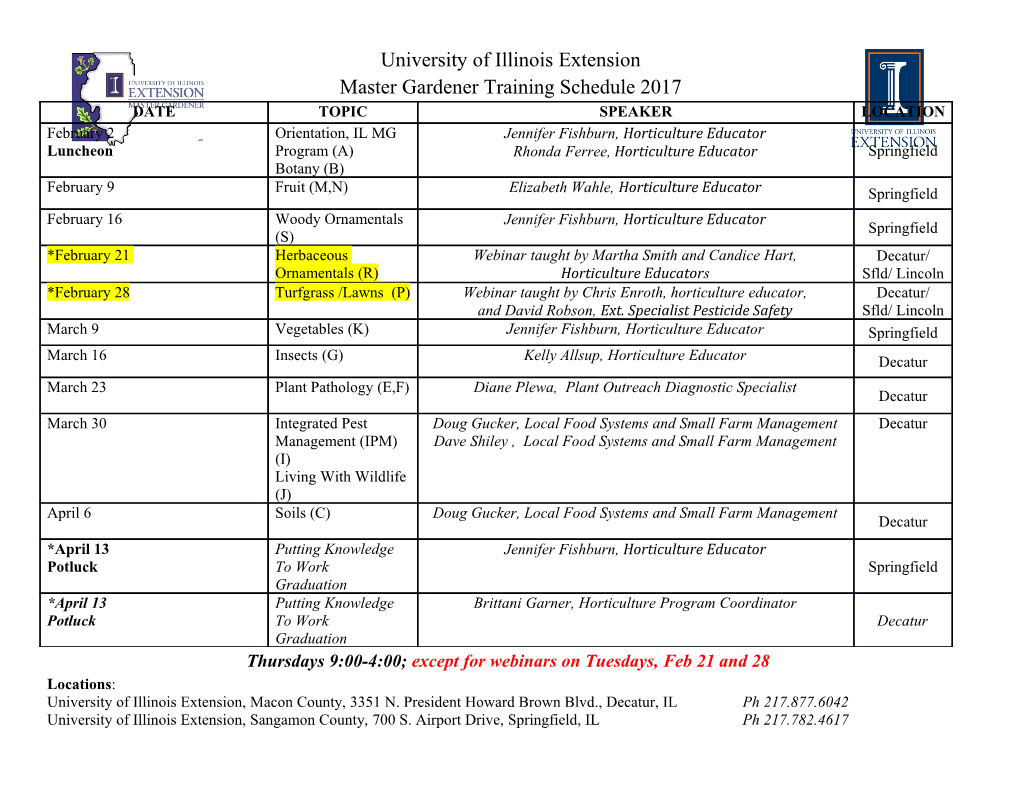
Travis Bean Guitars Page 1 of 10 http://www.autohobbydigest.com/aluminum_guitars/travisbean.html Go JUN AUG SEP Close 41 captures 7 Help 15 Nov 04 - 7 Aug 08 2007 2008 2009 Travis Bean This article discusses the history of the 1974-79 Travis Bean guitars and basses. It provides a brief history of the instruments as well as discussing some current popular Travis Bean topics such as identifying and dating the instruments. History of the Travis Bean Guitar Travis Bean manufactured aluminum neck guitars and basses from 1974 to mid-1979. Travis Bean had two partners: Marc McElwee and Gary Kramer (Kramer left within a few months of the first production run and went on to manufacture his own guitars ). All Travis Beans were handmade in a factory in Sun Valley, California. Quality was very important to the small staff, and either Bean or McElwee played every single guitar and bass before it left the factory. Travis Bean guitars were built around the patented one piece neck. Raw Reynolds 6061-T6 aluminum stock was used to produce a one piece neck that ran from the tuning machines all the way down to the bridge. The bridge mounted directly to the neck unit, and the strings ran through the body. The pickups were made with Alnico 5 magnets and capped with stainless steel covers. On top of the pickup covers was etched "Travis Bean". Like the bridge, the pickups mounted directly to the neck assembly, with adjustment and mounting "bolts" accessable from the back of the guitar (there are no screw heads visible on the front of the guitar, even the bridge mounting screw heads are "hidden" beneath the saddle pieces). The rosewood or ebony fretboards were epoxied directly to the neck. On later models, the fretboards were epoxied to a 3/32 aluminum plate which was then bonded to the neck. The wood bodies were epoxied to the neck assembly. Travis Beans came with Schaller, and Grover tuning machines were used through most of the production years, with Gotoh machines being used toward the end as well. Most Travis Bean http://web.archive.org/web/20080807220144/http://www.autohobbydigest.com/alumi... 23/06/2013 Travis Bean Guitars Page 2 of 10 guitars and basses came with brass nuts. Knobs and switch handles were various types (clear,gold,black,etc) and assembly of these items depended on what was in stock and on hand. The aluminum neck design had it's fair share of criticism. People complained about the aluminum expanding and contracting with changes in temperature, thus causing tuning problems. There were also complaints about the neck being too cold. Travis Bean tried to combat this problem by making a black acrylic neck coating standard on all Model 500's at some point, and optional on the Artist, the Standard and the Bass Guitars. Travis Bean Sales literature argued that this coating gave the neck "the warmth and feel of a conventional guitar neck (you don't feel the wood, you feel the finish; the lacquer or the paint)." The coated neck was never a real popular option, most people probably liked to see the aluminum neck. The Standard Guitar was the most popular model. It had two Travis Bean Humbuckers, a rosewood fretboard with dot inlays, and a magnolia body. A koa wood body could be had at an added cost. The Artist was basically a Standard with a carved top (much like a Paul Reed Smith guitar). All Artist's had koa wood bodies. These guitars were priced higher than any of the other Travis Beans, in fact some Travis Bean Sales literature points out that the only thing your are paying extra for are visual aesthetics. The Model 500 had a similar neck unit as the Standard and the Artist, except it's form factor as it entered the wood body is somewhat different than that of the Standard and the Artist. The difference, no doubt, doesn't affect sound in an adverse fashion. In simple terms, the "neck-thru" design of the the 500 does not reveal itself as it travels through the body to the bridge as it does with the Standard and the Artist. Whiel the Artist and the Standard used a symmetrical ES-335 shaped body, the Model-500 was similar to a Stratocaster. It had two Travis Bean single coil pickups, an aluminum bridge (rather than a chrome-plated brass bridge), and a plastic pickguard. (there is a picture of a http://web.archive.org/web/20080807220144/http://www.autohobbydigest.com/alumi... 23/06/2013 Travis Bean Guitars Page 3 of 10 Model 500 below). Travis Bean also made a wedge shaped guitar, appropriately named "The Wedge". It was basically shaped like a Gibson flying V, only it was triangular (no lower "v" notched out), and symmetrical as well. Production of this model was quite low, although it was available from 1975 to 1979. In 1979 production of Travis Bean guitars and basses ended. Over time additional investors were brought in to help with cash flow problems. Some of Bean's financial backers began pressuring him to lower prices and costs and cut corners. Not wanting to sacrifice quality, Bean decided to close up shop. Travis Bean had also become disinterested with the many aspects of a production operation. I don't know if a total production figure can be nailed down. In a recent [late 1990s] Vintage Guitar Magazine article by C. William Kaman II (Ovation Guitars) pinpoints the production at 3650 total, with 1422 Standards, 755 Artists, 1023 basses, 45 Wedge guitars, and 36 Wedge basses (that leaves about 370 for the Model 500 and any miscellaneous and prototype guitars that may have been built). I'm not convinced that production was this high, however, these numbers have been backed by Travis Bean himself, and no one has been able to offer any information to the contrary. Travis Beans were expensive in their day. A 1978 price list shows the Model 500 retailing for $500, the Standard Guitar (later called the TB1000S) going for $995, and the Artist Guitar (later known as the TB1000A) listing for $1,195. Lefty models added another $200 to the price. Despite this high price, production costs were so high that in interviews, Travis Bean has made no bones about it, he lost money on every guitar he built. Most Travis Bean guitars were finished in either a clear finish on a Koa or Magnolia body or with the opaque colors of red, black, white, and cream. By far the most common finish for Standards and Artists is a clear acrylic finish. Since most of uniqueness of the guitar is actual the neck assembly, and since the pickups mount to the neck and the bridge does as well, and the body is little more than a "handle". the shape of the wood body could be varied http://web.archive.org/web/20080807220144/http://www.autohobbydigest.com/alumi... 23/06/2013 Travis Bean Guitars Page 4 of 10 without adding much difficulty to the final assembly process. Due to this "unit" construction, custom body shapes would have been easy to make, however Travis discouraged the manufacture of "custom" shaped guitars. There were custom applications including some double neck Travis Beans and some lefthanded versions as well. As an aside, Travis Bean seem to strive toward ensuring a "production" shop image to the public (as apposed to a "custom" guitar shop). Evidence of this is his reluctance to accept custom orders, as well as advertisements and sales literature offering a distinct model line. left to right: Wedge, Standard #547 with koa body, Artist #615 back and front (center) missing pick guard with a non-original sunburst finish. Note that the lower horn is shaped differently than the upper horn; Model 500 (far right ). Travis Bean Returns to Guitar Building In 1998, Travis Bean announced that he would soon be building guitars again. These guitars were to share some of fine qualities of his original guitars, but in addition, Travis Bean was to incorporate some "new ideas". He designed and built a few prototypes, launched a business, and made press announcements. Travis Bean contracted with Bernie Hepner of Edenhaus guitars to build the new guitars but only 9-10 were actually made. These guitars were priced at $6000 to $8000 each, which no doubt, accounted for the lack of buyer interest. Travis Beans Dating and Running Changes http://web.archive.org/web/20080807220144/http://www.autohobbydigest.com/alumi... 23/06/2013 Travis Bean Guitars Page 5 of 10 There is also a question of dating Travis Beans and finding when a particular guitar was manufactured. Obivously the serial number goes along way to determining the date with higher numbers being produced later in the years of production. Some direction can be provided by looking at changes in production as well. Serial Numbers: Serial numbers can be very confusing. To date every theory or pattern that I've see put forth has proven to be flawed by epirical evidence. The following serial number schema may ressemble some truth, but it has been proven to be somewhat incorrect: Serial numbers are not unique number across all Travis Beans. All production model lines began numbering with #10. For the Wedge, the Bass, and the Model-500 models, serial numbers were unique for each of the three models. That is to say that each of these three models started with #10 and incremented upward as models were produced (to illustrate this point, there was a Bass #10, a Model-500 #10, and a Wedge #10).
Details
-
File Typepdf
-
Upload Time-
-
Content LanguagesEnglish
-
Upload UserAnonymous/Not logged-in
-
File Pages10 Page
-
File Size-