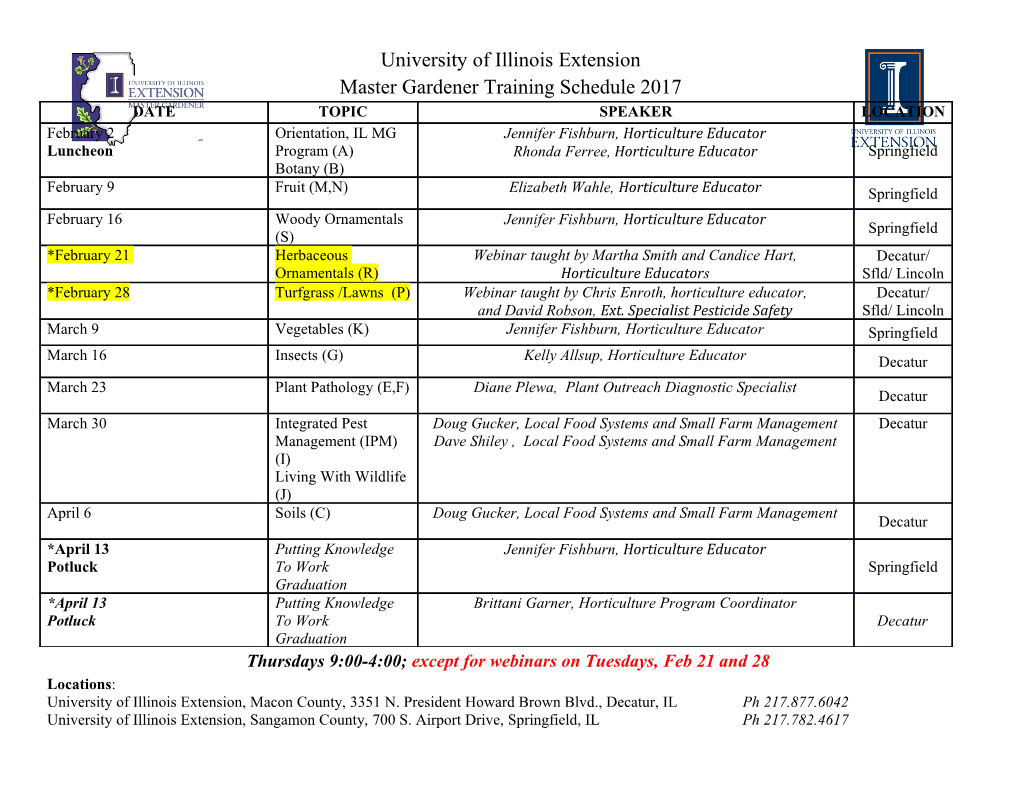
VIVAK® sheet Technical guide fabricating, forming, finishing VIVAK® sheet Superior performance and versatility Fabricating VIVAK copolyester is a highly versatile PETG plastic that offers CONTENTS SAWING BAND SAWS a unique balance of physical properties and ease in fabrication. A circular blade with carbide-tipped teeth utilizing the “triple-chip” Band saws are useful for trimming formed parts or irregular The high impact strength and durability of VIVAK allow for Fabricating Page tooth design is the preferred method of cutting VIVAK® sheet. shapes. Band saws should be run at 2,000 feet per minute and thinner gauges and higher rates of production through a variety Table or overhead saws can be used successfully. have between 3-15 teeth per inch. Coarser (larger tooth) blades of fabrication techniques, including die cutting, punching, and Sawing . 3 perform better with thicker gauge plastic. Because vibration can low-temperature forming. Routing . 4 CIRCULAR SAWS induce cracking of VIVAK sheet, proper support of the part to be VIVAK sheet offers deep draws, complex die cuts, and precise Shearing, blanking, punching . 4 trimmed is important. If the cut edge is not smooth, cracks will Circular saws should be run at relatively high speeds in the range molded-in details without sacrificing structural integrity. It can be Laser cutting . 4 propagate from erose or notched edges. of 8,000-12,000 linear feet per minute. Blades should have 3-5 bonded or fastened with adhesives, tapes, ultrasonic welding, Die cutting . 4 or rivets. VIVAK is manufactured with a resin that complies with teeth per inch. As a general rule, thicker gauge sheet requires Note: Always use proper eye protection when sawing. Drilling . 5 FDA requirements for food contact, and is available in a thickness fewer teeth per inch. A circular saw is preferable to a band saw range from .020" to .500". It is available in a wide range of sheet Milling . 5 for straight cuts, because a smoother cut can be achieved. When sizes, colors, and finishing options. sawing thin gauge sheet, it is important to have a good supporting Forming edge on the saw table with minimal gap between the saw blade Features and benefits: Brake forming and cold bending . 6 and table edge. When stack cutting, it is a good idea to clamp the • Complex die cutting Strip heating . 6 top surface to prevent vibration. Be sure tabletops are smooth and free of projections that might scratch or mar the VIVAK. • Down gauging Thermoforming . 7 • Riveting Forming equipment . 7 Sawing recommendations • Punching Heaters . 7 • Superior impact strength Molds . .8 Type of cut Tool Blade type Blade parameters Blade speed • Design flexibility Mold design . 8 Straight cut Circular saw Triple-chip 7-1/4"dia., 40 teeth (carbide-tipped cutoff) 4,500 rpm • Cold forming Heating cycle . .9 design 7-1/4" dia., 200 teeth plywood blade Shading or screening . 9 Curved cut Saber or jigsaw Finish cutting 7 teeth per inch Drape and cylindrical forming . 10 blade Free drawn vacuum dome forming . 11 Curved cut Band saw 1/2" 3 teeth per inch 2,000 ft/min Free blown billow forming of dome . 11 Trimming & Router Carbide-tipped 3/8" dia. 20,000 rpm Registration forming . 11 deflanging or high-speed steel, double fluted Bonding/Fastening Solvent bonding . 12 Circular saw troubleshooting Band saw troubleshooting Transfer tape bonding . 12 Welding . 12 Problem: Melting or gummed edges Problem: Melting or gummed edges Mechanical fastening . 12 Suggested 1. Increase blade tooth size Suggested 1. Increase tooth size solutions: 2. Reduce saw speed solutions: 2. Reduce saw speed Finishing 3. Provide better clamping and/or 3. Use air to cool blade Sanding . 13 support for material 4. Check blade sharpness 4. Use air to cool blade Jointing-planing . 13 Problem: Chipping 5. Reduce feed rate Flame polishing . 13 6. Inspect blade for sharpness Suggested 1. Decrease tooth size solutions: 2. Slow down stock feed rate Solvent polishing . 13 Chipping Problem: 3. Provide better clamping and/or Hot stamping . 13 Suggested 1. Decrease blade tooth size support to eliminate vibration Screen printing . 13 solutions: 2. Increase saw speed 4. Check blade sharpness 3. Increase feed rate Performance/Performance comparison 4. Inspect blade for sharpness Physical properties . 14 5. Check blade and arbor for wobble Comparison . 14 6. Check blade fence alignment Chemical Resistance . 15 Visit Plaskolite.com/Fabrication/VIVAK/Vendors 2 3 VIVAK® sheet Superior performance and versatility Fabricating VIVAK copolyester is a highly versatile PETG plastic that offers CONTENTS SAWING BAND SAWS a unique balance of physical properties and ease in fabrication. A circular blade with carbide-tipped teeth utilizing the “triple-chip” Band saws are useful for trimming formed parts or irregular The high impact strength and durability of VIVAK allow for Fabricating Page tooth design is the preferred method of cutting VIVAK® sheet. shapes. Band saws should be run at 2,000 feet per minute and thinner gauges and higher rates of production through a variety Table or overhead saws can be used successfully. have between 3-15 teeth per inch. Coarser (larger tooth) blades of fabrication techniques, including die cutting, punching, and Sawing . 3 perform better with thicker gauge plastic. Because vibration can low-temperature forming. Routing . 4 CIRCULAR SAWS induce cracking of VIVAK sheet, proper support of the part to be VIVAK sheet offers deep draws, complex die cuts, and precise Shearing, blanking, punching . 4 trimmed is important. If the cut edge is not smooth, cracks will Circular saws should be run at relatively high speeds in the range molded-in details without sacrificing structural integrity. It can be Laser cutting . 4 propagate from erose or notched edges. of 8,000-12,000 linear feet per minute. Blades should have 3-5 bonded or fastened with adhesives, tapes, ultrasonic welding, Die cutting . 4 or rivets. VIVAK is manufactured with a resin that complies with teeth per inch. As a general rule, thicker gauge sheet requires Note: Always use proper eye protection when sawing. Drilling . 5 FDA requirements for food contact, and is available in a thickness fewer teeth per inch. A circular saw is preferable to a band saw range from .020" to .500". It is available in a wide range of sheet Milling . 5 for straight cuts, because a smoother cut can be achieved. When sizes, colors, and finishing options. sawing thin gauge sheet, it is important to have a good supporting Forming edge on the saw table with minimal gap between the saw blade Features and benefits: Brake forming and cold bending . 6 and table edge. When stack cutting, it is a good idea to clamp the • Complex die cutting Strip heating . 6 top surface to prevent vibration. Be sure tabletops are smooth and free of projections that might scratch or mar the VIVAK. • Down gauging Thermoforming . 7 • Riveting Forming equipment . 7 Sawing recommendations • Punching Heaters . 7 • Superior impact strength Molds . .8 Type of cut Tool Blade type Blade parameters Blade speed • Design flexibility Mold design . 8 Straight cut Circular saw Triple-chip 7-1/4"dia., 40 teeth (carbide-tipped cutoff) 4,500 rpm • Cold forming Heating cycle . .9 design 7-1/4" dia., 200 teeth plywood blade Shading or screening . 9 Curved cut Saber or jigsaw Finish cutting 7 teeth per inch Drape and cylindrical forming . 10 blade Free drawn vacuum dome forming . 11 Curved cut Band saw 1/2" 3 teeth per inch 2,000 ft/min Free blown billow forming of dome . 11 Trimming & Router Carbide-tipped 3/8" dia. 20,000 rpm Registration forming . 11 deflanging or high-speed steel, double fluted Bonding/Fastening Solvent bonding . 12 Circular saw troubleshooting Band saw troubleshooting Transfer tape bonding . 12 Welding . 12 Problem: Melting or gummed edges Problem: Melting or gummed edges Mechanical fastening . 12 Suggested 1. Increase blade tooth size Suggested 1. Increase tooth size solutions: 2. Reduce saw speed solutions: 2. Reduce saw speed Finishing 3. Provide better clamping and/or 3. Use air to cool blade Sanding . 13 support for material 4. Check blade sharpness 4. Use air to cool blade Jointing-planing . 13 Problem: Chipping 5. Reduce feed rate Flame polishing . 13 6. Inspect blade for sharpness Suggested 1. Decrease tooth size solutions: 2. Slow down stock feed rate Solvent polishing . 13 Chipping Problem: 3. Provide better clamping and/or Hot stamping . 13 Suggested 1. Decrease blade tooth size support to eliminate vibration Screen printing . 13 solutions: 2. Increase saw speed 4. Check blade sharpness 3. Increase feed rate Performance/Performance comparison 4. Inspect blade for sharpness Physical properties . 14 5. Check blade and arbor for wobble Comparison . 14 6. Check blade fence alignment Chemical Resistance . 15 Visit Plaskolite.com/Fabrication/VIVAK/Vendors 2 3 Fabricating continued Routing Die cutting Drilling Routing produces a smooth edge on VIVAK® sheet and can be VIVAK sheet in gauges up to .100" can be die cut using steel 20" Drills specifically designed for plastics are recommended. employed to cut curved or irregular shapes. Routers with a speed rule or matched metal dies. Steel rule dies are the most common Standard twist drills for metal or wood can also be useful. of 20,000 to 25,000 rpm are preferred. Use straight fluted carbide- type, and double bevel blades provide adequate edges for most VIVAK® sheet is easily drilled using zero-degree rake angle bits tipped router bits. High-speed steel bits may also be used. Bits applications. If improved edge finish is required, try the flush type with dubbed off cutting edges. Regulate pressure and speed until should be 3/8" to 1/2" diameter for best results. Portable routers, of blade. Under normal conditions, 3 point (.042") thick blades a continuous spiraling chip is observed.
Details
-
File Typepdf
-
Upload Time-
-
Content LanguagesEnglish
-
Upload UserAnonymous/Not logged-in
-
File Pages16 Page
-
File Size-