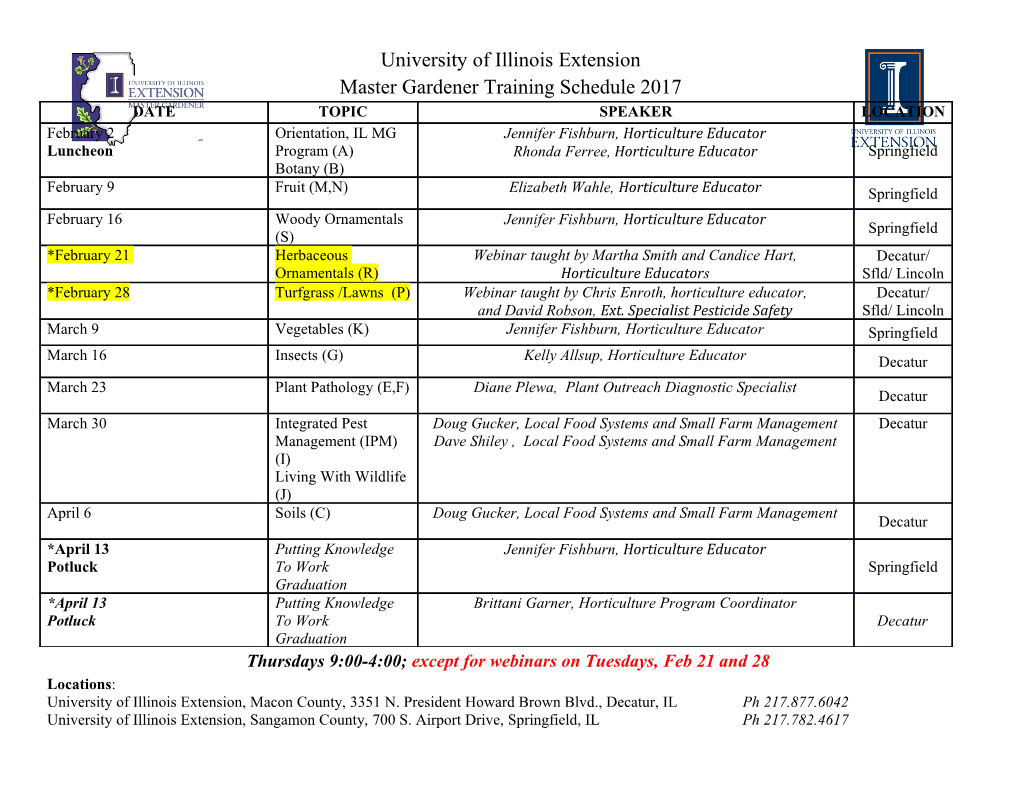
Proprietary process technology S-SBR Solution Styrene-Butadiene Rubber copolymers Versalis proprietary process technologies available for licensing II 1 Our company Our commitment to excellence, in quality of our Versalis – the petrochemical subsidiary of Eni – is products and services, makes our company an active a dynamic player in its industry sector facing the partner for the growth of customers involved in multifold market needs through different skills. petrochemical business. With a history as European manufacturer with more Through engineering services, technical assistance, than 50 years of operating experience, Versalis stands marketing support and continuous innovation, our as a complete, reliable and now global supplier in the knowledge is the key strength to customize any new basic chemicals, intermediates, plastics and elastomers project throughout all phases. market with a widespread sales network. Customers can rely on this strong service-oriented Relying on continuous development in its production outlook and benefit from a product portfolio that plants as well as in its products, strengthening the strikes a perfect balance of processability and management of the knowledge gained through its long mechanical properties, performance and industrial experience, Versalis has become a worldwide eco-friendliness. licensor of its proprietary technologies and proprietary catalysts. The strong integration between R&D, Technology and Engineering departments, as well as a deep market expertise, are the key strengths for finding answers to customers requirements. Introduction to Versalis solution SBR technology Solution polymerized styrene-butadiene rubber Versalis can always provide appropriate solutions to Versalis S-SBR technology allows to provide with Industrial applications is the unrivalled raw material for highly specified different client’s needs thanks to its capabilities and a single line a fairly broad range of economically First production line was built in Grangemouth (UK) in tyre components used in the fabrication of high experience in the following fields: feasible capacities: up to 65 kt/y per reaction unit, up 1995, based on batch process technology and having a performance tyres, where the lowest fuel consumption to 40 Kt/y per finishing line (batch grades), up to 45 capacity of 30 kt/y, followed in 1999 by a new reaction and the highest durability are required. Research & Development kt/y per finishing line (continuous grades). section based on continuous polymerization process The wide product portfolio allowed by the Versalis The presence of a strong R&D team, established in technology. technology can be then used for fabrication of special Ravenna since the early 70s, qualifies Versalis as Wastes and emissions A third unit, based on 100 kt/y capacity with tyre threads showing enhanced wet grip performance, an outstanding owner of know-how in the field of The process produces oily waste water which continuous and batch polymerization lines, has been as well as for fabrication of winter tyres and special elastomers. Reliable and updated facilities (pilot plants, can be treated in a normal bio-treatment. Large licensed in the Far East and is on stream since 2009. mechanical goods. Depending on desired product synthesis and analytical labs, equipment for elastomer waste air emissions from finishing require only a Two further plants in the Far East are on stream since and application, batch and continuous polymerization processing), allow Versalis to continuously up-to-date scrubbing process (dedusting). Some selected exhaust 2017 (a batch one with a capacity of 40 kt/y and a process are available in Versalis solution SBR the technology in order to support the elastomers streams from finishing section are usually sent to a continuous one with a capacity of 60 kt/y). 2 technology. S-SBR proprietary technology has been business in a very competitive and demanding market regenerative-type thermal oxidizer (ISBL) in order to Another plant, based on batch technology (60 kt/y) 3 developed as an alternative to emulsion technology scenario. Additional services are then available for minimize the environmental impact of the process. has been licensed in Middle East and is currently to produce new product grades and also to greatly potential Licensees, such as technical assistance, Normal process venting are collected and can be sent under construction. reduce some environmental impact of the emulsion training, development of analytical methods, site to flare or other OSBL systems. technology. assistance for start-up and follow up, development of tailor made products on demand. Main technology highlights are: large production flexibility due to availability Process design & operational experience of both batch and continuous polymerization Process design is flexible and able to face different technologies, whose selection is driven by the final conditions and constraints. Any project is individually application of the product; evaluated to offer the best solution, tailored to specific cyclopentane, cyclohexane or n-Hexane or blend customers needs. Thermal and fluodynamic analysis highly compatible with all different polymer (CFD) can be applied to the design of key equipment compositions, can be used as solvent depending on such as reactors, agitators and strippers. local climate conditions; The design takes also advantage of the Versalis high and medium vinyl grades as well as Dry and long-term manufacturing experience. Oil Extended polymers are allowed; New technological solutions are first tested in production of polymers with linear radial or production plants and the acquired experience branched different macrostructures; transferred to the licensed technology, in order to Main process parameters process design advanced features in reach not only the best process performances, but also polymerization and purification sections; a safe and reliable plant arrangement. per MT of S-SBR small quantity of volatile organic compounds Raw Materials (Butadiene, Styrene, Aromatic Oil) 1,003 kg (solvent) entering finishing section (low release Mechanical design during extrusion); Versalis Engineering Dept. has been working in close Electricity - Continuous Process 0.5 MWh optimized configuration of the stripping section coordination with the Process Dept. since a long time. with three stages arrangement to minimize steam This fact has allowed to develop unique and well Electricity - Batch Process 0.6 MWh consumption without impacting emissions of voc. sound engineering solutions for critical equipment, Steam (Medium Pressure + Low Pressure(1)) 5 MT that guarantee the best results in terms of mechanical reliability and process performances. (1) 10 barg and 6 barg respectively. Expected consumption related to standard Plant configuration, solvent Cyclopentane, mild site climate, air cooling applied where possible. The Europrene® S-SBR Process copolymers product portfolio description The Versalis S-SBR technology enables the production The tyre main applications of Versalis S-SBR grades Solution polymerized styrene-butadiene rubber is grades to be produced. Reaction temperature control of many grades of Dry and Oil Extended polymers are: obtained by anionic copolymerization of styrene is enabled by the use of boiling reactor while the using through batch or continuous polymerization. Tuning silica based compound for H/V tread; and butadiene initiated by lithium alkyls in paraffine of proper randomizing agent ensures a complete the polymer composition (% of styrene) and polymer ultra High performance tyre tread; or cycloaliphatic solvent; due to the large difference randomness of styrene with the desired level of vinyl microstructure (% of vinyl group) is possible to obtain silica based compound for H/V tread winter. of reactivity ratios for the two monomers, addition unit. products, in the field of tyre application, characterized of a living chain-end modifier changing the The polymerization conditions lead to a practically by: Such portfolio of products is continuously improved by above-mentioned reactivities is required to obtain complete depletion of monomers; at the end of good processability; our R&D centers through tyre manufacturers feedback. a well randomized copolymer. polymerization the living chain ends are terminated good ice/snow grip; All polymer grades are stabilized with a specifically by addition of substances which modify the polymer good rolling resistance; designed antioxidant package. The rubber macrostructure can be efficiently structure; so radial or branched or linear rubber can grades with optimum compromise between rolling managed/driven by a proper selection of be obtained in order to match the required properties. resistance and grip. polymerization type (batch, continuous), reaction After polymerization completion the solution is then 4 conditions and suitable coupling or branching pumped to a blend tank operating at slight pressure. 5 agents, greatly enhancing the final properties of Residual traces of unconverted monomers, together vulcanized rubber. It is worth to note that the long with a portion of the solvent, are flash vaporised, chain branching, due to radical reactions forming high condensed and then recycled to the wet solvent tank, molecular weight arms, is a competitive advantage while the concentrated polymer solution is blended in of Versalis technology. The elastic properties of the the blend tanks. uncured rubber are then greatly modified, allowing an The blended solution with the antioxidant agents is
Details
-
File Typepdf
-
Upload Time-
-
Content LanguagesEnglish
-
Upload UserAnonymous/Not logged-in
-
File Pages7 Page
-
File Size-