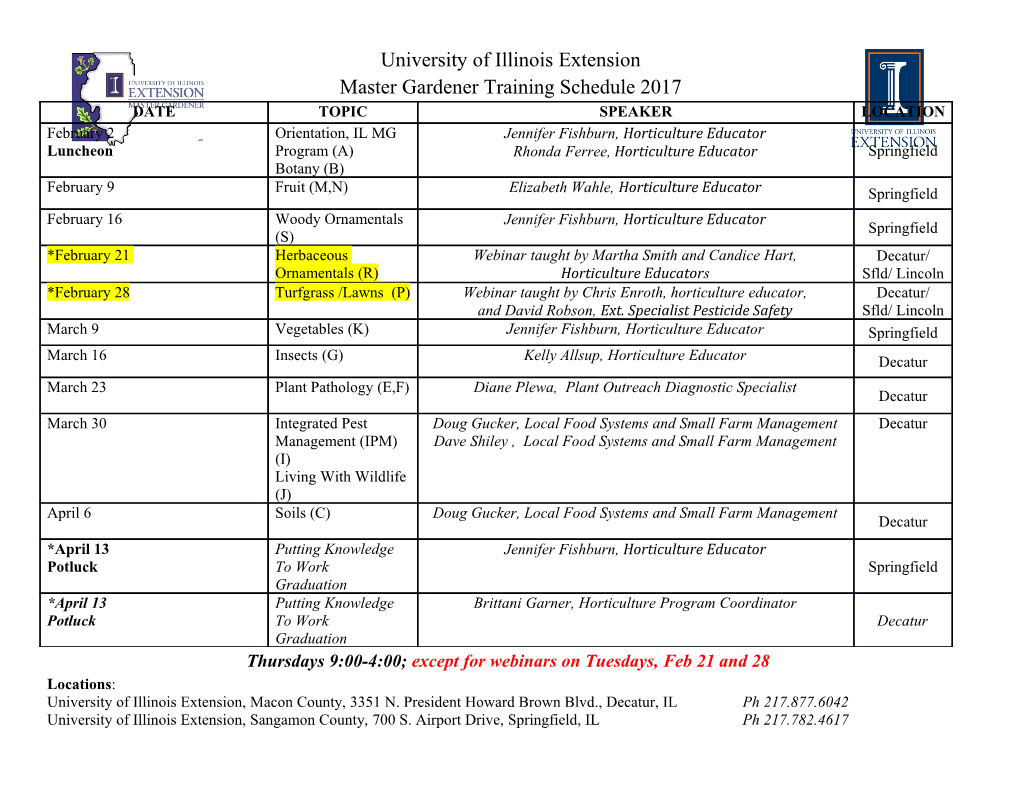
Plastic mesocombustors Jeongmin Ahn*, and Paul Ronney Aerospace and Mechanical Engineering University of Southern California Los Angeles CA 90089-1453 Abstract Recent experimental and theoretical studies of heat-recirculating combustors have demonstrated the importance of thermal conduction through the structure of the combustor on its performance. In particular, this solid-phase heat conduction inevitably degrades performance via transfer of heat out of the reaction zone to the surrounding structure, which is then lost to ambient. This in turn leads to a reduction of reaction temperature and thus sustainable reaction rates. By use of platinum- based catalysts in spiral counterflow "Swiss roll" heat-recirculating combustors, we have been able to sustain nearly complete combustion of propane-air mixtures at temperatures less than 150˚C using combustors built with titanium (thermal conductivity (k) of 7 W/m˚C). Such low temperatures suggest that high-temperature polymers (e.g. polyimides, k ≈ 0.3 W/m˚ C) may be employed as a combustor material. With this motivation, a polyimide Swiss roll combustor was built using CNC milling and tested over a range of Reynolds numbers with propane fuel and Pt catalyst. The combustor survived prolonged testing at temperatures up to 450˚C. Reynolds numbers as low as 2 supported combustion, with thermal power as low as 3 watts and temperatures as low as 72˚C. These initial results suggest that polymer combustors may prove more practical for meso- or microscale thermochemical devices due to their lower thermal conductivity and ease of manufacturing. Applications to electric power generation via single-chamber solid oxide fuel cells are discussed. Introduction is fixed. This makes heat transfer design simpler than gas It is well known that hydrocarbon fuels contain 100 phase combustion in which the location of reaction zone times more energy per unit mass than lithium-ion batteries, may change in undesirable ways. Also, the lower thus devices converting of fuel to electricity at better than temperature of catalytic combustion makes thermal stresses 1% efficiency represent improvements in portable electronic and materials limitations less problematic. devices and other battery-powered equipment [1]. At small In particular, our experiments and modeling [4,5] have scales, however, heat and friction losses become more shown that counter-current heat-recirculating reactors significant, thus devices based on existing macro-scale require thin walls with low thermal conductivity for designs such as internal combustion engines may be maximum performance at small scales. Normally metallic impractical. Consequently, many groups have considered or ceramic reactors are required for high temperatures, but heat-recirculating burners or “excess enthalpy” burners first metals have high thermal conductivity (thus relatively poor studied 30 years ago [2,3] for thermal management and performance in small-scale devices) and thin-walled thermoelectric, piezoelectric or pyroelectric devices, having ceramics are too fragile and still have marginally acceptable no moving parts, for power generation. In heat-recirculating thermal conductivity. Instead, we construct our reactors burners, by transferring thermal energy from the combustion from polyimide plastics, which have far lower thermal products to the reactants without mass transfer (thus dilution conductivities than metals (typically 100x lower) or even of reactants), the total reactant enthalpy (sum of thermal and ceramics (typically 10x lower). Polyimides have excellent chemical enthalpy) is higher than in the incoming cold high temperature resistance compared to practically all other reactants and therefore can sustain combustion under plastics. Plastics have the additional advantages of low conditions (lean mixtures, small heating value fuels, large cost, ease and variety of fabrication techniques, durability heat losses) that would extinguish without recirculation. and electrical insulation properties. The ease of fabrication At smaller scales heat losses become more important due moreover enables us to pursue more complex Swiss roll to increased surface area to volume ratios. A potential configurations as may be necessary for maximum fuel means of reducing the impact of these losses is to employ utilization. catalytic combustion, which may allow lower temperatures and thus allow reaction to occur at higher heat losses than Specific Objectives can possibly be sustained with non-catalytic combustion. Our experimental and theoretical studies [4,5] of heat- The higher surface area to volume ratio at small scales recirculating combustors clearly confirmed that thin walls makes area-limited catalytic combustion even more with low thermal conductivity materials are needed for attractive as compared to volume-limited gas phase maximum performance at small scales. We have been able combustion. There are additional potential advantages of to sustain reaction of propane-air mixtures with Pt foil catalytic combustion as well. Since chemical reactions only catalyst at temperatures less than 150˚C using combustors occur on the catalyst surface, the location of the heat source * Corresponding author: [email protected] Associated Web site: http://cpl.usc.edu/ built with titanium. Such low temperatures suggest that which we have found yields far superior performance at polyimides may be employed as a combustor material. lower temperatures [4], were placed along the walls at the Consequently, the objectives of this work are to build center of the burner. The top of the burner is sealed with and test polyimide Swiss roll combustors over a range of fibrous ceramic blanket, backed by aluminum plates, Reynolds numbers and assess the feasibility of polyimide secured with Heat Shield ceramic adhesive. The fresh fuel- Swiss roll combustors for self-sustained thermal air mixture is plumbed through a manifold attached to the management at the low Reynolds numbers that would be inlet of the Swiss roll. Electrically heated Kanthal wire was encountered in a microscale device. used for ignition. The burner was instrumented with thermocouples located at the center and in each inlet and Experimental Apparatus exhaust turn (six total). Hastings mass flow controllers The concept of polymer reactors were tested using were used to regulate the flow rate of fuel and air through reactors made from commercially available DuPont™ the burner. Labview data acquisition software was used to Vespel™ or Kapton™ polyimides. These polymers are record the response of each thermocouple and to control the completely non-flammable in air; the minimum oxygen mass flow controllers. concentration that sustains combustion is 53% / 45% for Vespel™ / Kapton™. Vespel™ is a hard plastic, typically Results and Discussion sold in block form, that is ideally suited for CNC milling; Recently, our experimental and theoretical studies [4,5] the reactors (Fig. 1) were milled automatically from of heat-recirculating combustors indicate that optimal SolidWorks™ CAD files; with this scheme we were able to combustor performance could be achieved by reducing wall design, built and test new design configurations in 1 – 2 thermal conductivity. A Vespel™ (k ≈ 0.29 W/m˚C) Swiss working days. The outside dimensions of Vespel™ burner roll that was geometrically similar to the 3.5-turn titanium are 46 mm wide by 46 mm deep by 25 mm tall with 0.5 mm (k ≈ 7 W/m ˚ C) combustor used previously [4] was wall thickness. The gap-width for each inlet and exhaust constructed to test this hypothesis. channel is 3 mm. Due to the limitation of CNC milling Figure 3 shows a comparison of the extinction limits technique, very thin-walled structures are difficult to mill, obtained between with the Vespel™ and titanium Swiss another simple fabrication technique that is to fold 0.25 mm rolls. These limits are shown in Figure 3 over the range of thick sheets of Kapton™ into spirals and glue them to base Reynolds numbers tested. The Reynolds number is defined made by same material (Fig. 2) was developed. The outside based on the area-averaged gas velocity at the inlet, the gas dimensions of Kapton™ burner are 15 mm wide by 15 mm kinematic viscosity at the inlet, and the gap width. Lean and deep by 15 mm tall. The gap-width for each inlet and rich extinction limits were determined by starting from a exhaust channel is 1 mm. steady burning state and decreasing or increasing the fuel concentration with the igniter off. (a) (b) Figure 1a: 46 mm CNC-milled Vespel™ Swiss roll reactor Figure 1b: Vespel™ reactor in test configuration Figure 3: Comparison between extinction limits obtained (a) (b) with the Vespel™ and titanium Swiss rolls. Figure 2a: 15 mm folded Kapton™ reactor Figure 2b: Kapton™ reactor in test configuration, top The figure demonstrates that reducing wall thermal sealing plate removed for clarity. conductivity extends extinction limit to lower Reynolds numbers and allows weaker mixtures to be burned, The performance of these reactors was tested using particularly at low Reynolds numbers when heat loss propane fuel and Pt foil catalyst specially treated with NH3, becomes predominant. For both the Vespel™ and titanium 2 burners, the lean flammability limit is actually rich of demonstrated. These temperatures are high enough to stoichiometric at low Reynolds numbers. provide excellent single-chamber solid oxide fuel cells Figure 4 shows the maximum temperatures at the lean (SOFC) performance (not shown) when using our and rich extinction limits obtained
Details
-
File Typepdf
-
Upload Time-
-
Content LanguagesEnglish
-
Upload UserAnonymous/Not logged-in
-
File Pages4 Page
-
File Size-