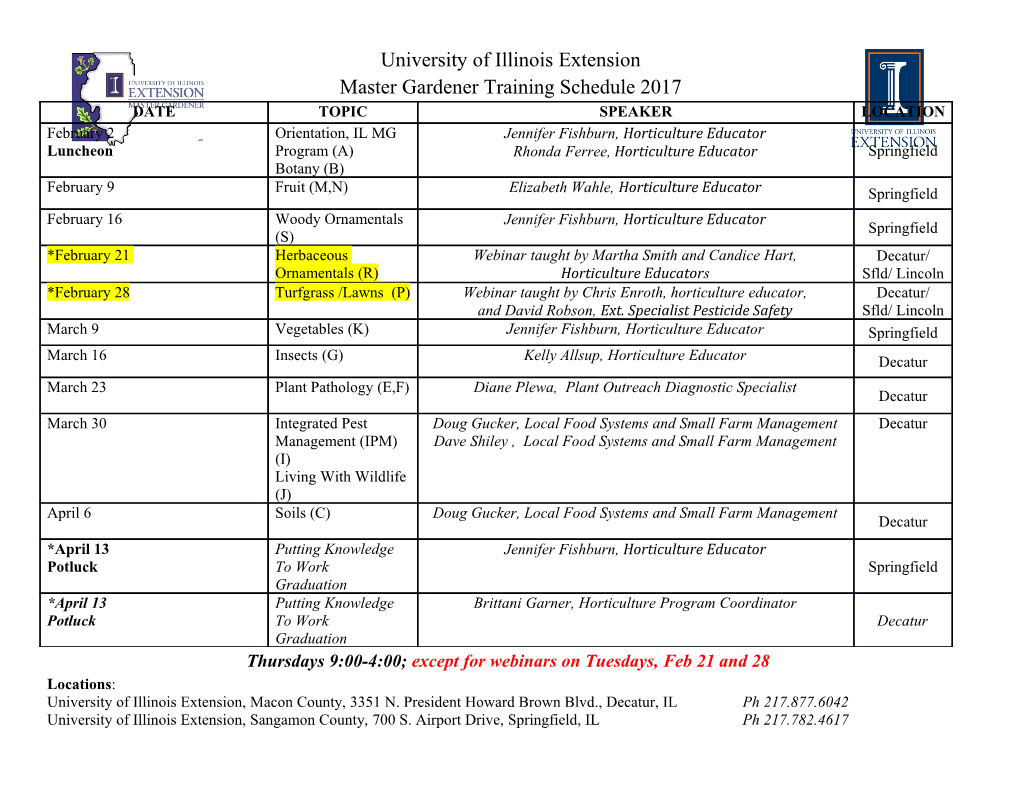
Home Search Collections Journals About Contact us My IOPscience Scanning probe nanoimprint lithography This article has been downloaded from IOPscience. Please scroll down to see the full text article. 2010 Nanotechnology 21 075305 (http://iopscience.iop.org/0957-4484/21/7/075305) View the table of contents for this issue, or go to the journal homepage for more Download details: IP Address: 130.209.6.43 The article was downloaded on 25/04/2012 at 17:02 Please note that terms and conditions apply. IOP PUBLISHING NANOTECHNOLOGY Nanotechnology 21 (2010) 075305 (6pp) doi:10.1088/0957-4484/21/7/075305 Scanning probe nanoimprint lithography F Dinelli1, C Menozzi2,4, P Baschieri1, P Facci2 and P Pingue3,5 1 IPCF, Consiglio Nazionale delle Ricerche, CNR Campus, Via G. Moruzzi 1, Pisa PI 56100, Italy 2 CNR-INFM S3 National Research Center on Nanostructure and BioSystems at Surfaces, Via Campi 213/a, 41100 Modena, Italy 3 NEST, Scuola Normale Superiore and CNR-INFM, Piazza San Silvestro 12, I-56127 Pisa, Italy 4 Dipartimento di Fisica, Universit`a di Modena e Reggio Emilia, Via Campi 213/a, 41100 Modena, Italy E-mail: [email protected] Received 5 November 2009, in final form 23 December 2009 Published 21 January 2010 Online at stacks.iop.org/Nano/21/075305 Abstract The present paper reports on a novel lithographic approach at the nanoscale level, which is based on scanning probe microscopy (SPM) and nanoimprint lithography (NIL). The experimental set-up consists of an atomic force microscope (AFM) operated via software specifically developed for the purpose. In particular, this software allows one to apply a predefined external load for a given lapse of time while monitoring in real-time the relative distance between the tip and the sample as well as the normal and lateral force during the embossing process. Additionally, we have employed AFM tips sculptured by means of focused ion beam in order to create indenting tools of the desired shape. Anti-sticking layers can also be used to functionalize the tips if one needs to investigate the effects of different treatments on the indentation and de-molding processes. The lithographic capabilities of this set-up are demonstrated on a polystyrene NIL-patterned sample, where imprinted features have been obtained upon using different normal load values for increasing time intervals, and on a thermoplastic polymer film, where the imprint process has been monitored in real-time. Studies of polymeric films by means of atomic force measure normal and lateral forces. AFM can thus provide microscopy (AFM) [1] have begun almost immediately after topographical, mechanical and adhesion properties of the the technique’s inception [2]. These investigations have sample investigated [12, 13], making it an ideal tool for dealt with a wide range of issues, from the molecular lithographic applications. In the end, it can be stated that NI organization [3] to wear [4], lithography [5] and mechanical and AFM techniques can be found very useful for studying properties [6]. This has originated from the absolute novelty surface properties, used separately or in combination. represented by investigating non-conductive surfaces on the The initial aim of the work herein presented was nanoscale. In parallel, the development of the nano-indenter to develop a novel approach that might allow one to (NI) [7] has provided the scientific community with another perform scanning probe nanoimprint lithography (SP-NIL). powerful tool for material characterization. The two techniques Specifically, we intended to investigate the phenomena have different characteristics and each one can be appropriated occurring during the process of pattern formation when a stamp for addressing different material properties. On the one is placed in contact with a polymeric film as in standard hand, NI can provide a quantitative analysis of Young’s and NIL. Towards the accomplishment of this goal, we have plastic moduli, not achievable with the same accuracy with individuated AFM as the most suitable tool due to its imaging, AFM [8, 9]. For instance, Cross and co-workers have recently alignment and positioning capabilities, its high sensitivity to demonstrated the NI capabilities of studying thin films on adhesive forces and dynamics analysis [14]. We have thus rigid substrates [10, 11]. On the other hand, AFM, initially developed for imaging rather than testing surface properties, is assembled an experimental set-up that allows one to define the very sensitive to small force values and one can simultaneously indentation parameters and to monitor the cantilever deflection and torsion during the indentation process. In particular, we 5 Author to whom any correspondence should be addressed. have introduced in standard force versus distance curves the 0957-4484/10/075305+06$30.00 1 © 2010 IOP Publishing Ltd Printed in the UK Nanotechnology 21 (2010) 075305 F Dinelli et al Figure 1. (A) Schematics of the experimental set-up. The cantilever is mounted on a piezo-tube. SEM images of a tip modified by means of FIB in order to create a square-shaped punch for indenting and a small tip for imaging: (B) low magnification lateral view; (C) top view; (D) high magnification lateral view. ‘hold’ time, defined as the lapse of time during which the tip cycle typically observed for any piezoelectric material. This and the surface are in contact under a given load. We have also phenomenon reflects itself in the two branches of the force used a focused ion beam (FIB) to modify AFM tips in order to versus distance curves: they do not fully superimpose although make them suitable for both imaging and indenting [15, 16]. the x-axis values are nominally the same ones. For a correct The experimental set-up is briefly described in the data analysis, one needs to record force versus distance curves following (see schematics in figure 1(A)). The microscope on a rigid surface as reference (e.g. silicon oxide) [18]. Due head is a commercial one (SMENA, NT-MDT). In the reported to the high stiffness of the rigid surface, one can assume that configuration, the cantilever is always moved with respect to the deformation of the two bodies is negligible and that all the the sample when imaging or indenting. The cantilever/sample displacement between the cantilever base and the specimen is alignment can be adjusted in two ways: with a screw that tilts converted into cantilever deflection. Under this assumption, the plane where the AFM head stands along the direction of one can calibrate the optical lever detection system. As the cantilever long axis; or with the three legs of the AFM described above, for a complete monitoring of the whole head that can be independently shortened or lengthened. The process, an additional parameter has been implemented in our electronics (based on a DSP) and software have both been software. It allows one to set a certain thold during which the developed in our laboratory [17]. They allow one to approach tip is maintained in contact with the surface at a given Fset. the tip to the sample and stop at a given force value that we This approach is derived from force clamp experiments [19] call the ‘maximum load’ (Fmax). At this moment a feedback where the cantilever deflection and torsion are monitored while circuit is activated, keeping the normal force constant at a value keeping the load constant. thold is also very similar to the previously set (Fset). Fmax and Fset can be varied in order to so-called ‘dwell time’ that is defined in e-beam lithography reduce undesired effects due to creep of the piezo-actuator. The (EBL) or in dip pen nanolithography (DPN) [20]. During this normal load is maintained at Fset for a variable lapse of time interval, we are therefore able to monitor and record data such called in the following the ‘hold’ time (thold), during which the as the cantilever deflection and torsion as well as the vertical vertical displacement and the lateral forces are recorded. displacement of the tip with respect to the sample. The actuator of our AFM head is a tube made of As mentioned earlier, one of our goals was to mimic and piezoceramic material. The tube elongation is not linear study the NIL process. It is known that homogeneous NIL with the applied voltage and is characterized by a hysteresis on large areas can be rather difficult to perform. Besides 2 Nanotechnology 21 (2010) 075305 F Dinelli et al alignment issues, problems still unsolved regard fluid-dynamic phenomena of polymers filling the mold. Addressing this issue at the nanoscale level would be beneficial to finding viable solutions. We have thus designed tips with the desired shapes as a way to realize indenters directly on AFM cantilevers. In order to shape the tip according to our purposes, an FIB system has been employed [16]. This procedure can be in principle applied to any tip, shaping it in nearly any arbitrary fashion. In this first exemplifying experiment, we have decided to employ a very stiff cantilever in order to perform the NIL process on a polymeric sample at room temperature, where high pressure is required to produce significant embossing. In more detail, the employed cantilever had an elastic constant of ∼38 N m−1. Figures 1(B)–(D) show SEM images of the tip used to collect the data presented. One can see that a square punch has been fabricated at the apex of the cone and that a smaller tip has also been realized in the same region for imaging purposes. The plane where the two objects lie forms an angle of about 10◦ with respect to the cantilever long axis (figure 1(B)). This modification has been devised in order to facilitate the alignment of the scanning plane with the specimen.
Details
-
File Typepdf
-
Upload Time-
-
Content LanguagesEnglish
-
Upload UserAnonymous/Not logged-in
-
File Pages7 Page
-
File Size-