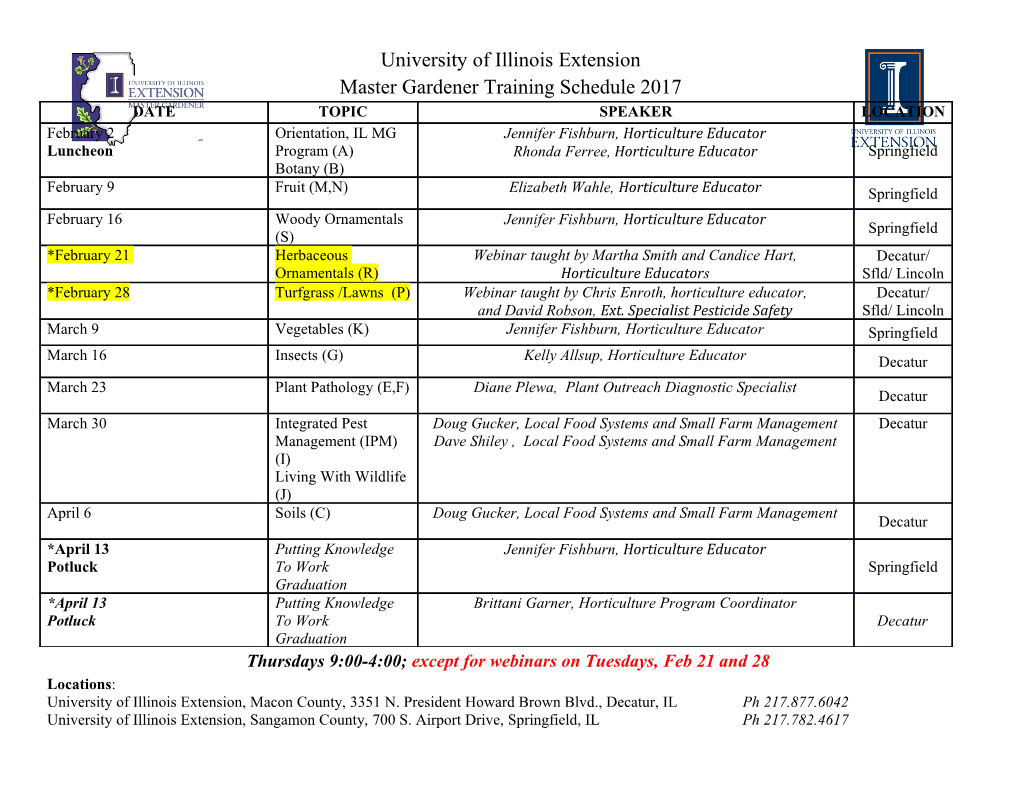
Conference Proceedings Plastics Are Shaping Tomorrow Today April 18-21,1988 Society of Plastics Engineers IMG, POLYMER MO DIFIERS&ADDmV ES, THERMOPLA STICS, FAILURE ANALYSIS, COM PUTERSINPLAS TICS, MATERIALS & FOAMS, ENER GETIC PROCESS ING, POLYMERS COLOR & APPEAR ANCE, ENERGE TIC, DISPOSING & RECYCLING OF PLASTIC ALLOYS & BLE NDS, PLASTICS IN ELECTRONICS &PHOTOTRONICS 46th ANNUAL iCHNICAL CONFERENCE & EXHIBITS Contents COLOR AND APPEARANCE DIVISION Synthetic Complex Metal Oxide Pigments for Plastics 2 J. Hackman, The Shepherd Color Co. Colored Luminescence—The Next Frontier 7 T. Mahany II, Eldon Enterprises Ltd. Liquid Color in PET Packaging 10 D. Peacock, PDI The Effects of Metal Ions on Daylight Fluorescent Pigments in Plastic Systems 12 J. Cook, Day-Glo Color Corp. Colorants for Polymers Regulation as Indirect Food Additives 16 G. McCowin, Food and Drug Administration Refractive Index—A Key to Understanding Color Differences 18 B. Donald, Dow Chemical Co. R. Mathew, Americhem, Inc. The Effect of Concentrate Viscosity Characteristics on Color Development in LLDPE Film 22 R Patet, Colortech Inc. W. Baker, Queen's University Concentrates of Minerals, Additives, and Pigments Using Low MW Polypropylene Carriers 24 L. Bourland, ARCO Chemical Co. Color Stability of Pigmented Polystyrene 28 D. Holtzen, £ /. du Pont de Nemours & Co., Inc. EXTRUSION DIVISION Extrusion Characteristics of Polypropylene Resins 34 C. Cheng, Exxon Chemical Co. Analysis of Slump in Plastic Pipe Extrusion 38 A. Giacomin, Texas A&M University S. Doshi, McGill University Product Liability—Who Pays for It? , 41 R. Gregory, Robert Gregory Associates, Inc. Evaluating Extruder Screw Performance 45 E. Steward and W. Kramer, Crompton & Knowles Corp. On-Line Additive Injection in the Extrusion Process 51 S. Houlihan, Parker Hannifin Corp. Heat Transfer in Twin Screw Extruders 54 D. Todd, Baker Perkins Inc. Mixing Performance in a Non-lntermeshing, Counter-Rotating Twin Screw Extruder: Experimental Study of Key Parameters Affecting the Nip Region 59 D. Bigio and D. Penn, University of Maryland Towards a Better Understanding of Mixing in a Co-Rotating Twin Screw Extruder 64 D. Kalyon, A. Gotsis, C. Gogos, and C. Tsenoglou, Stevens Institute of Technology Heat Transfer in Twin Screw Extruders 67 H. Larsen and A. Jones, £ /. du Pont de Nemours & Co., Inc. ANTEC '88/vii A Comparative Study of Single and Twin Screw Devolatilizers 71 V. Notorgiacomo and J. Biesenberger, Stevens Institute of Technology Optimisation of Compounding Machines 76 J. Colbert, Baker Perkins Chemical Machinery . •> Scaleup of Counter-Rotating Non-lntermeshing Twin Screw Extruders 80 R. Nichols, Welding Engineers, Inc. J. Lindt, University of Pittsburgh A Numerical Procedure for Evaluation of Mixing in the Nip Region of a Non-lntermeshing, Counter-Rotating Twin Screw Extruder 85 D. Bigio and S. Zerafati, University of Maryland Simulation of Flow of Polymer Melts in Intermeshing Co-Rotating Twin Screw Extruders 89 W. Szydlowski and J. White, The University of Akron Finite Element Modeling of a Counter-Rotating, Tangential (CRT) Twin Screw Extruder 93 K. Nguyen and J. Lindt, University of Pittsburgh Current Developments in Twin Screw Design and Its Application in the Preparation of Polymer Blends 96 K. Kapfer, Werner & Pfleiderer GmbH Feed Mechanism and Screw Design for Grooved Feed Extruders 102 W. Krueger, 3M Co. The Compressibility of the Resin Solid Feed Bed in Extrusion 105 S. Derezinski, Eastman Kodak Co. Extrusion of Polyethylene Pipe Compounds with Double Flight Screws 109 Y. Gau, Union Carbide Corp. An Enhanced Plasticating System Using a Combination of a High-Speed Extruder and Gear Pump 114 G. Menges and H. Langhorst, Institute for Plastics Processing Extruder Screw Analysis 120 R. Kline, Hoechst Celanese Corp. Temperature Development in Pure Drag Flow, Exact Analytical Solution 125 C. Rauwendaal, Raychem Corp. ' J. Ingen Housz, Twente University Dependence of Melt Temperature on Screw Speed and Size in Extrusion 132 Y. Guo and C. Chung, Rensselaer Polytechnic Institute Polycad: A Finite Element Program for Polymer Flow Analysis Through Extrusion Dies 137 J. Vlachopoulos, P. Behncke, and J. Vlcek, McMaster University A Heuristic Approach to Modeling Viscoelasticity in Polymer Processing 140 E. Mitsoulis, University of Ottawa Analysis of Fluted Mixing Devices for Single Screw Extruders 145 D. Sebastian, A. Kiani, and R. Rakos, Stevens Institute of Technology Blown Stretch Film Processing Parameters 149 D. Smith, Battenfeld Gloucester Engineering Co. Equipment and Processing Update for the Blown Film Extrusion of Linear Low Density Polyethylene 151 W. Bode, Battenfeld Gloucester Engineering Co. Review of Developments in Blown Film Machinery Over the Last Decade 158 D. Lounsbury, SANO Inc. Practical Considerations in Barrier Film Coextrusion 162 H. Brax, BC Enterprises, Inc. On-Line Layer Discrimination of Multi-Layer Structures 1£5 S. Shapiro, Aeonic Systems Experimental/Theoretical Studies on a Special Sheet Die 168 J. Charrier and R. Ciplijauskas, McGill University A. Catani and C. de Grandpre, IGM/CNRC J. Agassant and B. Vergnes, CEMEF/Ecole des Mines The Analysis of Non-Isothermal Multi-Layer Coextrusion Flows—A New Approach 172 Y. Shu, S. Chen, and J. Cheng, University of Lowell Automatic Blown Film Dies for High Quality Film 175 W. Feistkorn, Windmoller & Holscher Predicting Flow Performance of Spiral Mandrel Dies 179 J. Perdikoulias, J. Vlcek, and J. Vlachopoulos, McMaster University Viii /ANTEC '88 Correlation Between Orientation and Tear Strengths on Blown Linear Low-Density Polyethylene (LLDPE) Films 183 C. Lee, I. Peat, L. Wild, and R Fernando, USI Chemicals Co. Double Bubble Tubular Film Extrusion Process to Produce Biaxially Oriented Polyethylene terephthalate) Films 187 H. Kang, M. Cakmak, and J. White, University of Akron M. Pollack, Eastman Kodak Co. Utilization of Pressure Transducers for Improved Control of the Extrusion Process 193 R. Infante, Dynisco, Inc. New Melt Pressure Transducer Enhancements 197 W. Wareham and T. Healy, Dynisco, Inc. Maximizing Extruder Throughput and Product Quality Between Screw-Installation and Rebuilding 201 K. O'Brien, Hoechst Celanese Corp. The Processing Functions of Polish and Draw Roll Stands in Plastic Sheet Production 205 W. Virginski, Davis-Standard Division INJECTION MOLDING DIVISION Experimental Determination and Analysis of the Flow Pattern During the Filling of a Complex Mold and Its Dependence on Gate Characteristics 212 A. Garcia-Rejon, G. Salloum, R Girard, and G. Lague, National Research Council of Canada Effects of Deviations from Ideal Runner Balance in Multi-Cavity Co-Injection Molding 216 M. Amon and T. Tung, American National Can Co. Optimization of Gate Location and Operational Molding Conditions for Injection Molding 219 I. Pandelidis, Q. Zou, and I Lingard, University of Maryland Injection Molding—A Systems Approach 223 M. Urquhart, Husky Injection Molding Systems The Hydro-Flex Gate for Injection Molding 226 J. Von Holdt, Plas-Tool Co. Hot Runner Molding Thermodynamic Behaviour of the Gate Area 229 H. Rozema, Mold-Masters Ltd. Determination of Approximate Feasible Molding Space for Injection Molding 233 I. Pandelidis and Q. Zou, University of Maryland A Schematic Overall View of Packing Process in Thermoplastics Injection Molding 237 T. Shibayama, Nagoya Municipal Comparisons Between Injection Mold-Filling Simulation and Experiments 240 V. Wang, Advanced CAE Technology, Inc. C. Hieber and K. Wang, Cornell University J. Werlin and K. Malburn, Eastman Kodak Co. A Bi-Dimensional Model for Thermoplastic Mold Filling Simulation: Fill 2 245 S. Philipon, J. Villemaire, M. Vincent, and J. Agassant, Cenfre de Mise en Forme des Materiaux M. de la Lande, G. Degeneve, and A. Latrobe, CISI Ingenierie A Study of Finite Element Mold Filling Analysis in Application 250 S. Chen, R Pai, and C. Hsu, Application Engineering Corp. Quick Mold Change for Injection Molding Machines 255 R Glorio, Incoe Corp. An Introduction to the Molding of Optical Disc Substrates 259 M. Dunn, Klockner Ferromatik Desma Process Engineering Design of RAM Screws for Injection Molding Machines with Regard to an Improved Melt Quality and Higher Plasticizing Capacity 263 G. Langecker, Battenfeld Entwicklungsgesellschaft MBH New Mixing Screw Concepts for Injection Molding 267 R. Nunn, University of Lowell S. Takashima, HPM Corp. Melt Homogeneity in Injection Molding: Application of a Ring-Bar Device 271 G. Peischl and I. Bruker, General Electric Corporate Research and Development Mechanism for Injection Molding of Difficult High-Aspect-Ratio Configurations 276 G. Galic and S. Maus, Galic/Maus Ventures Melt Viscosity Measurements Using an Instrumented Injection Molding Nozzle 279 R. Malloy, S. Chen, and S. Orroth, University of Lowell ANTEC '88/ix A New Method to Predict the Structural Stability of Injection Molded Parts. A Combination of Flow Simulation and Finite Element Stress Analysis Techniques 285 G. Salloum, A. Garcia-Rejon, R. Connolly, and G. Lague, National Research Council Canada „ Post-Filling Simulation of Injection Molding and Its Applications 290 V. Wang, Advanced CAE Technology, Inc C. Hieber, Cornell University A Statistical Study on the Effects of Velocity and Cavity Pressure on Retained Orientation 294 C. Davis, J. Hudson, and B. Stechulte, GMI Engineering & Management Institute Adaptive Process Control for Injection Molding 298 R. Nunn, University of Lowell C. Grolman, Johnson Wax Transfer Point Control Comparison Between Mold Parting Line
Details
-
File Typepdf
-
Upload Time-
-
Content LanguagesEnglish
-
Upload UserAnonymous/Not logged-in
-
File Pages9 Page
-
File Size-