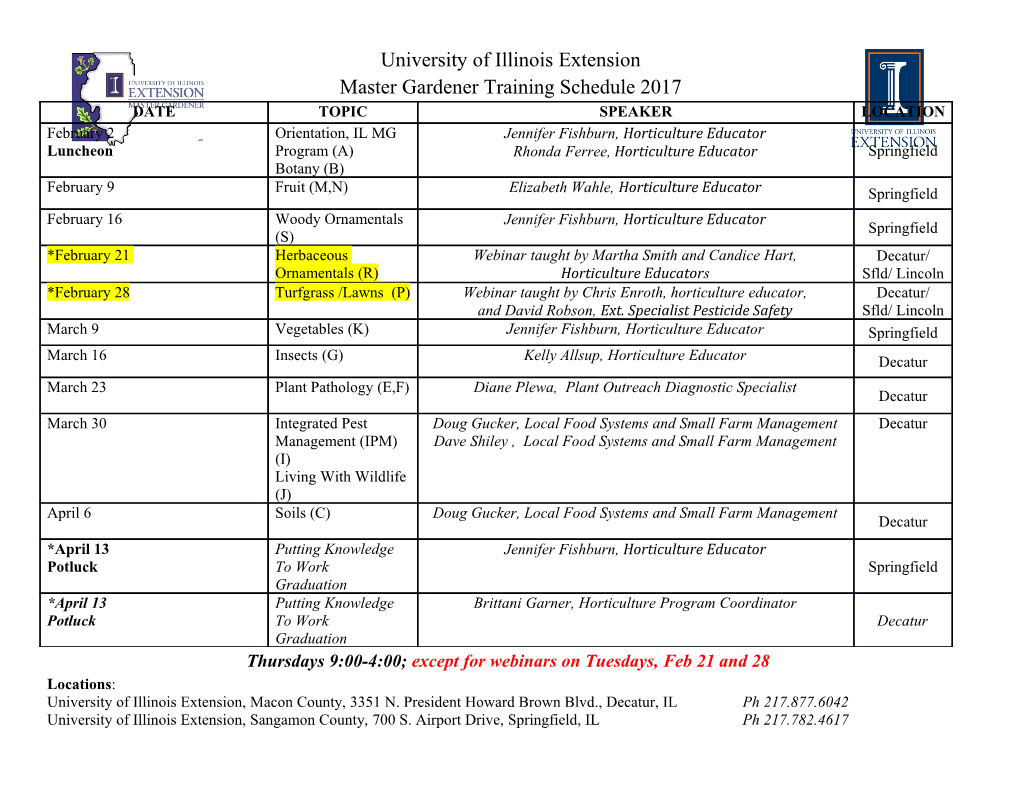
Plywood vs. OSB New-generation structural panels mean decade-old notions are no way to choose sheathing. Here’s what you need to know. BY SEAN GROOM Price • Basic OSB panels are generally several dollars cheaper than CDX plywood. Moisture resistance • Plywood absorbs water faster and dries out faster than OSB. Both types of panels swell around the edges as they get wet, but plywood returns nearly to its original thickness as it dries, while OSB swelling is irreversible. Job-site handling ike the old latex- versus oil-paint debate, people hold • OSB panels lie flat and are engineered for consistent strong feelings about oriented strand board (OSB) and ply- quality without knots or voids. Plywood, on the other wood. Because there seems to be some truth on each side hand, resists edge damage better and weighs less of the argument, it’s not easy to figure out which type of Lstructural panel you should be using. than OSB. From a cost-saving perspective, the appeal of OSB is easy to Performance understand. Sheathing a 2500-sq.-ft. house with OSB can save about • As structural panels, plywood and OSB are designed to $900 compared to the cost of plywood sheathing. OSB advocates also meet the same load and span ratings. However, tile and point out that these panels are more uniform than plywood and that resilient-flooring associations generally do not recom- OSB has a higher “green building” value because it can be manufac- mend installing their products directly over OSB. tured from lower-grade logs rather than veneer-grade timber. Many wood species can be used for OSB, not just softwoods, as is the case Environmental concerns with plywood sheathing. Plywood advocates counter that it’s tough • OSB can be manufactured from lesser-quality trees and to argue with a 50-year durability record and claim that plywood is a with less glue than plywood. stronger panel that holds up better to water. Despite the strong opinions, contractors and homeowners have been adopting OSB steadily since its commercial introduction around 1980. 94 FINE HOMEBUILDING Drawings this page: Don Mannes Seattle, WA Des Moines, IA CDX $18.49 CDX $19.96 1 -in. 1 -in. ⁄2 OSB $13.49 ⁄2 OSB $16.25 3 CDX $25.99 3 CDX $28.40 ⁄4-in. ⁄4-in. OSB $24.99 OSB $23.98 Cost comparison A survey of lumber- Waterford, CT yards around the CDX $23.34 country revealed that 1 -in. ⁄2 OSB $16.74 despite rising prices, 3 CDX $34.49 you generally can save ⁄4-in. OSB $29.80 a few bucks on com- modity-grade structur- al panels buying OSB Santa Fe, NM CDX $19.98 instead of plywood. 1 -in. ⁄2 OSB $15.38 Structural-panel prices 3 CDX $29.48 Atlanta, GA fluctuate daily, so ⁄4-in. OSB $29.12 CDX $15.06 these prices capture a 1 -in. ⁄2 OSB $15.63 snapshot in time. The 2500-sq.-ft. house 3 CDX $23.50 price difference nar- ⁄4-in. 3 OSB $22.26 rows for ⁄4-in. panels. Plywood sheathing $5,984.53 Within 10 years, it had snagged one-third of the mar- of plywood, citing more frequent delaminations, core ket from plywood, and by 1999, OSB production had voids, and out-of square panels. surpassed plywood. Mills now produce about 1.5 times Joseph Lstiburek of Building Science Corporation, more OSB than plywood, and APA–The Engineered who lectures extensively on mold and building practices, Wood Association forecasts that OSB will continue to best sums up the prevailing view: “I would not hesitate gain market share. OSB a heartbeat to use OSB despite the fact that it is both sheathing more water sensitive and more mold sensitive than ply- Rocky starts for plywood and OSB wood. The cost benefits, the versatility benefits, and the $5,075.08 Carpenters were quick to find flaws in both plywood stiffness and structural benefits outweigh the associated and OSB when they were introduced to the market. risks if the product is used intelligently.” The first plywood panels were produced 100 years ago, but it took 30 years of glue development and the post- Water can ruin any panel World War II building boom for plywood to become a The knock against the first generation of OSB was that widely used sheathing product. Still, many older builders $909.45 savings to the edges swelled when the panels became wet. Con- refused to give up on the solid-pine planks they had your bottom line by tractors may have saved a few bucks buying OSB, but used for years. Over time, the skeptics either retired or sheathing a typical part of that savings disappeared with the added labor were won over by improved panel quality and price. 2500-sq.-ft. house cost of sanding down swollen edges to restore flatness Plywood was the dominant sheathing material 20 exclusively with OSB to a subfloor. Homeowners noticed the problem every years ago when OSB became widely available. The instead of plywood time they pulled into their driveways and saw the edges hefty price difference was an incentive for builders to (costs based on an of OSB sheathing panels outlined in their roof shingles. try OSB. Unfortunately, the new product had a ten- average of survey To limit swelling, manufacturers have adjusted the dency to swell permanently when it became wet. And prices) mix of resins and wax content used to manufacture when it was soaked, some carpenters reported, it fell OSB. They’ve also sealed panel edges to improve water apart. The similarity in appearance to early waferboard, a panel with resistance (sidebar p. 98). These steps haven’t made OSB waterproof, no structural rating and little water resistance, also created confu- but plywood isn’t waterproof, either. Both types of panels will expe- sion over OSB’s performance capabilities. rience problems if water is allowed to puddle on the sheathing or if OSB manufacturers have addressed many of the swelling problems, panels are left exposed to the elements for an extended time. and contractors have found the latest generation of OSB greatly Plywood and OSB are wood products, and the veneers or flakes in improved at a time when many of them complain about the quality a panel react with water the same way that any other form of wood Drawings top left: Don Mannes. Drawings right: Dan Thornton. FEBRUARY/MARCH 2005 95 Grain orientation provides strength. Peels from a log are laid up by alternating the grain direction of each ply at 90° to the one below it. Panel manufacturing: ply vs. strand It’s not unusual for a strength just as ply- are used for plywood, them into thin layers with homeowner to complain wood does. OSB can use much smaller- the grain of the flakes that OSB is just a bunch OSB and plywood both diameter trees, and the running in one direction. of woodchips that are start with debarked trees. quality isn’t as important. Additional strand layers glued together and ask A plywood mill peels the Because OSB panels don’t are added with the grain for plywood because it’s veneer from a spinning need a continuous peeled of each layer in an alter- “real” wood. In fact, log with a giant knife. The veneer, the log doesn’t nating direction, creating plywood advertisements veneers are coated with have to be as straight, a thick mat of cross- encourage this perception glue and laid up with the and the number of knots laminated strands. of OSB. grain orientation at 90° to doesn’t matter. Once plywood panels or Although OSB is indeed the sheet below. The wood strands are OSB mats are assembled, made from thousands of OSB mills chip the logs dried and then fed into a they are pressed under wood flakes that are into flakes roughly 1.5 in. blender that coats them intense heat and pressure glued together, it relies wide, 3 in. to 6 in. long, with wax and resins. The to activate the resins, and on layers of alternating and 0.028 in. thick. Com- flakes then pass through the finished panels then grain orientation for pared to the trees that giant “combs” that orient are trimmed to size. responds: by absorbing moisture and swelling. If a wood panel remains wet long enough, it will decay. If you think you’ve noticed that OSB and plywood get wet at dif- ferent rates, you’re right. This is what Lstiburek means when he says OSB is more water sensitive than plywood. Because plywood is made out of peeled layers of a log, the wood fibers are intact across the entire panel and wick water relatively quickly across the panel. On the other hand, thousands of wood flakes make up an OSB panel, so the wicking action is interrupted continuously. Consequently, OSB takes a lot longer than plywood to get wet. But wet OSB takes a lot longer to dry out, something you need to account for before you in- stall roofing, siding, or flooring. The differences between veneers and flakes affect not only how panels get wet, but also what happens when they get wet. Both Strength in numbers. Each layer of thin, narrow types of panels swell when they absorb moisture; however, wax-and-resin-coated wood strands is arranged with its grain direction orient- because flakes don’t transfer moisture well, OSB is more like- ed 90° to the layer below, just like ly to swell around the edges and in isolated spots. A greater plywood.
Details
-
File Typepdf
-
Upload Time-
-
Content LanguagesEnglish
-
Upload UserAnonymous/Not logged-in
-
File Pages6 Page
-
File Size-