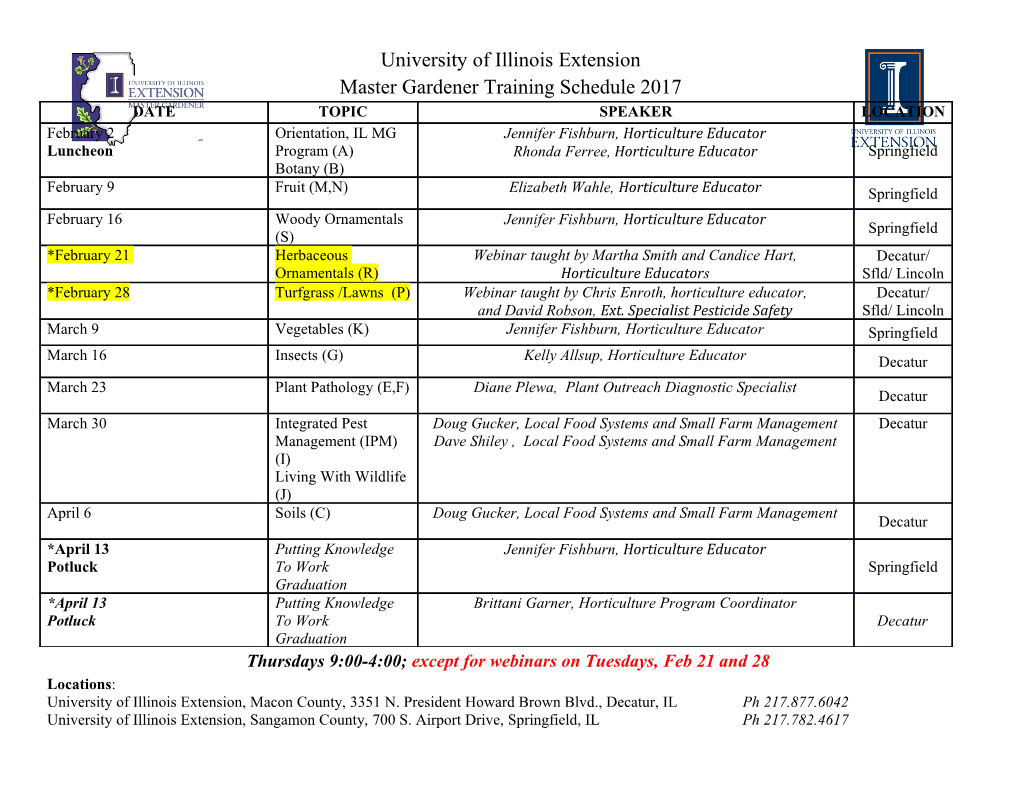
ReturnClose and to SessionReturn DESIGN OF A 45 CIRCUIT DUCT BANK Mark COATES, ERA Technology Ltd, (UK), [email protected] Liam G O’SULLIVAN, EDF Energy Networks, (UK), liam.o’[email protected] ABSTRACT CIRCUIT REQUIREMENTS Bankside power station in London, closed in 1981 but the The duct block was designed to carry the following XLPE substation that is housed in the same building has remained insulated cable circuits without exceeding the operating operational. The remainder of the building has housed the temperature of any cable within the duct block. Tate Modern art gallery since 2000. EDF Energy Networks is now engaged in a project to upgrade and modernise o Four 400/230V circuits with a cyclic loading of 300A. Bankside substation. Part of this work involves the o Twenty 11kV circuits with a cyclic loading of 400A. diversion of about 45 cable circuits into a duct block within o Sixteen 20kV circuits with a cyclic loading of 400A the basement of the substation. The circuits include pilot o Four 66kV circuits with a cyclic loading of 300A circuits, LV circuits and 11 kV, 22 kV, 66kV and 132 kV o Two 132kV circuits with a cyclic loading of 700A circuits. This paper describes the process involved in o Six pilot circuits. designing the duct bank. The cyclic load was taken to be a step wave with 100 % load factor from 08.00hrs to 20.00hrs and 0.8pu from KEYWORDS 20.00hrs to 08.00hrs. Duct bank, Magnetic field, Surface temperature, Cable rating. The cables selected for this installation were of types commonly used by distribution companies in the UK. They were: INTRODUCTION o 400 V, 3 or 4-core XLPE insulated, unarmoured, cables, Bankside power station, on the south bank of the Thames in o 11 kV, Single-core cables laid in triplex formation London, closed in 1981 but the substation that is housed in generally to BS 7870-4.10, the same building has remained operational. In 1995 work o 20 kV, Single-core cables laid in triplex formation was started to transform part of the power station building generally to BS 7870-4.10, into an art gallery, The Tate Modern, which was opened in o 66 kV, Single-core, XLPE insulated cables with copper 2000. EDF Energy Networks is now engaged in a project to wire and aluminium foil screen, upgrade and modernise the Bankside substation. Part of o 132 kV, Single-core, XLPE insulated cables with copper this work involves the diversion of about 45 cable circuits wire and aluminium foil screen. into a duct bank within the basement of the substation. The circuits include pilot circuits, LV circuits, 11 kV, 22 kV, 66kV 150 mm diameter plastic ducts to ENA Technical and 132 kV circuits. Specification 12-24 were selected. The proposed duct bank was to be approximately 100 m The 132 & 66 kV circuits were to be installed in trefoil ducts long over a width of 13 m with a depth of 1.2 m. and the other circuits were to be installed in single ducts. Because of potential future uses for the area above the duct RATINGS CALCULATIONS bank there were a number of factors that had to be taken into account when designing the duct configuration and Nominal Ratings selecting the cable sizes to be used. These included: The first stage in the calculations was to obtain nominal o Maximum cable conductor temperature single circuit, steady state, in duct, ratings for the cable o Floor surface temperature types to be used in the installation. o 50 Hz Magnetic field levels o Cable routing requirements The steady-state current ratings for the LV cables were taken from a base data used to develop ERA Report 69-30 The calculation methods used to design the duct bank were Pt V, [1], those for the 11 kV cables were taken from the a mixture of traditional cable rating calculations, analytical steady state section of Engineering Recommendation P17 calculations for floor surface temperatures and magnetic Part 3, [2]. Nominal steady-state current ratings for the 20 field levels and finite element methods to determine kV, 66 kV and 132 kV cables were calculated, using the shielding requirements. methods set out in IEC 60287, [3], from nominal cable dimensions provided by cable manufacturers. All of the current ratings were adjusted for an ambient temperature of 20°C and a soil thermal resistivity of 1.2 K.m/W. It was ReturnClose and to SessionReturn assumed that the cable screens would be solid bonded in cables selected would run at more than 90°C. This was not all cases. acceptable and showed that the assumption of a grouping factor of 0.7 was overly optimistic. A general cyclic rating factor for the group was calculated using the equation given in Clause 3.2.2 of IEC 60853-1, The calculation method was based on the mutual heating [4]. Although the equations given in IEC 60853-2, [5], were between circuits. Because of this the conductor size more appropriate for the higher voltage cables the simpler selected for one circuit will influence the conductor approach of Part 1 was used for the initial calculations. temperature, and hence the selection of sizes, for surrounding circuits. Thus it would have been possible to select different conductor sizes for each circuit to arrive at a Cable selection solution where none of the cables would be operating at For the initial calculations it was assumed that the ducts higher than 90°C. However it was not considered practical would be installed in three tiers with a horizontal spacing of to specify which cable size should be installed in each duct. 600 mm and a vertical spacing of 500 mm. The only To simplify the final installation it was decided that only one limitation on the location of cables within the duct bank was conductor size would be used for each voltage group. that the 132 kV circuits should be near the sides of the duct bank. This limitation was imposed by the route of the After several iterations, with increased conductor sizes, it existing cables. was concluded that an acceptable solution could not be reached with the duct arrangement chosen. The initial selection of cable sizes was achieved by assuming that a grouping factor of 0.7 would be applicable The duct arrangement was then changed so that the ducts to the group. in the top layer were on 400 mm centres and the ducts in the lower 2 layers were staggered with 800 mm between The temperature rise at each cable due to the heat centres. Eight trefoil ducts were arranged on the lower dissipated by all of the other cables was then calculated layers to accommodate the 132 & 66 kV circuits and allow 2 using the method set out in IEC 60287-2-1 Clause 2.2.3.1. spares. The equation used to calculate these temperature rises, ∆θp, was: With the new cable arrangement lower temperatures were achieved but an acceptable solution still could not be found. θ∆+θ∆+θ∆+θ∆=θ∆ p2p1p L kp L qp [1] The initial data was then revisited and it was decided that Where: because the ducts were to be surrounded with concrete it d ′ 1 pk was reasonable to use a lower value of thermal resistivity =θ∆ ρ W ln for the surrounding medium. A value of 1 K.m/W was used kp 2π kT d pk for the next iteration. θ∆ kp = temperature rise at cable p due to heat dissipated An acceptable solution was achieved where none of the by cable k, cables exceeded their maximum operating temperature of 90 °C. However the conductor size required for the 132 kV ρT = thermal resistivity of backfill, Wk = power dissipation from cable k, cables was considered to be excessive and the triplex 22 kV cables had an outside diameter that was close to the duct d’pk = distance from cable p to the reflection of cable k in the ground-air interface, size. In order to reduce the size of the 132 kV cables the effect of single-point bonding was investigated. Also the dpk = distance from cable p to cable k . effect of the cyclic load was considered in greater detail. The temperature rise of each cable due to the load it carried For the next calculations the cyclic rating factor was was calculated on the basis that this temperature rise was calculated for each cable based on the method set out in proportional to the square of the load current. This was Clause 7.3 of IEC 60853-2. added to ∆θp and the ambient temperature to determine the conductor temperature for each cable. The final solution gave the cable conductor temperatures listed in Table 1 with the duct layout shown in Fig. 1. These initial calculations demonstrated that many of the ReturnClose and to SessionReturn Figure 1 Duct layout Table 1 Cable temperatures It is also noted that the solution that has been arrived at is not the only solution for this number of circuits. Increasing Temperature Temperature Circuit Circuit the conductor size in one voltage group could allow the °C °C conductor size to be reduced in another voltage group. 400 V,1 82 20 kV, 1 53 Also moving ducts closer together or further apart will 2 75 2 55 influence the calculated temperatures. However it was considered that adopting a relatively simple duct 3 82 3 82 arrangement with regular spacings would lead to a simpler 4 81 4 76 installation. 11 kV, 1 70 5 55 FLOOR SURFACE TEMPERATURE 2 71 6 53 The calculations described above are based on the method 3 71 7 55 given in IEC 60287.
Details
-
File Typepdf
-
Upload Time-
-
Content LanguagesEnglish
-
Upload UserAnonymous/Not logged-in
-
File Pages6 Page
-
File Size-