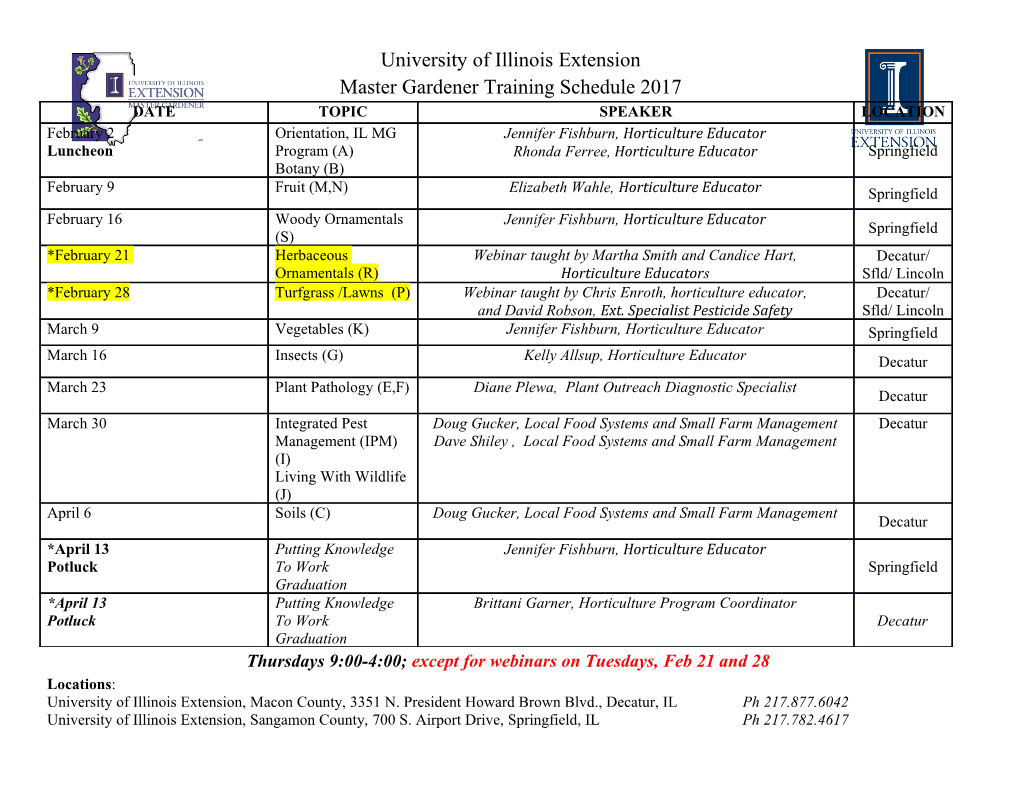
University of Pennsylvania ScholarlyCommons Department of Chemical & Biomolecular Senior Design Reports (CBE) Engineering 5-4-2015 Fluidized Catalytic Cracking to Convert Biomass to Fuels Stephen Boust University of Pennsylvania Mo Green University of Pennsylvania Serena Machi University of Pennsylvania Follow this and additional works at: https://repository.upenn.edu/cbe_sdr Part of the Biochemical and Biomolecular Engineering Commons Boust, Stephen; Green, Mo; and Machi, Serena, "Fluidized Catalytic Cracking to Convert Biomass to Fuels" (2015). Senior Design Reports (CBE). 72. https://repository.upenn.edu/cbe_sdr/72 This paper is posted at ScholarlyCommons. https://repository.upenn.edu/cbe_sdr/72 For more information, please contact [email protected]. Fluidized Catalytic Cracking to Convert Biomass to Fuels Abstract The process of biomass fluidized catalytic cracking (BFCC) has been adapted from the traditional fluidized catalytic cracking of crude oil in petroleum refineries. Instead of a naphtha eedstf ock, BFCC can accommodate various types of biomass that is cracked into more valuable aromatic and olefinic compounds. This plant inputs forest biomass and will be located in southwestern Louisiana, where wood output exceeds 100 million kg/yr in over ten counties. Biomass, procured in the form of wood chips, must first be dried to a moisture content below 10 wt% and crushed to a particle size of 100-500 micron. The wood sawdust is then fed to a circulating fluidized bed riser, where it undergoes catalytic fast pyrolysis (CFP) in the presence of a ZSM-5 catalyst. CFP occurs at a high temperature of 600 °C, producing an effluent syngas composed of omatics,ar olefins, and olatiles.v The biogas is separated from water and volatiles, produced by deoxygenation processes, in a three phase pressure vessel. The more valuable products of benzene, toluene, and xylenes are then separated from the high-boiling components. The proposed design converts 400,000 metric tons of wood to 17.4 million kilograms of a BTX mixture per year, including 4.6, 7, and 3.3 million kilograms per year of benzene, toluene, and xylenes, respectively. In addition, 345 GWh of electricity is produced yearly as a byproduct. The required total permanent investment for this project is $93 MM. At a discount rate of 10% and BTX sale price of $1.1/kg, the base case net present value (NPV) is $(157 MM) and the expected ROI is -20%. The result of this base case analysis suggests that this project should not be further pursued. The best case scenario assumed double the yield of BTX at a sale price of $1.54/kg and a renewable fuel credit of $1.01/gal, resulting in a NPV of $506 MM, an IRR of 70%, and a ROI of 81 %. The economic feasibility of this project is also sensitive to the availability and price of biomass, as well as the catalyst degeneration rate within the system. Disciplines Biochemical and Biomolecular Engineering | Chemical Engineering | Engineering This working paper is available at ScholarlyCommons: https://repository.upenn.edu/cbe_sdr/72 Prof. Leonard Fabiano Dr. Talid Sinno Dr. Matthew Targett Department of Chemical and Biomolecular Engineering School of Engineering and Applied Science University of Pennsylvania 220 S. 33rd Street Philadelphia PA, 19104 April 14, 2015 Dear Prof. Fabiano, Dr. Sinno and Dr. Targett, Enclosed is our completed proposal for the project “Fluidized Catalytic Cracking to Convert Biomass to Fuels,” as proposed by Dr. Matthew Targett of LP Amina, in fulfillment of the requirements of CBE 459. The proposed design applies catalytic fast pyrolysis (CFP) to wood chips in a circulating fluidized bed riser in the presence of a ZSM-5 catalyst. The CFP products include volatile gases, coke, and a mixture of aromatics. The aromatic products are separated from the coke and volatiles to yield BTX. The heat network of the process has been optimized to produce steam for electricity generation. This process is renewable and utilizes non- food source biomass available in excess in the U.S. Although the market for BTX is currently in decline, the global petrochemicals market was valued at $559 billion in 2013 and is predicted to grow to $885 billion by 2020. BTX represents a $120 billion global market, historically growing at rates greater than the global GDP. BTX and its derivatives comprise feedstocks used by the chemical industry to make products such as automobile tires, nylon, laundry detergent, polyester clothing and packaging. The proposed design converts 400,000 metric tons of dry wood biomass to approximately 17.4 million kilograms of a BTX mixture per year, including 4.6, 7, and 3.3 million kilograms per year of benzene, toluene, and xylenes, respectively. In addition, almost 345 GWh/yr of electricity is produced. The required total permanent investment for this project is $93 MM. At a discount rate of 10% and a BTX sale price of $1.1/kg, the base case NPV is $(157 MM) and the projected ROI is -20%. The best case scenario assumed double the yield of BTX at a sale price of $1.54/kg and a renewable fuel credit of $1.01/gal, resulting in a NPV of $506 MM, an IRR of 70%, and a ROI of 86%. The result of this base case analysis suggests that this project should not be pursued further. Sincerely, Stephen Boust Mo Green Serena Machi FLUIDIZED CATALYTIC CRACKING TO CONVERT BIOMASS TO FUELS Stephen Boust Mo Green Serena Machi April 14, 2015 Industrial Consultant: Dr. Matthew Targett, LP Amina Faculty Advisor: Dr. Talid Sinno, University of Pennsylvania Department of Chemical and Biomolecular Engineering School of Engineering and Applied Science University of Pennsylvania Table of Contents 1. Abstract ....................................................................................................................................... 5 2. Introduction ................................................................................................................................. 7 2.1 Project Motivation ........................................................................................................ 8 2.2 Project Charter ............................................................................................................ 14 2.3 Innovation Map ........................................................................................................... 15 3. Concept Stage ........................................................................................................................... 17 3.1 Market Analysis .......................................................................................................... 18 3.2 Competitive Analysis .................................................................................................. 21 3.3 Preliminary Process Synthesis .................................................................................... 25 3.3.1 Reactor Yield and Mass Balance ................................................................. 26 3.3.2 Catalyst Lifetime .......................................................................................... 27 3.3.3 Catalyst Regeneration with Acid Wash ....................................................... 28 3.3.4 Use of Spray Condensers to Extract Liquid Product ................................... 30 3.3.5 Extractive Distillation for Purification of BTX Product .............................. 31 3.3.6 Co-sale of Propylene .................................................................................... 31 3.3.7 Process Design Influences ........................................................................... 32 3.4 Assembly of Database................................................................................................ 34 4.Process Flow Diagrams and Material Balances ......................................................................... 37 4.1 Overall Process Flow Diagram ................................................................................... 38 4.2 Block 100: Biomass Preparation ................................................................................. 40 4.3 Block 200: Pyrolysis & Catalyst Regeneration .......................................................... 42 4.4 Block 300: Product Separation ................................................................................... 46 4.5 Block 400: Heat Integration ........................................................................................ 50 4.6 Block 500: Electricity Generation .............................................................................. 56 5.Process Descriptions .................................................................................................................. 59 5.1 Process Overview........................................................................................................ 60 5.2 Process Section 100: Biomass Preparation ................................................................. 61 5.3 Process Section 200: Pyrolysis & Catalyst Regeneration ........................................... 61 5.4 Process Section 300: Product separation .................................................................... 63 5.5 Process Section 400: Heat Integration ........................................................................ 68 5.6 Process Section 500: Electricity Generation ............................................................... 70 6.Energy Balances and Utility Requirements ............................................................................... 71 6.1 Utility Costs Overview ..............................................................................................
Details
-
File Typepdf
-
Upload Time-
-
Content LanguagesEnglish
-
Upload UserAnonymous/Not logged-in
-
File Pages303 Page
-
File Size-