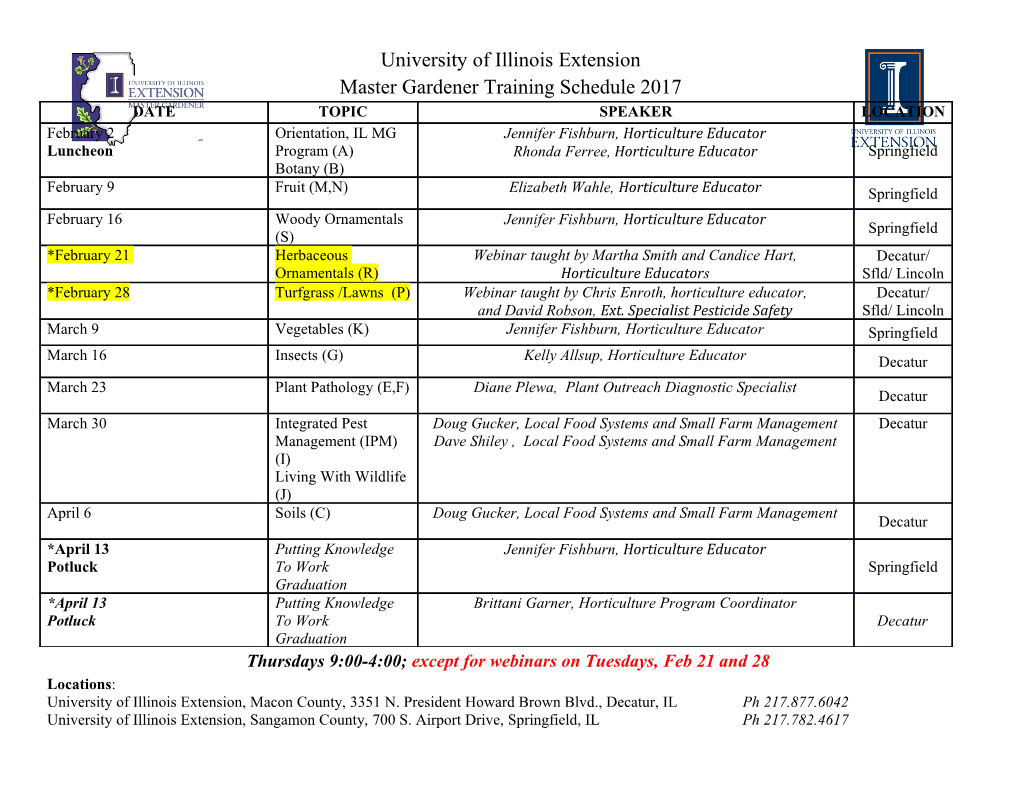
THE AMERICAN SOCIETY OF MECHANICAL ENGINEERS 345 E. 47th St., New York, N.Y. 10017 The Society shall not be responsible for statements or opinions advanced in papers or discussion at meetings of the Society or of its Divisions or Sections, 94-01-434 or printed In its publications. Discussion is ptintod only if the paper is pub- lished in an ASME Journal. Papers are available from ASME for 15 months after the meeting. Printed in U.S.A. Copyright © 1994 by ASME MEDWAY: A HIGH-EFFICIENCY COMBINED CYCLE POWER PLANT DESIGN Downloaded from http://asmedigitalcollection.asme.org/GT/proceedings-pdf/GT1994/78866/V004T10A019/2405123/v004t10a019-94-gt-434.pdf by guest on 25 September 2021 Darrell M. Leis Black & Veatch Kansas City, Missouri . Michael J. Boss and Matthew P. Me!sett GE Industrial and Power Systems Schenectady, New York 111111111111,U1111111111 ABSTRACT The Medway Project is a 660 MW combined cycle In April 1992, Medway Power Limited (MPL) power plant which employs two of the world's largest awarded an engineering, procurement, and construction advanced technology MS9001FA combustion turbine contract for the plant to a consortium of Europower generators and an advanced design reheat steam turbine Development Ltd. and TBV Power Ltd. The consortium generator in a power plant system designed for high is providing a turnkey nominal 660 MW gas fired reliability and efficiency. This paper discusses the power combined cycle plant. Europower, Marubeni plant system optimization and design, including Corporation's European branch, is providing the turbines. thermodynamic cycle selection, equipment arrangement, TBV Power is providing the balance of the plant using its and system operation. The design of the MS9031.FA joint venture partners, Tarmac Construction Ltd. for civil combustion turbine generator and the steam turbine construction and Black & Veatch International for generator, including tailoring for the specific application engineering and procurement. The mechanical and conditions, is discussed. electrical erection packages are being executed by European Community contractors. MPL has separate contracts for the switchyard with the National Grid MEDWAY'S OBJECTIVE—HIGH EFFICIENCY Company and for fuel gas with British Gas. The Medway Power Station, a 660 MW combined cycle power plant about 44 miles/70 km east of London, is a rust of its kind in the United Kingdom. The plant is FACTORS INFLUENCING SELECTION OF THE the first to install two General Electric (GE) 9FA COMBINED CYCLE advanced technology combustion turbines coupled to two MPL chose a gas fueled combustion turbine triple pressure reheat natural circulation heat recovery combined cycle plant because of the economic advantage steam generators (HRSGs) which feed steam to a reheat of the highly efficient advanced technology over the steam turbine. alternative solid fuel plant options. This selection was The combustion turbines, rated at 228 MW each, reinforced when MPL secured one of the limited long- will produce the highest output of 'any operating term fuel gas supply contracts with British Gas. The fuel combustion turbines in the world, a combination which gas delivery date dictated the overall project completion will result in one of the highest efficiency combined cycle schedule of 40 months. plants in the world. The atwo-on-one combined cycle turbine generator Medway Power Limited, a joint venture company arrangement gives MPL greater operating flexibility. formed by Applied Energy Services Electric Ltd. (AES) Three generators will feed the grid, allowing turndown or and subsidiaries of Seeboard and Southern Electric, is prompt surge capability. MPL economic studies included jointly developing the Medway Power Station on the Isle the regional grid limitation of 660 MW connected load at of Grain, Kent, on the River Medway, east of London. the National Grid Company intertie. AES Medway Operations (AESMO) will operate and The pro forma economic evaluation excluded bypass maintain the station. The Medway Station is under stacks and simple cycle operation from the baseload plant construction and commercial operation is planned for operating model. 1 August 1995. Presented at the International Gas Turbine end Aeroengine Congress end Exposition The Hague, Netherlands — June 13-15, 1994 This paper has been accepted for publication in the Transactions of the ASME Discussion of it will be accepted at ASME Headquarters until September 30, 1994 A reserve fuel oil facility offers revenue stream illustrate that the Medway Plant is highly efficient relative security and high plant availability to MPL in case the to the traditional combined cycle plants preceding it. fuel gas supply is cut off for any reason. The plant also includes an on-line performance monitoring system, which will further improve overall efficiency as operating procedures are optimi7cA MEDWAY POWER BLOCK The combined cycle block contains the turbines and Downloaded from http://asmedigitalcollection.asme.org/GT/proceedings-pdf/GT1994/78866/V004T10A019/2405123/v004t10a019-94-gt-434.pdf by guest on 25 September 2021 The Medway Plant is the site of a previous World the following major balance-of-plant equipment, all War II vintage oil storage depot. The 11 acre site, shown designed to increase the plant efficiency: on Figure 1, has provisions for additional capacity beyond • Two Nooter/Eriksen natural circulation, triple the initial 660 MW power block and is elevated above the pressure, reheat-type HRSG modular 200 year flood plain. packages. Each HRSG vents into a separate The three turbines in the power block are contained 65 m steel stack at an operating temperature in a common expandable generation building. The plant of 113° C. The HRSGs are unfired. The cooling water makeup is taken from the River Medway selection of the reheat design is key to the high intake structure, and heat is rejected to the wet plant efficiency. The HRSGs are fitted with mechanical draft cooling tower. Demineralized water for inlet duct acoustic lining instead of the steam cycle makeup and combustion turbine NO2 control traditional stack silencer. The reduced is produced in an onsite water treatment plant. An pressure drop improves cycle efficiency by onsite tank battery stores process water and reserve fuel reducing combustion turbine back-pressure. oil. The fuel gas used to supply the combustion turbines • Three GEC-Alsthom generator step-up is conditioned in an in situ gas compound. transformers rated for 290 MVA at 15 kV/420 Site effluents are collected, monitored, and treated kV, for trammicsion to the National Grid via to meet permitted standards before release. The plant the in situ switchyard. Two 20 MVA main stack emissions are designed to be lower than current auxiliary transformers power the unit auxiliary United Kingdom standards. The permitted values are loads. 45 ppm NO2 on gas fuel. • One Hamon twelve-cell mechanical draft, low The plant is designed for a boundary noise level of drift, low-noise, concrete structure evaporative 65 dBA. To stay within this level, the turbines are cooling tower. These features Will Millitnint acoustically enclosed, and the HRSGs are also treated the environmental impact to the plant and partly enclosed. Plant exterior walls are treated to ne:Thbors. The cooling tower provides 1.614 x achieve safe operator noise levels. 109 kJ/h of heat rejection capability at a flow rate of 612,000 1/min, ambient temperature of 11° C, and 80 percent relative humidity. The Performance and Efficiency tower is designed for 1.4 cycles of seawater The new and clean net plant overall efficiency, based concentration and is chlorinated from an on lower heating value (LHV), exceeds 53 percent while adjacent electrochlorinator. burning natural gas. The Medway combined cycle • One two-train, two-bed Glegg demineralizer baseload efficiency parameters are as follows: plant. The water plant has 4,670 Ipm capacity • CTG output = 228 MW at 11 C for maximum NO2 control water injection to • CTG heat rate = 10,180 kJ/kWh, LHV. the combustion turbine combustors while • CTG efficiency = 35 percent. burning reserve fuel oil. • STG output = 247 MW. • One Senior Thermal surface condenser • STG heat rate = 7,934 kJ/kWh. designed for full steam turbine bypass, fitted • STG efficiency = 88.7 percent HP with titanium tubes and tubesheet and water isentropic/91.8 percent 1P/LP isentropic. box coating for brackish cooling water. The • Auxiliary power and transformer losses 5 2.5 condenser is sized to supply 41 mm HgA back percent. pressure to the steam turbine at steam • Net output available = 682 MW. conditions of 538° C and at 97 bar abs for • Net heat rate = 6,800 kJ/kWh. main steam, 355° C at 28 bar abs for hot • Net plant efficiency = 53 percent. reheat, and 260° C at 6.7 bar abs, while These are conservative values which are subject to condensing 655,000 kg/h using 21 ° C cooling normal wear as the plant matures. These parameters water. 2 Downloaded from http://asmedigitalcollection.asme.org/GT/proceedings-pdf/GT1994/78866/V004T10A019/2405123/v004t10a019-94-gt-434.pdf by guest on 25 September 2021 Figure 1. Medway Plant Site Arrangement • One Graham vacuum-type feedwater deaerator rated at 228 MW on gas fuel, are the latest in high and storage tank common to both HRSG efficiency, low emission 50 Hz power generation feedwater pumping systems. The vacuum equipment which have been scaled up from the 160 MW deaerator selection contributes to the improved class MS7001FA 60 Hz combustion turbine. cycle efficiency. The deaerator will operate at The packaged arrangement developed for the 150 mm Hga and will exhaust to the MS7001FA and MS9001FA combustion turbines and condenser. accessories maximizes the efficient use of space within • Two Graham/Crane water-to-gas heat the building and reduces installation cost while exchangers sized to elevate the fuel gas maintaining high reliability and redundancy for key temperature from 27° C to 150° C.
Details
-
File Typepdf
-
Upload Time-
-
Content LanguagesEnglish
-
Upload UserAnonymous/Not logged-in
-
File Pages14 Page
-
File Size-