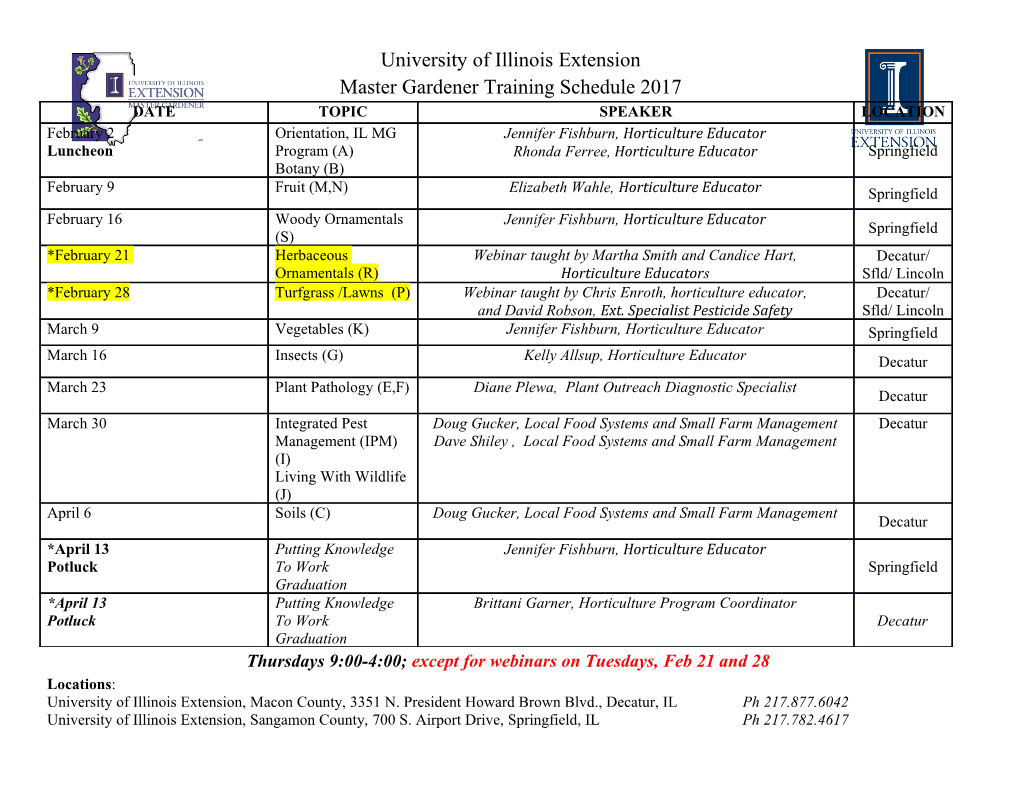
energies Article Validated Analytical Modeling of Diesel Engines Intake Manifold with a Flexible Crankshaft Salah A. M. Elmoselhy 1 , Waleed F. Faris 2,* and Hesham A. Rakha 3 1 CFisUC, Department of Physics, University of Coimbra, P-3004 516 Coimbra, Portugal; [email protected] 2 Department of Mechanical Engineering, International Islamic University Malaysia, Gombak, Kuala Lumpur 53100, Malaysia 3 Virginia Tech Transportation Institute, Virginia Polytechnic Institute and State University, 3500 Transportation Research Plaza, Blacksburg, VA 24061, USA; [email protected] * Correspondence: [email protected] Abstract: The flexibility of a crankshaft exhibits significant nonlinearities in the analysis of diesel engines performance, particularly at rotational speeds of around 2000 rpm. Given the explainable mathematical trends of the analytical model and the lack of available analytical modeling of the diesel engines intake manifold with a flexible crankshaft, the present study develops and validates such a model. In the present paper, the mass flow rate of air that goes from intake manifold into all the cylinders of the engine with a flexible crankshaft has been analytically modeled. The analytical models of the mass flow rate of air and gas speed dynamics have been validated using case studies and the ORNL and EPA Freeway standard drive cycles showing a relative error of 7.5% and 11%, respectively. Such values of relative error are on average less than those of widely recognized models Citation: Elmoselhy, S.A.M.; in this field, such as the GT-Power and the CMEM, respectively. A simplified version for control Faris, W.F.; Rakha, H.A. Validated applications of the developed models has been developed based on a sensitivity analysis. It has been Analytical Modeling of Diesel found that the flexibility of a crankshaft decreases the mass flow rate of air that goes into cylinders, Engines Intake Manifold with a resulting in an unfavorable higher rate of exhaust emissions like CO. It has also been found that the Flexible Crankshaft. Energies 2021, 14, 1287. https://doi.org/10.3390/ pressure of the gas inside the cylinder during the intake stroke has four elements: a driving element en14051287 (intake manifold pressure) and draining elements (vacuum pressure and flow losses and inertial effect of rotating mass). The element of the least effect amongst these four elements is the vacuum Academic Editors: pressure that results from the piston’s inertia and acceleration. The element of the largest effect is the Constantine Rakopoulos and pressure drop that takes place in the cylinder because of the air/gas flow losses. These developed Ali Elkamel models are explainable and widely valid so that they can help in better analyzing the performance of diesel engines. Received: 17 November 2020 Accepted: 25 January 2021 Keywords: nonlinear dynamics; fluid mechanics; diesel engine performance; exhaust emissions; Published: 26 February 2021 modeling and simulation Publisher’s Note: MDPI stays neutral with regard to jurisdictional claims in published maps and institutional affil- Article Highlights iations. 1. Validated Analytical model of the mass flow rate of air goes into cylinders with a flexible crankshaft; 2. Flexibility of the crankshaft decreases the mass flow rate of air that goes into cylinders, resulting in unfavorable higher rate of exhaust emission; Copyright: © 2021 by the authors. 3. Cylinder pressure during intake stroke has four elements: a driving element (intake Licensee MDPI, Basel, Switzerland. manifold pressure) and draining elements (vacuum pressure, flow losses and inertial This article is an open access article distributed under the terms and effect of rotating mass). conditions of the Creative Commons 1. Introduction Attribution (CC BY) license (https:// creativecommons.org/licenses/by/ The continual demand for diesel powertrain development is due to the distinguished 4.0/). operating features the diesel powertrains exhibit [1]. As a cost-effective tool for developing Energies 2021, 14, 1287. https://doi.org/10.3390/en14051287 https://www.mdpi.com/journal/energies Energies 2021, 14, 1287 2 of 20 diesel powertrains, modeling assumes a key role in such endeavor [2,3]. This is particularly true for Intelligent Transportation Systems (ITS) [4,5]. Due to its relative location, intake manifold significantly influences the performance of the rest of the elements of diesel powertrain so that its modeling comes first with respect to diesel powertrain. The research area of mechanical energy modeling and analysis still has been a hot area of research. This is evident in very recent research papers developed at highly esteemed institutions such as [6,7]. In addition, very recently the featured paper in the “Energies” journal—Volume 14—Issue 1 in 2021, has been on diesel engines performance. This indicates that this area of research is still a hot topic that is still investigated by highly esteemed European institutions such as [8]. The intake manifold along with the crankshaft, which are interconnected through the engine cylinder assembly, significantly influence the net power of the engine. There- fore, the modeling of their interconnection becomes critical. Because the flexibility of the crankshaft is an intrinsic characteristic of the dynamics of the crankshaft, the influence of such flexibility should also be modeled. Guzzella et al. [9] reported that there are two categories of modeling the engine dynamics: (1) Mean Value Model which spreads out major processes in the engine for modeling the input-output behavior with good accuracy but low computational cost; (2) Discrete Event Model which explicitly describes the reciprocating behavior of the engine. However, for the cylinder and intake manifold, the mean value models do not show the influence of the crank angle. In addition, Guzzella et al. did not present a discrete event model of the air mass flow rate in intake manifold and engine’s cylinder as a function of crank angle analytically. Acquati et al. [10] proposed a mean value model of the air flow and pressure in the intake manifold of spark ignition engines. However, the mean value model does not show the influence of the crank angle on the mass flow rate of air in the engine’s cylinder and on the gas speed dynamics in the engine’s cylinder. Among the key models in this field is the model developed by Ouenou-Gamo et al. [11] that analytically modeled the air intake process in a turbocharger diesel engine using the camshaft angular position. That study showed the influence of the turbocharger on the manifold and on the cylinders’ parameters during their filling. However, that model neglects the gases’ kinetic energy and the gas flow’s momentum conservation. Other researchers tried to explain the mechanism of fuel consumption that influences the actual Air/Fuel ratio based on understanding the collision behavior of fuel drops in the cylinder of diesel engines [12]. Aguilera-Gonza et al. [13], developed a pressure model based on fuzzy logic for regu- lating the intake manifold pressure in a four-cylinder diesel engine air-path system with Exhaust Gas Recirculation (EGR) and Variable Geometry Turbocharger (VGT). However, that model did not show analytically the influence of the intake manifold’s pressure on the dynamics of the crankshaft. Considering irreversible thermodynamic processes, Mehta and Bharti [14] presented irreversible Otto cycle model for net power generation and efficiency calculation by includ- ing bypass heat leakage, frictional losses and internal irreversibility factors associated with compression and expansion process. They showed that the power is independent of heat leakage term but is affected by irreversibility in terms of flow losses and frictional losses. The technology of a balance shaft with eccentric weight for offsetting the vibrations of the crankshaft has been also modeled. In this line of modeling, Kumhar et al. [15] have identified the two sources of diesel engine’s vibrations: (i) vibrations because of rotating and reciprocating inertial forces that act on the crankshaft and the parts connecting with it, (ii) Torsional vibration of the crankshaft due to combustion pulses. Kumhar et al., proposed a computational model of a balancer shaft with eccentric masses to counter balance these two vibrational forces. However, they have not shown analytically the influence of the intake manifold’s pressure on the dynamics of the crankshaft. Energies 2021, 14, 1287 3 of 20 Chaubey and Tiwari [16] also developed a computational model but of the intake manifold of a four-cylinder engine. They showed the effects of shape of runners on the intake manifold’s output. However, that research did not analytically model the mass flow rate of air in the engine’s cylinder nor did it analytically model the gas dynamics in the engine’s cylinder. Vojtíšek and Kotek [17] compared real driving measurement of air flow in gasoline engines as well as in diesel engines with a generic analytical model of the mass flow rate based on volumetric efficiency and throttling. They reported that the relative error of such a model exceeds 10%. However, the paper did not take into account the effect of the flexibility of the crankshaft on the mass flow rate of air in the engine’s cylinder. Rakha et al. [18] indicated that a widely valid and microscopic model of diesel engines is yet sought for evaluating the diesel powertrain technologies. Faris et al. [19] therefore modeled analytically the intake manifold of supercharged diesel engines treating the crankshaft of the engine as an inflexible shaft. However, the flexibility of the crankshaft was not taken into consideration in that modeling. Albeit vehicle analytical modeling describes the physical phenomena associated with engines with explainable mathematical trends, no analytical model has been developed as yet of the supercharged diesel intake manifold taking into account the flexibility of the crankshaft. The significance of this research is indicated in light of recent research that reflects the importance of the line of research of the effect of gas pressure on diesel engines performance to the research community [20].
Details
-
File Typepdf
-
Upload Time-
-
Content LanguagesEnglish
-
Upload UserAnonymous/Not logged-in
-
File Pages20 Page
-
File Size-