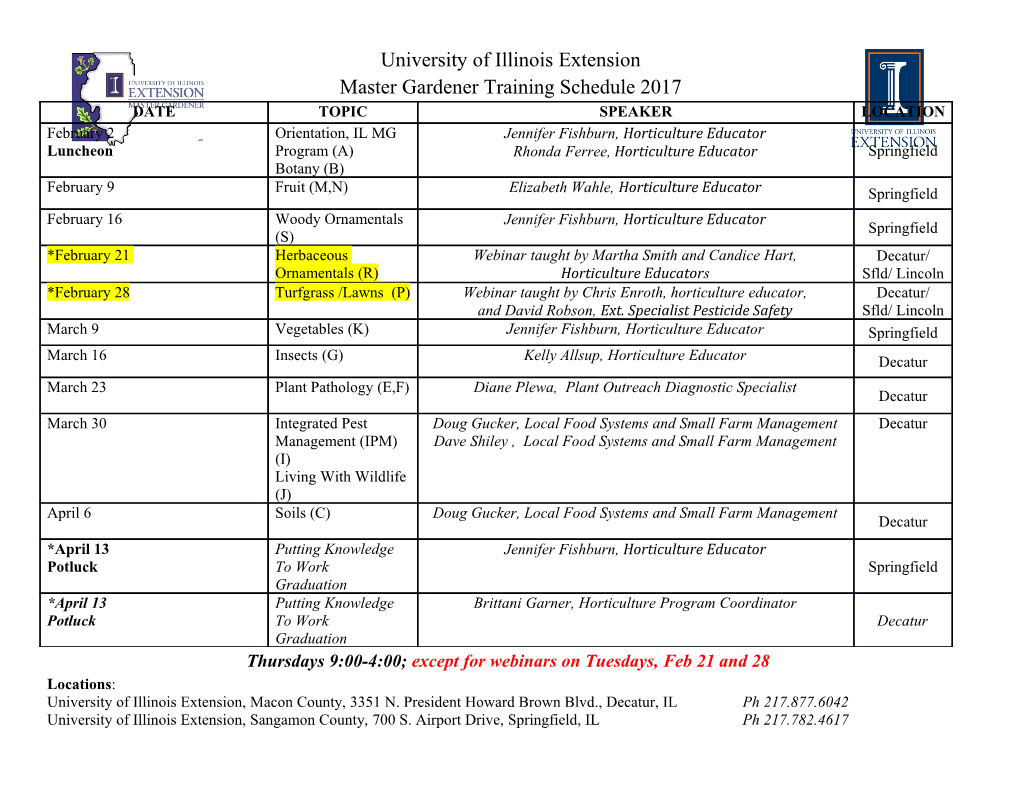
Section 6.1: The TurboFan Propulsion Cycle MAE 6530 - Propulsion Systems II 1 Overview MAE 6530 - Propulsion Systems II 2 Overview (2) • Turbofan engine is the most modern variation of the basic gas turbine engine. • As with other gas turbines, there is a core engine, whose parts and operation are nearly identical to the turbojet operation. • In the turbofan engine, the core engine is surrounded by a fan in the front and an additional turbine at the rear. MAE 6530 - Propulsion Systems II 3 Overview (3) MAE 6530 - Propulsion Systems II 4 Overview(4) • Turbofan engines power now all civil transports flying at transonic speeds up to Mach 0.9. • Several advantages to turbofan engines over both propeller-driven and turbojet engines • By enclosing fan inside a duct or cowling, aerodynamics are better controlled. • Fan is not as large as propeller, so increase of speeds along blade is less, and there is less chance of tip stall and shock wave development. • Turbofan can suck in more total air massflow than a turbojet, thus offer potential for generating more thrust. • Turbofan has low fuel consumption compared with turbojet. MAE 6530 - Propulsion Systems II 5 Jet Engine Performance Efficiency (revisited) Ratio of Power Developed from Engine (desired beneficial Propulsive Efficiency output) Thrust to Change in Kinetic Energy of the Moving Airstream (cost of propulsion) Propulsive power Kinetic energy production rate Maximum propulsive efficiency achieved by generating thrust moving as much air as possible with as little a change in velocity across the engine as possible. MAE 6530 - Propulsion Systems II 6 Jet Engine Performance Efficiency (2) • Maximum propulsive efficiency achieved by generating thrust moving as much air as possible with as little a change in velocity across the engine as possible. .. Fan provides that function MAE 6530 - Propulsion Systems II 7 Jet Engine Performance Efficiency (3) • Recall that optimal thrust level of a turbo jet is characterized by 1 ⎛ 1 ⎞ ⎛ γ ⎞ τ = ⋅ ⎜1+ ⎟τ ⎜ γ−1 ⎟ ( c )opt ⎜ ⎟ λ ⎜ ⎟ τ ⎝⎜ f ⎠⎟ (Πc ) =⎜τc ⎟ = r opt ⎜ ⎟ ⎝ ⎠opt • As supersonic flight Mach become larger, compression goes down until 1 ⎛ 1 ⎞ f 1= ⋅ ⎜1+ ⎟τ → τ = τ 2 ⎜ ⎟ λ λ r τr ⎝ f ⎠ f +1 …. optimal solution gets rid of compressor all together, and best engine becomes a ramjet! 8 MAE 6530 - Propulsion Systems II Jet Engine Performance Efficiency (4) • We are going to show that similar effect occurs as Mach drops significantly below Mach 1 • Trend emerges that replaces turbojet with Turbofan at lower Mach numbers Decreasing Mach Number 9 MAE 6530 - Propulsion Systems II Classification of Turbofan Engines MAE 6530 - Propulsion Systems II 10 Classification of Turbofan Engines (2) • Turbofan engines may be classified based on fan location as either forward or aft fan. • Based on a number of spools, engine may be classified as single, double, or triple spools. •Based on a bypass ratio, engine may be categorized as either low- or high- bypass ratio. • Fan may be geared or ungeared to its driving low-pressure turbine. • Mixed-flow types (where flow merges in nozzle) may be fitted with afterburner. MAE 6530 - Propulsion Systems II 11 Classification of Turbofan Engines (3) • High-bypass ratio turbofan (β > 5) achieves 75 % of thrust from bypass air - Ideal for subsonic transport aircraft. e.g. - Rolls-Royce Trent series (Airbus A330, A340, A350, A380), - Pratt & Whitney PW1000 G (geared) (Airbus A320neo, Bombardier CSeries, Embraer E2, Mitsubishi Regional Jet MC-21) - General Electric GE90 powering Boeing 777-300ER, 747. • Low-bypass ratio turbofan β ~ 1 achieves approximately equal thrust distribution between gas generator and bypass duct - Well suited to high-speed military applications. e.g. - Rolls-Royce RB199 in the Tornado - Pratt & Whitney F100-PW-200 in F-16A/B and F-15 - EuroJet Turbo GmbH EJ200 powering the Typhoon Fighter MAE 6530 - Propulsion Systems II 12 Classification of Turbofan Engines (4) • Unmixed Bypass Flow Turbofan 2-Spool High-bypass turbofan engine with a unmixed exhaust, showing the fan (pink) and core (red) exhaust streams • Mixed Bypass Flow Turbofan 2-spool, low-bypass turbofan engine with a mixed exhaust, showing the low-pressure (green) and high-pressure (purple) spools. MAE 6530 - Propulsion Systems II 13 Classification of Turbofan Engines (5) High Bypass Ratio • Modern high bypass ratio engine designed for long distance cruise at subsonic Mach numbers around 0.83. • Fan uses a single stage composed of a large diameter fan (rotor) with wide chord blades followed by a single nozzle stage (stator). • Bypass ratio is ~6 and the fan pressure ratio is ~2. MAE 6530 - Propulsion Systems II 14 Classification of Turbofan Engines (6) Low Bypass Ratio • Military turbofan designed for high performance at supersonic Mach numbers in the range of 1.1 to 1.5. • Fan has three stages with an overall pressure ratio of about 6 and a bypass ratio of only about 0.6. • Let’s investigate to understand why these engines look so different due to the the differences in the design flight condition. MAE 6530 - Propulsion Systems II 15 Classification of Turbofan Engines (7) MAE 6530 - Propulsion Systems II 16 Thrust of a TurboFan Engine m! a fan V m! a exit fan fan m! V m! a core exit core core m! a V m! fan exit a fan fan • 4-Primary Components of TurboFan Thrust o Bypass Momentum Thrust o Core Momentum Thrust o Fan Pressure Thrust Core Pressure Thrust o 17 MAE 6530 - Propulsion Systems II Thrust of a TurboFan Engine (2) m! a fan V m! a exit fan fan m! V m! a core exit core core m! a V m! fan exit a fan fan ⎛ ⎟⎞ ⎛ ⎟⎞ ⎛ ⎟⎞ ⎛ ⎟⎞ F = m! ⋅⎜V −V ⎟+ m! ⋅V + m! ⋅⎜V −V ⎟+⎜ p − p ⎟⋅ A +⎜ p − p ⎟⋅ A thrust acore exit ∞ ⎟ fuel exit a fan exit ∞ ⎟ exit ∞ ⎟ exit exit ∞ ⎟ exit ⎝⎜ core ⎠⎟ core ⎝⎜ fan ⎠⎟ ⎝⎜ core ⎠⎟ core ⎝⎜ fan ⎠⎟ fan Core Momentum Bypass Momentum Core Pressure Bypass Pressure Thrust Thrust Thrust Thrust 18 MAE 6530 - Propulsion Systems II Thrust of a TurboFan Engine (3) Air −to− fuel Ratio m! f = a m! fuel Bypass Ratio Total Air Massflow m! → a fan B m! a = m! a + m! a β = = core fan m! 1− B acore Bypass Fraction m! a β B = fan = m! a 1+ β ⎡ m! ⎤ m! a ⎛ ⎞ m! a ⎛ ⎞ F m! ⎢ core ⎜V V ⎟ fuel V fan ⎜V V ⎟⎥ p p A p p A thrust = a ⎢ ⋅⎜ exit − ∞ ⎟+ ⋅ exit + ⋅⎜ exit − ∞ ⎟⎥ +( exit − ∞ )⋅ exit +( 1exit − ∞ )⋅ exit m! ⎝⎜ core ⎠⎟ m! core m! ⎝⎜ fan ⎠⎟ fan ⎣⎢ a a a ⎦⎥ m! a m! a 1 1 core = core = = ! m! a m! a + m! a ma 1+ β ⎡ ⎤ core fan fan 1 ⎛ ⎞ 1 β ⎛ ⎞ 1+ F = m! ⎢ ⋅⎜V −V ⎟+ ⋅V + ⋅⎜V −V ⎟⎥ + m! thrust a ⎢ ⎜ exit ∞ ⎟ exit ⎜ exit ∞ ⎟⎥ a 1+ β ⎝⎜ core ⎠⎟ f core 1+ β ⎝⎜ fan ⎠⎟ core → ⎣ ⎦ m! m! m! a a − a ⎛ ⎞ ⎛ ⎞ core fan ⎜ p p ⎟ A ⎜ p p ⎟ A = =1− B ⎜ exit − ∞ ⎟⋅ exit +⎜ exit − ∞ ⎟⋅ exit ⎜ core ⎟ core ⎜ fan ⎟ fan m! a m! a ⎝ ⎠ ⎝ ⎠ m! a β m! 1 fan = B = , fuel = 19 ! ! MAEma 6530 -1Propulsion+ β ma Systemsf II Thrust of a TurboFan Engine (4) • Similar to the Previous Discussion for the TurboJet, Normalized Thrust is ⎡ V V ⎤ ⎛ p A p A A + A ⎞ F m! V ⎢1+ f + exit exit ⎥ ⎜ exit exit exit exit exit exit ⎟ thrust a ∞ β core β fan ⎜ core core fan fan core fan ⎟ (T) = = ⎢ ⋅ + ⋅ −1⎥ +⎜ ⋅ + − ⎟= turbofan p A p A ⎢ f 1+ β V 1+ β V ⎥ ⎜ p A p A A ⎟ ∞ 0 ∞ 0 ⎢ ( ) ∞ ∞ ⎥ ⎜ ∞ 0 ∞ 0 0 ⎟ ⎣ ⎦ ⎝⎜ ⎠⎟ m! V ρ ⋅ A ⋅V ⋅V γV 2 a ∞ = ∞ 0 ∞ ∞ = ∞ = γ ⋅ M 2 p A p A γ ⋅ R ⋅T ∞ ∞ 0 ∞ 0 g ∞ Isp ⋅g0 f (I) = =(T) ⋅ turbofan c turbofan γ ⋅ M Aexit + Aexit = Aexit → ∞ ∞ core fan ⎡ 1 ⎤ ⎢1 1 V V ⎥ ⎛ A p A ⎞ + ( + β) exit exit ⎛ ⎞⎜ exit exit exit ⎟ ⎢ f core β fan ⎥ A ⎜ p core fan fan ⎟ 2 ⎜ exit ⎟⎜ exit ⎟ (T) = γ ⋅ M∞ ⎢ ⋅ + ⋅ −1⎥ +⎜ ⎟⎜ ⋅ + −1⎟ turbofan ⎢ ⎥ ⎜ ⎟⎜ ⎟ (1+ β) V∞ 1+ β V∞ ⎝ A0 ⎠⎜ p∞ Aexit p∞ Aexit ⎟ 20 ⎢ ⎥ ⎝⎜ ⎠⎟ MAE 6530 - Propulsion⎣⎢ Systems II ⎦⎥ Thrust of a TurboFan Engine (5) • Fully expanded nozzle & f >> 1 • Inlet, fan, compressor, turbine, and fan /core nozzles are isentropic • Combustor heat addition is as constant pressure and Low Mach p = p = p → π = π = π = π =1 exit exit ∞ d b ncore n fan core fan γ γ ⎛ ⎞γ−1 ⎛ ⎞γ−1 γ ⎜ ⎟ , ⎜ ⎟ , γ−1 . πc =⎜τc ⎟ πc =⎜τc ⎟ πt =(τt ) core ⎝⎜ core ⎠⎟ fan ⎝⎜ fan ⎠⎟ ⎡ V V ⎤ ⎢⎛ 1 ⎞ exit ⎛ ⎞ exit ⎥ 2 ⎢⎜ ⎟ core ⎜ β ⎟ fan ⎥ (Toptimal ) = γ ⋅ M∞ ⎜ ⎟⋅ +⎜ ⎟⋅ −1 = turbofan ⎢⎝⎜1+ β ⎠⎟ V ⎝⎜1+ β ⎠⎟ V ⎥ ⎢ ∞ ∞ ⎥ ⎣ ⎦ ⎡ ⎛V ⎞ ⎛V ⎞⎤ ⎢⎛ ⎞ ⎜ exit ⎟ ⎛ ⎞ ⎜ exit ⎟⎥ 2 1 ⎜ core ⎟ β ⎜ fan ⎟ M ⎢⎜ ⎟ ⎜ 1⎟ ⎜ ⎟ ⎜ 1⎟⎥ = γ ⋅ ∞ ⎜ ⎟⋅⎜ − ⎟+⎜ ⎟⋅⎜ − ⎟ ⎢⎝⎜1+ β ⎠⎟ ⎜ V ⎟ ⎝⎜1+ β ⎠⎟ ⎜ V ⎟⎥ ⎢ ⎜ ∞ ⎟ ⎜ ∞ ⎟⎥ ⎣⎢ ⎝ ⎠ ⎝ ⎠⎦⎥ f = ⋅ (Ioptimal )turbofan (Toptimal )turbofan γ ⋅ M∞ 21 MAE 6530 - Propulsion Systems II The Ideal TurboFan Cycle • Too lengthy to analyze all types of turbofan engines. So, only a simple single spool fan, compressor, turbine cycle will be analyzed • Look at Fan Bypass Flow Stream V ∞ m! a fan Vexit fan V M T • Look at by pass velocity ratio exit exit exit fan = fan ⋅ fan V∞ M∞ T∞ • First calculate bypass exit stagnation pressure P0 P0 P0 P0 exit P0 P0 → P = ∞ ⋅ 1 ⋅ 2 ⋅ fan ⋅ p → ideal cycle → π = 1 ⋅ 2 =1 0exit ∞ d fan p P P P P P ∞ 0∞ 01 02 0∞ 01 γ γ−1 ⎛ γ +1 2 ⎞ ⎜ ⎟ 22 → P0 = πr ⋅πc ⋅ p∞ = pexit ⋅⎜1+ Mexit ⎟ exit ⎜ ⎟ MAE 6530 - Propulsionfan Systemsfan II fan ⎝⎜ 2 fan ⎠⎟ The Ideal TurboFan Cycle (2) • Look at Fan Bypass Flow Stream V ∞ m! Vexit a fan fan γ ⎧ ⎫ ⎛ ⎞γ−1 ⎪ ⎪ γ +1 2 ⎟ fully expanded nozzle → ⎨⎪p = p ⎬⎪→ π ⋅π =⎜1+ M ⎟ exit ∞ r c ⎜ exit ⎟ ⎩⎪ fan ⎭⎪ fan ⎝ 2 fan ⎠ γ ⎛ ⎞γ−1 ⎛ γ +1 ⎞ Isentropic fan ⎜ ⎟ ⎜1 M 2 ⎟ → πc =⎜τc ⎟ → τr ⋅τc =⎜ + exit ⎟ fan ⎝⎜ fan ⎠⎟ fan ⎝⎜ 2 fan ⎠⎟ T0 ⎛ γ +1 ⎞ γ +1 τ = ∞ ⎜1+ M 2 ⎟→ M 2 = τ −1 r ⎜ ∞ ⎟ ∞ r T∞ ⎝ 2 ⎠ 2 γ +1 2 2 Mexit τr ⋅τc −1 Mexit τr ⋅τc −1 γ +1 2 2 fan fan fan fan → Mexit = τr ⋅τc −1→ = → 2 = 2 fan fan γ +1 2 τ −1 M τ −1 M r ∞ r 2 ∞ 23 MAE 6530 - Propulsion Systems II The Ideal TurboFan Cycle (3) • Look at Fan Bypass Flow
Details
-
File Typepdf
-
Upload Time-
-
Content LanguagesEnglish
-
Upload UserAnonymous/Not logged-in
-
File Pages38 Page
-
File Size-