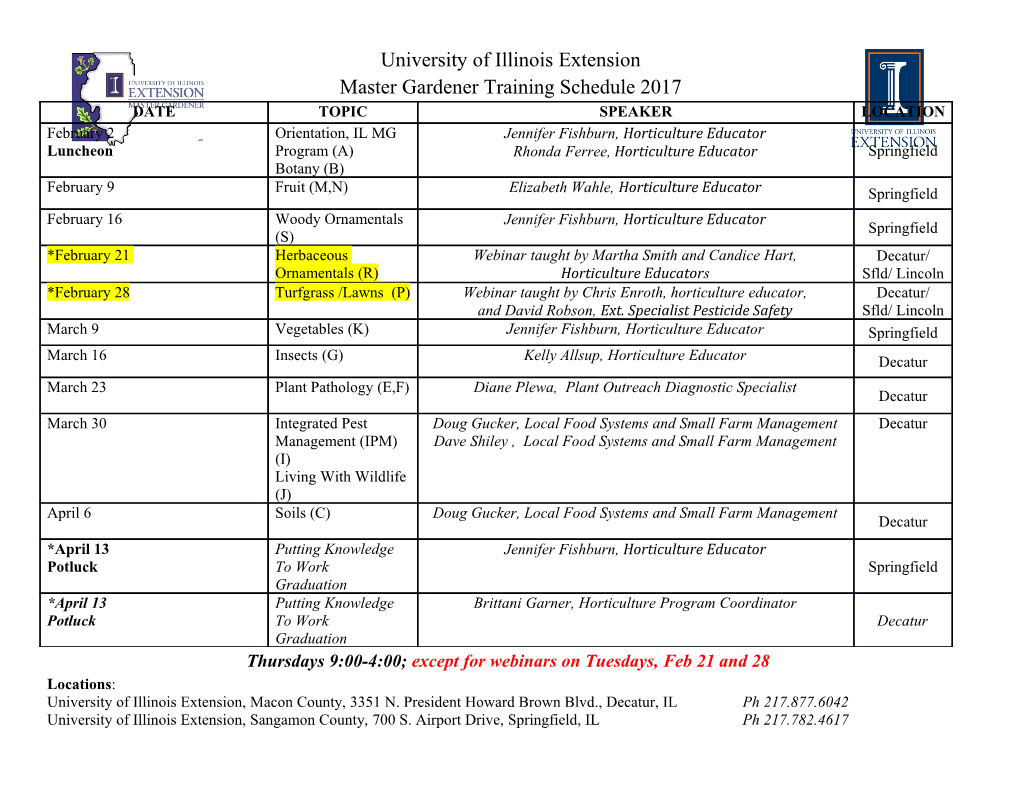
Scientific Bulletin of the Electrical Engineering Faculty – Year 13 No.4 (24) ISSN 1843-6188 IMPLEMENTATION OF ISA S88.01 STANDARD INTO AN AUTOMATED PROCESS G. OPREA Valahia University of Targoviste, Doctoral School of Engineering Science - Electrical Engineering, 35 Stancu Ion Street, 130105, Târgovişte, ROMANIA E-mail: [email protected] Abstract. S88 Batch Control Standard has been developed that causes equipment to do the things necessary to make under the auspices of the ISA (the Instrumentation, Systems, a product – no matter how that control is achieved. and Automation Society) and is the appropriate Standard to Manual control is best or quite appropriate in many apply in many Batch Process Control or Automation projects. cases; automatic control is better in others. S88 works The S88 standard enables clear and concise transfer of with either case, or both. It is based on the premise that information between different disciplines, specifically the Process Engineer and the Automation Engineer. The whether a function is controlled manually or standard breaks down 'process areas' into 'process cells', automatically it is the function that is important. This is 'process units', 'equipment modules' and finally 'phases'. particularly important in modern manufacturing Using these smaller 'blocks' the URS (User Requirement approaches where there is usually the need for smooth Specification), FDS (Functional Design Specification) and integration of manual and automatic control activities. ultimately the final control software, are constructed in a Few plants actually run all night with the lights out and logical 'easy to follow' way. people are a long way from being obsolete. Keywords: process, areas, cells, units, equipment modules, phases. 2. CONTROL PHILOSOPHY AND S88 STRUCTURE 1. INTRODUCTION From the side of the control system the complete plant is The ISA1-88.01-1995 Batch Control standard has had a divided up into single control modules, phases and major impact on the way batch process automation is recipes. With these control modules and phases the done today. It has influenced everything from the way complete plant with all its instrumentation is defined. control systems are built to the way project requirements This structure follows the S88.01 architecture [3]. are written and has simplified and reduced the cost of batch control automation along the way [1]. At any time the state of the complete plant with all the equipment will be visualized on the various PC-screens. S88 defines Recipes, which describe products and how Motors, valves, limit switches will change colours those products are produced. Recipe procedures reside depending on their state. The analogue values are on a PC, while the programming code running the displayed as a number and in a trend. production equipment resides in the PLC (programmable logic controller) or DCS (distributed control system) 2.1 Control modules residing within the equipment [2]. A control module is controlling a single equipment part. When it comes time to make a product, the The available control modules are: valves (On/Off manufacturing requirements defined by the recipe and its valves or proportional valves), motors (fix speed and procedure are linked to the required equipment. The variable speed), analogue sensors (temperature, pressure, recipe phase within the PC batch server communicates flow, weight, etc.), digital sensors (proximity switches, with the equipment phases via a set of protocols held in safety switches, etc.), PID control loop (for temperature, the PC. These protocols define the states the equipment flow, pressure, etc.) and counters (for dosing via flow may function in, e.g. idle, active, pause, stop etc, and the meters) [4]. possible transitions between states. A Phase Logic Interface (PLI) resides in the PLC or DCS system to On the SCADA system each of these control modules enforce these transition protocols and communicate back will be displayed by a corresponding symbol. For each and forth with the PC. The fundamental difference control module a faceplate can be opened for additional between traditional control and control as outlined in information. This faceplate gives also the possibility to S88 is that S88 adds control of procedure and a level of adjust parameters such as monitoring times, PID loop coordination control necessary to keep multiple parameters, thresholds, etc. A service mode for procedures sorted out. The concepts that are spelled out authorised users is available to operate an actor in a in terms of a batch manufacturing environment are service mode or set substitute values for a sensor. consistent regardless of whether the control is provided manually or automatically. It treats control as a function In the next example (Figure 1), is described the specifications of an equipment module control. 16 ISSN 1843-6188 Scientific Bulletin of the Electrical Engineering Faculty – Year 13 No.4 (24) uses the vacuum pump, plus a couple of valves and the pressure transmitter [5]. The phases can be operated in manual and automatic mode. The manual mode can be used for the commissioning of the single phases as well as for trouble shooting. In manual mode the operator is responsible for the entering of the correct set points and for the starting and stopping at the correct time. A production is normally carried out in automatic mode, where the set points for the phases and the sequencing are specified in the control recipes. Some of the mentioned phases are static, meaning that they need to be switched off. In this case the start and a stop phase are available. Other phases are non static; they switch off automatically after e.g. having dosed the required quantity. Common to all phases is that the phase will be paused when a control module of an equipment part which is used by the phase has created an error. E.g. a valve does not reach the requested position, motor trips out, fault on a sensor, etc. A phase in pause will automatically deactivate all equipment parts which are used by this phase. Meaning the valves will be closed and the motors will stop. A paused phase may also pause another phase. This is the case, when the running signal from one phase is one of the permissive for another phase. 2.3 Phase control panels Phase control panels are boxes with the phase reference number followed by the phase description. They are the operational steps through which the production process goes. P100 P100 P100 P100 Heating Heating Heating Heating loop loop loop loop Figure 2. Sample phase control panels The panels will change color, (Figure 2) depending on the status of the phase it refers to: Figure 1. Equipment module control specifications - Clear Phase not active; - Green Phase active; Inputs are indicated in a prescribed format on top of the - Salmon Phase currently paused; picture, outputs are shown on the bottom and in the - Red Phase stopped – either in alarm or by operator central part the processing which is necessary is action. described. Any other equipment module control should be described in the same manner. By selecting the phase control panel a pop-up (Figure 3) will appear on screen which contains all the relevant data 2.2 Phases for that phase. It also contains the manual operator control soft buttons for that phase. The information and A phase is a combination of some of the control available functions within a phase control panel vary modules, which has to be operated together to achieve a from phase to phase. In the phase control panel pop-up specified result. The phase pressure control for example section all available parameters are listed. The section is split into to 3 parts: 17 Scientific Bulletin of the Electrical Engineering Faculty – Year 13 No.4 (24) ISSN 1843-6188 - Set points: These parameters, such as the required pressure or temperature are typically changed more frequently. They can be used in a recipe at different stages of the batch with different values. If a phase is running in manual mode the set points for the manual mode will be used. If a phase is running in automatic mode, the set points from the recipe will be used. - Plant specific data: These parameters cannot be changed from recipe to recipe. The parameters can only be changed by persons Figure 4. Phases flow chart with a special access level. For each of the 3 main process steps, process 1, process - Actual values: 2 and process 3, individual control recipes are defined. These parameters cannot be changed; they display the These recipes contain all the required information to actual values for different variables. control the process. This includes times, speeds, product ingredients, temperatures, weights and so on. The control system will handle the download of the correct control recipes according to the master recipe at the right time into the several process units. 2.6 Master recipes A master recipe contains the control recipes for the different process steps. For each final product a master recipes needs to be defined. To start a production of a specified product the corresponding master recipe has to be loaded. The system then will download the correlated control recipes for the 3 process steps into the different process units. 3. PLANT CONTROL SYSTEM AND OPERATOR INTERFACE S88 defines hierarchical recipe management and process segmentation frameworks, which separate products from the processes that make them. The standard enables re- Figure 3. Phase control panel pop-up and ,,actual” popup use and flexibility of equipment and software and provides a structure for coordinating and integrating 2.4 Transition condition recipe-related information across the traditional ERP, MES and control domains. In case the plant is operated in automatic mode by running a recipe, the system steps on to the next phase in The control system downloads the control recipes at the the sequence when this transition condition for the required time according to a master recipe.
Details
-
File Typepdf
-
Upload Time-
-
Content LanguagesEnglish
-
Upload UserAnonymous/Not logged-in
-
File Pages5 Page
-
File Size-