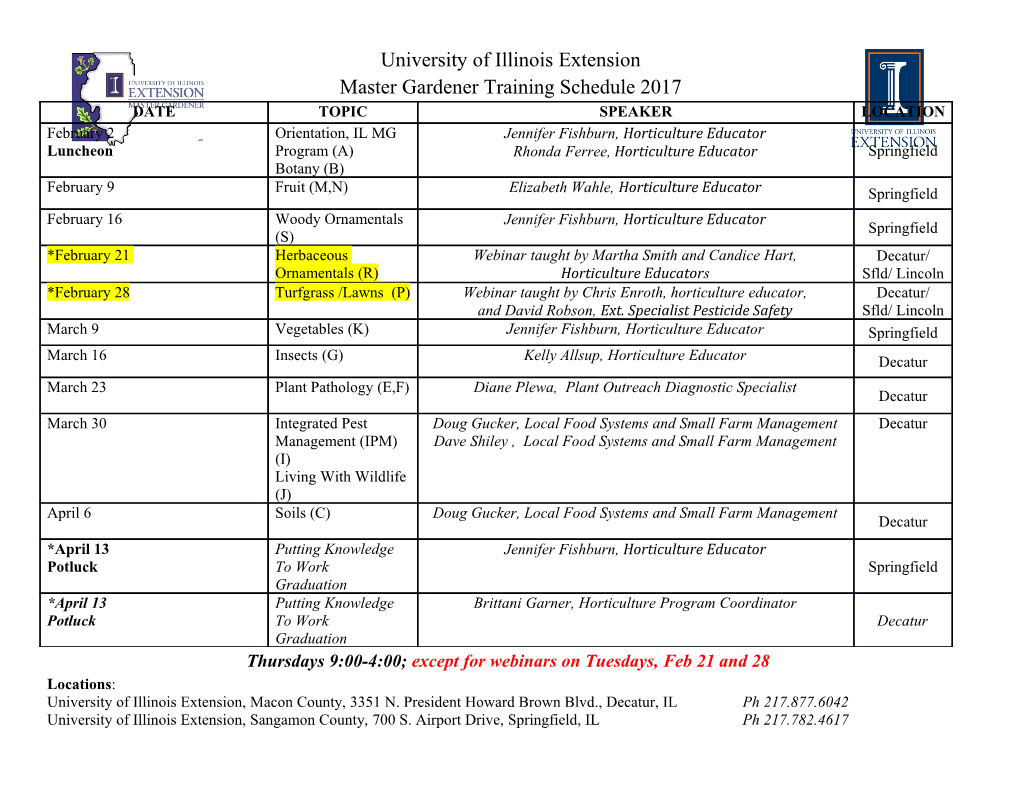
1(14) 29 November 2012 Background document for N,N-Dimethylacetamide (DMAC) Document developed in the context of ECHA’s fourth Recommendation for the inclusion of substances in Annex XIV Information comprising confidential comments submitted during public consultation, or relating to content of Registration dossiers which is of such nature that it may potentially harm the commercial interest of companies if it was disclosed, is provided in a confidential annex to this document. 1. Identity of the substance Chemical name: N,N-Dimethylacetamide (DMAC) EC Number: 204-826-4 CAS Number: 127-19-5 IUPAC Name: N,N-Dimethylacetamide 2. Background information 2.1. Intrinsic properties N,N-Dimethylacetamide (DMAC) was identified as a Substance of Very High Concern (SVHC) according to Article 57 (c) as it is classified in Annex VI, part 3, Table 3.1 (the list of harmonised classification and labelling of hazardous substances) of Regulation (EC) No 1272/2008 as toxic for reproduction 1B, H360D (“May damage the unborn child”)1, and was therefore included in the Candidate List for authorisation on 19 December 2011 following ECHA’s decision ED/77/2011. 1 This corresponds to a classification as toxic for reproduction category 2 (R61: May cause harm to the unborn child) in Annex VI, part 3, Table 3.2 (the list of harmonised classification and labelling of hazardous substances from Annex I to Directive 67/548/EEC) of Regulation (EC) N° 1272/2008 2(14) 2.2. Imports, exports, manufacture and uses 2.2.1. Volume(s), imports/exports In 2010 the total manufactured volume was in the range of 15,000-20,000 tonnes. The total import of DMAC into the EU as a substance on its own was in the range of 1,000-2,000 tonnes and the total export was 3,000 – 4,000 tonnes. DMAC was to some extent imported in mixtures, mainly for the production of fibres, and in articles as residual content (<3%) of fibres and films. Based on the data obtained, the total annual consumption of DMAC in the EU as process chemical and for formulation of mixtures is estimated at 11,000-19,000 tonnes per year (ECHA, 2011). 2.2.2. Manufacture and uses 2.2.2.1. Manufacture and releases from manufacture DMAC is manufactured by the reaction of dimethylamine (DMA) and acetic acid in closed systems (OECD, 2001 in ECHA, 2011). The reaction takes place at elevated temperature and pressure and the substance is purified by distillation. According to information provided by registrants during the consultation in the context of the preparation of the A.XV Dossier, DMAC is manufactured within a high integrity contained system where little potential for exposure exists. The end product is transferred into vessels/large containers at dedicated automated facilities. Sampling is undertaken using closed loop systems. The likelihood for worker exposure is higher during maintenance and lab analysis (ECHA, 2011). Automated filling of the product minimises worker exposure during filling. In addition, the use of gloves greatly reduces the potential for incidental dermal contact. Exposures to DMAC are likely to be highest during maintenance operations, in particular in the absence of adequate PPE (ECHA, 2011). Based on emission factors provided by some of the registrants, it is estimated that approximate 3.5 tonnes of DMAC per year is released in the EU from the manufacturing process to waste water directed to sewage treatment plants. Air emissions from the manufacturing process are roughly estimated at approximately 0.5 tonnes per year (ECHA, 2011). 2.2.2.2. Uses and releases from uses Uses According to information provided by the registrants (ECHA, 2011) and further data received during the public consultations (RCOM, 2011; RCOM, 2012), the use in the EU is allocated as follows: 3(14) • Agrochemicals, pharmaceuticals and fine chemicals (65-70% of tonnage) DMAC is a dipolar, aprotic solvent with high solving power for high molecular- weight polymers. The solvent is miscible with - and can be used for - a wide range of organic and inorganic compounds. The polar nature of DMAC enables it to act as a combined solvent and reaction catalyst in many reactions. Furthermore, its boiling point (166ºC) allows reactions to be carried out at much higher temperatures than would be achievable in many organic solvents, without the need to operate under pressure. DMAC is furthermore reported to be used to some extent as intermediate for synthesis of some substances. DMAC is also used as excipient (carrier ingredient) in human and veterinary pharmaceuticals due to its polar, aprotic characteristics. Applications relate to pharmaceuticals (e.g. antibiotics and novel contrast media), agrochemicals (fertilisers, pesticides etc.), and fine chemicals. Among the processes reported by industry to be carried out during those uses are: mixing with reactants, (trans)-pouring from containers, separation from products (by filtration or distillation), re-use (after purification by distillation), and equipment cleaning and disposal (ECHA, 2011). • Man-made fibres (20-25% of tonnage) DMAC is used in the production of man-made fibres made of polymers such as: acrylic (180kton of fibres produced / 70kton used in the EU; CIRFS – the European Man-made Fibres Association - in RCOM, 2011) polyurethane-polyurea copolymer (elastane; 30kton produced / used) and meta-aramid (6kton produced, <6kton used). It acts as the solvent in the polymerization reaction and helps transfer the polymer through the spinning process (see description below) to produce very fine fibres. To some extent, DMAC is also used in mixtures applied to add specific additives or other polymers into the fibre spinning process (RCOM, 2011). The main part of the fibres is used for production of clothing. For instance, elastane fibres are used in swimsuits, underwear, socks, absorbent hygiene products such as baby diapers and incontinence products, etc. DMAC is mainly used for the manufacturing of continuous filament fibres 2 and to a less extent for staple, discontinuous lengths of fibre 3. The fibres are to some extent used in combination with other fibres (e.g. elastane mixed with cotton or polyester fibres; meta-aramid fibres in combination with fibre glass, for instance for protective clothing and gloves). 2 Continuous filament fibres are used for weaving, knitting or carpet production 3 Non-continuous fibres can be spun into yarn or incorporated in unspun uses such as fillings or nonwovens 4(14) A part of fibres are used as technical textiles for other applications, for example: Fibreglass/meta-aramid nonwoven (felt) fabrics used for aerospace composites Surface tissue made of polyacrylonitril used in fibre reinforced plastics (FRP-applications, e.g. for truck cabins). Meta-aramid fibres are used in different systems where properties typical of textiles should be adapted to high ambient temperatures. An example is filters for hot gas filtration. Paper made from synthetic meta-aramid polymer in two physical forms: short fibres (floc) and microscopic fibrous binder particles (fibrids). The paper is widely used in two major end uses including (i) insulation for electrical equipment applications in liquid and dry transformers, motors, and generators and (ii) structural composites. Spinning refers to the process where fluid polymer filaments emerge from the holes in a spinneret, and gradually solidify; when DMAC is used, solidification is achieved either by precipitation in a chemical bath where the spinneret is submerged – so called wet spinning - or by evaporating the solvent in a stream of air or inert gas, named dry spinning. The solvent is recovered and recycled several times in the process. The consumption of DMAC (0.5-1% per cycle) is due to: the solvent losses caused by the acid hydrolysis during recovery, environmental releases, residuals of solvent remaining in the fibres and DMAC disposed of as waste from the process. Recovery is reported to be achieved by installations comprising a distillation unit, a squeezing column unit and a DMAC stripping unit. The fibres are further processed (transfer and filling operations, rewinding and beaming, spinning of yearn, and knitting/weaving in order to produce the fabric, which will consequently be dyed and/or washed), with DMAC typically being present as a residue at significant concentration only in the first steps of the fibre processing (raw fibres may contain up to 3% of residual DMAC, but typical DMAC 4 content is between 0.1and 0.5%; the greige fabric,- i.e. the fabric before it’s bleached / dyed- normally contains DMAC levels below 0.1%5, which will further be reduced during dying/washing.; No detectable or very low level of residual DMAC are reported to be present in final textiles (e.g. in baby diapers, residues are reportedly at ppb levels). • Industrial coatings (3-5% of tonnage) Approximately 3-5% of the DMAC in the EU is used as solvent in coatings for industrial use. The only use which has been described in detail (during consultations with industry) is the use of the substance in the production of 4 For acrylic fibres residues are reported by CIRFS European Man-made Fibres Association to be lower than 0.3%, for elastane around 0.3% and for m-aramid residues are reported to be higher with an average of 0.6% (RCOM, 2011). In the most recent public consultation (RCOM, 2012), the average DMAC residues reported herein for raw fibres (0.1 – 0.5%) were basically confirmed. It was also confirmed that higher residue values (up to 1 - 1.2%) may occur in some cases, but it was also stated that upper reported levels of 3% are historical. 5 So-called spun dyed fibres, where the fibre is dyed during the fibre production, thereby avoiding consumption of substantial volumes of water and chemicals in comparison with the conventional dying process, may contain somewhat higher DMAC residues.
Details
-
File Typepdf
-
Upload Time-
-
Content LanguagesEnglish
-
Upload UserAnonymous/Not logged-in
-
File Pages14 Page
-
File Size-