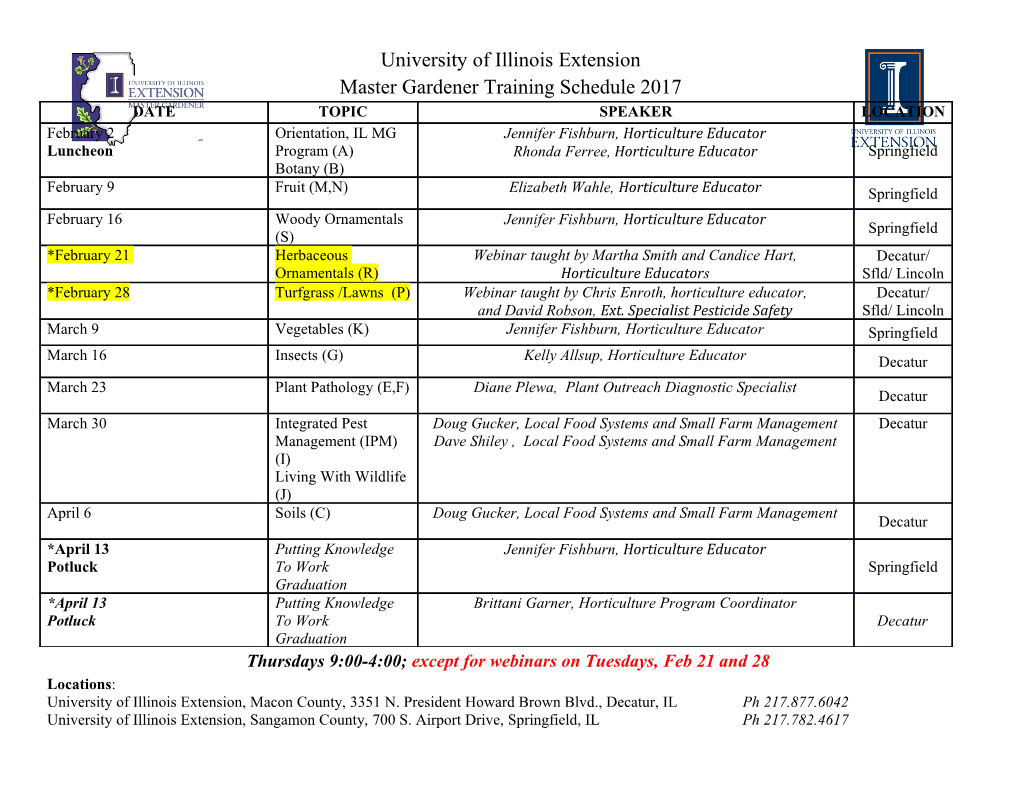
International Journal of Advanced Science and Technology Vol. 29, No. 03, (2020), pp. 4629 - 4642 Optimization of Friction Welding Parameters in Dissimilar Materials using Taguchi’s Method Dr. R N. Ramanujam1, Dr. S. Krishnamohan2, 1,2Professor Dept of Mechanical Engineering E.G.S. Pillay Engineering College Nagapattinam Abstract At present there are various welding process is introduced among them there is Friction welding (FW) is a fairly recent technique that utilizes a non on sumable welding tool to generate frictional heat and plastic deformation at the welding location, There by affecting the formation of a joint while the material is in solid state. The technique can produce joints utilizing equipment based on traditional machine tool technologies, the main aim of this paper to obtained friction weld element of dissimilar material and optimizing the friction welding parameters in order tom establish the weld quality. Taguchi method is applied for optimizing the welding parameters to attain maximum tensile strength of the joint and hardness of the welded joint. It is widely used in aerospace and automotive industrial applications. The process parameters play a major role in determining the high tensile strength of the weld of dissimilar materials.1.Rotational speed, 2.Friction pressure, 3.Friction time, 4.Forge pressure. 1. I.NTRODUCTION: Welding is the process of joining two or more pieces of the same or dissimilar materials to achieve complete coalescence. It is the process of joining similar or dissimilar metals by the application of heat with or without the application of pressure and addition filler metal. The edges of the metal pieces to be welded are brought to plastic state by the heat or filler metal is added and on cooling, the pieces join together and a permanent joint is produced. There is various methods are available 1. GAS WELDING: classified as; Air acetylene welding, Oxy acetylene welding, Oxy hydrogen welding ,. Process gas welding 2. ARC WELDING: classified as;. Carbon ARC welding, flux cored ARC welding. Gas tungsten welding, plasma ARC welding, gas metal ARC welding , Shielding metal ARC welding 3. RESISTANCE WELDING: classified as Resistance spot welding, projection welding, Resistance seam welding , flash welding ,. upset welding , percussion welding ,High frequency resistance welding 5. OTHER WELDING PROCESS: classified as; Electro slag welding , Electron beam welding, Laser beam welding, Induction welding ,Thermit welding 6. SOLID STATE WELDING: classified as; Cold welding, diffusion welding, Explosion welding, forge welding,. friction welding , Hot pressure welding ,Roll welding, Ultra sonic welding 1.1 FRICTION WELDING A method of operating on a work piece comprises offering a probe of material harder than the work piece to the continuous surface of the work piece of the causing relative cyclic movement between the probe on the work piece will urging the probe and work piece together whereby frictional heat is generated as the probe enters the work piece so as to create a plasticized region ISSN: 2005-4238 IJAST 4629 Copyright ⓒ 2019 SERSC International Journal of Advanced Science and Technology Vol. 29, No. 03, (2020), pp. 4629 - 4642 in the work piece material around the probe, stopping the relative cyclic movement, and allowing the plasticized material to solidify around the probe. This technique, which we refer to as “friction welding” provides a very simple method of joining a probe to a work piece. 1.2. TYPES OF FRICTION WELDING: Linear Friction Welding Spin Welding Rotary Friction Welding Inertia Friction Welding Friction Surfacing Friction Stud Welding Friction Stir Welding Friction stir welding (FSW) is a novel welding technique invented by The Welding Institute (TWI) in 1991. FSW is actually a solid-state joining process that is a combination of extruding and forging and is not a true welding process. Since the process occurs at a temperature below the melting point of the work piece material, FSW has several advantages over fusion welding. Some of the process advantages are given in the following list: 1. FSW is energy efficient. 2. FSW requires minimal, if any, consumables. 3. FSW produces desirable microstructures in the weld and heat-affected zones 4. FSW is environmentally “friendly” (no fumes, noise, or sparks) 5. FSW can successfully join materials that are “unweldable” by fusion welding methods. 6. FSW produces less distortion than fusion welding techniques. Many dissimilar metal combination can be joined and there are a number of process variation including: 1.3.SPIN WELDING: Four different phases can be distinguished in the vibration welding process, the solid friction phase, the transient phase, the steady state phase, the cooling phase. 1. In the solid friction phase the heat is generated as a result of friction between two surfaces. This causes the polymer material to heat up until the melting point is reached. The heat generated is dependent on applied tangential velocity and pressure. 2. In the second phase a thin molten polymer is formed which grows as a result of ongoing heat generation. In this stage hest is produced by viscous dissipation. At first only a thin molten layer exists and consequently the shear rate and viscosity heating contribution are large. As the thickness of molten layer increases the degree of viscous heating decreases. 3. Thereafter (start of third phase) the melting rate equals the outward flow rate (steady state). As soon as the phase has been reached, the thickness of molten layer is constant. The steady state is maintained until a certain melt down depth has been reached, at which point the rotation is stopped. ISSN: 2005-4238 IJAST 4630 Copyright ⓒ 2019 SERSC International Journal of Advanced Science and Technology Vol. 29, No. 03, (2020), pp. 4629 - 4642 4. At this point (phase 4) the polymer melt cools and solidification starts, while film drainage still occurs since the welding pressure remains. After all the materials has solidified, drainage stops and join is formed. 1.4. APPLICATION OF FRICTION WELDING: It can be used for various applications: Commercial , Aerospace, Hydraulic, Automobiles, Bi-metal: 2. TAGUCHI METHOD The technique of laying out the conditions of experiments involving multiple factors was first proposed by the Englishman sir R.A. Fisher. The method is popularly known as the factorial design of experiment. A full factorial design will identify all possible combination for a given set of factors. Since most industrial experiment usually involve significant number of factors, a full factorial design results in a large number of experiment. To reduce the number of experiments to a practical level, only a small set from all the possibilities is selected. The method of selecting a limited number of experiments which produces the most information is known as a partial fraction experiments. Although this method is well, there are no general guidelines for its application or the analysis of the results obtained by performing the experiments. Taguchi constructed a special set of general design guidelines for factorial experiments that cover many application. Taguchi has envisaged a new method of conducting design of experiments which are based on well defined guidelines. This method uses a special set of array called orthogonal arrays. These standard arrays stipulate the way of conducting the minimal number of experiments which could give the full information of all the factors that affect the performance parameter. The crux of the orthogonal arrays method lies in choosing the level combinations of the input design variables for each experiment. 2.1. A TYPICAL ORTHOGONAL ARRAY There are many standard orthogonal arrays available, each of the arrays is meant for a specific number of independent design variables and levels. For example, if one wants to conduct an experiment to understand the influence of 3 different independent variables with each variable having 3 set values (level values), then an L9 orthogonal array might be the right choice. The L9 orthogonal array is meat for understanding the effect of 3 independent factors each having 3 factor level values. This array assumes that there is no interaction between any two factors. While in many cases, no interaction model assumption is valid, there the some cases where is a clear evidence of interaction. A typical case of interaction would be the interaction between the metrical properties and temperature 2.2. ORTHOGONAL AARRAY ISSN: 2005-4238 IJAST 4631 Copyright ⓒ 2019 SERSC International Journal of Advanced Science and Technology Vol. 29, No. 03, (2020), pp. 4629 - 4642 The table 2.1 shows an L9orthogonal array. There are totally 9 experiments to be conduct and each experiment is based on the combination of level values as show in the table. For example, the third experiment is conducted by keeping the independent design variable 1 at level1, variable 2 at level 3 and variable 3 at level 2.3 PROPERTIOES OF AN ORTHOGONAL ARRAY The orthogonal arrays have the following special properties that reduce number of experiments to be conducted. The vertical column under each independent variable of the above has a special combination of level settings. All the level settings appear an equal number of times. For L9 array under variable3, level 1, level 2 and level 3appears thrice. This is called the balancing property of orthogonal arrays. All the level values of independent variable are used for conducting the experiments. 3. The sequence of level values for conducting the experiments shall not be changed. The reason for this is that the arrays of each factor columns are mutually orthogonal to any other column of level values. The inner product of vectors corresponding to weight is zero. If the above 3 levels ISSN: 2005-4238 IJAST 4632 Copyright ⓒ 2019 SERSC International Journal of Advanced Science and Technology Vol. 29, No. 03, (2020), pp. 4629 - 4642 are normalized between -1 and, then the weighing factors for level 1,level 2 , level 3 are -1 , 0 ,1respectively 2.4 MINIMUM NUMBER OF EXPERIMENTS TO BE CONDUCTED The design of experiments using the orthogonal array is, in most cases, efficient when compared to many other statistical designs.
Details
-
File Typepdf
-
Upload Time-
-
Content LanguagesEnglish
-
Upload UserAnonymous/Not logged-in
-
File Pages14 Page
-
File Size-