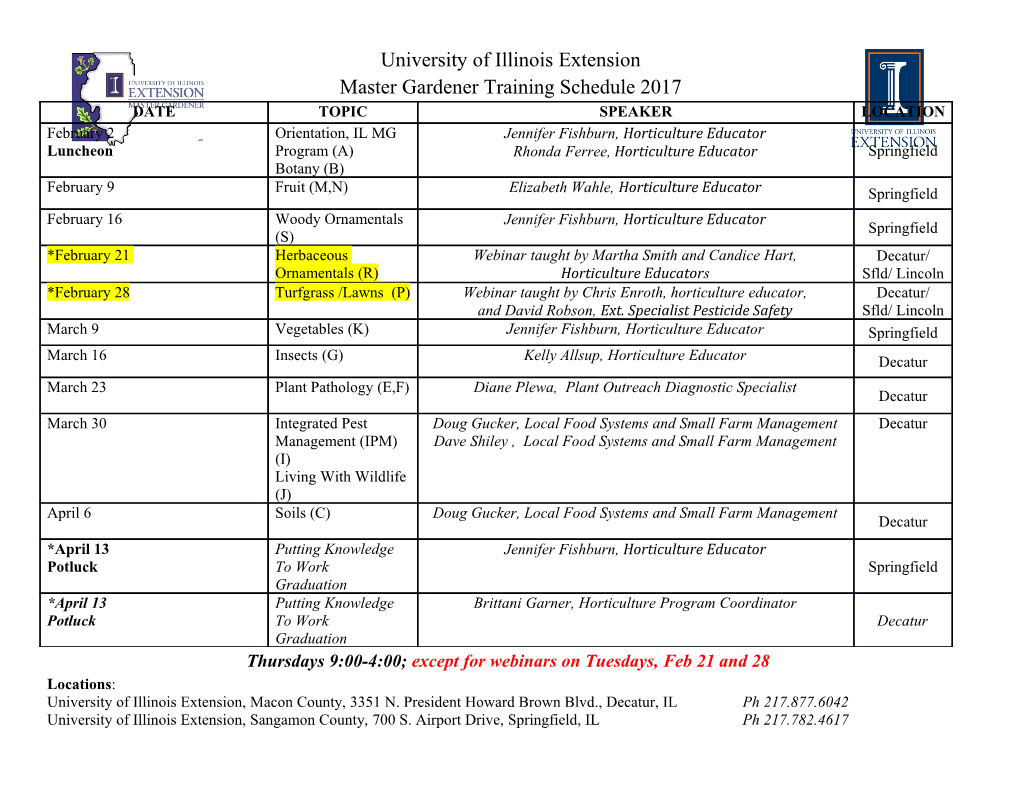
l L> M V iD L D L A Lr C n ~ tnl ~ ta TKSTING. LABORATORIES. Enyln ~ ~ ra ivi ~ tallur y I ate 1 Xl C ~ 2%0 Seventh Blvd. ~ St. Loula, Mlaaouri 53104 31'/771-7111 I.T.L. REPORT NO. 87-5-77 ONE HOUR FIRE ENDURANCE TEST CONDUCTED ON A LADDER CABLE TRAY WITH h P-1000 UNISTRUT ATTACHMENT PROTECTED PITH THE THERMO-LAG 330 FIRE BARRIER SYSTEM DATE OF ISSUE: 26 JUNE 1987 REVISION I: 29 JUNE 1987 +502070099 870y07 PDR ADOCK 05000397 PDR I N DUSTRI A I~ TESTINO LABORATORIES I no. I.T.L. REPORT NO. 87 5-77 ONE HOUR FIRE ENDURANCE TEST CONDUCTED ON h ihDDER CABlZ TRAY PITH h P-1000 UNISTRUT ATTACHMENT PROTECTED WITH THE THERMO-LAG 330 FIRE BARRIER SYSTEM TEST DATE: 7 MAY 1987 TEST LOCATION: THERMAL SCIENCE, CASSENS DRIVEIN'200 ST. LOUIS, MISSOURI 63026 hPPROVED BY: INDUSTRIAL TESTING LABORATORIES, INC» 2350 SEVENTH BQ)LEVARD ST+ LOUIS~ MISSOURI 63104 hLLAN M. SIEGEL, P.E. DIRECTOR DATE OF ISSUE: 26 JUNE 1987 REVISION I: 29 JUNE 1987 In no event shall Industrial Testing Laboratories, Inc. be responsible to anyone for vhatever use or nonuse is made of the information contained in this Report and in no event shall Industrial Testing Laboratories, Inc., its employees, or its agents incur any obligation or liability for damages including, but not limited to, consequential damages, arising out of or in connection vith the use, or inability to use, the information contained in this Report. I T.L. REPORT NO. 87-5-77 TABLE OF CONTENTS SECTION TITLE PAGE NO ~ leO INTRODUCTION AND SUMMARY 1.1 Introduction 1 2 Summary 2 0 PURPOSE 3 0 TEST LOCATION 4 0 TEST PLAN STANDARDS AND REFERENCES 3 4 1 ASTM E119 Fire Endurance Test 4 2 Mater Hose Stream Test 4 ~ 3 Electrical Circuit Integrity Monitoring 5 0 DESCRIPTION OF TSI'S HIGH TEMPERATURE TEST FURNACE 5 1 Transfer Cart 6.0 TEST ASSEMBLY 13 6 1 Cable Installation 13 6.2 Opening Sealant 13 I.ToL. REPORT NO. 87-5-77 TABLE OF CONTENTS CONTINUED SECTION TET1Z PAGE NO. 7.0 FIRE BARRIER SYSTEM 15 8.0 TEST MATERIALS 17 8 1 THERMO-LAG Stress Sld.n Type 330-69 17 8.2 THERMO-LAG 330-1 Subliming Material 17 8.3 THERMO-LAG 330 Prefabricated Panels 17 9.0 TEST INSTRUMENTATION 17 10. 0 THERMOCOUPLES 18 10 1 High Temperature Test Furnace Thermocouples 18 10. 2 Test Assembly Thermocouples 18 11 0 TEST OBSERVATIONS 20 11. 1 Details of the One Hour Fire Endurance Test 20 ll.2 Details of the Water Hose Stream Test 20 11. 3 Details oi The Electrical Circuit Integrity Monitoring 21 12. 0 TEST RESULTS 23 I.T.L. REPORT NO. 87-5-77 TABlE OF CONTENTS LIST OF FIGURES PAGE NO ASTM E119 TEST METHOD TIME/ TEMPERATURE RELATIONSHIP FOR ONE HOUR FIRE ENDURANCE TEST CABLE INTEGRITY MONITORING CIRCUITS PHOTOGRAPH OF THE EIGHTWHANNEL EVENT RECORDER AND THE MULTI-LIGHT DISPLAY PANEL TSI 'S HIGH TEMPERATURE TEST FURNACE 10 GENERAL AMULNGEMENT OF A TEST ARTICLE IN THE TEST FURNACE 12 GENERAL ARRANGEMEhT OF CABLES Ih CABLE TRAY 14 SCHEMATIC DRY'ING OF THE THERMO-LAG 330 FIRE BARRIER PROTECTED TEST. ASS&1BLY 16 LOCATION OF THERMOCOUPLES 19 I i I.T.L. REPORT NO ~ 87-5-77 TABLE OF CONTENTS LIST OF FIGlJRES SECTION TITLE PAGE NO. THERMAL GRADIENT IN UNISTRUT ATTACHMENT AFTER ONE HOUR ASTM E119 FIRE EXPOSURE 24 10 AVERAGE AND MAXIMUM OF ALL CABLE SURFACE TEMPERATURES RECORDED WITHIN THE CABLE TRAY DURING THE ONE HOUR FIRE ENDURANCE TEST 27 P-1000 UNISTRUT SURFACE TEMPERATURES RECORlKD DURING THE ONE HOUR FIRE ENDURANCE TEST 29 12 COMPARISON OF THE ASTM E119 TEST METHOD TIME/TEMPERATURE CURVE PITH THE ACTUAL RANGE OF TEMPERATURES RECORDED DURING THE ONE HOUR FIRE ENDURANCE TEST 30 I.T.L. REPORT NO+ 87-5-77 TABIZ OF CONTENTS LIST OF TABLES TABLE NO ~ TITLE PAGE NO. THERMOCOUPLE CHANNEL ASSIGNMENT FOR MONITORING ELECTRICAL CIRCUIT INTEGRITY MITHIN THE TEST ASSEMBLY 22 AVERAGE AND MAXIMUM OF ALL CABLE SURFACE TEMPERATURES RECORDED WITHIN THE CABLE TRAY DURING THE ONE HOUR FIRE ENDURANCE TEST 26 P-1000 UNISTRUT SURFACE TEMPERATURES, RECORDED DURING THE ONE HOUR FIRE ENDURANCE TEST 28 INDUSTRIAL TESTI N G LABORATORIES I n c. I. T. L. REPORT NO. 87-5-77 ONE, HOUR FIRE ENDURANCE TEST CONDUCTED ON A CABLE TRAY WITH A P1000 UNISTRUT ATTACHMENT PROTECTED WITH THE THERMO-LAG 330 FIRE BARRIER SYSTEM 1. 0 . INTRODUCTION AND STPBIARY 1.1 Introduction This report presents the results obtained from performing a one hour ASTM E119 type fire endurance test, followed by a ~ster hose stream test, on a modified ladder cable tray test assembly, protected with a 0.500 inch minimum thickness of the THERMO-LAG 330 Fire Barrier System. The test assembly consisted of a 12" x 4" ladder cable tray modified to include a 21-3/4" long L-shaped P1000 unistrut section welded to one side of the cable tray. The P1000 unistrut section, commencing at the point of attachment to the cable tray and measuring around the exterior of the attachment, was protected with a 0.500 inch minimum dry film thickness of THERMO-LAG Prefabricated Panels. Four (4) thermocouples were mounted one inch outside the protected section in order to monitor the temperature along a nine (9) inch length of the unistrut. The cable tray was also enclosed with a 0.500 inch minimum dry film thickness THERMO-LAG Prefabricated Panel fire barrier. The panels were fastened to the tray by 0.5" by 0.'020" minimum stainless steel banding material, installed alternately at a maximum of 12 inch intervals. A total of 42 generic power and instrumentation cables were installed in the cable tray test assembly. In addition, a flared transition design vas installed on the upper leg of the cable tray at its )unction vith the penetration through the concrete slab, and a caulked-in flared transition design vas installed on the lover leg at its penetration through the concrete slab. The fire test vas conducted in accordance vith the applicable sections of the American Nuclear Insurers Bulletin 15(79), "ANI/MAERP Standard Fire Endurance Test Method to Qualify a Protective Envelope for Class lE Electrical Circuits". All of the materials comprising the THERMO-LAC 330 Fire Barrier System vere manufactured and applied in accordnace vith all applicable sections of Thermal Science's ("TSI") Nuclear Quality Assurance Program Manual/Quality Control Operating Procedures Manual, vhich has been previously accepted by the American Nuclear Insurers- The design configuration used in this test program is described in Section 7.0 of this test report. 1.2 Suanaary Based on the results and observations of this test: (1 ) The test assembly, as described in Section 1.1, vas exposed to the standard time/temperature environment of ASTM E119 for 60 minutes, folloved by a 2 1/2 minute minimum vater hose stream test. Folloving the test, the pover, control, and instrumentation cables vere tested and foun'd to function vith no loss oi circuit integrity (2) The recorded cable surface temperatures in the cable tray section of the test assembly during exposure to the 60 minute fire endurance test did not exceed: A. Average Cable Surface Temperature 133.5F B'aximum Individual Cable Surface Temperature 165 'F (3) The thermal gradient over the nine inch distance vithin the P- 1000 unistrut section after 60 minutes exposure to the fire endurance test vas as follovs: TC/l;o.'ocation Temperature(F) 25 2 3/4" to right of Cable Tray 119- 9 26 1 3/4" from front of Vnistrut 371. 2 27 3 3/4" from front of Vnistrut 498. 3 28 5 3/4" from front of Vnistrut 615. 5 29 7 3/4" from front of Vnistrut 846-8 ~, ~ il 0 These findings show that a P-1000 unietrut section protected a 0.500 inch minimum thickness Prefabricated Panel fire barrier and extending nine (9) inches, as measured from its interface with the outer periphery of the fire barrier, limited the surface temperature at the ad)oining section of the unistrut to the cable tray to 119.9F. (4) The P1000 unistrut, vhen protected with a 0.500 inch minimum dry film thickness Prefabricated Panel, along a span of nine (9) inches as measured into the fire xone from the point of penetration through the fire barrier did not degrade the. electrical integrity of the protected assembly. (5) The transition sections, installed at the )unction of the upper and lower legs of the cable tray and concrete access slab of the test furnace, functioned successfully as evidenced by the relative uniformity of temperature measurements .at all locations in the test assembly and by the fact that they did not allow the penetration of smoke, flames, and water into the test assembly. These recorded temperatures vere below the 325F maximum established for the cable surface temperatures by )urisdictional authorities. 2. 0 PURPOSE The purpose of this test vas to: 1) Demonstrate that the fire barrier design tested herein meets the applicable performance criteria of ANI;s Bulletin 85(79) and the 325F cable surface limitation imposed by Jurisdictional authorities. 2) Demonstrate by test that a P1000 unistrut, when protected with a 0.500 inch nominal thickness of the TkK1RO-LAG Prefabricated Panel, along a span of 9 inches as measured into the fire xone from the point of penetration through the fire barrier, vill not degrade the electrical integrity of the protected assembly. 3 ' TEST LOCATION The test vas conducted on 7 May 1987 at the laboratory facilities of TSI in St.
Details
-
File Typepdf
-
Upload Time-
-
Content LanguagesEnglish
-
Upload UserAnonymous/Not logged-in
-
File Pages422 Page
-
File Size-