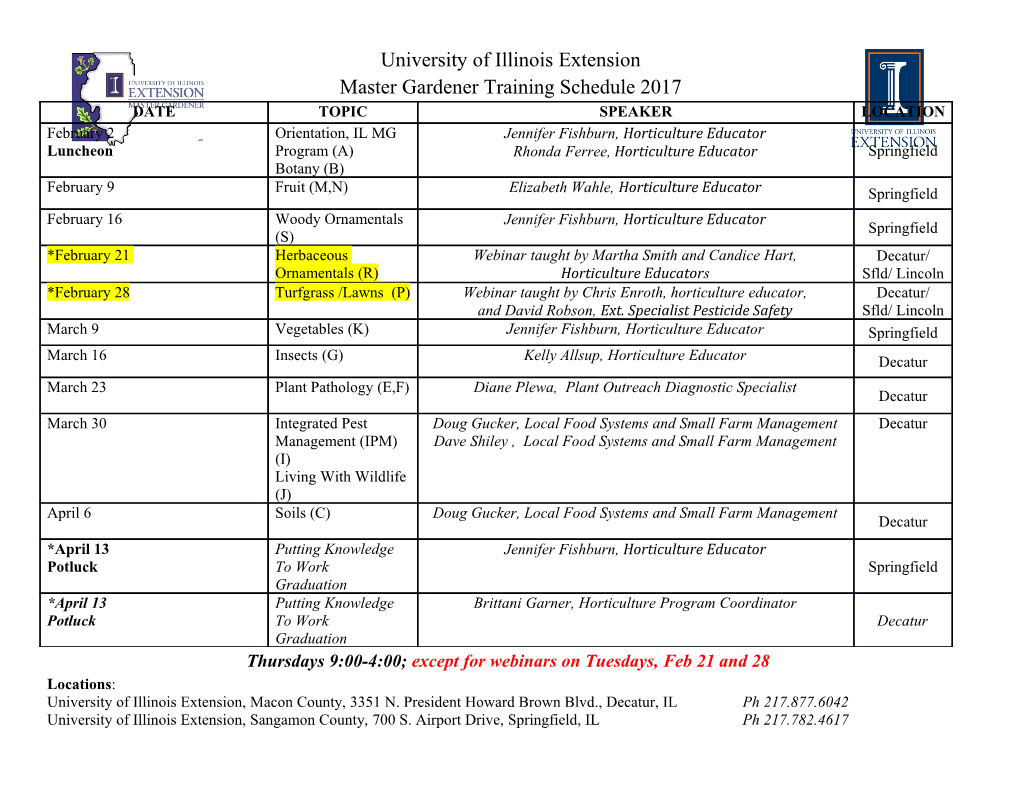
Turbo-Union RB199 Development of the F2, the first British axial flow turbo-jet, began in f 940. After initial flight trials in the tail of an Avro Lancaster, two F2s were installed in a Gloster Meteor and first flew on 13 November 1943. After early problems the F2/4 Beryl was developed which gave up to 4000 lb thrust and was used to power the Saunders Roe SR/A1 flying boat Metrovick F2/4 Beryl fighter. 16: Afterburning Contents Page Introduction 169 Operation of afterburning 170 Construction 173 Burners Jet pipe Propelling nozzle Control system 173 Thrust increase 175 Fuel consumption 178 2. Afterburning consists of the introduction and burning of fuel between the engine turbine and the jet pipe propelling nozzle, utilizing the unburned oxygen in the exhaust gas to support combustion (fig. 16-1). The resultant increase in the temperature of the exhaust gas gives an increased velocity of the jet INTRODUCTION leaving the propelling nozzle and therefore increases the engine thrust. 1. Afterburning (or reheat) is a method of augmenting the basic thrust of an engine to improve 3. As the temperature of the afterburner flame can the aircraft take-off, climb and (for military aircraft) be in excess of 1,700 deg. C., the burners are usually combat performance. The increased power could be arranged so that the flame is concentrated around obtained by the use of a larger engine, but as this the axis of the jet pipe. This allows a proportion of the would increase the weight, frontal area and overall turbine discharge gas to flow along the wall of the jet fuel consumption, afterburning provides the best pipe and thus maintain the wall temperature at a safe method of thrust augmentation for short periods. value. 169 Fig. 16-1 Principle of afterburning 4. The area of the afterburning jet pipe is larger than mixed exhaust stream. An alternative method is to a normal jet pipe would be for the same engine, to inject the fuel and stabilize the flame in the individual obtain a reduced velocity gas stream. To provide for by-pass and turbine streams, burning the available operation under all conditions, an afterburning jet gases up to a common exit temperature at the final pipe is fitted with either a two-position or a variable- nozzle. In this method, the fuel injection is scheduled area propelling nozzle (fig. 16-2). The nozzle is separately to the individual streams and it is normal closed during non-afterburning operation, but when to provide some form of interconnection between the afterburning is selected the gas temperature flame stabilizers in the hot and cold streams to assist increases and the nozzle opens to give an exit area the combustion processes in the cold by-pass air. suitable for the resultant increase in the volume of the gas stream. This prevents any increase in OPERATION OF AFTERBURNING pressure occurring in the jet pipe which would affect 7. The gas stream from the engine turbine enters the functioning of the engine and enables afterburn- the jet pipe at a velocity of 750 to 1,200 feet per ing to be used over a wide range of engine speeds. second, but as this velocity is far too high for a stable 5. The thrust of an afterburning engine, without flame to be maintained, the flow is diffused before it afterburning in operation, is slightly less than that of enters the afterburner combustion zone, i.e. the flow a similar engine not fitted with afterburning velocity is reduced and the pressure is increased. equipment; this is due to the added restrictions in the However, as the speed of burning kerosine at normal jet pipe. The overall weight of the power plant is also mixture ratios is only a few feet per second, any fuel increased because of the heavier jet pipe and after- lit even in the diffused air stream would be blown burning equipment. away. A form of flame stabilizer (vapour gutter) is, therefore, located downstream of the fuel burners to 6. Afterburning is achieved on low by-pass engines provide a region in which turbulent eddies are formed by mixing the by-pass and turbine streams before the to assist combustion and where the local gas velocity afterburner fuel injection and stabilizer system is is further reduced to a figure at which flame stabi- reached so that the combustion takes place in the lization occurs whilst combustion is in operation. 170 Fig. 16-2 Examples of afterburning jet pipes and propelling nozzles. 171 8. An atomized fuel spray is fed into the jet pipe 16-3): this latter method is known as 'hot-shot' through a number of burners, which are so arranged ignition. Once combustion is initiated, the gas as to distribute the fuel evenly over the flame area. temperature increases and the expanding gases Combustion is then initiated by a catalytic igniter, accelerate through the enlarged area propelling which creates a flame as a result of the chemical nozzle to provide the additional thrust. reaction of the fuel/air mixture being sprayed on to a 9. In view of the high temperature of the gases platinum-based element, by an igniter plug adjacent entering the jet pipe from the turbine, it might be to the burner, or by a hot streak of flame that assumed that the mixture would ignite spontaneous- originates in the engine combustion chamber (fig. ly. This is not so, for although cool flames form at Fig. 16-3 Methods of afterburning ignition. 172 temperatures up to 700 deg. C., combustion will not cooling corrugations, to form a single skin. The rear take place below 800 deg. C. If however, the of the heatshield is a series of overlapping 'tiles' conditions were such that spontaneous ignition could riveted to the surrounding skin (fig. 16-4). The shield be effected at sea level, it is unlikely that it could be also prevents combustion instability from creating effected at altitude where the atmospheric pressure excessive noise and vibration, which in turn would is low. The spark or flame that initiates combustion cause rapid physical deterioration of the afterburner must be of such intensity that a light-up can be equipment. obtained at considerable altitudes. 10. For smooth functioning of the system, a stable Propelling nozzle flame that will burn steadily over a wide range of 14. The propelling nozzle is of similar material and mixture strengths and gas flows is required. The construction as the jet pipe, to which it is secured as mixture must also be easy to ignite under all a separate assembly. A two-position propelling conditions of flight and combustion must be nozzle has two movable eyelids that are operated by maintained with the minimum loss of pressure. actuators, or pneumatic rams, to give an open or closed position (para. 4.). A variable-area propelling nozzle has a ring of interlocking flaps that are hinged to the outer casing and may be enclosed by an outer CONSTRUCTION shroud. The flaps are actuated by powered rams to Burners the closed position, and by gas loads to the interme- 11. The burner system consists of several circular diate or the open positions; control of the flap concentric fuel manifolds supported by struts inside position is by a control unit and a pump provides the the jet pipe. Fuel is supplied to the manifolds by feed power to the rams (para. 18). pipes in the support struts and sprayed into the flame area, between the flame stabilizers, from holes in the downstream edge of the manifolds. The flame CONTROL SYSTEM stabilizers are blunt nosed V-section annular rings 15. It is apparent that two functions, fuel flow and located downstream of the fuel burners. An propelling nozzle area, must be co-ordinated for sat- alternative system includes an additional segmented isfactory operation of the afterburner system, These fuel manifold mounted within the flame stabilizers. functions are related by making the nozzle area The typical burner and flame stabilizer shown in fig. dependent upon the fuel flow at the burners or vice- 16-4 is based on the latter system. versa. The pilot controls the afterburner fuel flow or the nozzle area in conjunction with a compressor delivery/jet pipe pressure sensing device (a pressure Jet pipe ratio control unit). When the afterburner fuel flow is 12. The afterburning jet pipe is made from a heat- increased, the nozzle area increases; when the resistant nickel alloy and requires more insulation afterburner fuel flow decreases, the nozzle area is than the normal jet pipe to prevent the heat of reduced. The pressure ratio control unit ensures the pressure ratio across the turbine remains unchanged combustion being transferred to the aircraft structure. and that the engine is unaffected by the operation of The jet pipe may be of a double skin construction afterburning, regardless of the nozzle area and fuel with the outer skin carrying the flight loads and the flow. inner skin the thermal stresses; a flow of cooling air is often induced between the inner and outer skins. 16. Since large fuel flows are required for afterburn- Provision is also made to accommodate expansion ing, an additional fuel pump is used. This pump is and contraction, and to prevent gas leaks at the jet usually of the centrifugal flow or gear type and is pipe joints. energized automatically when afterburning is selected. The system is fully automatic and incorpo- 13. A circular heatshield of similar material to the jet rates 'fail safe' features in the event of an afterburner pipe is often fitted to the inner wall of the jet pipe to malfunction.
Details
-
File Typepdf
-
Upload Time-
-
Content LanguagesEnglish
-
Upload UserAnonymous/Not logged-in
-
File Pages12 Page
-
File Size-