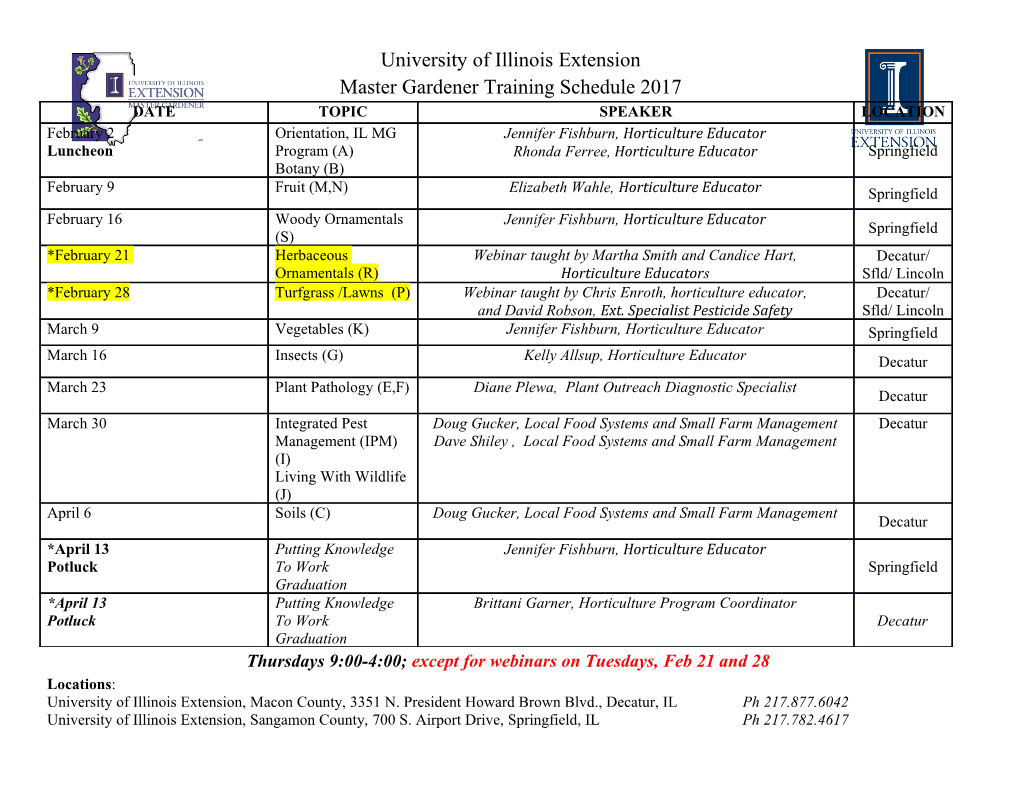
Journal of Engineering Research and Studies E-ISSN 0976-7916 Research Article APPLICATION OF CAD IN RAPID PROTOTYPING TECHNOLOGY 1Mr.Sanjay C. Kumawat, 2Mrs. A.L.Gawali Address for Correspondence 1Lecturer in mechanical Department, J.T.M.College Of Engg.Faizpur, Jalgaon 2Lecturer in Mechanical. Department, SSGBCOE&T Bhusawal (MH) ABSTRACT Now a day, one of the critical factors in competitive technology is “time to market” along with foolproof design. This critical factor indicates the entire product design cycle from concept to product design to prototype to manufacturing process design to actual implementation. To have command over this critical factor Computer aided designing (CAD) and manufacturing (CAM) is taking hold as a mean of speeding the time to market for new product development. This paper described how CAD approach is used in Rapid Prototyping techniques (RPT) for design and development of new products. Use of this CAD techniques in RPT techniques shorten the time to market and further for research and development of time of new products. KEYWORDS: CAD/CAM, Rapid Prototyping Technology (RPT) 1.0 INTRODUCTION analyzed and modified just considering like physical Computer-Aided-Design (CAD) involves the use of prototype [4]. computers to create product design drawing and 3D 2.3 Third Phase: Rapid Prototyping models. This CAD is associated with interactive Rapid Prototyping of physical parts, also known as, computer graphics. CAD system is powerful tool and desktop manufacturing, free-form fabrication, or layer used in mechanical design, and geometrical modeling manufacturing technology represents the third phase in of products and components. Computer-Aided- the evolution of prototyping [4]. Manufacturing (CAM) involves the use of computer 3.0. Introduction to Rapid Prototyping technology to assist in all the phases of manufacturing Rapid Prototyping is an important recent advancement a product, including process and production planning, in manufacturing. The Rapid Prototyping is a process machining, scheduling, management, and quality by which a solid physical model of a part is made control. These two-system i.e. CAD/CAM are directly form a 3-dimensional CAD drawing. The term combined to get added benefit. The database developed rapid prototyping (RP) also refers to a class of during CAD is stored and then CAM processes it technologies that can automatically construct physical further, into the necessary data and instructions for models from Computer-Aided Design (CAD) data. product quality [2]. Rapid Prototyping Technology This technique was developed in mid-1980s [8]. Rapid (RPT) is developed in 1988. RP enable the prototyping is an "additive" process, combining layers development of a geometrically exact replica of a part of paper, wax, or plastic to create a solid object. In in matter of hours, as compare to days or weeks using contrast, most machining processes (milling, drilling, traditional model-shop techniques. Rapid prototyping grinding, etc.) are "subtractive" processes that remove of physical parts also known as solid free from material from a solid block. RP’s additive nature fabrication, desktop manufacturing or layer allows it to create objects with complicated internal manufacturing technology [1]. features that cannot be manufactured by other means. 2.0 Prototyping Definition These "three dimensional printers" allow designers to A prototyping is the first or original example of quickly create tangible prototypes of their designs, something that has been or will be copied or rather than just two-dimensional pictures. Such models developed; it is a model or preliminary version [4]. have numerous uses. They make excellent visual aids There are three phases of prototyping as described for communicating ideas with co-workers or follows. customers. In addition, prototypes can be used for 2.1 First Phase: Manual (or hard) prototyping design testing. For example, an aerospace engineer The first phase began many centuries ago. In this might mount a model airfoil in a wind tunnel to phase, prototypes are typically not very sophisticated measure lift and drag forces [4]. Of course, "rapid" is a and fabrication of prototype takes on average about relative term. Most prototypes require from three to four weeks. The techniques used in making these seventy-two hours to build, depending on the size and prototypes tend to be craft-based and extremely labour complexity of the object. This may seem slow, but it is intensive [4]. much faster than the weeks or months required to make 2.2 Second Phase: Soft or Virtual prototyping. a prototype by traditional means such as machining. In this phase, computer models were created using These dramatic time savings allow manufacturers to CAD modeling software and can be tested, stressed, bring products to market faster and more cheaply. At JERS/Vol.II/ Issue IV/October-December, 2011/252-257 Journal of Engineering Research and Studies E-ISSN 0976-7916 least six different rapid prototyping techniques are (magnetic resonance imaging) and x-ray data, and laser commercially available, each with unique strengths [7]. and digitizing arm scans. 4.0 Benefits of Rapid Prototype Technique [RPT]. Representation methods used to describe CAD Helps in complete visualization of the physical geometry vary from one system to another. A standard model. interface is needed to convey geometric descriptions Communicating desired form, fit, and function. from various CAD packages to RP systems. The STL Providing feedback about ergonomic and (StereoLithography) file i.e. (. STL file) consists of an aesthetic requirements. unordered list of triangular facets representing the Providing an example to a vendor for quotation. outside skin of an object. There are two STL file Facilitating quick changes in a design (especially formats. One is the ASCII format and the other is true for castings). binary format. The size of an ASCII STL file is lager Reduced cycle times and increased innovation. than that of the binary format but is human readable we can build mold components directly from the [2]. CAD geometry In an STL file, triangular facets are described by a set 5.0 Applications of Rapid Prototype Technique. of X, Y, and Z co-ordinates for each of the three In design verification vertices and a unit normal vector with x, y, and z to • In product development. indicate which side of facet is an inside the object. An • In engineering Analysis example is shown in Fig. 3. • In Manufacturing Tooling. • Aerospace Industry. • Automotive Industry. • Dental device development. • Biomedical Industry. • Jewelry Industry. • Coin Industry. • Tableware Industry. • Electronic products. 6.0 Limitations of Rapid Prototype Technique. Fig. 1 CAD Approach for Rapid Prototyping • Limitation on maximum size of the model. Large parts usually must be built separately and connected manually. • Larger parts can be quite expensive. • Limited material properties. • Varying accuracy between the x-, y-planes and the z-plane. • Because parts are built in sections, the properties may not be very isotropic. • Initial investment and maintenance cost is high. 7.0 .STL file as a prototype data 3D Systems developed the STL file format to transfer Fig .2 The basic procedure for RP modeling geometry to the SLA machine. STL files are faceted There are several advantages with the STL file. Firstly, representations of data composed of triangles. The data it provides a simple method of representing 3- for the STL file can come from a variety of sources: a dimensional CAD data. Secondly, it is a de facto solid CAD model, a sewn (air-tight) surface quilt, MRI standard, which is used in most of the CAD systems (magnetic resonance imaging) and x-ray data, and laser and RP systems. Finally, it can provide simple files for and digitizing arm scans. data transfer for geometric shapes [3]. Several 7.0 .STL file as a prototype data disadvantage of the STL file exist. Firstly, the STL file 3D Systems developed the STL file format to transfer is many times larger than the original CAD data file for geometry to the SLA machine. STL files are faceted a given accuracy parameter. The STL file carries much representations of data composed of triangles. The data redundant information such as duplicate vertices and for the STL file can come from a variety of sources: a edges. solid CAD model, a sewn (air-tight) surface quilt, MRI JERS/Vol.II/ Issue IV/October-December, 2011/252-257 Journal of Engineering Research and Studies E-ISSN 0976-7916 Fig. 3 STL file with triangular facets 8.0 The Basic Process for all Rapid Prototype manageability to produce a useful STL file. In the Technique. third step , a pre-processing program prepares the STL Although several rapid prototyping techniques exist, all file to be built. Several programs are available, and employ the same basic five-step process. The steps are most allow the user to adjust the size, location and as described follows. orientation of the model. Build orientation is important 1) Create a CAD model of the design. for several reasons. First, properties of rapid prototypes 2) Convert the CAD model to STL format. vary from one coordinate direction to another. For 3) Slice the STL file into thin cross-sectional layers. example, prototypes are usually weaker and less 4) Construct the model one layer atop another. accurate in the z (vertical) direction than in the x-y 5) Clean and finish the model. plane. In addition, part orientation partially determines First step , the object to be built is modeled using a the amount of time required to build the model. Placing Computer-Aided Design (CAD) software package. the shortest dimension in the z direction reduces the Solid modelers, such as Pro/ENGINEER, Solid Works, number of layers, thereby shortening build time. The Inventor, and Catia tend to represent 3-D objects more preprocessing software slices the STL model into a accurately than wire-frame modelers such as number of layers from 0.01 mm to 0.7 mm thick, AutoCAD, and will therefore yield better results.
Details
-
File Typepdf
-
Upload Time-
-
Content LanguagesEnglish
-
Upload UserAnonymous/Not logged-in
-
File Pages7 Page
-
File Size-