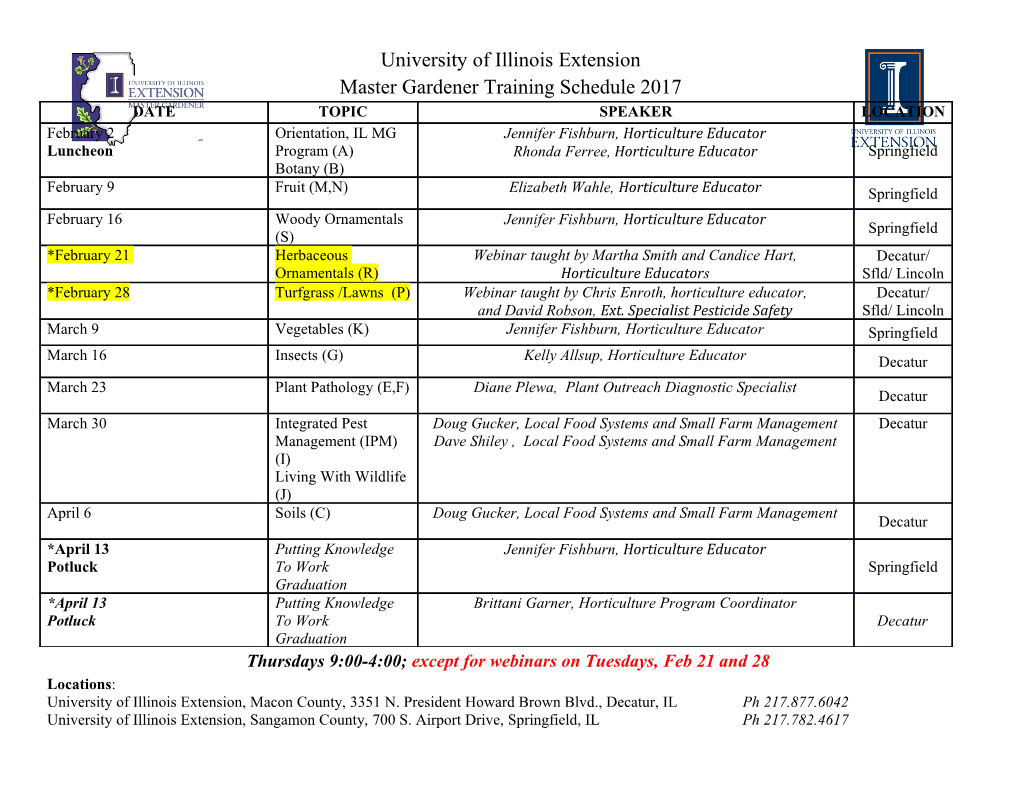
ARDOP: A Versatile Humanoid Robotic Research Platform Sudarshan S Harithas Harish V Mekali BMS College of Engineering BMS College of Engineering Bangalore, Karnataka, India Bangalore, Karnataka, India [email protected] [email protected] ABSTRACT designs and software packages of ARDOP have been made available This paper describes the development of a humanoid robot called open-source and it can be replicated within $1000. ARDOP. The goal of the project is to provide a modular, open-source, Our contribution can be summarized as follows: and inexpensive humanoid robot that would enable researchers (1) Development of a robust, modular, inexpensive humanoid ro- to answer various problems related to robotic manipulation and bot and open-source of its design files and software packages perception. ARDOP primarily comprises of two functional units that can be easily reproduced. namely the perception and manipulation system, here we discuss (2) Formulation and design of 6DOF robotic manipulator con- the conceptualization and design methodology of these systems sidering workspace and torque constraints. The arm can and proceed to present their performance results on simulation perform object manipulation to sub-centimeter range accu- and various custom-designed experiments. The project has been racy. maintained on our page https://ardop.github.io/. KEYWORDS Humanoid Robot, robotic manipulator design, object manipulation, kinematics, Perception 1 INTRODUCTION The multidisciplinary research community has been increasingly focusing on developing robots that can assist and perform activ- ities with humans in the loop. To serve the increase in attention, a robust modular research platform that can aid in rapid testing and software development, while being affordable, simple to recon- figure is of prime importance. Here we present Autonomous Robot Development Open Source Platform (ARDOP) a robot that intends to accelerate research primarily in the domains of manipulation [1], and perception [2] [3]. The robot is depicted in Fig. 1 At the core ARDOP consists of two functional units namely the perception and manipulation system . A calibrated RGBD Microsoft Kinect camera [4] and the pan-tilt joint of the neck form the per- ception system, the manipulation system includes a pair of 6DOF robotic manipulators and its corresponding control system. A de- Figure 1: ARDOP, a Humanoid Robotic Research Platform. tailed description of the conceptualization, design, and development of individual systems has been presented in this paper. Furthermore, 2 DESIGN we present the ARDOP arm where the manipulator is constructed The structural design of ARDOP depicted in Fig. 3, the robot is built considering the workspace and torque constraints. Additionally, using aluminum and is powder coated to ensure electric insulation we evaluate the independent and coordinated performance of these and enhanced aesthetic beauty. The design of the robot is inspired systems through a series of experiments such as workspace aware by the bodily structure of "centaur" 1. In this section, we describe the object manipulation and Tic-Tac-Toe. mechatronic architecture of ARDOP, followed by the manipulator Research across industry and academia have resulted in a few of design and kinematics. the finest robots such as PR2 [5] , Robot Cosero [6],Intel HERB[7], Armar III [8], Pepper [9], bipedal robots such as ASIMO [10], 2.1 Mechatronic Architecture ASIMO [10], and Petman [11], Atlas [12] form another class of The mechatronic architecture describes the interactions between humanoid robots. These robots have helped to expedite research the actuators, sensors, computation, and power distribution circuits. but despite their impressive performance and encouraging results The mechatronic architecture of ARDOP is depicted in Fig. 4. they are very expensive for purchase and only a few of them are The architecture includes three modules open source but are difficult to replicate. Whereas all the hardware Head: RGBD Camera (Kinect) with pan-tilt neck joint (2DOF • actuator). ,, . 1https://en.wikipedia.org/wiki/Centaur ,, Sudarshan S Harithas and Harish V Mekali Arm: a pair of 6DOF manipulators. torque. Furthermore, we can interpret that motors at joints 푆 and • 1 Upper Base: Housing for computer, drivers, power supply 푆 would have a higher torque requirement when compared to mo- • 2 units, and controllers. tors at other joints. Therefore, we consider the torque 푇1 (of motor A 12V 60Ah battery connects to the power distribution and servo 푆1) and 푇2 (of motor 푆2) to constrain and obtain the optimal link control board and powers the manipulation and the perception sys- length 퐿1 and 퐿2, that would enable the arm to access maximum tems of ARDOP. The power supply is secured and monitored by workspace volume. the safety circuits and power meter respectively. The manipulation Considering Fig. 6(a), the torque 푇1 and 푇2 can be obtained from system consists of two 6DOF arms which are controlled using the Eq. 1 and 2 respectively, where 푚퐿1 and 푚퐿2 is the mass of the link. Arduino Mega development board and the perception system con- sists of a Kinect camera and a 2DOF pan-tilt joint. Furthermore, 퐿1 퐿2 푇1 =푚 푚 퐿 1 푚 퐿1 3푚 퐿 1 퐿 2 ARDOP has a tall neck of length 46푐푚, which places the camera at 퐿1 ( 2 ) + ( ) + 퐿2 ( + 2 ) + ( + ) an optimal viewing position, additionally, it helps to counter the blind spot in the depth image of the Kinect camera. The laptop with 푚 푝 퐿1 퐿 2 퐿 푒푒푓 (1) Intel i5-6200U CPU with 16 GB RAM and a 1 TB HDD is housed in + ( + + ) the performs the computation and inter-system coordi- upper base 퐿2 푇 =푚 3푚 퐿 푚 푝 퐿 퐿 (2) nation. 2 퐿2 ( 2 ) + ( 2) + ( 2 + 푒푒푓 ) An aluminium sheet with density 퐷 = 2.7 10 3 퐾푔 , thickness 2.2 Software Architecture ( ) × − 푐푚3 (H) 0.3푐푚 and breadth (B) of 12푐푚 is used for arm design. Consid- The modular software stack allows for simple user interface and ering the rectangular structure of the sheet, the volume of link L1 development, it comprises of four layers as depicted in Fig. 2 and L2, their volume can be expressed as, Hardware Abstraction The layer comprises of the drivers • 푉=퐿 , 12 0.3 and controllers that communicate with the hardware actua- 1 2 × × tors/sensors. and mass of link L1 and L2 can be expressed as, TheOS layer consists of the Robot Operating System that • 푀푎푠푠 푀 = 퐷푒푛푠푖푡푦 퐷 푉표푙푢푚푒 푉 is central to the software architecture. This layer provides ( ) ( )× ( ) various tools and libraries that are required for the user level 3 푚 퐿 , =2.7 10 12 0.3 퐿 , program development. ( 1 2) × − × × × 1 2 System Service this layer includes the various user defined 푚 퐿 =9.72 10 3 퐿 =퐾 퐿 (3) • 1,2 − 1,2 1,2 programs that can be deployed on the robot. Fig. 2 depicts ( ) × × × Substituting퐿 2 = 42 퐿 1 and the above results in Eq. 1 and 2, the program stack of the three systems specific to the various − experiments that we had conducted as detailed in section 3. 푘 42 2 푇 =푚퐿 ( ) 3푚 42 0.2 50 (4) Application this is an actionable layer where the final imple- 1 1 + 2 + ( ) + ( ) • mentation of the program can be observed. 퐾 42 퐿1 2 푇 = ( − ) 3푚 42 퐿 0.2 42 퐿 8 (5) 2 2 + ( − 1) + ( − 1 + ) 2.3 Manipulator Design The worst-case torque 푇 , 푤푐 analysis is performed by increasing ( 1 2 ) ARDOP is geometrically symmetric in the sagittal plane. It has two the torque requirement by 75% i.e. 푇 , = 1.75 푇 , and considering 1 2 × 1 2 identical 6 DoF arms with its shoulder joint equidistant from the efficiency factor (휂= 0.7) for the available motor with a stall torque base of the neck. Fig. 5, depicts the geometric and coordinate frame of 35퐾푔.푐푚. Two motors are used in the shoulder joint 푆1 to increase representation of ARDOP. A 3DOF spherical wrist has been used the stability and robustness of the arm, moreover, this implies that to enable the manipulator to access the complete volume of the the effective torque at joint 푆1 is 70퐾푔.푐푚. The worst-case analysis workspace in all possible orientations, the ARDOP arm is shown in factor (훽) is given by, Fig. 6. 휂 0.7 The arm design involves determining the mass, link length and 훽= = =0.4 1.75 1.75 selecting appropriate motors for a given payload. From the stick di- agram of the arm is shown in Fig. 6(a), the following considerations Hence,푇 = 70훽= 28퐾푔.푐푚, and푇 = 35훽= 14퐾푔.푐푚. are made: 1푤푐 2푤푐 (1) The arm length퐿 퐿 퐿 = 50푐푚. 푇1 <푇 1푤푐 푎푛푑 푇2 <푇 2푤푐 (6) 1 + 2 + 푒푒푓 (2) The end-effector length퐿 푒푒푓 =8푐푚, this implies A graph as shown in Fig. 7 is plotted between the various values 퐿 퐿 = 42푐푚. 1 + 2 of link length 퐿1 and its corresponding expected torque values 푇1 (3) Maximum payload mass 푚 = 0.2푘푔 (inclusive of the mass 푝 and 푇2. For all the points that do not obey the worst case condition as of the end-effector). given by Eq. 6 are eliminated and a value of " 10" would assigned − (4) All six motors of the same mass (푚), 푚푠0 =푚 푠1 =푚 푠2 = to them indicating their elimination. From the graph it can be 푚 =푚 =푚 =푚=0.064푘푔. 푠3 푠4 푠5 further inferred that the available link length 퐿1 is between 16푐푚 It can be observed from Fig. 6, that the mass of the arm is dis- to 24푐푚. We choose an optimal and safe value of 퐿1 = 20푐푚 and tributed along the axis of motor 푆 , which decreases its required 퐿 = 42 퐿 = 22푐푚. 0 2 − 1 ARDOP: A Versatile Humanoid Robotic Research Platform ,, Figure 2: Software Design Figure 3: ARDOP Structural Design 2.3.1 Simulation.
Details
-
File Typepdf
-
Upload Time-
-
Content LanguagesEnglish
-
Upload UserAnonymous/Not logged-in
-
File Pages7 Page
-
File Size-