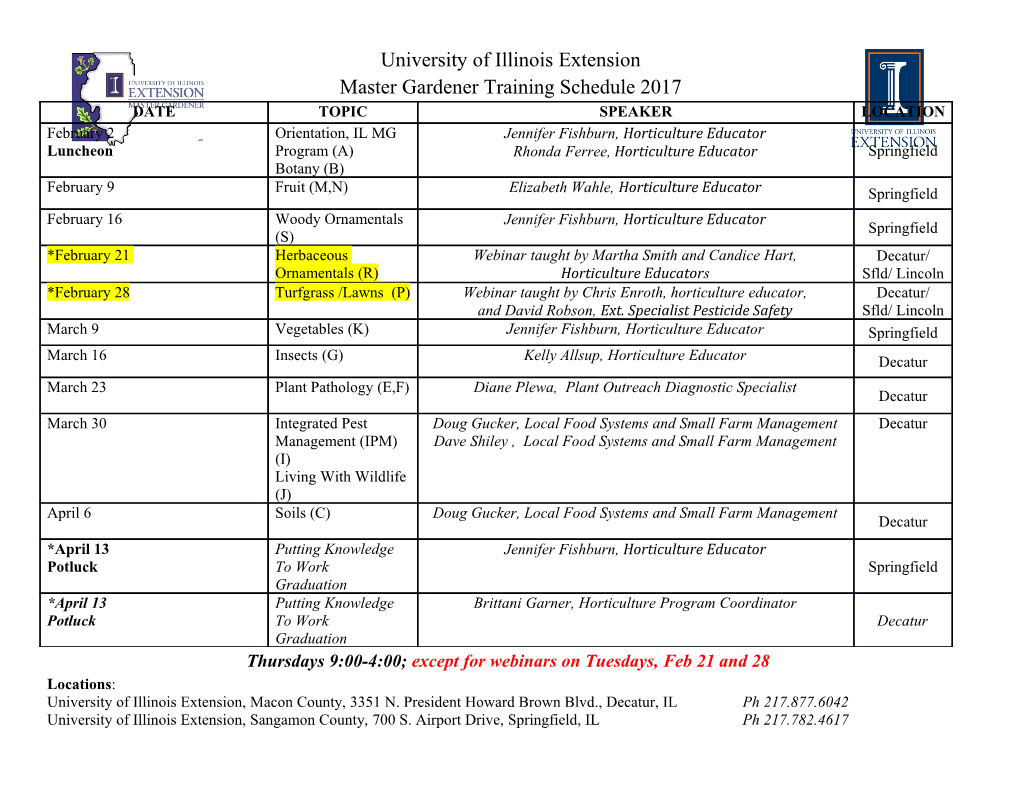
M02_KALP1681_06_SE_C02.QXD 1/12/09 7:46 PM Page 56 Mechanical Behavior, Testing, and Manufacturing Properties of CHAPTER 2 Materials 2.1 Introduction 56 2.2 Tension 57 • This chapter examines the effects of external forces on the behavior of materials, 2.3 Compression 66 and the test methods employed in determining various mechanical properties. 2.4 Torsion 67 • The tension test is described first. This test is commonly used for quantifying a 2.5 Bending (Flexure) 68 2.6 Hardness 68 number of material parameters, including elastic modulus, yield stress, ultimate 2.7 Fatigue 74 strength, ductility, and toughness. 2.8 Creep 75 • Compression tests are then described. These tests are useful because they more 2.9 Impact 75 2.10 Failure and Fracture closely simulate manufacturing processes; nonetheless, they have the unavoid- of Materials in able drawback of contributing friction to the testing. Manufacturing • Bending tests are particularly useful for brittle materials; three- and four-point and in Service 76 tests are in common use. 2.11 Residual Stresses 81 2.12 Work, Heat, and • Hardness and the variety of hardness tests and their applicability are then Temperature 82 explored. EXAMPLES: • Fatigue involves the failure of material due to cyclic or repeating loads, whereas 2.1 Calculation of Ultimate creep is deformation due to the application of a constant load over an extended Tensile Strength 63 period. 2.2 Calculation of Modulus of Resilience from • The chapter ends with descriptions of the types of, and factors involved in, failure Hardness 72 and fracture of materials. 2.1 Introduction In manufacturing operations, numerous parts and components are formed into dif- ferent shapes by applying external forces to the workpiece, typically by means of var- ious tools and dies. Common examples of such operations are forging turbine disks, extruding various components of aluminum ladders, drawing wire for making nails, and rolling metal to make sheets for car bodies. Forming operations may be carried out at room temperature or at elevated temperatures, and at a low or a high rate of deformation. These operations are also used in forming and shaping nonmetallic materials such as plastics and ceramics, as described throughout this book. As indicated in Fig. 1.2, a wide variety of metallic and nonmetallic materials is now available, with an equally wide range of properties, as shown qualitatively in Table 2.1. This chapter covers those aspects of mechanical properties and behavior of metals that are relevant to the design and manufacturing of products and includes commonly used test methods employed in assessing various properties. 56 M02_KALP1681_06_SE_C02.QXD 1/12/09 4:30 PM Page 57 Section 2.2 Tension 57 TABLE 2.1 Relative Mechanical Properties of Various Materials at Room Temperature, in Decreasing Order. Metals are in Their Alloy Form. Strength Hardness Toughness Stiffness Strength/Density Glass fibers Diamond Ductile metals Diamond Reinforced plastics Carbon fibers Cubic boron nitride Reinforced plastics Carbides Titanium Kevlar fibers Carbides Thermoplastics Tungsten Steel Carbides Hardened steels Wood Steel Aluminum Molybdenum Titanium Thermosets Copper Magnesium Steels Cast irons Ceramics Titanium Beryllium Tantalum Copper Glass Aluminum Copper Titanium Thermosets Ceramics Tantalum Copper Magnesium Reinforced plastics Reinforced thermosets Thermoplastics Wood Reinforced thermoplastics Tin Thermosets Thermoplastics Lead Thermoplastics Lead Rubbers 2.2 Tension The tension test is the most common method for determining the mechanical prop- erties of materials, such as strength, ductility, toughness, elastic modulus, and strain- hardening capability. The tension test first requires the preparation of a test specimen, as shown in Fig. 2.1a. Although most tension-test specimens are solid and round, they can also be flat or tubular. The specimen is prepared generally according Elastic Plastic Stress UTS Y Y Fracture Ϫ1 Offset tan E 0 eo eu ef Strain (for lo ϭ 1) ⌬l lo Ao le Original Uniform elongation gage lu length, lo lf Neck Fracture Total elongation Post-uniform elongation lf Af (a) (b) FIGURE 2.1 (a) A standard tensile-test specimen before and after pulling, showing original and final gage lengths. (b) A typical tensile-testing machine. M02_KALP1681_06_SE_C02.QXD 1/12/09 4:30 PM Page 58 58 Chapter 2 Mechanical Behavior, Testing, and Manufacturing Properties of Materials P to ASTM specifications; various other specifications Stress, s ϭ Ao Elastic Plastic are also available from corresponding organizations around the world. Ultimate tensile strength (UTS) Typically, the specimen has an original gage length, lo, generally 50 mm (2 in.), and a cross-sectional Yield stress (Y ) area, Ao, usually with a diameter of 12.5 mm (0.5 in.). Uniform It is mounted in the jaws of a tension-testing machine Necking Fracture elongation (Fig. 2.1b) equipped with various accessories and con- trols so that the specimen can be tested at different temperatures and rates of deformation. 2.2.1 Stress–Strain Curves l Ϫ l A typical deformation sequence in a tension test is Strain, e = o Offset lo shown in Fig. 2.2. When the load is first applied, the specimen elongates in proportion to the load, called FIGURE 2.2 A typical stress–strain curve obtained from a linear elastic behavior. If the load is removed, the spec- tension test, showing various features. imen returns to its original length and shape, in a man- ner similar to stretching a rubber band and releasing it. The engineering stress (nominal stress) is defined as the ratio of the applied load, P, to the original cross-sectional area, Ao, of the specimen: P s = . (2.1) Ao The engineering strain is defined as (l - lo) e = , (2.2) lo where l is the instantaneous length of the specimen. As the load is increased, the specimen begins to undergo nonlinear elastic deformation at a stress called the proportional limit. At that point, the stress and strain are no longer proportional, as they were in the linear elastic region, but when unloaded, the specimen still returns to its original shape. Permanent Unload (plastic) deformation occurs when the yield stress, Y, of the material is reached. Stress The yield stress and other properties of various metallic and nonmetallic materi- als are given in Table 2.2. For soft and ductile materials, it may not be easy to determine the exact lo- Load cation on the stress–strain curve at which yielding occurs, because the slope of the curve begins to decrease slowly above the proportional limit. Therefore, Y is Strain usually defined by drawing a line with the same slope as the linear elastic curve, Elastic recovery but that is offset by a strain of 0.002, or 0.2% elongation. The yield stress is then defined as the stress where this offset line intersects the stress–strain curve. This Permanent deformation simple procedure is shown on the left side in Fig. 2.2. As the specimen begins to elongate under a continuously increasing load, its cross-sectional area decreases permanently and uniformly throughout its gage FIGURE 2.3 Schematic illus- length. If the specimen is unloaded from a stress level higher than the yield stress, tration of the loading and the unloading of a tensile-test the curve follows a straight line downward and parallel to the original slope of specimen. Note that, during the curve (Fig. 2.3). As the load is increased further, the engineering stress eventu- unloading, the curve follows a ally reaches a maximum and then begins to decrease (Fig. 2.2). The maximum en- path parallel to the original gineering stress is called the tensile strength, or ultimate tensile strength (UTS), of elastic slope. the material. Values for UTS for various materials are given in Table 2.2. M02_KALP1681_06_SE_C02.QXD 1/12/09 4:30 PM Page 59 Section 2.2 Tension 59 TABLE 2.2 Mechanical Properties of Various Materials at Room Temperature Elongation in Poisson’s Metals (wrought) E (GPa) Y (MPa) UTS (MPa) 50 mm (%) ratio (v ) Aluminum and its alloys 69–79 35–550 90–600 45–4 0.31–0.34 Copper and its alloys 105–150 76–1100 140–1310 65–3 0.33–0.35 Lead and its alloys 14 14 20–55 50–9 0.43 Magnesium and its alloys 41–45 130–305 240–380 21–5 0.29–0.35 Molybdenum and its alloys 330–360 80–2070 90–2340 40–30 0.32 Nickel and its alloys 180–214 105–1200 345–1450 60–5 0.31 Steels 190–210 205–1725 415–1750 65–2 0.28–0.33 Titanium and its alloys 80–130 344–1380 415–1450 25–7 0.31–0.34 Tungsten and its alloys 350–400 550–690 620–760 0 0.27 Zinc and its alloys 50 25–180 240–550 65–5 0.27 Nonmetallic materials Ceramics 70–1000 — 140–2600 0 0.2 Diamond 820–1050 — 60,000 — 0.2 Glass and porcelain 70–80 — 140 0 0.24 Silicon carbide (SiC) 200–500 — 310–400 — 0.19 Silicon nitride (Si2N4) 280–310 — 160–580 — 0.26 Rubbers 0.01–0.1 — — — 0.5 Thermoplastics 1.4–3.4 — 7–80 1000–5 0.32–0.40 Thermoplastics, reinforced 2–50 — 20–120 10–1 0–0.5 Thermosets 3.5–17 — 35–170 0 0.34–0.5 Boron fibers 380 — 3500 0 0.27 Carbon fibers 275–415 — 2000–3000 0 0.21–0.28 Glass fibers 73–85 — 3500–4600 0 0.22–0.26 Kevlar fibers 62–117 — 2800 0 0.36 Spectra Fibers 73–100 — 2400–2800 3 0.46 Note: In the upper part of the table the lowest values for E, Y, and UTS and the highest values for elongation are for pure metals.
Details
-
File Typepdf
-
Upload Time-
-
Content LanguagesEnglish
-
Upload UserAnonymous/Not logged-in
-
File Pages32 Page
-
File Size-