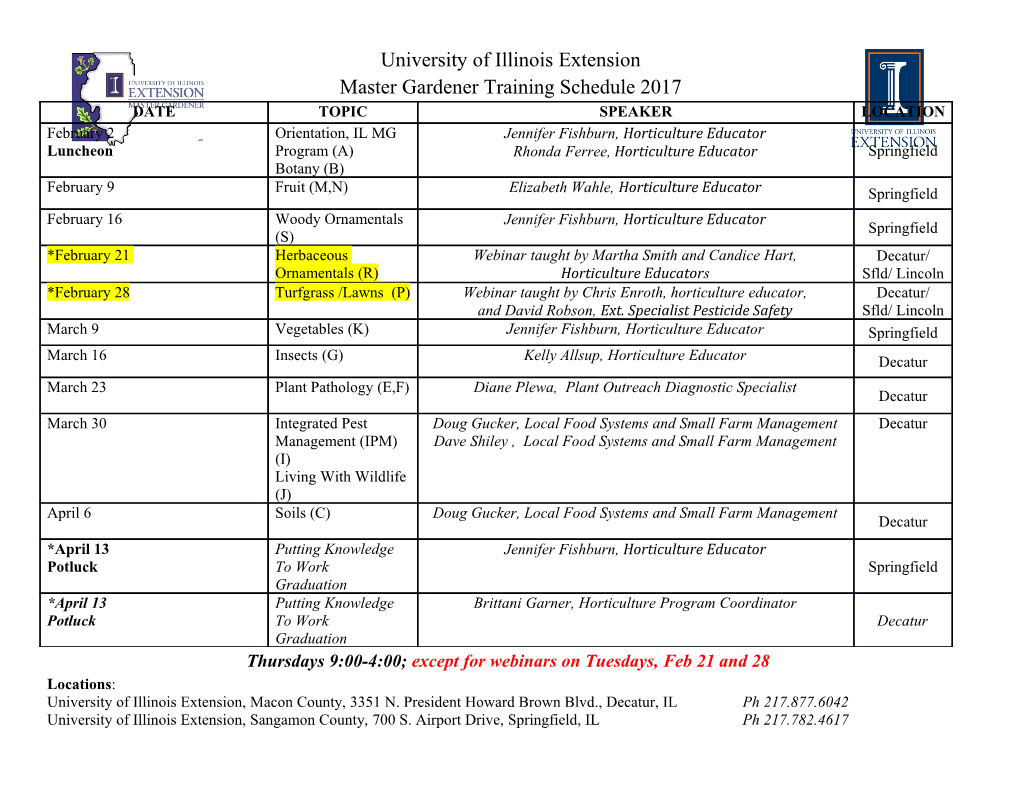
NOTICE CERTAIN DATA CONTAINED IN THIS DOCUMENT MAY BE DIFFICULT TO READ IN MICROFICHE PRODUCTS. dSa./ NREL/MP-451-4778B . UC Category': 270 • DE92 NRHL/MP--451-4778B DE92 04032.1 Safety Analysi%^.eport For the Use of Hal|ardous Production Materials in Photovoltaic Applications at the National Renewable Energy Laboratory Volume II: Appendices •.-ft '4^ oil, R.S, Crandall B»P. Nelson P.D. Moskowitz V.M. Fthenakis *N?S! National Renewable Energy Laboratory 1617 Cole Boulevard Golden, Colorado 80401-3393 A Division of Midwest Research Institute Operated for the U.S. Department of Energv under Contract No. DE-AC02-83CH10093 " July 1992 Hi ^_ oismiuuiiuh or IMUI NOTICE Tnis report was ptepared as an account of work sponsoied by an agency of the United States government Neither the United Slates government nor any agency thereof nor any of their employees, makes any warranty express o< implied or assumes any legal liability Of tesponsibility'or the accuracy completeness or usefulness of any information apparatus product or process disclosed 01 represents that its use would not infringe privately owned, rights Reference herein to any specie commercial product process or service by trade name trademark manufacturer or otherwise ooes not necessarily constitute or imply its endorsement recommendation or favoring by the United Slates government or any agency lhereo> The views and opinions of authors expresseo herein do not necessarily state or reflect those of the United State; government or any agency theieof APPENDICES - TABLE OF CONTENTS A: AffCJtiftflt/RisK Appends Appendix Al Failure Rate Data (appendix references provided at end of appendix A3) Appendix A2 Estimating Concentrations from Gas/Vapor Releases in Gas Cabinets & Laboratories (appendix references provided at end of appendix A3) Appendix A3 PVPUFF: Gaussian Puff Dispersion Model €: Code Appendices Appendix CI UFC Article 80 - Hazardous Materials Appendix C2 UFC Anicle 51 - Semiconductor Fabrication Facilities Using Hazardous Production Materials to the MDA Toxic Gas Alarm i: Institute Appending Appendix 11 Emergency Response Procedures to the MDA Toxic Gas Alarm Appendix 12 NREL Chemical Hygiene Plan Appendix 13 NREL Comments to Fluer Recommendations Appendix 14 Excerpts on Natural Disaster from Harvey Report Appendix 15 SERI ES&H Office Quality Assurance Plan M: Manufacturing Appendices Appendix Ml MSDSs (M1.1-M1.19, save Ml .14) for HPMs listed in Table 3a of the SAR Appendix M2 Manufacturer Specifications for Metalorganic Bubbler Appendix M3 Manufacturer Specifications for Secondary Containment for Gas Cylinders Appendix M4 Manufacturer Specifications for Pneumatically Operated Cylinder Valve Appendix M5 Manufacturer Specifications for Drv Chemical Gas Cabinet Scrubber Appendix M6 Manufacturer Specifications for Fume Scrubber Appendix M7 Manufacturer Specifications for Vent Gas Scrubber/Scram System Appendix M8 Burn Box - Plus Schemaric Design for Effluent Treatment S: Sanu^fe^M£ndk£a Appendix S1 Sample Checklist for Hazardous Gas Cylinder Changing Procedures Appendix S2 Sample Training Log Appendix S3 Sample Toxic Gas Inventory Log Appendix S4 Sample Preventative Maintenance Log Appendix S5 Sample Safety Interlock/Alarm Inspection Log APPENDIX Al FAILURE RATE DATA In the storage, handling, use and disposal of toxic gases, accidental releases may arise for any of the following reasons; design errors, construction errors, equipment failures, human errors, and process upsets. Marsh and McLennan Protection Consultants [1] have analyzed 100 major incidents (fire, explosion, and toxic release) in the hydrocarbon-chemical industry and classified the causes of these events into the following categories: mechanical equipment failure, processs upsets, human error and arson or sabotage. Figure Al shows their compiled statistic s on these incidents. Failure of individual components in isolauon may not result in the accidenul ielease of a hazardous gas or liquid. Often a release may occur only after a senes of components fail. These tiains of events or failures are often identified using fault and ^\cnt tree analyses. These techniques have not been used in this SAR because of the scoping nature of this document. To help identify tht rough order of magnitude for events probabilities, sample system/component failure rate data compiled by EPA [21 are shown in Table Al-1. Table A1-2 gives representative data for operator or human error. Because these data are derived from industries other then the semiconductor or photovoltaic industry, they are presented as representative estimates only. BREAKDOWN OF ACCIDENTS IN THE HYDROCARBON-CHEMICAL INDUSTRY Figure A1 ' " « ' ll| ' f i" '111 "i (IP! HI II ii |iiitn|i||i|||i|i iu IUP T Mfipfi APPENDIX TABLE AM TYPICAL FAILURE RATES* SYSTEM PROCESS COMPONENTS FAULTS/YEAR Process System Components Control valve 0.25 - 0.60 Differential pressure transmitter 0.76- 1.73 Variable area flowmeter transmitter 0.68 - 1.01 Thermocouple 0.088 -0.52 Pneumatic controller 0.29 - 0.38 Flow Control Components Flowmeters D/P cell and transmitter 0.76- 1.73 Magnetic 2.18 Flow controller 0.29 - 0.38 Control valve 0.25 - 0.60 Flow switch 1.12 Flow indicators 0.026 Check valve (backflow prevention) 1.10 x 10"4 Control loop 1.73 Pressure Control Components Pressure/Transducer/Transmitter 0.76- 1.73 Pressure indicator 0.026- 1.41 Pressure switch 0.34 Control valve 0.25 - 0.60 Pressure controller 0.29 - 0.38 Pressure control loop 1.73 Temperature Control Components Sensor With Thermowell Thermocouple (TC) 0.52 Resistance temperature detector 0.41 Temperature transducer 0.88 Temperature controller 0.29 - 0.38 Control valve 0.25 - 0.60 Control loop 1.73 Appendix A1 Quality Control Components Load Cell Weigh System 3.75 Level Detection System Differential pressure transducer 1.71 Float system 1.64 Capacitance system 0.22 Electrical Conductivity Probes 2.36 Row totalizer 1.0 Mixing System Components Mechanical Agitator (agitator motor only) "Normal" Service 0.088 "Severe" Service 8.8 Induced Flow Pump System (pump and motor only) "Normal" Service 0.26 "Severe" Service 8.8 Static mixer NA Flow switch 1.12 Pressure switch 0.34 Tachometer 0.044 Composition System Components Composition Determination Equipment Density NA •indicator NA •transmitter _NA pH Meter 5.88 Viscosity Sensor NA •indicator NA •transmitter NA Chemical Species Analyzers Chromatograph 30.6 Infrared Analyzer 1.40 Oxygen Analyzer 2.5 - 5.65 Moisture Analyzer (gases) 8.0 Conductivity Sensor 14.2 - 16.7 Appendix Al Vessel Components Vessel shell -6 Complete failure 3x10 Rupture equivalent to 6 in opening 7x10 Flanged head joint N/A Flanged nozzle piping connections, flange leak or rupture 0.0026 Seam welds N/A Piping Components Pipe wall, under 3 in. diameter nipture 8.8 x 10 Pipe wall over 3 in. diameter rupture 8.8 x 10 Flanged joint, leak or rupture 0.0026 Gasket leak 0.026 Welded joim,leak 2.63 x 10"5 Valve casing N/A Valve stem seal N/A Manual valve Failure to operate 0.365 Failure to remain open (plug) 0.0365 Leak or rupture 8.8 x 10" Solenoid valve - failure to operate 0.365 Automated valves Failure to operate 0.1095 Failure to remain opern (plug) 0.0365 Leak or rupture 3.65 x 10" Check valves Failure to open 0.0026 -4 Reverse flow leak 1.10 x 10 Rupture 8.8 x 10"5 Process Machinery Components Pumps Failure to start 0.365 Failure to run 0.011 -3 Shaft seal, major leak 5x10' Compressors N/A * adapted from [ 1 j APPENDIX TABLE Al-2 HUMAN OPERATOR ERROR ESTIMATES Estimated Rates Activity Selection of a key-operated switch rather than a non-key switch this value 10"4 does not include the error of decision where the operator misinterprets situation and believes key switch is correct choice. Selection of a switch (or pair of switches) dissimilar in shape or location io-3 to the desired switch (or pair of switches), assuming no decision error. For example, operator actuates large-handled switch rather than small switch. 3 x 10 " General human error of commission, e.g., misreading label and, therefore selecting wrong switch. General human error of omission, where there is no display in the control .9 10 l room of the status of the item omitted, e.g., failure to return manually operated test valve to proper configuration after maintenance. 3 x 10"3 Error of omission, where the items being omitted are embedded in a procedure rather than at the end as above. 3 x 10'2 Simple arithmetic errors with self-checking but without repeating the calculation by redoing it on another piece of paper. Given that an operator is reaching for an incorrect switch (or pair of 1/x switches), he selects a particular similar-appearing switch (or pair of switches), where x = the number of incorrect switches (or pair of switches) adjacent to the desired switch (or pair of switches). The 1/x applies up to 5 or 6 items. After that point the error rate would be lower because the operator would take more time to search. With up to 5 or 6 items he doesn't expect to be wrong and therefore is more likely to do less deliberate searching. Given that an operator is reaching for a wrong motor-operated valve 10"1 (MOV) switch (or pair of switches), he fails to note from the indicator lamps that the MOV(s) is (are) already in the desired state and merely changes the status of the MOV(s) without recognizing he had selected the wrong switch(es). Monitor or inspector fails to recognize initial error by operator. Note: IO"1 With continuing feedback of the error on the annunciator panel, this high error rate would not apply. - 10-n Personnel on different work shift fail to check condition of hardware unless required by check list or written directive.
Details
-
File Typepdf
-
Upload Time-
-
Content LanguagesEnglish
-
Upload UserAnonymous/Not logged-in
-
File Pages251 Page
-
File Size-