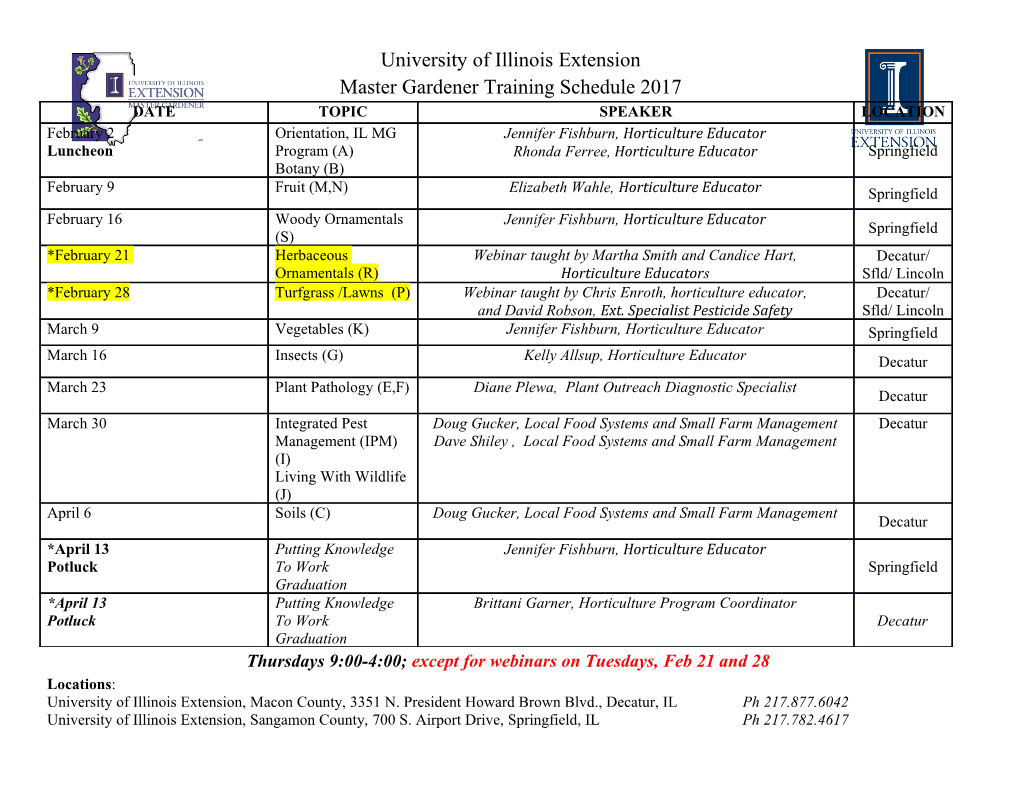
Heat Transfer Effects on the Processing — Structure Relationships of Polyetheretherketone (Peek) Based Composites* Chris N. Velisaris and James C. Seferis t Polymeric Composites Laboratory, Department of Chemical Engineering University of Washington, Seattle, Washington 98195 * Reprinted by permission of the Society of Plastics Engineers t Author to whom correspondence should be addressed ABSTRACT 1. INTRODUCTION An analytical methodology capable of describing Carbon fiber reinforced polymer composites are interrelations between thermal processing and polymer rapidly becoming popular alternatives to aluminum and structure for thermoplastic based composite laminates steel in applications that require materials of high was developed. Specifically, this modelling methodology strength with light weight. The carbon fiber reinforcement was used to describe experimental results generated with offers stiffness and strength, while the polymeric matrix a specially designed match die quench mold by processing offers interlaminar shear strength, solvent and damage both neat PEEK polymer and carbon fiber reinforced resistance as well as determines the long term durability laminate samples at different cooling rates. The developed of the composite system as a whole. High performance model accurately predicted temperature profiles for polymer composites have been traditionally made up PEEK laminates of different thicknesses under normal as of carbon fibers as the reinforcement and a high well as extreme quenching conditions of 114°C/sec. performance epoxy as the matrix. However, unmodified surface cooling rates that are possible to generate with epoxy matrices currently in use have several limitations. the quench mold. In general, the modelling methodology Among them are finite shelf life before processing, a is capable of predicting a part's thermal profile during tendency for brittle behavior when fully cured, and processing in terms of the composite's microscopic reprocessing limitations. In light of these difficulties, intrinsic properties (fiber and matrix), composition, and thermoplastic matrices such as Polyetheretherketone lamina orientation. Furthermore, by coupling to the (PEEK), as well as modified thermosetting polymers, are thermal profile description, a previously developed attracting attention, offering solutions to these specific crystallization kinetics model for PEEK polymer and its problems, as well as advantages for automated carbon reinforced composite, a quantitative description manufacturing. As is typical for all polymer systems of structural development during processing was obtained. however, properties such as stiffness, strength, solvent Thus, with this analytical methodology, a skin-core resistance, and toughness, depend on the polymer crystallinity profile, where the crystallinity varies with structure and consequently, the processing method used part-thickness as a result of uneven cooling experienced for that polymer. Accordingly, the development of a during processing, was predicted both for the neat PEEK methodology to characterize the processing-structure- polymer and its carbon reinforced laminate forms. property relationships of a composite system has been Finally, the developed methodology clearly established the central theme of our work, often referred to as the the interplay of both microscopic heat transfer and 'Trinity' of polymer composite usage evaluation /1, 2/. kinetics of crystallization/solidification of the matrix In order to extend development of our methodology to that must be accounted for in predicting the final high performance thermoplastic composite systems, we structure of a carbon fiber reinforced laminate that will, have chosen, for detailed investigations, carbon fiber in turn, govern microscopic and macroscopic reinforced PEEK as an appropriate model system /1 -11/. performance. A semicrystalline thermoplastic such as PEEK can be 13 Vol. 1, No. 1, 1988 Heat Transfer Effects on the Processing - Structure Relationships of Polyetheretherketone (Peek) Based Composites analyzed in terms of our two-phase methodology, where APC2, obtained from ICI were examined in this study the material is described in terms of anisotropic crystalline 119/. and noncrystalline phases that make up the polymer For our crystallization and heat transfer consideration, 112-18/. The addition of carbon fibers to a semicrystalline very little difference was evident in properties assumed polymer system can affect the crystallization kinetics of for PEEK polymer in its neat form and in the APC1 and the polymer and further influence the micromechanics APC2 composites if the proper volume fraction of of both phases /1, 3, 4, 7/. The intrinsic properties of reinforcement was accounted for /1, 3, 4/. Accordingly, the crystalline and noncrystalline phases of matrix and the composite samples will be generally referred to as reinforcement, along with their special arrangements PEEK/CF samples with the volume fraction of fibers that depend on the processing conditions, determine the specified at a nominal 60%. These materials were bulk properties of the composite /1-12/. Accordingly, an examined in terms of their processing-structure relation- important first step in understanding how composite ships through the preparation of neat PEEK resin and properties depend on processing conditions is to composite plaques in the quench match die mold /1, characterize this processing-structure relationship. 3-5/. The volume fraction crystallinity of the neat PEEK A high temperature quench match die mold for specimens processed at various cooling rates in the mold characterizing the processing-structure relationship of was measured with the Density Gradient Technique both neat PEEK and its carbon fiber reinforced (DGT) /I/. It is significant to note, however, that the composites was used extensively in this study /3-5, 10/. crystallization model was developed based on data This mold has capabilities of heating polymer surfaces to generated by differential scanning calorimetry (DSC) 450°C, and cooling those surfaces at rates up to /4, 7/. 120°C/second. In general, composite plaques with Neat PEEK resin plaques were prepared for the rectangular cross sections are formed in the mold. When crystallinity evaluation at cooling rates ranging from forming thick composite specimens at high surface 0.03 to 114°C/second, with a process melt temperature cooling rates through typical consolidation and of 375°C, where cooling rates were taken as the average lamination processes such as compression molding, a value between the approximate glass transition and melt skin-core phenomenon, where the matrix structure is temperatures of PEEK, 144 and 334° C, respectively dependent on the distance from the specimen surface, /19/. The specimens, prepared for skin-core cystallinity can become significant /1, 3, 4, 10). This effect is due to profile evaluation, were either 6 χ 2 χ 0.04 in. thick or 6 the small thermal diffusivity exhibited by thermoplastic χ 2 χ 0.16 in. thick. Specific details on the processing materials, which causes the specimen core to cool at a conditions employed are available elsewhere /3/. For all slower rate than the surface. Typically, a thick semi- samples, the degree of crystallinity reported here was crystalline polymer part quenched at the surface will determined with the DGT. For thin specimens, repre- have a noncrystalline skin and a high crystallinity core, sentative samples for DGT measurements were taken and, consequently, such processed parts display across the entire thickness of those specimens. For the properties that vary from the skin to the core /3/. The thick specimen DGT analysis, samples were cut from presence of carbon fibers can complicate this effect 0.02 inch surface, quarter-plane, and mid-plane plaque through reinforcement influences on the crystallization sections, where the plaque quarter-plane was defined as kinetics and on the bulk thermal diffusivity. In an effort the plane half way between the plaque surface and to characterize this effect, in this work, a heat transfer mid-plane. model was coupled with a nonisothermal crystallization In addition to the neat resin processing, unidirectional kinetics model to provide a generalized methodology for twelve-ply PEEK/CF laminates were consolidated in describing processing of carbon reinforced high order to analyze the heat transfer effects in forming performance thermoplastics, in general, and for PEEK operations. In a typical consolidation procedure, all plies specifically. were first tacked together. Next, the plies were heated from 25 to 375°C at 10°C/minute under contact 2. EXPERIMENTAL pressure and held at 375°C for 10 minutes at 150 psig pressure. Finally, the plaques were quenched at the The neat PEEK resin used in this study was obtained maximum mold cooling rate. For these specimens, the from Imperial Chemical Industries (ICI) as Grade 450P, temperature at the center of each plaque was monitored in powder form /19/. In addition, the carbon fiber as a function of time by the placement of a fine gauge reinforced PEEK (PEEK/CF) composite, both APC1 and thermocouple between the upper and lower 6 plies. 14 CJV. Velisaris and J.C. Seferis Science and Engineering of Composite Materials From the molding results, experimental data at high Physical Properties ' surface cooling rates indicated that the temperature χ-" Processing (.Temperatur* ^reilley profile at the mold surfaces could be approximated as C linear from the melt processing temperature
Details
-
File Typepdf
-
Upload Time-
-
Content LanguagesEnglish
-
Upload UserAnonymous/Not logged-in
-
File Pages10 Page
-
File Size-