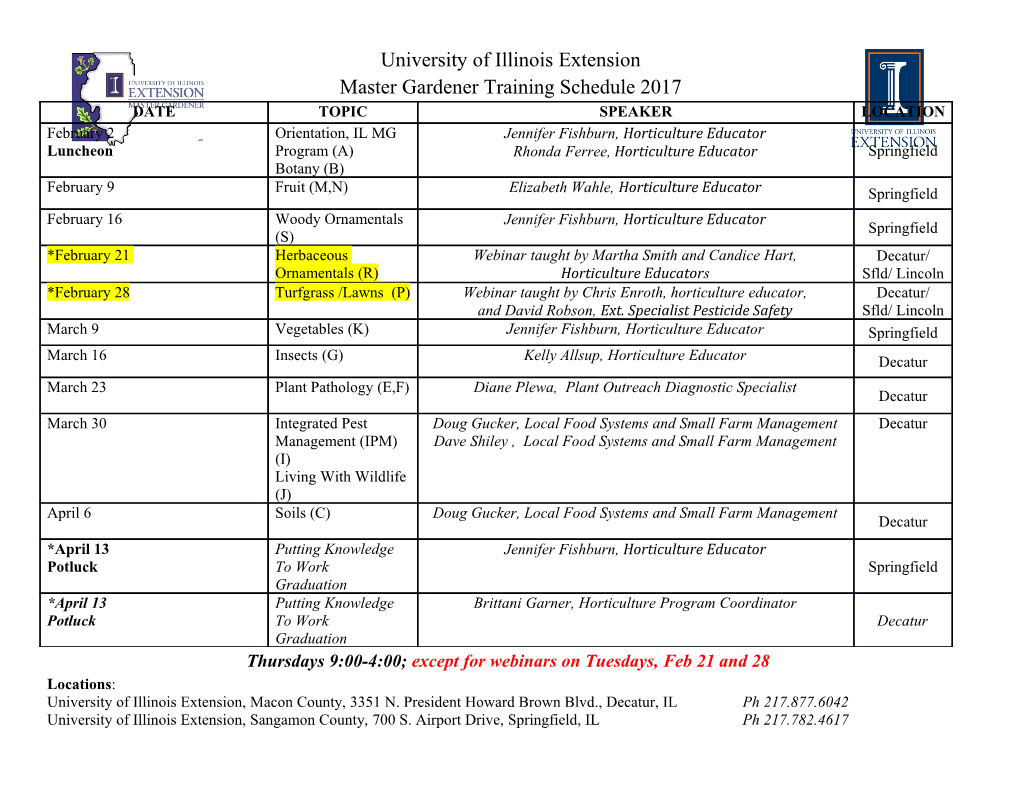
North Carolina Agricultural and Technical State University Aggie Digital Collections and Scholarship Dissertations Electronic Theses and Dissertations 2011 Impact Damage Resistance And Tolerance Of Polymer Nano-Fiber Interleaved Composite Laminates Paul Kwaku Akangah North Carolina Agricultural and Technical State University Follow this and additional works at: https://digital.library.ncat.edu/dissertations Recommended Citation Akangah, Paul Kwaku, "Impact Damage Resistance And Tolerance Of Polymer Nano-Fiber Interleaved Composite Laminates" (2011). Dissertations. 26. https://digital.library.ncat.edu/dissertations/26 This Dissertation is brought to you for free and open access by the Electronic Theses and Dissertations at Aggie Digital Collections and Scholarship. It has been accepted for inclusion in Dissertations by an authorized administrator of Aggie Digital Collections and Scholarship. For more information, please contact [email protected]. IMPACT DAMAGE RESISTANCE AND TOLERANCE OF POLYMER NANO-FIBER INTERLEAVED COMPOSITE LAMINATES by Paul Kwaku Akangah A dissertation submitted to the graduate faculty in partial fulfillment of the requirements for the degree of DOCTOR OF PHILOSOPHY Department: Mechanical Engineering Major: Mechanical Engineering Major Professor: Dr. Kunigal Shivakumar North Carolina A&T State University Greensboro, North Carolina 2011 ABSTRACT Akangah, Paul Kwaku. IMPACT DAMAGE RESISTANCE AND TOLERANCE OF POLYMER NANO-FIBER INTERLEAVED COMPOSITE LAMINATES. (Major Professor, Dr. Kunigal Shivakumar). North Carolina Agricultural and Technical State University. The primary limitation of fiber reinforced composite laminates is their poor interlaminar strength and fracture toughness that result in poor impact damage resistance and tolerance. A number of methods have been tried to address this limitation. These methods are limited by factors such as increase in cost, weight, or loss of in-plane properties. A promising approach which does not degrade the in-plane properties is interleaving. Thermoplastic particle interleaving has been applied to reinforce laminates but the primary concern of in-plane properties degradation has not been addressed. Polymer nano-fiber interleaving was investigated in this dissertation as an alternative approach to particle interleaving. The concept showed promise because of the very high surface area to volume ratio and high strain to fracture of the interleaving Nylon-66 nano- fibers. The objectives of the work were to determine the relationship between the electric field and the polymer flow-rate, to improve the electrospinning process, to assess low- velocity impact damage resistance and tolerance, and to compare the performance of the base laminate to the interleaved laminate. An electrospinning set-up with a collector current management technique was developed to match the electric field to the flow-rate. Twenty-four ply quasi-isotropic base and interleaved AS4/3501-6 composite laminates were produced. Interleaving was achieved with 0.7 g/m2 nano-fabric. The impacted specimens were retested in compression. The results showed that interleaving increased the threshold impact height and force by 26% and 13%, respectively. At 4.0 J threshold impact energy, residual compression strength was 40% for the base and 45% for the interleaved laminates. School of Graduate Studies North Carolina Agricultural and Technical State University This is to certify that the Doctoral Dissertation of Paul Kwaku Akangah has met the dissertation requirements of North Carolina Agricultural and Technical State University Greensboro, North Carolina 2011 Approved by: _________________________________ _________________________________ Dr. Kunigal Shivakumar Dr. Sameer A. Hamoush Major Professor Committee Member _________________________________ _________________________________ Dr. Samuel P. Owusu-Ofori Dr. Shih-Liang Wang Committee Member Committee Member _________________________________ Dr. Samuel P. Owusu-Ofori Dr. Sanjiv Sarin Department Chairperson Associate Vice Chancellor for Research and Graduate Dean ii DEDICATION I dedicate this success to my late father, Mr. Martin Sai Akangah, who imbued in me the spirit of hard work and compassion. iii BIOGRAPHICAL SKETCH Paul Akangah was born in Accra, Ghana to Mr. Martin Akangah and Madam Victoria Hounglah. He received his Bachelor’s degree in Mechanical Engineering from the Kwame Nkrumah University of Science and Technology (KNUST), Kumasi, Ghana, in 1993. He obtained his M.Sc degree in Mechanical Engineering from the Norwegian University of Science and Technology, Trondheim, Norway, in 1998. He was first employed at Nestle Ghana Ltd, as a Technical/Management Trainee and later promoted to Assistant Industrial Engineer. At Nestle, he was responsible for energy and utility monitoring, and capacity planning. From 2002 to 2004, he was an instructor at the Arcada Polytechnic, Espoo, Finland. He received another M.Sc degree from the Royal Institute of Technology (KTH) in Energy Engineering in 2005. From 2004 to 2006, he was an instructor at his alma mater, KNUST as well as a part-time Instructor at the Regional Maritime University (RMU) in Accra, Ghana. He enrolled in the Department of Mechanical Engineering Ph.D. program at the North Carolina Agricultural and Technical State University in 2006. His research is in the area of polymer nano-fiber interleaving and its effect on the impact damage resistance and tolerance of carbon/epoxy composite laminates. iv ACKNOWLEDGMENTS First and foremost, I would like to thank my supervisor, Dr. Kunigal Shivakumar, who provided me with guidance, support and encouragement throughout my study. Acknowledgments are also extended to my committee members, Dr. Samuel Owusu- Ofori, Dr. Shih-Liang Wang and Dr. Sameer A. Hamoush for reviewing my work and offering many useful recommendations. I am very grateful to the Center for Composite Materials Research (CCMR) at the North Carolina A & T State University (NC A&T SU) and the Department of Mechanical Engineering for the opportunity to enroll in this program. I am indebted to the following funding agencies; U.S. Army Research Laboratory-Micro Autonomous Systems and Technology, Office of Naval Research, U.S. Army Research Office, and NASA URC for their financial and technical assistance. Thanks also to the CCMR Staff, especially, Mr. Mathew Sharpe, Laboratory Manager, Dr. Shivalingappa Lingaiah, Mr. John Skujins, Prof. Robert Sadler and Mr. Jesse Chambers-an engineering graduate of NCAT and currently with Bechtel Marine Propulsions Corporation, for various assistance in completing this work. I also like to thank my fellow graduate students, especially, Anthony Cunningham, ABSM Talucdher Rupan, Ebony Adams, Mohammed Mynul and Mohammed Ali for their support. My heartfelt appreciation to Mr. Kwame Akangah and Mrs. Moniqe Fagla, who encouraged and motivated me to fight on when all hope, seemed to be lost. A special thanks to my childhood friend, Mr. Eric Fiafor, for his continual friendship. To my wife Hermione and my sons Russell and Victor for their love. To God, be the Glory! v TABLE OF CONTENTS LIST OF FIGURES .......................................................................................................... xii LIST OF TABLES.........................................................................................................xviii LIST OF SYMBOLS ....................................................................................................... xix CHAPTER 1. INTRODUCTION ...................................................................................... 1 1.1 Background........................................................................................................... 1 1.1.1 Angle-ply Laminates................................................................................. 4 1.1.2 Cross-ply Laminates ................................................................................. 7 1.2 Methods to Prevent Edge Delaminations............................................................ 10 1.3 Literature Review on Low Velocity Impact Characterization............................ 13 1.3.1 Basic Impact Mechanics ......................................................................... 13 1.3.2 Important Accomplishments in Impact Mechanics ................................ 14 1.3.3 Test Standards for Impact and Compression After Impact Tests ........... 20 1.4 Methods to Enhance Impact Damage Resistance and Tolerance ....................... 22 1.4.1 Matrix Toughening Method.................................................................... 22 1.4.2 Through-the-thickness Reinforcement Method ...................................... 23 1.4.3 Interleaving Method................................................................................ 24 1.5 Limitations of Current Methods.......................................................................... 28 1.6 The Polymer Nano-fiber Interleaved Concept.................................................... 29 1.7 Goals and Objectives .......................................................................................... 30 1.8 Scope ................................................................................................................ 31 vi CHAPTER 2. ELECTROSPINNING PROCESS AND IMPROVEMENTS ................. 32 2.1 Introduction......................................................................................................... 32 2.2 Electrospinning at CCMR..................................................................................
Details
-
File Typepdf
-
Upload Time-
-
Content LanguagesEnglish
-
Upload UserAnonymous/Not logged-in
-
File Pages199 Page
-
File Size-