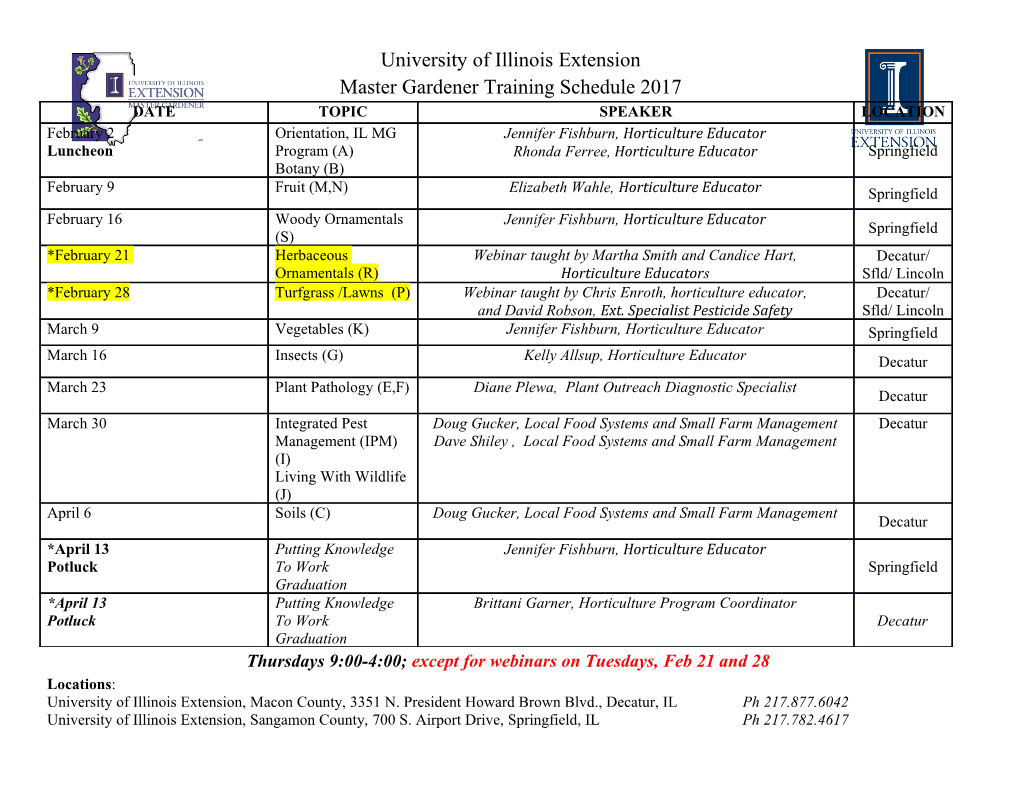
SELF-LUBRICATING POLYMER COMPOSITES: USING NUMERICAL TRIBOLOGY TO HIGHTLIGHT THEIR DESIGN CRITERION Villavicencio M. D. (1,2,3,4), Renouf M. (2,6), Saulot A. (1,6), Michel Y. (3), Mahéo Y. (4), Colas G. (5), Filleter T. (5), Berthier Y. (5,6) (1) LaMCoS, Université de Lyon, INSA-Lyon, CNRS, Villeurbanne, France. Email: maria.villavicenciorojas@insa- lyon.fr, [email protected], [email protected] (2) LMGC, Univ. Montpellier, CNRS, Montpellier, France. Email: [email protected] (3) CNES, 18 avenue Edouard Belin, 31401 Toulouse Cedex 9, France. Email: [email protected] (4) SKF Aerospace, F-26300 Châteauneuf-sur-Isère, France. Email: [email protected] (5) Department of Mechanical and Industrial Engineering, University of Toronto, Toronto, Canada. Email: [email protected], [email protected] (6) InTriG, International Tribology Group, Villeurbanne, France. ABSTRACT double transfer (see Fig.1) [3][4][5]. Among those After the cessation of RT/Duroid 5813, manufacturing materials RT/Duroid 5813 and PGM-HT are known for tests were performed by CNES and ESA/ESTL in order their use in space applications. After the cessation of to find an alternative material. Although PGM-HT was RT/Duroid 5813 manufacturing, PGM-HT was selected selected as the best candidate, limitations about its as the best replacement option [6]. Nevertheless, after tribological capabilities to replace RT/Duroid 5813 were tribological expertise on lifetests carried out by Sicre et later pointed out. Today, the predictability of the al [3], it was concluded that the performance of PGM- tribological behaviour of those materials is not fully HT as a replacement for Duroid should be improved. overcome. The motivation to this work is to For PGM-HT as for RT/Duroid 5813 its composition complement studies of self-lubricating materials by remain still not fully known, despite the fact that the coupling experimental analyses with numerical importance of the composite microstructure on the modelling, in order to predict their tribological tribological performances has been previously pointed behaviour. A Discrete Element Method is chosen to out [3][4][7][8], the role and impact of the different construct the numerical material, because it allows to constituents on the degradation and lubrication represent wear and the third body generation at the scale mechanisms remain not well understood (as the size of of the ball/retainer contact. An underlying role of the the fillers, the microstructure, or the volume fraction). adhesion between components in controlling the tribological properties of the transfer film has been In this work, it is proposed to couple an experimental observed. and a numerical approach in order to complement the on-going studies that investigate self-lubricating INTRODUCTION materials with a focus on PGM-HT composite. An The accomplishment of spacecraft missions strongly accurate simulation of the double transfer mechanism is depends on the reliability of mechanisms. This not an easy task: the whole mechanism should be reliability in turn, depends on the life and functionality represented (for example the bearing and its of their components parts: here lays the importance of solicitations), the degradation of the composite material space tribology. A recent example is the Juno mission and the evolution of the debris within the system. to Jupiter, which has been stuck in making long laps Despite modelling the whole system is desired, it is around the planet because of “sticky valves” [1]. possible to have a local approach to identify the possible scenarios of double transfer mechanisms. For such a In space applications, design of the components and of model, Discrete Element framework appears as the most the lubricants must be robust not only to endure the appropriate tools to describe third body flows [9] (from conditions of space, but also the rigours of the launch material degradation to wear). An equivalent numerical environment. Both liquid and solid lubricants can be approach has already been used in the context of C/C used for space applications. Where temperature and composites [10]. In the present work, the approach is contamination issues exclude the use of fluid lubricants, extended to self-lubricating composites. As a first solid lubrication is used [2]. Self-lubricating composite approach a single contact is taken into account, and only materials are an example of dry lubricants. They are an elementary volume of the cage/ball contact is usually used as the retainer material of ball bearings. considered. A meshless strategy is used, and the volume The composite is involved in forming a composite is discretized with circular rigid bodies. Consisting of transfer film from the cage to both balls and races by independent elements, a discrete element modelling intermittent sliding contact at balls/cage contact all must integrate interaction laws between the elements to along lifetime, so the retainer material itself provides enable to describe both the overall mechanical lubrication to the bearing by a mechanism known as ___________________________________________________________________ Proc. ‘ESMATS 2017’, Univ. of Hertfordshire, Hatfield, U.K., 20–22 September 2017 F periodic conditions L Cage 1’# Ball periodic conditions V L (a) (b) (c) Figure 1 – (a) Scheme of the double transfer mechanism. The zones 1, 1’, 2 and 2’ are used as a reference to point the orientation of the ball and the contact ball/cage. A first contact is made between the cage and the ball: see zone 1’; then the ball transfers the transfer film (also known as third body) to the races. (b) Zoom of the contact cage-ball. (c) Scheme of the mechanical boundary conditions applied on a composite (PGM-HT) numerical sample of size L, under tribological conditions, with a force F applied on the top, and a shearing speed v applied in the bottom representative of the speed of the ball. behaviour of materials [9] (as elastic modulus, density tomography it was possible to build the numerical or Poisson's ratio) and the local tribological behaviour sample (see section 3.1). (detachment, agglomeration of third body particles). Such laws must be included in a composite geometric 2.1 Microstructure and Composition Studies model of the proportions and shapes of its components For the microstructure analyses SEM observations are (matrix and / or reinforcements and / or fillers...). carried out. To this end, samples are cut perpendicularly Experiment analyses are carried out to inform the to the axis of the cylinder, at room temperature. Then, model. X-Ray tomography and Atomic Force the surfaces generated after cutting are observed in a Microscopy (AFM) analyses are made to identify the SEM FEI, XL30 (see Fig. 2). It is observed by SEM that volume fraction of the components (fibre, MoS2 and fibres of PGM-HT have a diameter of about 20 µm, and PTFE) and the adhesion between them, respectively. their length is of about 100 µm. Regarding MoS2 Constituent data obtained from experimental analyses particles, their size could reach 100 µm. These results are shown in Section 2. Then, model hypothesis are validate the observations made in literature about PGM- presented and are related to the experimental results in HT [3]. It has in fact a coarser microstructure than Section 3. Finally, results obtained by DEM simulations RT/Duroid 5813 (in which the fibre length can reach are shown in Section 4. 300 µm and their diameter can be smaller than 3 µm, while the MoS2 particles have a size of about 10 µm). 2. EXPERIMENTAL CHARACTERISATIONS EDX analyses are carried out on the fibres of PGM-HT In order to create the numerical sample, several in order to identify their components. The following information is necessary: 1) the composite composition elements were found: Si, Al, O, S, and Ca. According to (from a material and a geometrical point of view), 2) an the chemical composition and to SEM observations, it estimation of the size of the representative element appears that PGM-HT is composed of E-glass fibres. volume and 3) the interaction laws and adhesion values between the different elements of the model. To fulfil After these first characterisations, an X-ray Tomograph the three previous points, three characterisations are High resolution (type tomograph RX Solutions realised: 1) observations by Scanning Electron EasyTom Nano – with a resolution of 0.7μm per pixel) Microscopy (SEM), 2) observations by X-ray is used in order to build a realistic 3D image of the tomography and 3) adhesion measurements by atomic microstructure of PGM-HT, and to be able later to build force microscopy (AFM). The sample of the self- a realistic morphological representation of this lubricating material used for observation is cylindrical, composite. For the X-ray analyses, samples of and has a length of 12 mm, and a diameter of 7 mm. 0.5×0.5×0.5 mm3 are cut at room temperature. 3D The material observed was PGM-HT, produced by JPM volumes are reconstructed (see Fig 3.) through the Mississippi (USA). This sample is the same that the ImageJ software and its extension Fiji. Under X-ray, the one used in [4] for the tribological testing (same batch, white areas indicate the presence of MoS2, light grey same machining process and it is also preconditioned in areas indicate the presence of glass or mineral fibres vacuum). In order to determine the microstructure and (according to the composite), and the black areas are the composition of the composite, two techniques of related to the PTFE matrix. X-ray tomography not only observations have been used: Scanning Electron allows to visualize in the bulk and in 3D, but also to Microscopy and X-ray Tomography. With SEM it was measure the volume fractions of the components. It possible to have information about the fibres diameter, appears that the PTFE represents two-thirds of the length, and chemical composition.
Details
-
File Typepdf
-
Upload Time-
-
Content LanguagesEnglish
-
Upload UserAnonymous/Not logged-in
-
File Pages9 Page
-
File Size-