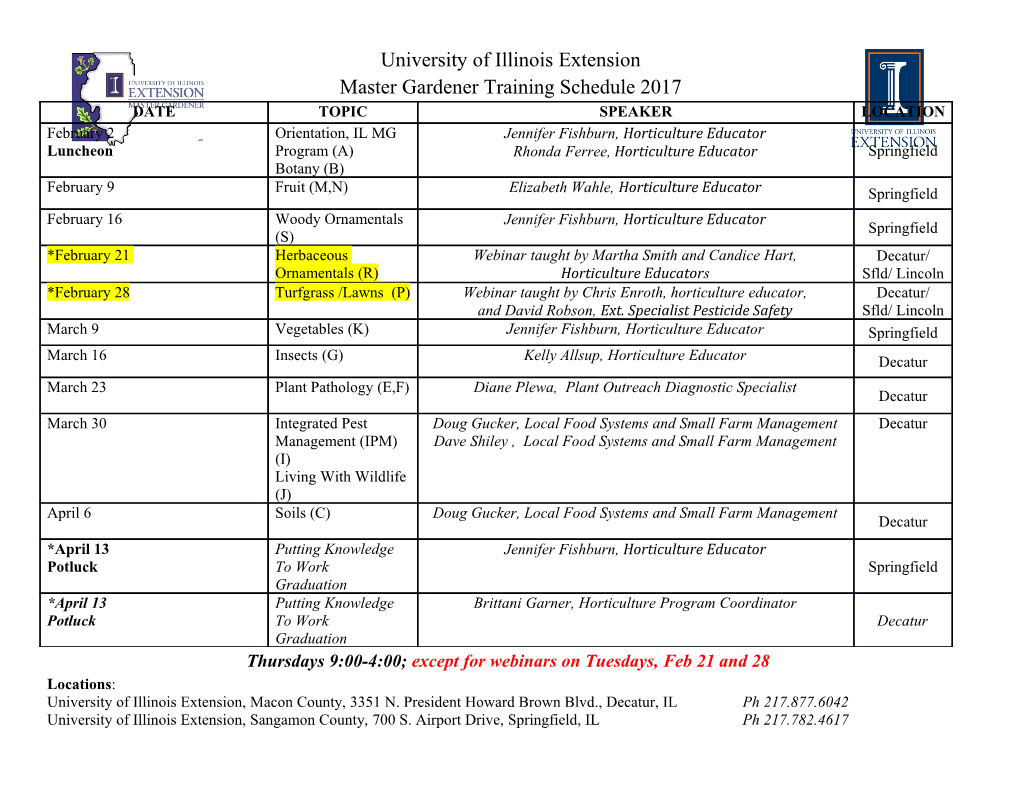
N O T I C E THIS DOCUMENT HAS BEEN REPRODUCED FROM MICROFICHE. ALTHOUGH IT IS RECOGNIZED THAT CERTAIN PORTIONS ARE ILLEGIBLE, IT IS BEING RELEASED IN THE INTEREST OF MAKING AVAILABLE AS MUCH INFORMATION AS POSSIBLE NEAR TERM HYBRID PASSENGER VEHICLE DE'. ELOFMEN7 YRGGRAA, PHASE I COYTRACT NUMBER 955188 FINAL REPORT MINICARS, INC. 55 DEPOT ROAD GOLETA, CALIFORNIA 33017 ~f Tecnn~log;), 5poqsoreci 9y the National Aeronautics and Space Adninistra ti on . I (AASA) under Contract N.AS7- ICO, pursuaat to an intera~ency3yreement letw2en the Departnent ~f Enqy [DOE) a11d ?Il;SA. I 55 Depc,t Road, Goleta. California 9301 7 (805) 964-6271 TELEX 677605. Telecopier (805) 964-7669 MIni cars Report Number FR-4500-09-79- II NEAR TERM HYBRID PASSENGER VEHICLE DEVELOPMENT PROGRAM, PHASE I Contract Number 9551 88 FINAL REPORT September 1979 VOLUME I1 Prepared by MINICARS, INC. 55 Depot Road Goleta, Cal ifornia 9301 7 This work was performed for the Jet Propulsion Laboratory, Cal ifornia Institute of Technalogy, sponsored by the National Aeronautics and Space Administration (NASA) under Contract NAS7-100, pursuant to an Interagency Agreement between the Department of Energy (DOE) and NASA. TABLE OF CONTENTS APPENDIX - TITLE PRELIMINARY DESIGN DATA PACKAGE SENSITIVITY ANALYSIS REPORT This rc~ortcontains information prepared by Minicars, Inc. under JPL sub-contract. Its content is not necessarily endorsed by tha Jet Propulsion Laboratory, California Institute of Technology, or the National Aerona-utics and Space Administration. 27 August 1979 The present document is a revised version of the Minicars, Inc. Preliminary Design Data Package", dated 25 July 1979. The revision consists primarily of an adden- dum, which is included at the end of the reDort.- -L - Othenrise, only minor changes (most1,y typographical) have been made in the--- - test itself. It should be noted that in some cases (notably, the electronic control system hardware design), the pre- liminary design has been supplemented in Minicars' Technical Proposal for Phase 11 of the Near Term Hybrid Vehicle Program. SUBMITTED BY: MINICARS, INCORPORATED 55 DEPOT ROAD GOLETA, CALIFORNIA 93017 TABLE OF CONTENTS Section Page 1 IKTRODUCTION .................... 1 TRADE-OFF STUDY SUMMARY RESULTS * * 4 2.1 Weight .................... 4 2. 2 Powertrain Configuration ........... 4 2.3 SubsystemSizing ............... 4 2.4 SubsystemBelection .............. 5 2.5 Regenerative Braking and Environmental Control 5 2.6 Operational Strategy ............. 5 VEHICUUYOUT ................... 6 3.1 Designconcept ................ 6 3.2 Base Vehicle Selection ............ 6 3.3 Battery Pack Configuration .......... 7 3.4 Vehicle Size and Weight ...... ....... 12 3.5 Structural Modifications ........... 13 3.6 Occupant Crash Protection ........... 25 3 .7 Vehicle Dynamics ............... 42 3.8 Aerodynamics ................. 48 DRIVETRAIWnXSIGN ................. 51 4.1 Transnission Concept Selection ......... 51 4.2 Transmission Dssign .............. 56 4.3 Coupling Devices ............... 72 4.4 Accessory Drive ................100 4.5 Powertrain Integration ............ 104 4.6 DicselEngine .................104 4.7 ElectricMotor ................109 POWER CONDITIONING UNIT ..............113 5.1 Introduction ................. 113 5.2 Field Controller Requirements .........113 5.3 Field Controller Design Approaches ......114 5.4 Battery Charger Requirements . 115 5.5 Charger Design Approaches . 115 5-6 Overall ~otoz. Control System Operation 116 5.7 Power Transistor Selection ..........i16 5.8 Detailed Circuit Description 118 5.9 Power Electronics Assembly Packaging 124 BATTERYSUBSYSTEM ................ -125 TABLE OF CONTENTS ~Cont'd) Section Page 6.1 Selection of Battery Type ........... 125 6.2 Duty Cycles and Vehicle Requirements ..... 126 6.3 Battery Charger ................ 128 6.4 Battery Thermal Acquirements ......... 129 6.5 Battery Container Design ........... 130 CONTROL SYSTEM .................. 7.1 NTHV Control System Preliminary Design ... 7.2 Identification of Control System Requirements 7.3 Software Algorithm Characterizations .... 7.4 Selection of System Designs and Candidate Processors ................. 7.5 Sensor and Actuator Characteristics ..... 7.6 Display Characteristics and Human Factors Considerations ............... 7.7 NTHV Microcomputer System Design ...... 7.8 NTHV Diagnostic Systems ........... 7.9 Power Supply ................ 7.10 Power and Ground Design Considerations ... 7.11 Electromagnetic Compatibility Considerations 7.12 Control System Integration ......... ENVIRONMENTAL SYSTEM ................ 194 8.1 Heating .................... 194 8.2 Airconditioning ............... 197 8.3 CompressorDrive ............... 197 8.4 Effects on Operational Strategy ........ 197 PRELIMINARY DESIGN NTHV SPECIFICATIONS ....... 199 TECHNOLOGY REQUIREMENTS .............. 209 DATA SOURCES AND ASSUMPTIONS ............ 211 11.1 List of Data Sources Used .......... 211 11.2 List of Significant Assumptions 211 References ........................ 214 Appendix P .Control System Algorithms . 217 Appendix B .Control System Design Considerations 223 Appendix C .Built-in Testinq Design . 228 Appendix D .Example of a Microprocessor Timing Layout 233 Addendum to Preliminary Design Data Package .Design Options AA1 iii LIST OF ILLUSTRATIONS Figure Title Page Minicars Near Term Hybrid Vehicle .......... Configuration A ................... Configtiration B ................... Configuration C ................... Configuration D ................... Crash Pulse for 1980 Chevrolet Citation: 35 mph Frontal Barrier Impact ............... Body Structure Reinforcements ............ Body Structure Reinforcements .Rear ........ Front Suspension Arrangement ............ Front Suspension Strut Details ........... Front Suspension Reinforcement ........... Rear Suspension Reinforcements ........... Existing Citation Dashboard ............. ACRS Citation Dashboard ............... VW Passive Belt Knee Restraint Bar ......... VW Passive Belt Knee Restraint Bar Cross Section . GM ACRS Steering Whee! . and Driver Module ...... GM ACRS Column Mast and Slip Rate Assembly ..... Tube/Mandrel Steering Shaft Assembly ......... Ganged Driver Inflator Module. Pan Front ...... RSV Door Interior ............. .... LRSV Door Interior ................. NTIIV Rack and Pinion Steering Gear System ...... NTHW Diagonal Split Brake System ........... Comparison of Citation and NTHV Aerodynamics .... Transmission Power Loss - Typical Automatic and Manual Transmission ................. Transmission Power Loss - Low Loss Automatic and Automated Manual Transmissions ........... Volkswagen Rabbit Automatic Transmission ...... Chrysler A-404 Automatic Transmission ........ General Motors TH-125 Automatic Transmission .... General Motors TH-125 Automatic Transmission Modified for NTHV .................. Chrysler A-404 Automatic Transmission Modified foz NTHV ........................ TH 125 Hydraulic Oil Circuit ............ Typical Shift Pattern for an Automatic Transmission . Shift Pattern - Typical Automatic Transmission . LIST OF ILLUSTRATIONS (Cont' d) Figure No. Title -Page 4-11 Shift Pattern for Best Economy - Diesel Engine Only . 71 4-12 Shift Pattern for Best Efficiency - Electric Motor Only . 72 Driving Force vs. Vehicle Speed for a Typical Engine and Transmission . 73 Clutch Engagement at Minimum RPM and Maximum Torque 74 Wide Open Throttle Driving Force vs. Speed . 75 Three Element Hydrodynamic Torque Converter . 76 Torque Converter Oil Flow . 76 Torque Converter Performance Curve . 77 Torque Converter fnput Speed and Torque for Various SpeedRatios......... ............ 7g Input Speed vs. Torque for the Engine and Torque Converter Cambination . 79 Torque Converter Output Torque vs. Output Speed . 80 Torque Converter Performance, Chrysler A 397 . 83 Torque Converter Output Torque vs. Output Speed, Turbocharged VW Diesel/Chrysler A-398 Converter . 84 Cross Section of Lock-up Torque Converter - = . 85 MotorO~tp~t..................... 86 Torque Converters for Field Control Electric Motor . 87 Range of Converter Output Field Control Motor withTorqueConverterA . 83 Range of Converter Output Field Control Motor withTorqueConverterB . 89 Range of Converter Output Field Control Motor with TorqueConverterCo . * . 89 Range of Clutch Output Field Control Motor with Cl~t~h........................ 89 Fluid Coupling . 9; Fluid Coupling Perforinance Curve . 94 Effect of Fluid Coupling Fill on Zero Speed Ratio IIIPU~S... 95 Torque Converter . 97 1956 Twin Coupling Hydramatic . - 97 Accessory Drive Concept . i03 DrivetrainPackage . .lo5 Drivetrain Package . 106 DrivetrainPackage . 107 MotorOutputat70Volts. 110 LIST OF ILLUSTRATIONS (Contld) Figure No . Title Page 4-41 Motor Power Output with 72 Volt Battery Pack. 24 KW MI Compound Motor with Field Control ......111 Proposed Electric Motor ................112 Field Saturation ...................114 Power Conditioning System ..............117 Field/Charger Power Electronics Assembly .......119 Current Control Loop .................120 Current Control ~oopResponse Waveforms .......121 aattery Contaicer Construction ............132 Battery Container Assembly ..............133 ~ethodoiod~utiiited in <he devclcpment oi the Control System Preliminary Design ......... 135 Example of Controllable Software Timing ....... 146 Layout in a Selected Executive .VOS Operating Mode for Use on Powertrain Controller Microprocessor Single Mjcroprocessor System ............ 155 Dual Microprocessor System ............. 156 Micro?rocessor
Details
-
File Typepdf
-
Upload Time-
-
Content LanguagesEnglish
-
Upload UserAnonymous/Not logged-in
-
File Pages354 Page
-
File Size-