gas, various dry chemicals are effluent for high levels of overdose (WEF, 1996). available which form sulfur dioxide in solution. Careful process control will help prevent These include sodium sulfite (Na2SO3), sodium overdosing. metabisulfite (Na2S2O5), sodium bisulfite (NaHSO3), a 38 percent aqueous solution of sodium Equipment for gaseous sulfonation metabisulfite, and sodium thiosulfate (Na2S2O3), among others (Lind, 1995). Equipment required for gaseous sulfonation using SO2 is similar in design to that used for When dissolved in water, chlorine hydrolyzes to chlorination, except that the materials are chosen form hypochlorous acid (HOCl) and hypochlorite for their application-specific chemical resistance ions (OClG) which, taken together, are referred to as (WEF, 1996). The four basic components of the “free chlorine.” (Free, uncombined chlorine, Cl2, is system include: sufficient gas supply with rarely found in wastewater since the conditions of automatic switch-over between cylinders; a formation are relatively extreme [Lind, 1995]). metering system, usually consisting of a vacuum Once formed, the free chlorine reacts with natural regulator and a rotameter for feed rate control; one organic matter in water and wastewater to form or more injectors with check valves; and a residual chlorinated organic compounds. The free chlorine analyzer to measure and transmit a continuous also combines with ammonia to form mono-, di-, signal proportional to the chlorine residual in the and trichloramines in quantities dependent on the sample stream. ratio of chlorine to ammonia nitrogen (Lind, 1995). In small concentrations, exposure to SO2 can cause When either sulfur dioxide or sulfite salts are eye and throat irritation. In high concentrations, dissolved in water, aqueous sulfur compounds in exposure can produce a suffocating effect caused by the +4 oxidation state are produced, often notated irritation to the upper respiratory tract. Therefore, S(IV) (Helz and Nweke, 1995). The S(IV) species, facility design should include features for safe -2 such as the sulfite ion (SO3 ), reacts with both free storage, handling, and use of sulfur dioxide. The and combined forms of chlorine, as illustrated in chlorine and sulfur dioxide cylinders should be equations (1) and (2) (WEF, 1996): located in separate rooms and stored in a well- ventilated, temperature-controlled area so that their but this suffers from loss of accurate calibration at temperature never drops below 18 or exceeds 70 low concentrations (Finger et al., 1985). Though degrees Celsius. Gas leak detectors are necessary in some sources claim to have developed process the storage area and the sulfonator area. An control methods employing oxidation reduction emergency eyewash shower and self-contained potential (ORP) as an effective stand-in for direct breathing apparatus should also be provided. All chlorine measurement (Bossard et al., 1995), other personnel should receive emergency response sources assert that ORP is an inappropriate training. Facilities with more than 1,000 pounds of technique for this purpose (WEF, 1996). For these SO2 stored on-site must abide by the Process reasons, control of dechlorination—particularly Management Safety Standard in the OSHA dechlorination to zero residual—has been regulations (OSHA, 1998). problematic. Treatment plant operators have had to work around this limitation using various control Effect of Temperature on Gas Withdrawal Rate strategies. The room temperature where the gas supply is One commonly used strategy is the use of a “zero- located should be maintained around 70 degrees F shifted” or “biased” analyzer (WEF, 1996; Nagel, to ensure optimal gas withdrawal rates (WEF, 1994). In this scheme, a residual chlorine analyzer 1996). At this temperature, the maximum safe is used and a known concentration, X, of chlorine sulfur dioxide gas withdrawal rate is approximately is added to the effluent sample to be analyzed. In 2 lb/hr for a 150 lb container, or 25 lb/hr for a ton this technique, the “zero” point is shifted by the container. Higher temperatures are required to value of X, and residual chlorine or sulfur dioxide achieve higher continuous gas withdrawal rates. can be inferred from the result of sample analysis. Strip heaters or liquid baths may be used for this purpose. Two types of control systems are often used for dechlorination (WEF, 1996). A “feed-back” Injector Selection control system can be used at treatment plants that are not required to dechlorinate their effluents to Proper selection of the injector is critical for proper zero levels. With feed-back control, an analyzer system operation. The injector produces a vacuum measures the chlorine residual at a point that draws sulfur dioxide gas through the downstream of the sulfur dioxide addition. This sulfonator. It then mixes the gas with dilution signal, along with flow rate data, is relayed back to water supply and injects the solution into the the sulfonator and the dosage is automatically
Details
-
File Typepdf
-
Upload Time-
-
Content LanguagesEnglish
-
Upload UserAnonymous/Not logged-in
-
File Pages7 Page
-
File Size-