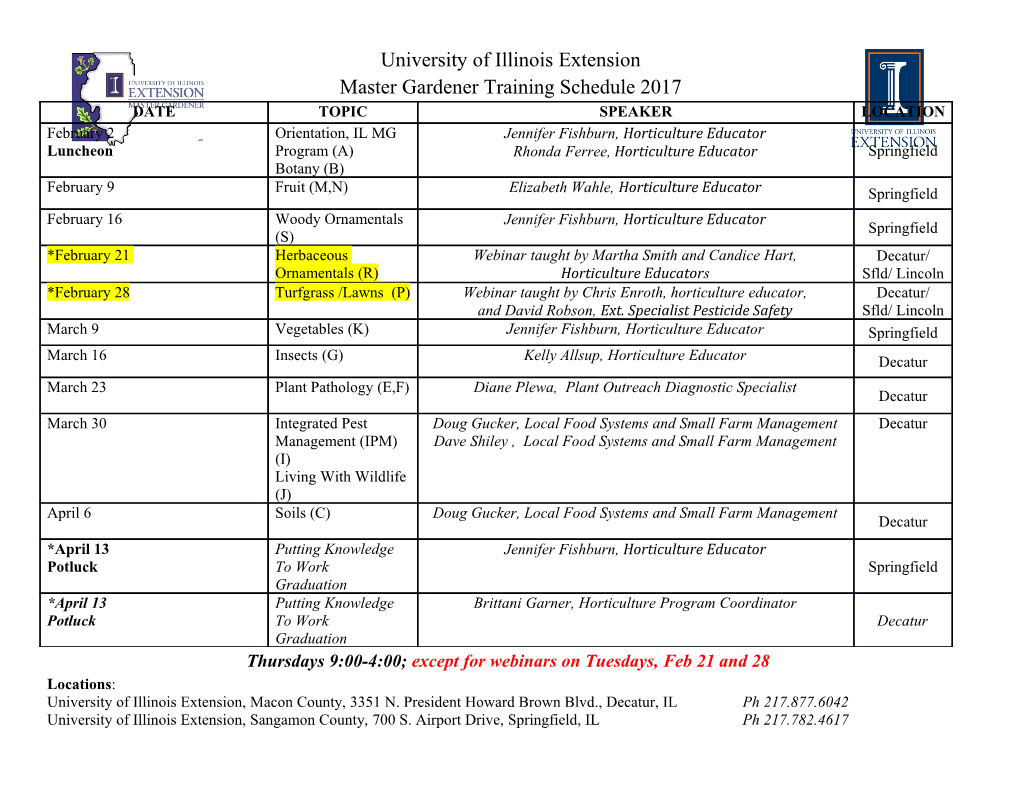
DESIGN AND DEVELOPMENT SOURCEBOOK PRODUCT DESIGN FOR DIE CASTING in Recyclable Aluminum, Magnesium, Zinc and ZA Alloys Although great care has been taken to provide accurate and current information, neither the author(s) nor the publisher, nor anyone else associated with this publication, shall be liable for any loss, damage or liability directly or indirectly caused or alleged to be caused by this book. The material contained herein is not intended to provide specifi c advice or recommendations for any specific situation. Any opinions expressed by the author(s) are not necessarily those of NADCA. Trademark notice: Product or corporate names may be trademarks or registered trademarks and are used only for identifi cation and explanation without intent to infringe nor endorse the product or corporation. © 2015 by North American Die Casting Association, Arlington Heights, Illinois. All Rights Reserved. Neither this book nor any part may be reproduced or transmitted in any form or by any means, electronic or mechanical, including photocopying,microfilming, and recording, or by any information storage and retrieval system, without permission in writing form the publisher. DESIGN AND DEVELOPMENT SOURCEBOOK PRODUCT DESIGN FOR DIE CASTING in Recyclable Aluminum, Magnesium, Zinc and ZA Alloys 2015 Seventh Edition Published by the North American Die Casting Association NORTH AMERICAN DIE CASTING ASSOCIATION Product Design for Die Casting i PREFACE Product Design for Die Casting was originally prepared and published for designers, engineers and specifiers through a cooperative effort of the die casting industry and the United States Department of Commerce. It was initially financed by contributing members of a marketing affiliate of the North American Die Casting Association (NADCA), and the U.S. Department of Commerce through a grant/cooperative agreement. Acknowledgement is made to the selfless individuals, representing die casters, industry suppliers and engineers and managers, who spent many hours contributing, reviewing and verifying data. All known sources of published information on the die casting process as it applies to product design were researched. Portions of the text and some of the illustrations in this manual were adapted from Product Design and Development for Magnesium Die Castings with the permission of the Dow Chemical Company. Several illustrations are reproduced with the permission of the International Lead Zinc Research Organization. In addition to this book the North American Die Casting Association also provides die casting product design assistance through its NADCA Design program which consists of the following resources: NADCA Design web site: www.diecastingdesign.org NADCA Design seminars: www.diecastingdesign.org/seminars Phone support: 847.279.0001 E-mail support: [email protected] Designers, engineers and specifiers are also urged to consult NADCA Product Specification Standards for Die Castings, published by the North American Die Casting Association; these standards include standard and precision tolerances (including geometric dimensioning) for current production practices under varying manufacturing conditions. The standards also include Tooling, Alloy, Engineering & Design, Quality Assurance and Commercial guidelines. For die casting produced with the semi-solid and squeeze casting processes the publication NADCA Product Specification Standards for Die Castings Produced by the Semi-solid and Squeeze Casting Processes is available. Additional copies of this publication and other publications are available from the North American Die Casting Association: North American Die Casting Association www.diecasting.org 3250 N. Arlington Heights Rd., Ste. 101 Arlington Heights, IL 60090 Phone: 847.279.0001 Fax: 847.279.0002 ii Product Design for Die Casting PRODUCT DESIGN FOR DIE CASTING CONTENTS 1 The Die Casting Option 1 1.1 Die Casting Advantages: Summary 1 1.2 Advances in Die Casting Process Technology 1 1.3 Developments in Die Casting Alloys 2 1.4 Die Casting’s Range of Product Capabilities 2 1.5 The Economic Equation 6 1.6 The Benefits of Designing for Manufacturing 6 1.7 Miniature, Heat Treated, High Vacuum, Squeeze & Semi-Solid Metal Casting 6 1.8 Serviceability & Recycling 8 2 Product Development 9 2.1 Working Environment 12 2.2 Structural Criteria 16 2.3 Manufacturing Economics 26 2.4 Die Casting Versus Other Processes 32 3 Product Design 37 3.1 Geometry Optimization 38 3.2 Assemblies 47 3.3 Machining 64 3.4 Surface Finishing 67 3.5 Prototyping 79 4 The Conventional Die Casting Process 87 4.1 Understanding the Die Casting Cycle 88 4.2 Characteristics of Die Casting 93 4.3 Preventing Casting Defects 94 4.4 Alloys and Properties 97 4.5 Aluminum Die Castings 98 4.6 Magnesium Alloys 106 4.7 Zinc 111 4.8 ZA Alloys 115 4.9 Early Designer-Die Caster Interaction 116 4.10 Alloy Selection 116 5 High Integrity Die Castings 125 5.1 High Vacuum Die Casting 125 5.2 Squeeze Casting 129 5.3 Semi-solid 130 Product Design for Die Casting iii iv Product Design for Die Casting 1 THE DIE CASTING OPTION When functional products are designed for volume production, the high-pressure die casting process is one of the prime production options considered by product engineers. Components can be cast at high speed from a range of durable metal alloys while faithfully capturing the most intricate design details. This ability to maintain close tolerances, often eliminating all machining, can make the process the optimum choice for lower volume production as well. The introduction of new, higher-performing die casting alloys and process technology makes old design assumptions about the limitations of the process obsolete; dimensional specifications, draft angles, as-cast flatness, porosity reduction can be achieved to levels unheard of just a few years ago. 1.1 Die Casting’s Advantages: Summary This checklist summarizes the advantages of today’s die casting process from the perspective of the product designer seeking to maximize product performance and minimize product cost. • Modern process technology that insures consistent quality • Freedom to design intricate configurations • Net-shape casting economies, even at lower volumes • Wide variety of available alloys and alloy properties • The rigidity, look and feel of metal • Meets moderate to high-strength performance needs • Moderate to high impact and dent resistance • Documented fatigue strength characteristics • Pressure tightness for hydraulic and pneumatic components • Bearing properties that often eliminate separate bearings • Excellent sound damping properties • Inherent EMI shielding for electronic applications • High-quality surface finish for decorative applications • Meets criteria for serviceability and recyclability 1.2 Advances in Die Casting Process Technology The die casting process today has been well researched and systematically quantified in terms of thermodynamics, heat transfer and fluid flow parameters. This technology has been transferred to the die casting industry, where its use has made a significant improvement in the design of die casting dies, the die steel used in die construction, and in virtually all die casting production options. Product Design for Die Casting 1 Chapter 1: The Die Casting Option Die casting machines today are being fitted with new, high-technology electronic systems that control production processes according to exact parameters and continuously monitor production output. Casting accuracy is greatly improved, variations from casting-to-casting are sharply reduced, and production costs are more closely controlled. Today advanced die casting systems are producing castings with extremely close tolerances and reduced draft angles (in some cases zero draft) on selected features, eliminating finish machining operations. This casting precision has lowered the break- even point for die casting versus low-volume production processes and increased its economic advantages over high volume alternatives. The specific implications of these changes for the product designer are presented in this manual. 1.3 Developments in Die Casting Alloys A wide range of alloys are used for die casting today. A separate section will deal in detail with the four families that currently account for most of the functional and decorative die castings produced in the United States: aluminum, magnesium, zinc, and ZA (zinc-aluminum). Copper, tin and lead are being die cast for certain specialized applications. Ferrous die castings are also being produced on a very limited basis. Die casting alloys are precisely formulated to offer mechanical properties equivalent to medium-strength metals. They are generally several times as strong and many times more rigid than plastics, and the mechanical properties of the higher-strength die casting alloys compare favorably with powder iron, brass and low carbon steel. When compared with high-performance plastics or advanced composites, die casting alloys can often deliver the required product strength at a cost advantage. New die casting alloys have been introduced and have proven their capabilities in full-scale production and field use. The methods now being used to produce them have been modified to reduce impurities, improve overall metal quality, improve product reliability, and reduce energy consumption. Figure 1.1 Fog Light Housing This die cast aluminum 383 fog light housing eliminated a two piece plastic and aluminum casting assembly. The reflective optics, pivot bosses and height adjustment features are
Details
-
File Typepdf
-
Upload Time-
-
Content LanguagesEnglish
-
Upload UserAnonymous/Not logged-in
-
File Pages163 Page
-
File Size-