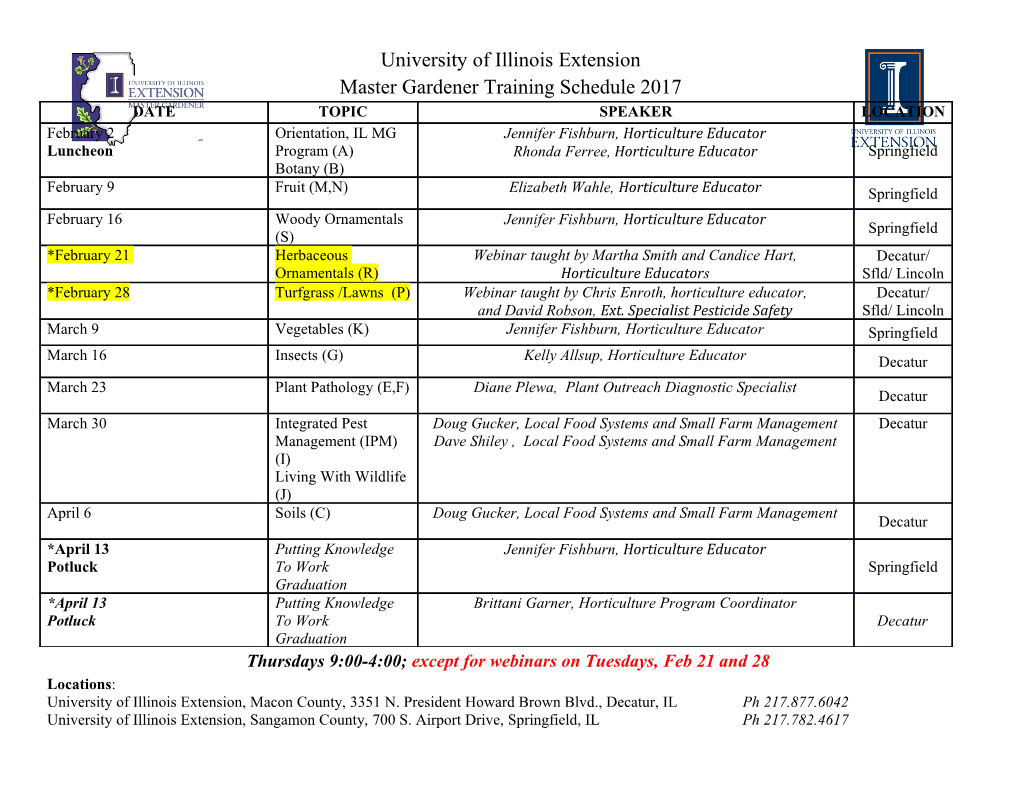
Trans. Japan Soc. Aero. Space Sci. Vol. 56, No. 6, pp. 328–336, 2013 Numerical and Experimental Analyses of the Ducted Fan for the Small VTOL UAV Propulsion By Leesang CHO,1Þ Seawook LEE2Þ and Jinsoo CHO2Þ 1ÞDepartment of Mechanical Systems Engineering, Hansung University, Seoul, Republic of Korea 2ÞSchool of Mechanical Engineering, Hanyang University, Seoul, Republic of Korea (Received February 9th, 2012) Ducted fans have higher thrust performance, higher propulsion efficiency and lower noise characteristics due to their duct system compared with commercial isolated propellers. The purpose of this study is to present design procedures in order to improve the aerodynamic performance of the ducted fan for the small VTOL UAV propulsion. In addition, the duct effect of ducted fans is analyzed to satisfy design requirements and improve performance. Aerodynamic design of the rotor and the stator blades of the ducted fan involves a series of steps: meanline analysis, through-flow analysis and aerodynamic analysis, based on consideration of the design requirements. The thrust performance of the ducted fan is somewhat higher compared with that of the rotor only, but wind tunnel test results of the ducted fan do not satisfy the design requirements. The thrust performance of the ducted fan is significantly different in the CFD results and wind tunnel results due to the inconsistency of the intake and the duct shape. Therefore, the thrust performance of the ducted fan would be somewhat improved by the optimization of the intake and the duct shape. Key Words: Ducted Fan, Free Vortex Design, Through-Flow Analysis, CFD Analysis, Wind Tunnel Test Nomenclature rotor: rotor efficiency stator: stator efficiency [A]: finite difference coefficient matrix Ã: degree of reaction b: mean stream surface thickness parameter : air density DR: rotor diameter : stream function F: flux vector !~: angular velocity Fz: force vector in z direction G: flux vector 1. Introduction H: flux vector I: relative enthalpy, or rothalpy Autonomous flying vehicles, which are commonly known J: source term as unmanned aerial vehicles (UAVs), are currently used for N: rotational speed military missions and civil applications such as reconnais- p: pressure sance, surveillance and topographical surveys.1) UAVs take R: ducted fan radius advantage of the lower operating cost, the lower risk and r: blade radius the higher practical use compared with manned aircraft in r~: position vector of rotating reference frame warfare and danger zones.2) rtip: blade tip radius Ducted-fan UAVs are typical example of vertical take- T: temperature, thrust off/landing (VTOL) UAVs, which do not need a runway U: solution vector, blade rotational speed and can constantly observe surveillance areas by hovering, Utip: blade tip speed and there is more interest in them than existing fixed-wing V: absolute velocity UAVs.3) Vr: radial component of absolute velocity Ducted-fan UAVs can also operate in hover mode and can Vz: axial component of absolute velocity fly at high speed by pitching over towards a horizontal atti- 4) V: tangential component of absolute velocity tude. Therefore, ducted-fan UAVs have attracted attention Wr: radial component of relative velocity as the future combat system due to their more compact size Wz: axial component of relative velocity and higher static thrust/power ratio than any other VTOL 5) W: tangential component of relative velocity UAV. z: axial component In general, a conceptual description of a ducted-fan UAV : absolute flow angle is shown in Fig. 1. The rotor is the propeller at the center of : relative flow angle the UAV, which is supported by the fuselage. The fuselage fan: fan efficiency is connected to the duct by struts, and the duct encases the remaining internal components. The stator blades, which Ó 2013 The Japan Society for Aeronautical and Space Sciences Nov. 2013 L. CHO et al.: Numerical and Experimental Analyses of the Ducted Fan for the Small VTOL UAV Propulsion 329 Fig. 2. Mission profiles of the ducted-fan VTOL UAV. Most studies on ducted-fan UAVs have used CFD analy- Fig. 1. Schematic diagram of the ducted-fan VTOL UAV.3) sis and wind tunnel tests to investigate performance rather than design optimization to improve aerodynamic perfor- mance. Furthermore, the stability of ducted-fan UAVs has straighten the swirling flow induced by the rotor, are located mainly been investigated from the point of view of flight downstream of the rotor inside the duct. Finally, the moving control. flaps (or control vanes) are downstream of the stators, creat- The stability and the flight control of ducted-fan UAVs ing control forces and moments from the high-speed exit are the most important factors. flow to stabilize and steer the UAV.6) As shown in Fig. 2, ducted-fan UAVs demand high The General Dynamics ducted-fan UAVs were developed endurance due to the same thrust performance despite the and flown starting in 1960 with the PEEK aircraft.7) In 1999, small size and light weight. Therefore, the improvement the Micro Craft iStar vehicle was manufactured (two 9-inch of the thrust performance and the propulsion efficiency for diameter flight test vehicles manufactured under DARPA ducted-fan UAVs is required based on a systematic study funding).8) of the aerodynamic design and the aerodynamic analysis Ducted fans have higher thrust performance, higher pro- of the ducted fan. pulsion efficiency and lower noise characteristics due to In this study, systematic design procedures are presented their duct system compared with commercial isolated pro- in order to improve the aerodynamic performance of the pellers.9) Empirical data show that the total thrust produced ducted fan for the small VTOL UAV propulsion. The duct by the ducted rotor system in hover mode is usually 20 to effect of the ducted fan is analyzed to satisfy design require- 50% greater than that of an identical unducted rotor operat- ments and improve performance as well as verify the results ing at the same power.10) presented by McCormick.10) In recent years, aircraft researchers and designers have shown great interest in the use of ducted fans for the propul- 2. Ducted Fan Design sion of UAVs and special air vehicles which can achieve vertical take-off and landing. To improve the aerodynamic performance of the ducted Guerrero et al.3) implemented a multidisciplinary design fan for the small VTOL UAV propulsion, systematic optimization framework to enable conceptual design of design procedures are required for the rotor and the stator ducted-fan UAVs. blades. Design procedures of the rotor and stator blades Ko et al.11) presented the design tool, which enables mul- for the ducted fan are shown in Fig. 3. tidisciplinary design optimization (MDO) and trade studies Aerodynamic design processes for the rotor and stator in the conceptual and preliminary phases of design. blades of the ducted fan follow a series of steps, which are Computational fluid dynamics (CFD) analyses and wind meanline analysis, through-flow analysis and aerodynamic tunnel tests have been performed on the ducted fan by analysis, based on consideration of the design requirements. several researchers. When the performance characteristics of the designed Akturk et al.12) investigated viscous and turbulent flow ducted fan do not satisfy the design requirements at each fields around and inside the ducted fan for hover and for- design step, the design process is restarted again at the ward flight conditions with cross-wind using a commercial previous design step. CFD tool (FLUENT) and the PIV system in the wind tunnel. In this present paper, the rotor and stator blades of the Fleming et al.13) measured aerodynamics characteristics ducted fan are designed using meanline analysis and the of the baseline vehicle and traditional control vanes in simplified meridional flow method16,17) according to the cross-wind using the balance system in the wind tunnel. design requirements. Through-flow analysis uses the matrix Avanzini et al.14) analyzed the flowfield around the air- method18) for the hub-to-shroud flow fields of the meridional 19) frame of the ducted fan vehicle and investigated the per- plane (Wu’s S2 surface ). Aerodynamic analysis of the formance and the stability characteristics. Furthermore, ducted fan is performed using a commercial CFD tool De Divitiis15) calculated aerodynamic coefficients of two (FLUENT) for the steady-state flow.20) Thrust performance ducted fan models to investigate performance and stability of the ducted fan is measured using the balance system in the in significant flight conditions. open type subsonic wind tunnel. 330 Trans. Japan Soc. Aero. Space Sci. Vol. 56, No. 6 Rotor inlet relative flow angle, β β1 Rotor outlet relative flow angle, 2 Stator inlet absolute flow angle, α α2 Stator outlet absolute flow angle, 3 90 60 30 Flow angles (deg.) Flow 0 0.2 0.4 0.6 0.8 1 r/rtip Fig. 4. Flow angle distributions of the rotor and the stator blades for the design requirements. θ 90 Camber angle, R Stagger angle, ξ } Rotor R Camber angle, θ 75 ξ S Stator Stagger angle, S } 60 45 30 15 Blade shape angles (deg.) 0 0.2 0.4 0.6 0.8 1 r/rtip Fig. 3. Design procedures of the ducted fan. Fig. 5. Blade shape angle distributions for the rotor and the stator blades of the ducted fan. 2.1. Free vortex design method The flow in the rotor blade passage of the ducted fan has no radial velocity component, which is commonly known as fan ¼ Ãrotor þð1 À ÃÞstator ð3Þ the radial equilibrium axisymmetric flow. 2.2. Fan design results The rotor and the stator blades of the ducted fan are Performance characteristics of the ducted fan are designed using a free vortex design condition with the radial estimated for the variation of design parameters based on equilibrium flow assumption.
Details
-
File Typepdf
-
Upload Time-
-
Content LanguagesEnglish
-
Upload UserAnonymous/Not logged-in
-
File Pages9 Page
-
File Size-