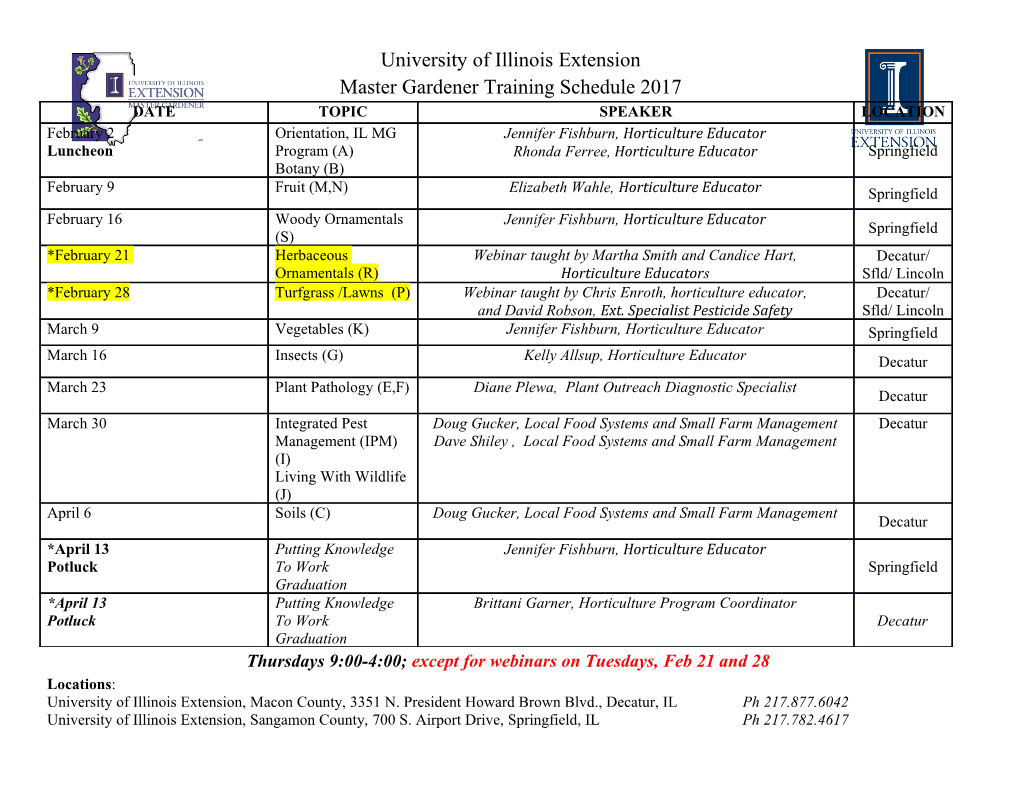
Patented Aug. 16, 1949 2.478,916 UNITED STATES PATENT OFFICE 2,478,916 REFORMING PRocess Vladimir Haensel, Clarendon Hills, and Curtis F. Gerald, Riverside, E., assignors to Universa Oil Products Company, Chicago, I., a corporation of Delaware No Drawing. Application December 21, 1946, Serial No. 71,659 13 Claims. (Cl 196-50) 2 This invention relates to a reforming process mally liquid hydrocarbons substantially or con and more particularly to a process for the re pletely into normally gaseous hydrocarbons. forming of a saturated gasoline fraction in the The desired selective cracking generally com presence of a particular catalyst and under se prises the removal of methyl, ethyl and, to a lected conditions of operation. lesser extent, propyl groups, in the form of The saturated gasoline fraction to be treat methane, ethane and propane as will be herein ed in accordance with the present invention after described. However, the removal of these comprise straight run gasolines, natural gaso radicals is controlled so that not more than. One lines, etc. The gasoline fraction may be a full or possibly two of such radicals are removed boiling range gasoline having an initial boiling O from a given molecule. For example, heptane point within the range of about 50 to about may be reduced to hexane, nonane to Octane or 90 F. and an end boiling point within the heptane, etc. On the other hand uncontrolled range of about 375 to about 4.25° F., or it may or non-selective cracking will result in the de be a selected fraction thereof which usually will composition of normally liquid hydrocarbons be a higher boiling fraction, commonly referred into normally gaseous hydrocarbons as, for ex to as naphtha, and generally having an initial ample, by the continued demethylation of nor boiling point of from about 150 to about 250 F. mal heptane to produce 7 molecules of methane. and en end boiling point within the range of Another important objection to the non-selec about 350 to about 425 F. tive or uncontrolled cracking is that this type of The term “reforming' is well known in the 20 cracking will result in the more rapid formation petroleum industry and refers to the treatment of larger quantities of coke or carbonaceous ma of gasoline fractions to improve the anti-knock terial which deposits on the catalyst and de characteristics. Straight run gasolines contain creases or destroys its activity to catalyze the naphthenic hydrocarbons, particularly cyclo desired reactions. This in turn results in shorter hexane Compounds, and paraffinic hydrocar 25 processing cycles or periods, with the necessity bons which usually are of straight chain or of more frequent regeneration of the catalyst by slightly branched chain structure, as well as burning the carbonaceous products therefrom or, varying proportions of aromatic hydrocarbons. should the catalyst activity be destroyed, it will In order to obtain best results in reforming op be necessary to shut down the unit to remove erations it is desired to dehydrogenate the naph 30 the old catalyst and replace it will new catalyst. thenic hydrocarbons to produce aromatics, to Another important feature in successful re cyclisize the straight chain paraffinic hydrocar forming processes is the matter of hydrogen bons to form aromatics, as well as to effect a production and consumption. Investigation has controlled type of cracking which is selective shown that the presence of hydrogen in the re both in quality and in quantity. In addition 3 5 forming Zone further tends to decrease the various other concomitant reactions occur such amount of carbonaceous deposits on the cata as isomerization, hydrogen transfer, etc. lyst. Reforming processes effected in the pres The cracking or splitting of carbon to carbon ence of hydrogen are known as "Hydroforming.' bonds is one of the important factors in success In view of the fact that the cost of hydrogen is ful reforming process. Controlled or selective 40 quite high, it is essential that there be no net Cracking is highly desirable since such cracking Consumption of hydrogen or, in other words, at will result in a product of improved antiknock least as much hydrogen must be produced in the characteristics. In general, the lower molecu process as is consumed therein. lar weight products have higher octane num In a broad aspect the present invention relates bers, and thus a final gasoline product of lower 45 to a process for reforming a straight run gasoline average molecular weight will usually have a fraction which comprises subjecting said frac higher octane rating. Further, during the tion to contact at reforming conditions with a Cracking reaction, isomerization or other molec catalyst prepared by compositing from about lular rearrangement occurs which also results in 0.2 gram to about 2 grams per 100 cubic centi products having higher antiknock characteris meters of final catalyst of a metal selected from tics. The selective cracking is also of particular the group consisting of platinum and palladium advantage when the charging stock contains with a dry cracking component. components boiling above about 400° F. in or In a specific embodiment the present invention der to convert these components to fraction boil relates to a process for reforming a straight run ing below about 400 F. It is thus seen that the gasoline fraction which comprises subjecting selective cracking results not only in an im said gasoline fraction to contact at a tempera proved quality product but also in an increase ture of from about 500 to about 875° F, and a in quantity of the desired products. pressure of from about atmospheric to about However, the cracking must be selective and 1000 pounds per square inch, at on hourly liq must not result in the decomposition of the nor 60 uid space velocity of from about 0.1 to about 8,478,916 3 4. 5, in the presence of from about 0.5 to about 10 tion of the salt as the case may permit. The mols of hydrogen, with a catalyst prepared by slica-alumina-zirconia catalyst may be formed compositing from about 0.2 gram to about 2 by adding the aluminum and/or zirconium salts grams of platinum per 100 cubic centimeters of together or separately. The catalyst may be in a dry silica-alumina composite. the form of granules of irregular size and shape The catalyst used in the present invention or the ground granules may beformed into pellets comprises platinum or palladium in amounts of of uniform size and shape by pilling, extrusion or from about 0.2 gram to about 2 grams per 100 other suitable methods. cubic centimeters of the final catalyst. Concen A particularly satisfactory method of forming trations of these metals below about 0.2 gram O the Cracking component is to add the acid to per 100 cc. are too low for satisfactory reform commercial water glass at a pH controlled to ing operations while, on the other hand, con form silica hydrogel, discharging the mixture of centrations of platinum above about 2 grams acid and water glass from a rotating disc or nozzle per 100 cc. are unsatfisfactory because they pro into a bath of oil of sufficient depth so that the duce excessive cracking. Therefore, it is an es 5 silica hydrogel sets into firm spheres during pas sential feature of the present invention that the Sage through the oil bath. The spheres may be concentrations of platinum or palladium in the removed from the bath in any suitable manner, catalyst shall be within the range of about 0.2 such as by being transported in a stream of water gram to about 2 grams per 100 cubic centimeters disposed beneath the oil layer. The silica spheres of the final catalyst. 20 may then be treated in any suitable manner to Due to the high cost of platinum and palladium, remove Sodium ions, followed by impregnating a major factor in the use of catalysts containing with a solution of soluble metal salt or salts. these metals is the quantity thereof to be used. In another embodiment silica-alumina spheres, As will be noted, the improved process of the silica-magnesia spheres, etc., may be formed by present invention requires Small quantities of 25 co-precipitation methods in a similar system. these metals. However, as the densities of the As another essential feature of the present in different cracking components vary considerably, vention it has been found that the cracking com the quantity of platinum or palladium in the ponent must be dried at a temperature of at least present specification and claims has been speci 350 F. before the platinum is composited there fied on the basis of grams thereof per cubic cen 30 with. This will be shown in detail in the follow timeters of final catalyst. The final catalyst ing example, from which it will be noted that charged to the process is usually determined as catalysts prepared by compositing platinum with so much volume required to fill a given portion dry silica-alumina yield products of high octane of the reaction zone, and the present method of number, whereas catalysts prepared by composit specifying the platinum or palladium concentra 35 ing platinum with undried silica-alumina result tion readily shows the quantity of these metals in products having a much lower octane number. required. The cracking component may be dried at a tem As another feature of the present invention, perature of from about 350° to about 500 F., we have found that the component to be com and/or calcined at a temperature of from about posited with the platinum or palladium must have 40 500 to about 1400" F.
Details
-
File Typepdf
-
Upload Time-
-
Content LanguagesEnglish
-
Upload UserAnonymous/Not logged-in
-
File Pages6 Page
-
File Size-