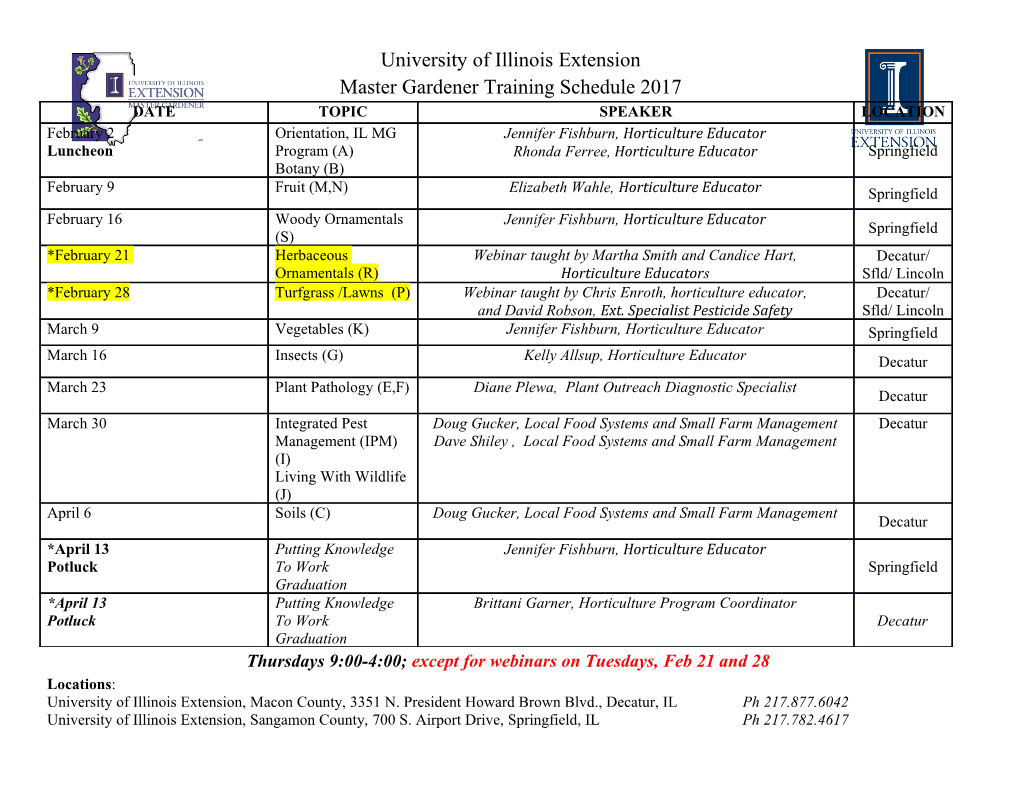
Materials Science and Engineering B 114–115 (2004) 251–254 Implant damage and redistribution of indium in indium-implanted thin silicon-on-insulator Peng Chena, Zhenghua Anb, Ming Zhua,b, Ricky K.Y. Fua, Paul K. Chua,∗, Neil Montgomeryc, Sukanta Biswasc a Department of Physics and Materials Science, City University of Hong Kong, Tat Chee Avenue, Kowloon, Hong Kong b State Key Laboratory of Functional Materials for Informatics, Shanghai Institute of Microsystem and Information Technology, Chinese Academy of Sciences, 865 Changning Road, 200050 Shanghai, China c Cascade Scientific, Brunel Science Park, Uxbridge, Middlesex UB83PH, UK Abstract The indium implant damage and diffusion behavior in thin silicon-on-insulator (SOI) with a 200 nm top silicon layer were studied for different implantation energies and doses. Rutherford backscattering spectrometry in the channeling mode (RBS/C) was used to characterize the implant damage before and after annealing. Secondary ion mass spectrometry (SIMS) was used to study the indium transient enhanced diffusion (TED) behavior in the top Si layer of the SOI structure. An anomalous redistribution of indium after relatively high energy (200 keV) and dose (1 × 1014 cm−2) implantation was observed in both bulk Si and SOI substrates. However, there exist differences in these two substrates that are attributable to the more predominant out-diffusion of indium as well as the influence of the buried oxide layer in the SOI structure. © 2004 Elsevier B.V. All rights reserved. Keywords: Indium; Implant damage; Diffusion; SOI; SIMOX 1. Introduction Silicon-on-insulator (SOI) substrates have many advan- tages over bulk silicon in high-speed, low-power devices As a heavy ion, indium has become a promising dopant [10–11] and indium implantation into SOI can further im- to achieve ultra-shallow or steep retrograde channel profiles prove the device performance. Although much research has (SRCP) in advanced metal-oxide-semiconductor field-effect- been devoted to indium implantation and diffusion in bulk transistors (MOSFETs) [1–4]. However, due to its heavy Si, that on indium implantation into SOI is relatively scarce. mass, implantation-induced damage is quite considerable In addition, although some dopants, such as boron and even at relatively low doses typically used in channel dop- phosphorus have been shown to exhibit different diffusion ing. Moreover, the poor electrical activation of indium in Si behavior in SOI compared to bulk Si [12–14], detailed com- due to the high ionization energy [5] and low solid solubility parison between the diffusion of indium in SOI and bulk sil- [6] necessitate the implantation of a higher dose. The large icon has not been carried out. In this work, the implantation amount of ion implantation induced damage will affect both induced damage and indium diffusion characteristics were indium diffusion during subsequent thermal processes and studied. The SOI wafers used were separation by implanta- the electrical characteristics of the final devices. Transient tion of oxygen (SIMOX) wafers that are commonly used for enhanced diffusion (TED) of indium in Si has been observed fully depleted metal-oxide-semiconductor field-effect tran- and the magnitude is comparable to that of boron [6–9], and sistors (MOSFETs) [15]. We investigated systematically the it poses one of the main challenges to form steep and shallow indium ion implantation induced damage under different im- profiles. plant energies and doses. The indium diffusion behavior in the SOI structure, especially in the top Si layer, was also ∗ Corresponding author. Tel.: +852 2788 7724; studied, and the results were compared to those obtained in fax: +852 2788 9549/7830. bulk Si. The difference between the indium diffusion pro- E-mail address: [email protected] (P.K. Chu). files in SIMOX and bulk Si implanted at a relatively high 0921-5107/$ – see front matter © 2004 Elsevier B.V. All rights reserved. doi:10.1016/j.mseb.2004.07.031 252 P. Chen et al. / Materials Science and Engineering B 114–115 (2004) 251–254 energy (200 keV) and high dose (1 × 1014 cm−2) was evalu- while the broad peak from channel number 200–300 origi- ated. nates from oxygen in the buried SiO2 layer. At around channel number 530 that corresponds to the silicon surface, the sam- ple implanted with 1 × 1014 cm−2 at 200 keV exhibits a sharp 2. Experimental peak in the surface region, clearly indicating that an amor- phous surface layer has been produced during the high dose SIMOX SOI wafers were used in our experiments. The and high energy implantation. However, the other three, in- cluding the sample implanted at the same energy of 200 keV top silicon layer was 200 nm thick and the buried SiO2 layer × 13 −2 (BOX) was 370 nm thick. <1 0 0> p-type silicon wafers were but at a lower dose of 1 10 cm , do not exhibit this also implanted for comparison. Before implantation, a 10 nm surface peak. It implies that the surface of these three sam- screen oxide was grown using dry oxidation at 950 ◦C. The ples have not been amorphized. This is in agreement with wafers were then implanted at room temperature with two the amorphization threshold dose reported before, which is − × 13 −2 different doses at 150 keV: (1) 5 × 1012 cm 2 and (2) 1 × around 5 10 cm at 200 keV [8]. For a dose less than − × 13 −2 1013 cm 2. Another set of samples was implanted at 200 keV 1 10 cm , the as-implanted samples retain most of the with: (3) 1 × 1013 cm−2 and (4) 1 × 1014 cm−2.A7◦C tilt crystal integrity. angle was employed for all implants to minimize channel- The RBS spectra indicating recrystallization of the amor- × 14 −2 + ing. After implantation, the wafers were annealed either us- phous layer in the SOI implanted with 1 10 cm In at ing rapid thermal annealing (RTA) at 1050 ◦C for 15 s or in 200 keV are shown in Fig. 2. In both spectra acquired after a furnace under nitrogen at 800 ◦C for 2 h. These annealing RTA or furnace annealing, the disappearance of the surface conditoins were chosen to minimize and maximize the ex- peak indicates that during each annealing process, the implant tent of transient enhanced diffusion, respectively [7]. The im- damage has been almost completely repaired and sufficient plantation damage was studied by Rutherford backscattering recrystallization of the amorphous surface layer has taken spectrometry (RBS) in the channeling mode. Secondary ion place. These results indicate that the indium implantation in- mass spectrometry (SIMS) was employed to acquire the ele- duced damage in the top Si layer of the SOI shows no notable mental depth profiles. The analysis was performed on a PHI difference from those created in bulk Si. The intrinsic point Adept-1010 Quadrupole SIMS instrument, using an oxygen defects in the top layer of SIMOX seem to have no significant primary beam with impact energy of 3 keV at an impact an- effects on the indium-related defects. gle of 45◦. The indium detection limit under these conditions Fig. 3 displays the indium SIMS profiles obtained from × 13 −2 was around 1 × 1016 at.cm3. the 1 10 cm samples implanted at 150 keV (Fig. 3a) or at 200 keV (Fig. 3b). In both cases, the shape of the in- dium profile after annealing at 800 ◦C for 2 h has undergone 3. Results and discussion no significant changes, whereas the tail end or post-peak re- gion has obviously broadened and spread deeper towards the Fig. 1 shows the RBS channeling spectra of the as- top Si–BOX interface. This behavior is similar to the TED implanted samples under four different implantation condi- effect reported in bulk silicon. It should be noted that even tions. The peak at channel 340 shows oxygen in the surface SiO2 layer that has not been removed before RBS analysis Fig. 2. RBS spectra of SOI implanted with In+ (1 × 1014cm−2 at 200 keV): Fig. 1. RBS channeling spectra acquired from SOI implanted with In+: (a) (1) as-implanted random profile; (2) as-implanted channeled profile; (3) 5 × 1012 cm−2 at 150 keV; (b) 1 × 1013 cm−2 at 150 keV; (c) 1 × 1013 cm−2 channeled profile after RTA; and (4) channeled profile after furnace an- at 200 keV; and (d) 1 × 1014 cm−2 at 200 keV. nealing at 800 ◦C for 2 h. P. Chen et al. / Materials Science and Engineering B 114–115 (2004) 251–254 253 Fig. 4. SIMS profiles of 200 keV 1 × 1014 cm−2 indium implanted samples: 115 + Fig. 3. SIMS profiles of indium in SIMOX implanted with In acquired (a) bulk Si; (b) SOI substrates. from: (a) 1 × 1013 cm−2 at 150 keV; (b) 1 × 1013 cm−2 at 200 keV, before and after furnace annealing at 800 ◦C for 2 h. of the SOI sample. After RTA, significant indium segregation when the implant energy rises to 200 keV, with the implant is observed in both the bulk silicon and SIMOX samples giv- dose still being 1 × 1013 cm−2 as shown in Fig. 3b, the in- ing rise to a peak at 130 nm below the surface. As shown in dium diffusion behavior is still similar to that in bulk Si. The the RBS results above, 1 × 1014 cm−2 indium dose is already higher implant energy only results in more indium dose loss. sufficient to create a completely amorphous layer in SOI. Ac- It seems that the SOI structure has no significant effect on cording to a previous study [9], the interstitials together with indium diffusion in these two cases.
Details
-
File Typepdf
-
Upload Time-
-
Content LanguagesEnglish
-
Upload UserAnonymous/Not logged-in
-
File Pages4 Page
-
File Size-