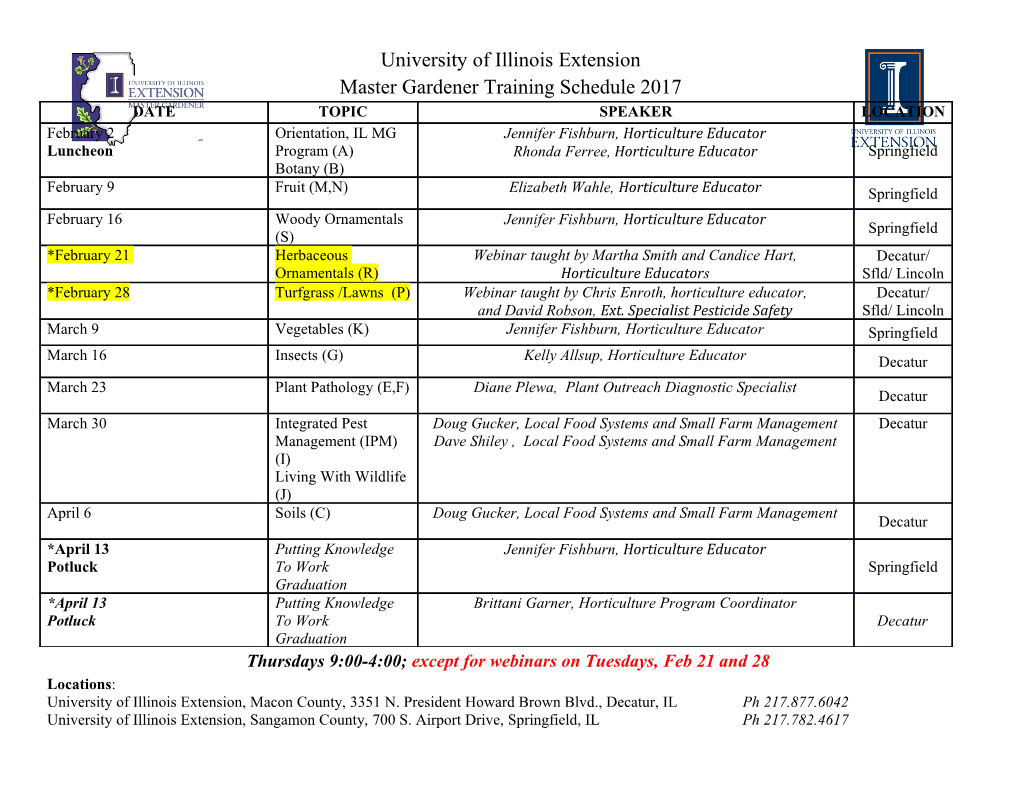
DOT/FAA/TC-15/47 Teardown Evaluation of a Federal Aviation Administration William J. Hughes Technical Center Composite Carbon/Epoxy Aviation Research Division Atlantic City International Airport Beechcraft Starship Aft Wing New Jersey 08405 September 2017 Final Report This document is available to the U.S. public through the National Technical Information Services (NTIS), Springfield, Virginia 22161. This document is also available from the Federal Aviation Administration William J. Hughes Technical Center at actlibrary.tc.faa.gov. U.S. Department of Transportation Federal Aviation Administration NOTICE This document is disseminated under the sponsorship of the U.S. Department of Transportation in the interest of information exchange. The U.S. Government assumes no liability for the contents or use thereof. The U.S. Government does not endorse products or manufacturers. Trade or manufacturers’ names appear herein solely because they are considered essential to the objective of this report. The findings and conclusions in this report are those of the author(s) and do not necessarily represent the views of the funding agency. This document does not constitute FAA policy. Consult the FAA sponsoring organization listed on the Technical Documentation page as to its use. This report is available at the Federal Aviation Administration William J. Hughes Technical Center’s Full-Text Technical Reports page: actlibrary.tc.faa.gov in Adobe Acrobat portable document format (PDF). Technical Report Documentation Page 1. Report No. 2. Government Accession No. 3. Recipient's Catalog No. DOT/FAA/TC-15/47 4. Title and Subtitle 5. Report Date TEARDOWN EVALUATION OF A COMPOSITE CARBON/EPOXY September 2017 BEECHCRAFT STARSHIP AFT WING 6. Performing Organization Code 7. Author(s) 8. Performing Organization Report No. John S. Tomblin and Lamia Salah 9. Performing Organization Name and Address 10. Work Unit No. (TRAIS) National Institute for Aviation Research Wichita State University Wichita, KS 67260 11. Contract or Grant No. 12. Sponsoring Agency Name and Address 13. Type of Report and Period Covered FAA Northwest Mountain Regional Office Final Report 1601 Lind Avenue SW Renton, WA 98057 14. Sponsoring Agency Code AIR-100 15. Supplementary Notes The FAA William J. Hughes Technical Center Aviation Research Division COR was Curtis Davies. 16. Abstract This report summarizes the findings of a study conducted on a composite carbon/epoxy Beechcraft Starship aft wing to determine the effects of aging after 12 years of service and 1800 flight hours. The Beechcraft Starship was the world’s first pressurized all-composite business turboprop and received Federal Aviation Administration certification in 1987. Only 53 Starships were manufactured; production was discontinued because of poor demand. Because of economic reasons and prohibitive fleet support costs, the original equipment manufacturer gathered and destroyed most of its Starship fleet. This report provides highlights of the results of the teardown study conducted on a Starship NC-8 aft wing. Results indicated that the composite structure maintained its structural integrity over 1800 flight hours with no significant degradation or detrimental signs of aging observed. It should be noted that the number of flight hours was too small to integrate the effects of mechanical fatigue. 17. Key Words 18. Distribution Statement Beechcraft Starship; Carbon/epoxy; Aging composites This document is available to the U.S. public through the National Technical Information Service (NTIS), Springfield, Virginia 22161. This document is also available from the Federal Aviation Administration William J. Hughes Technical Center at actlibrary.tc.faa.gov. 19. Security Classif. (of this report) 20. Security Classif. (of this page) 21. No. of Pages 22. Price 47 Unclassified Unclassified Form DOT F1700.7 (8-72) Reproduction of completed page authorized ACKNOWLEDGMENTS The authors would like to thank Ric Abbott for his invaluable input to the program. The authors also thank Tim Hickey, Abhijit Sonambekar, John Fitzpatrick, Antony Alford, Ping Taoh, and Chathuranga Kuruppuarachchige from the National Institute for Aviation Research. iii TABLE OF CONTENTS Page EXECUTIVE SUMMARY ix 1. INTRODUCTION 1 2. BEECHCRAFT STARSHIP AFT WING TEARDOWN STUDY 1 2.1 Test Article Description 1 2.2 Material Selection 5 2.3 Lightning Protection Scheme 5 2.4 Supporting Data for Certification 6 2.5 Left Wing-section NDi 6 2.6 Thermal Analysis 7 2.7 Moisture Content Evaluation 21 2.8 Microscopy 22 2.9 Starship Aft Wing Full-Scale Test 26 2.9.1 Full-Scale Article—NDI 26 2.9.2 Starship Aft Wing Full-Scale Test 29 3. CONCLUSIONS 36 4. REFERENCES 37 iv LIST OF FIGURES Figure Page 1 Beechcraft Starship under investigation (NC-8) 2 2 Beechcraft Starship airplane 3-view drawing with dimensions 3 3 Beechcraft Starship aft wing structural details 4 4 The (a) Starship aft wing structural H-joint details and (b) H-joint extracted from BL78 upper skin center spar 5 5 The (a) Starship aft wing structural V-joint details and (b) V-joint extracted from BL78 lower skin front spar 5 6 Beechcraft Starship aft wing TTU scans of the left upper- and lower-wing skins 7 7 Aft wing coupon nomenclature 8 8 DMA results for sample extracted from LS BL208 UF16 FS450 9 9 DMA results for sample extracted from LS BL48 UF35 FS402 9 10 DMA results for coupons extracted from NC-8 aft wing LS 11 11 DMA results for a sample extracted from US BL50 LF25 FS369 12 12 DMA results for a sample extracted from US BL74 LF25 FS369 12 13 DMA results for a sample extracted from US BL259 UF5 FS459 13 14 DMA results for coupons extracted from NC-8 aft wing US 15 15 DSC data for a sample extracted from LS BL50 LF28 FS 394 16 16 DSC data for a sample extracted from LS BL48 UF38 FS405 16 17 DSC data for a sample extracted from LS BL260 UF7 FS461 17 18 DSC data for a sample extracted from US BL50 LF27 FS 371 19 19 DSC data for a sample extracted from US BL74 LF17 FS 371 19 20 Moisture loss as function of time for coupons extracted from LS 21 21 Moisture loss as a function of time for coupons extracted from the US 22 22 US BL48 UF 39 23 23 US BL48 UF 40 23 24 US BL140 UF 20 24 25 US BL140 UF 19 24 26 US BL140 LF 19 25 27 US BL140 LF 20 25 28 LS BL74 LF 29 25 v 29 LS BL208 UF 20 26 30 Overview of the right upper aft wing of the Starship 27 31 Overview of the right lower aft wing of the Starship 28 32 Aft wing repair of US area 7 damage 29 33 Full-scale test setup 30 34 Bending moment vs. LSTA 31 35 Starship right main wing strain gage identification and NDI inspection grid (12″ spacing between gridlines) 32 36 Deformed wing at 40% limit load 33 37 Deformed wing at 70% limit load 33 38 Deformed wing at 100% limit load 34 39 Limit load percent vs. upper wing skin strain comparison (certification vs. post-teardown full-scale tests) 35 40 Limit load percent vs. lower wing skin strain comparison (certification vs. post-teardown full-scale tests) 35 41 Spectrum loading sequence 36 vi LIST OF TABLES Table Page 1 DMA data summary for NC-8 aft wing LS samples 10 2 DMA data summary for NC-8 aft wing US samples 14 3 DSC data summary for NC-8 aft wing LS samples 18 4 DSC data summary for NC-8 aft wing US samples 20 vii LIST OF ABBREVIATIONS AND ACRONYMS ASTEC Aircraft Structural Testing and Evaluation Center BL Buttock line DMA Dynamic mechanical analysis DSC Differential scanning calorimetry FS Fuselage station LASP Laminate Analysis Software Package LBL Left buttline LF Lower facesheet LS Lower skin LSTA Load station location MLG Main landing gear NDI Nondestructive inspection NIAR National Institute for Aviation Research OEM Original equipment manufacturer RBL Right buttline SPAID Sandwich Panel Analysis Impact/Delamination Tg Glass transition temperature TT Tap testing TTU Through-transmission ultrasonic UF Upper facesheet US Upper skin UT Ultrasonic testing viii EXECUTIVE SUMMARY Current economic conditions require the use of military and commercial aircraft beyond their original design service objectives. Therefore, it is necessary to understand aging aircraft in-service-induced deterioration to ensure the airworthiness and structural integrity of these airframes. Most previous aging aircraft studies have focused on metallic structures. However, as more composite components are being certified and used on aircraft structural components, it is crucial to address this aging concern for composite components. This report summarizes the findings of a study conducted on a composite carbon/epoxy Beechcraft Starship aft wing to determine the effects of aging after 12 years of service and 1800 flight hours. The Beechcraft Starship was the world’s first pressurized all-composite business turboprop and received Federal Aviation Administration certification in 1987. Only 53 Starships were manufactured; production was discontinued because of low demand. Because of economic reasons and prohibitive fleet support costs, the original equipment manufacturer gathered and destroyed most of its Starship fleet. This report provides highlights of the results of the teardown study conducted on a Starship NC-8 aft wing. Results indicated that the composite structure maintained its structural integrity over its service life and did not show significant degradation or detrimental signs of aging. However, the number of flight hours was too small to interrogate the effects of mechanical fatigue. ix 1. INTRODUCTION The Beechcraft Starship aft wing is the oldest primary structure in a small business aircraft built using composite materials. In the late 1970s, Beechcraft was leading the small business aircraft market following the success of its King Air twin aircraft.
Details
-
File Typepdf
-
Upload Time-
-
Content LanguagesEnglish
-
Upload UserAnonymous/Not logged-in
-
File Pages47 Page
-
File Size-