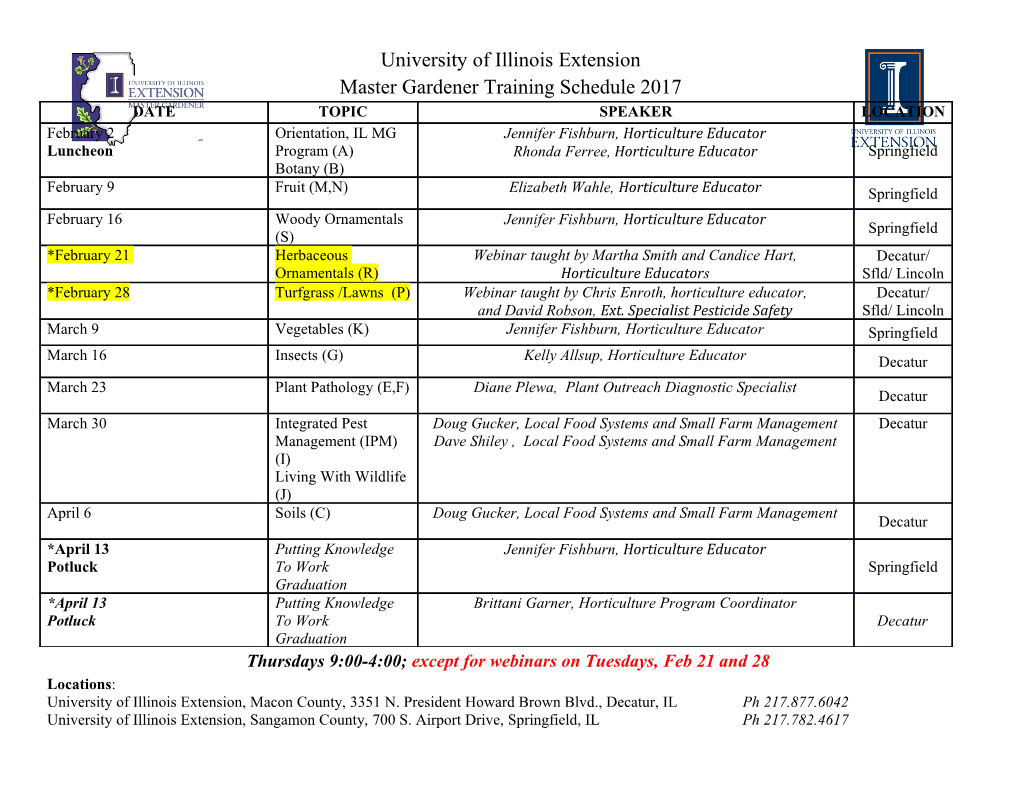
HORIZONTAL TAIL LOCA L ANGLE -OF -ATTACK AND TOTAL PRESSURE MEASUREMENTS THROUGH STATIC PRESSURE PORTS AND KIEL PITOT Rodrigo M. Granzoto*, Luiz A. Algodoal V.*, Gustavo J. Zambrano*, Gilberto G. Becker* *Embraer S.A Keywords : aerodynamics; CFD; flight-test; horizontal tail; angle-of-attack; sensor calibration Abstract horizontal tail area combined with more aft Aircraft handling qualities may be influenced by center-of-gravity positions, have led to a wing tip flow separations and horizontal tail concern over achieving more critical stability reduced efficiency caused by loss of local and controls characteristics during stall dynamic pressure or local tailplane flow maneuvers. Particularly, the aircraft handling separations in high angle-of-attack maneuvers. qualities characteristics may be influenced by From the flight testers perspective provided the wing tip flow separations and horizontal tail test aircraft presents sufficient longitudinal reduced efficiency caused by loss of local control authority to overcome an uncommanded dynamic pressure or local tailplane flow nose up motion, this characteristics should be separations in high angle-of-attack maneuvers. no safety factor. From the flight testers perspective, provided the Monitoring and measuring the local airflow in test aircraft presents sufficient longitudinal aircraft horizontal tail (HT) provides, control authority to overcome an eventual information for safe flight test envelope uncommanded nose up motion, this expansion and data for early aerodynamic characteristics should be no safety factor. knowledge and model validation. Once the flight mechanics analysis of test This work presents the development, airplane showed the longitudinal control installation, pre-flight calibration using authority to be safe enough to cope with all the computational fluid dynamics (CFD), flight test test conditions, there will still be the need for calibration, results and benefits of differential real time monitoring during the test execution to pressure based local angle-of-attack and total assure the assumptions and the models used for pressure measurements through 20 static all the previous analysis were valid. pressure ports and a Kiel pitot. These sensors were installed in a single-aisle, Two key parameters have been successfully four-abreast, full fly-by-wire medium-range jet used in flight to accomplish this need for real airliner with twin turbofan engines and time monitoring: conventional horizontal tail (low vertical • Horizontal tail local angle-of-attack position). (αHT ); and • Dynamic pressure measurements, 1 Introduction particularly the ratio between the free As an important part of the preparation for the stream dynamic pressure and the high incidence envelope expansion flight test horizontal tail local dynamic pressure campaign, the aircraft longitudinal stability and (η). the possible tendency for uncommanded pitch The first one ( αHT ) copes with the risk of movements must be considered. Newer aircraft reaching a tailplane stall, which decreases models, with increased aspect ratio and swept aircraft longitudinal stability and may lead to an wings, higher efficiency flaps, higher bypass uncommanded pitch movement. The second one engines (increased diameter) and, finally, lower 1 R. M. GRANZOTO, L. A. ALGODOAL V., G. J. ZAMBRANO, G. G. BECKER (η) copes with a possible reduction in The static pressure ports were designed to be longitudinal stability and control authority of a located on the leading edge of HT. This location non-stalled tail due to low dynamic pressure was chosen due to two different aspects: (i.e. due to engine or wing flow paths passing 1. Presents a higher sensitivity of static thought the tail position). pressure coefficient (C P) due to αHT Monitoring and measuring the local airflow in variation, aircraft horizontal tail (HT) provides, thus, 2. Easiness of installation and maintenance, information for safe flight test envelope once the pressure transducers can be expansion and data for early aerodynamic installed with the removal of the horizontal knowledge and model validation. tail leading edge, which is usually This work presents the development, removable in most airplanes for several installation, pre-flight calibration using other reasons (for example anti-ice piccolo computational fluid dynamics (CFD), flight test tubes installation). calibration, results and benefits of differential As the differential pressure ports are susceptible pressure based local angle-of-attack and total to blockage and local disturbances and pressure measurements through 20 static considering the safety effects of a wrong pressure ports and a kiel pitot. measure for real time monitoring during flight These sensors were installed in a single-aisle, test, it was chosen a conservative, robust and four-abreast, full fly-by-wire medium-range jet redundant design: the differential pressure ports airliner with twin turbofan engines and were distributed along ten chord positions for conventional horizontal tail (low vertical two distinct sections along the HT span. For this position). purpose, an averaging and a voting algorithm were employed for the final αHT measurement. 2 Sensors Installation Fig 1 shows the schematic architecture of the system. Once identified the need for real-time monitoring of HT local angle-of-attack, several options of different sensors were considered. Most of the available sensors, such as angle-of- attack vanes, smart probes, etc would have similar calibration challenges, but would significantly affect the HT structural characteristics; in addition, most of already available sensors, due to its size and ideal locations were considered to interfere with the α local airflow, thus interfering with the local HT Fig 1 – Schematic system architecture of the measurement itself. system The search for a local angle-of-attack measurement that would not significantly affect the HT structural design and also be non Considering the needs for quick time response, airflow-interferant led to a differential static good accuracy and resolution, the Honeywell pressure solution. This solution only requires PPT0002DNN2VB-S068 differential pressure small pressure ports (small holes) adequately sensor was chosen. located to be sensible to small pressure differences between the upper and lower surfaces of the HT airfoil. Those differential Honeywell PPT0002DNN2VB-S068 pressure measures are physically correlated to specifications[4]: local AOA variations. Digital Accuracy: ±0.05% FS 2 HORIZONTAL TAIL LOCAL AOA AND PT MEASUREMENTS THROUGH STATIC PRESSURE PORTS AND KIEL PITOT Analog Accuracy: ±0.06% FS To develop the proper correlation between Operating Temperature: -40 to 85ºC differential pressure and local angle-of-attack, Storage Temperature: -55 to 90ºC an estimation of the αHT (pre-flight) was done Sample Rate: 8.33ms to 51.2min using CFD. Digital Resolution: up to ±0.0011% FS The local α measure was assumed to be Analog Resolution: 1.22mV HT comprised of the following components: Long Term Stability: 0.025% FS per year Range: ±2 psi 1. Effects of pressure coefficient and elevator deflection on αHT (αHT1 ), since the local Since the PPT0002DNN2VB-S068 needs to be pressure and lift distributions are directly connected to the reference pressure using correlated with local angle of attack and capillary tubes, to avoid a possible pressure elevator deflection. wave lag in the final measure, a single static 2. Effect of aircraft free stream angle of attack pressure (P ref ) reference port was chosen and (α) and flap angle ( αHT2 ), since the wing lift positioned as close as possible to transducers and downwash interferes with local HT minimizing the tubes length and consequently airflow and changes the chordwise and its internal air volume. The P ref was located in spanwise distribution of local lift on HT. the lower side of HT. 3. Effect of HT incidence ( αHT3 ), since the The local dynamic pressure was measured relative geometric position of HT changes through a kiel pitot installed on the lower side of the aerodynamic interference characteristics the HT using a pre-existent access panel for between wing-tail and fuselage-tail, thus easiness of installation and maintenance. The changing local HT pressure distribution. Kiel pitot vertical position was chose to keep it α out of the boundary layer. In order to derive the relations to calculate HT1 , α α Fig 2 provides detailed information for the ΗΤ2 and HT3 , CFD Simulations were position of installed pressure ports, pressure performed with Metacomp Technologies transducers and kiel pitot. CFD++ code[1], to simulate subsonic airflow conditions. Three different types of CFD simulations were run: • Wing-Body-Pylon-Nacelle tailless aircraft (WBPN); • Body-Horizontal-Tail (BH) wingless aircraft, with different elevator deflections; Fig 2 - HT sensors positions and installation • Complete aircraft (WBPNH) with horizontal tail incidence variation. 3 Pre-Flight Sensors Calibration The non-interfering differential pressure solution adopted does not provide a direct local AOA measurement thus requiring means to convert differential pressure measurements in angle-of-attack measurements. 3 R. M. GRANZOTO, L. A. ALGODOAL V., G. J. ZAMBRANO, G. G. BECKER The αHT2 was calculated using WBPN CFD runs with wing interference results calculated at 25% of local HT chord virtual position for each spanwise HT section, as it may be seen by Fig 5. Fig 6 shows the local alpha spanwise distribution as a function of free-stream α for
Details
-
File Typepdf
-
Upload Time-
-
Content LanguagesEnglish
-
Upload UserAnonymous/Not logged-in
-
File Pages10 Page
-
File Size-