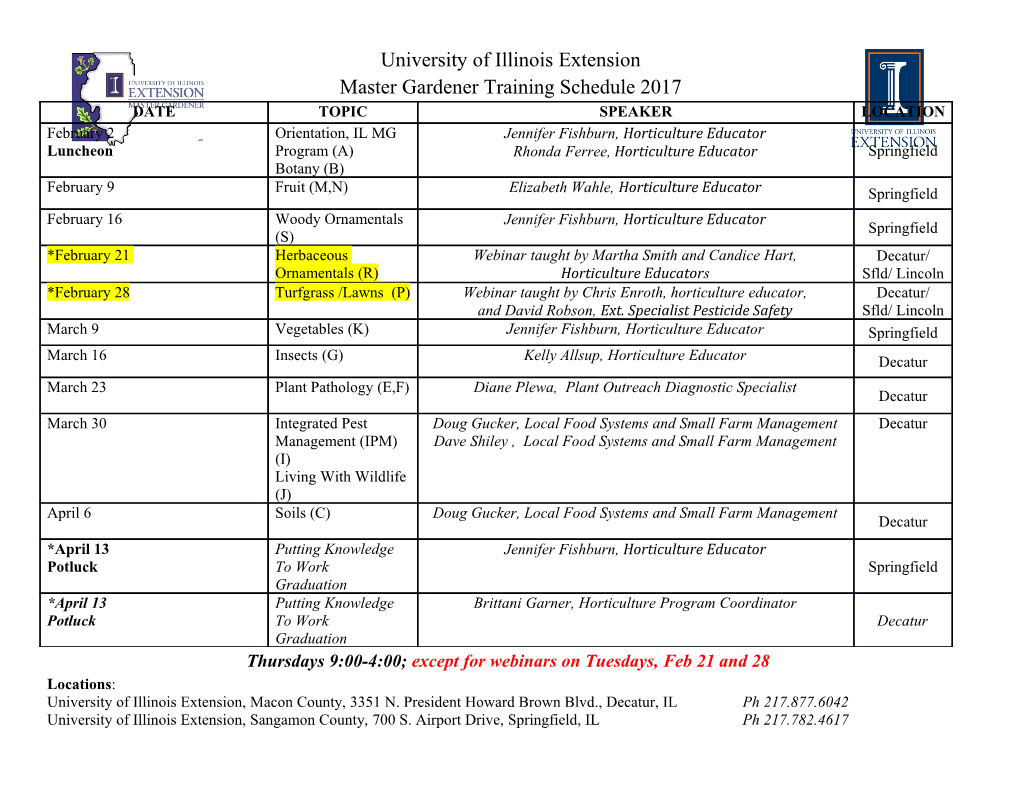
Struct Multidisc Optim DOI 10.1007/s00158-010-0612-9 INDUSTRIAL APPLICATION Development of a framework for truss-braced wing conceptual MDO Ohad Gur · Manav Bhatia · William H. Mason · Joseph A. Schetz · Rakesh K. Kapania · Taewoo Nam Received: 3 June 2010 / Revised: 18 October 2010 / Accepted: 10 December 2010 c Springer-Verlag (outside the USA) 2011 Abstract The paper describes the development of a mul- Abbreviations tidisciplinary design optimization framework for con- ceptual design of truss-braced wing configurations. This (·)break break section unconventional configuration requires specialized analysis (·)cr cruise tools supported by a modular and flexible framework to (·)jury jury accommodate different configurations. While the previous (·)root root section framework developed at Virginia Tech was a monolithic (·)strut main strut Fortran-77 code, the need for more flexibility for com- (·)tip tip section plex truss-braced wing configurations was addressed by (·)wing wing the development of this new framework, which is based on Phoenix Integration ModelCenterTM environment. The Nomenclature framework uses updated structural and aerodynamic de- sign modules that enable a more general geometry defini- A cross-sectional area tion. The new framework, thus, provides a foundation AC load-bearing cross-sectional area for future design concepts, especially multi-member truss- b wing span braced wing configurations. The fuel saving potential of CLα vehicle lift coefficient slope these truss-braced wing configurations is presented by com- c chord paring different truss designs with gradually increased level cavg average chord of complexity. cfuel fuel-tank chord cst wing-box chord Keywords MDO · Truss-Braced Wing · Framework · D drag Design environment dnacelle, lnacelle diameter and length of the engine nacelle, respectively E1, E2 Young’s Modulus of the wing skin and spar webs, respectively (EI)xx,(EI)zz bending stiffness The paper was presented as AIAA Paper 2010-2754 in the 6th AIAA F shear force Multidisciplinary Design Optimization Specialist Conference, s April 12–15, 2010, Orlando, Florida. (GJ) torsion stiffness G , G Shear Modulus of the wing skin and O. Gur (B) · M. Bhatia · W. H. Mason · 1 2 J. A. Schetz · R. K. Kapania spar webs, respectively Virginia Polytechnic Institute and State University, g acceleration of gravity Blacksburg, VA 24061-0203, USA Kg gust alleviation factor e-mail: [email protected] L lift T. Nam M Mach number Georgia Institute of Technology, Atlanta, GA 30332-0150, USA m vehicle mass O. Gur et al. ng gust load factor 1 Introduction q shear flow q0 constant shear flow in the skin to sat- A CONCEPTUAL design is a complex process that com- isfy the requirement of closed-beam bines analyses from a variety of disciplines. The design section environment framework should connect the various dis- qT shear flow in the skins ciplinary analyses while enabling easy replacement and Rel chordwise Reynolds number upgrading of these disciplinary analyses. This is especially SFlaps flap area true in a case where unconventional air vehicle configu- SFuel,CS cross sectional area of the fuel tank rations are to be designed requiring generalized analysis Sref reference area modules. This paper describes the development of a Truss- SW wing area Braced Wing (TBW) design framework, concentrating on s non-dimensional coordinate the challenges of modeling and designing this revolutionary Tmax .req maximum required thrust configuration. TSFCcr cruise thrust specific fuel consumption Various descriptions of conceptual-design frameworks TSFCSLS static sea level thrust specific fuel are available in the literature. Each framework puts the consumption emphasis on a different topic. For example, the framework t cross sectional thickness developed by Perez et al. (2006) is concentrated on design- t¯ average skin thickness ing the vehicle control system. Thus, most of the develop- t0, t1 lower and upper locations of the wing ment effort in that was invested towards studying the control skin, respectively system analysis. Mukhopadhyay (2007) reviews several t2 skin thickness of the leading and trail- cases of conceptual design with emphasis on the struc- ing edge spar webs tural analysis. He presents design examples for conventional tnew, told new and old skin thickness, airliners, a Blended Wing Body (BWB) configuration, a respectively High Altitude Long Endurance (HALE), and space vehicles. tstress, tbuckling thickness required to satisfy the stress Antoine and Kroo (2005) concentrate on the noise and emis- and buckling limits, respectively sion analyses, along with an aerodynamic analysis to design u,w transverse and chordwise bending de- environmental-friendly vehicles. formations, respectively During the 1950’s, Pfenninger (1976) proposed the de- V airspeed sign of a truss-braced wing to achieve a reduction in both VG gust velocity the thickness to chord ratio, wing sweep, and an increase Vx , Vz transverse shear forces in the wing span so as to reduce the structural weight, W1, W2, W3 FLOPS wing weight parameters but with complex topology as shown in Fig. 1. Following WBM bending material weight Pfenninger’s lead, the concept of a Strut-Braced Wing Wengine engine weight Wfold wing folding mechanism weight Wi , W f initial and final weight, respectively Wref , lref , dref , Tref weight, length, diameter, and thrust, of reference engine, respectively WSM shear material weight X, Y , Z coordinates α angle of attack ε A axial strain η integration parameter ηc convergence factor ηfold non-dimensional spanwise fold location θ y torsional rotation 0.25 quarter chord sweep μg mass ratio ρ air density σ air density ratio σ A axial stress Fig. 1 One of Pfenninger’s visions (1976) for a truss braced wing σ B longitudinal stress aircraft Development of a framework for truss-braced wing conceptual MDO (SBW) configuration was investigated using Multidisci- minimum TOGW objective function probably represents plinary Design Optimization (MDO) tools (Grasmeyer the most commonly used goal, and emphasizes a lower 1999; Gundlach et al. 2000). The framework used for these life-cycle cost, while the minimum fuel objective function studies was written at the late 1990’s using a monolithic emphasizes lower operational cost and lower emissions. Fortran-77 code. Comparison of the designs resulting from these goals sheds This paper describes the development of a new frame- light on the design limits and trends. The new design envi- work which enables an extended design domain to a multi- ronment enables rapid change of the cost function using the member TBW and other futuristic concepts which include ModelCenterTM drag-and-drop feature. complex topology. To enable treatment of a more general Design constraints are imposed on performance, such topology, a specialized parametric geometry was devel- as: take-off and landing field length, minimum rate-of- oped. The various analysis and design modules were then climb after take-off, single engine flight, etc. Additional written to comply with this new parametric geometry. The constraints are imposed on maximum tip deflection while paper includes a description of these modules with empha- encountering a taxi bump and sufficient fuel capacity as dic- sis on their compatibility to the TBW configuration. In tated by the mission. Again changing the constraints and addition, the need for a modular design environment that their limit values can be done in an easy manner using the supports future developments, leads to the use of Phoenix new design environment. Integration’s ModelCenterTM (2009), which supports such The design variables may include any of the geometric a dynamic and flexible framework. parameters for both the wing and the tail: wing span, wing Last, the paper presents representative results for a min- thickness-to-chord ratios, chords, and sweep; strut/truss imum fuel/emission design problem. The design process length; and some operational variables such as: required was conducted using four different configurations: can- thrust and cruise altitude. tilever, single strut SBW, jury-TBW, and 2-jury TBW. The cross comparison between these configurations empha- 3 Framework description sizes the advantage of TBW airplanes over conventional configurations. Past results (Grasmeyer 1999; Gundlach et al. 2000)forthe TBW design case were obtained using a monolithic code. 2 TBW problem statement This code was written using Fortran 77, and it uses a file based user interface. The outline of the old framework com- The main TBW design requirement is the accomplishment ponents is shown in Fig. 3. The main analyses (propulsion, of a mission which is defined here as flying a range of 14,316 km (7,730 NM) with 305 passengers (see Fig. 2), Baseline Design which is very similar to that of the Boeing 777-200ER. It is assumed that the aircraft has the same fuselage as that of a Boeing 777. The aircraft is outfitted with a high-wing inte- Preprocessing grated with truss structures and a T-tail, and is powered by two, high bypass-ratio, turbofan, fuselage mounted engines. Weight Various goals can be considered when designing an air- Convergence vehicle (Jensen et al. 1981; Malone and Mason 1996), Optimizer Propulsion System with an appropriate definition of the objective function for each goal. Possible goals may be one of the following three: minimum Take-Off Gross Weight (TOGW), mini- Aerodynamic mum fuel/emissions, and maximum lift-to-drag ratio. These three figures-of-merits represent different emphases. The Performance, Structural Design Mach 0.85 Mach 0.85 Cost Function, Module Constraints Climb 69.44 m/sec (135 kn) Approach Speed Weight Estimation 348 km (350 NM) 3353 m (11,000 ft) 14,316 km (7,730 NM) 3,353 m (11,000 ft) Reserve Range T/O Field Length Range LDG Field Length Fig. 2 Basic mission used for our design Fig. 3 Old framework components O. Gur et al. aerodynamics, structures, and weight estimation) are in a d. Connecting the old framework to other design frame- weight convergence loop, while the calculation of the design works or additional analysis modules requires a spe- goals and constraints is done as part of the outer optimiza- cially developed interface.
Details
-
File Typepdf
-
Upload Time-
-
Content LanguagesEnglish
-
Upload UserAnonymous/Not logged-in
-
File Pages22 Page
-
File Size-