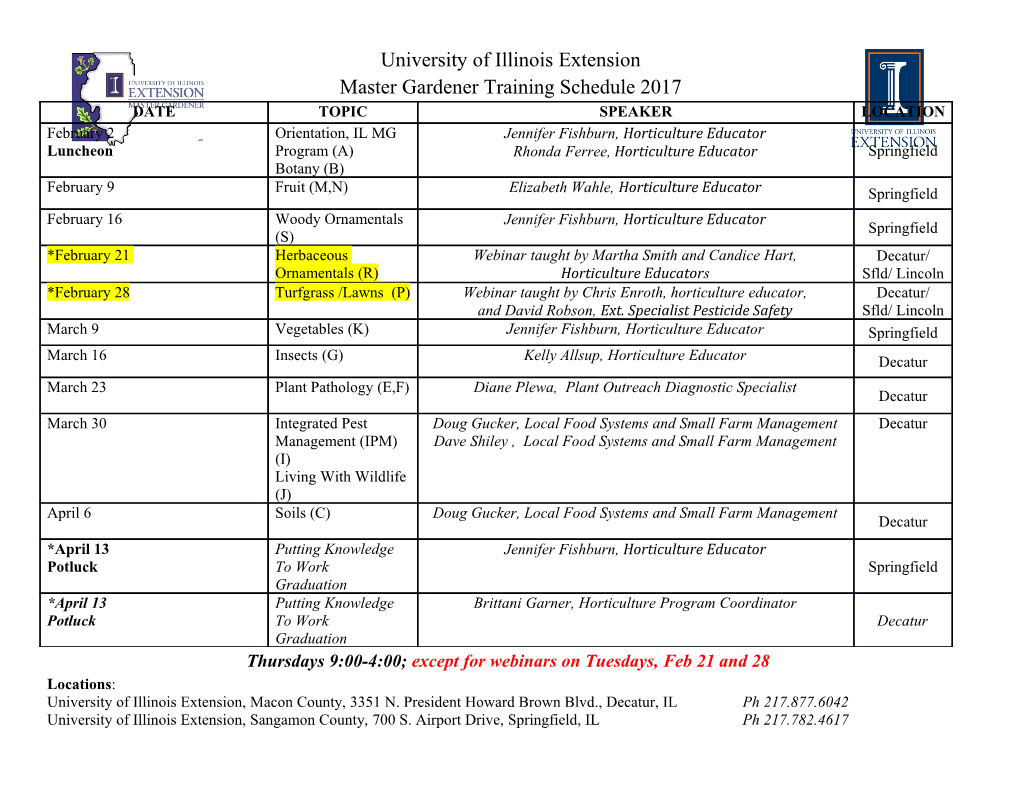
SAE TECHNICAL PAPER SERIES 983038 Investigation of a Ford 2.0 L Duratec for Touring Car Racing Pat Morgan, Ray Kach, Curt Hill, Dan Demitroff and Bruce Monroe Ford Motor Company Tom Dettloff, Wiley McCoy and Dean Battermann McLaren Engines, Inc. Reprinted From: 1998 Motorsports Engineering Conference Proceedings Volume 2: Engines and Drivetrains (P-340/2) Motorsports Engineering Conference and Exposition Dearborn, Michigan November 16-19, 1998 400 Commonwealth Drive, Warrendale, PA 15096-0001 U.S.A. Tel: (724) 776-4841 Fax: (724) 776-5760 The appearance of this ISSN code at the bottom of this page indicates SAE’s consent that copies of the paper may be made for personal or internal use of specific clients. This consent is given on the condition, however, that the copier pay a $7.00 per article copy fee through the Copyright Clearance Center, Inc. Operations Center, 222 Rosewood Drive, Danvers, MA 01923 for copying beyond that permitted by Sec- tions 107 or 108 of the U.S. Copyright Law. This consent does not extend to other kinds of copying such as copying for general distribution, for advertising or promotional purposes, for creating new collective works, or for resale. SAE routinely stocks printed papers for a period of three years following date of publication. Direct your orders to SAE Customer Sales and Satisfaction Department. Quantity reprint rates can be obtained from the Customer Sales and Satisfaction Department. To request permission to reprint a technical paper or permission to use copyrighted SAE publications in other works, contact the SAE Publications Group. All SAE papers, standards, and selected books are abstracted and indexed in the Global Mobility Database No part of this publication may be reproduced in any form, in an electronic retrieval system or otherwise, without the prior written permission of the publisher. ISSN 0148-7191 Copyright 1998 Society of Automotive Engineers, Inc. Positions and opinions advanced in this paper are those of the author(s) and not necessarily those of SAE. The author is solely responsible for the content of the paper. A process is available by which discussions will be printed with the paper if it is published in SAE Transactions. For permission to publish this paper in full or in part, contact the SAE Publications Group. Persons wishing to submit papers to be considered for presentation or publication through SAE should send the manuscript or a 300 word abstract of a proposed manuscript to: Secretary, Engineering Meetings Board, SAE. Printed in USA 983038 Investigation of a Ford 2.0 L Duratec for Touring Car Racing Pat Morgan, Ray Kach, Curt Hill, Dan Demitroff and Bruce Monroe Ford Motor Company Tom Dettloff, Wiley McCoy and Dean Battermann McLaren Engines, Inc. Copyright © 1998 Society of Automotive Engineers, Inc. ABSTRACT CAE tools, and the configurations generated were tested on both an air flow bench and dynamometer. A Super This paper summarizes an investigative study done to Flow 600 (3) air flow bench was used to collect the air evaluate the feasibility of a Ford Duratec engine in 2.0 L flow data. A Froude AG-250 HS dynamometer equipped Touring Car Racing. The investigative study began in with McLaren Engines data acquisition was used for early 1996 due to an interest by British Touring Car engine performance testing. The benchmark for our test- Championship and North American Touring Car Champi- ing was a current competitive V-6 (Figure1). Testing was onship sanctioning bodies to modify rules & demand the done in two phases each consisting of separate engine engine be production based in the vehicle entered for configurations. Problems for each of the two Phases competition. The current Ford Touring Car entry uses a encountered will be described. The North American Mazda based V-6. This Study was intended to determine Touring Car Championship regulations (2) were used as initial feasibility of using a 2.0 L Duratec V-6 based on the the parameters for engine design. A complete listing of production 2.5L Mondeo engine. Other benefits engine related rules are found in the appendix. expected from this study included; learning more about the Duratec engine at high speeds, technology exchange CORRECTED BENCHMARK POWER AND TORQUE CURVES between a production and racing application, and gaining 350 high performance engineering experience for production engineering personnel. 300 In order to begin the Duratec feasibility study, an initial 250 analytical study was done using Ford CAE tools. Addi- tional analytical work was done with respect to the basic 200 effects of bore, stroke, and per cylinder displacement on the air speed, filling capability, piston speed, and friction 150 of the engine. Benchmarking and other considerations CORRECTED TORQUE/H-P were given to surface to volume ratio, compression ratio 100 and combustion chamber shape, overall engine package, etc. 50 Cor. Torque Cor. H-P Though the resulting paper studies yielded a basic indi- 0 4500 5000 5500 6000 6500 7000 7500 8000 8500 9000 9500 cation that the Duratec engine would not be competitive RPM in 2.0L form for Touring Car Racing, many lessons were learned about the limits of the engine. This paper Figure 1. describes the results of the actual development program and their correlation to the analytical work. DEFINITION OF THE DURATEC ENGINE INTRODUCTION The Duratec V-6 is a 2.0 liter version of the 2.5 liter pro- duction V-6. The reduced displacement resulted from The objective of this paper is to document the study of changing the stroke from 79.5 mm to 62.4 mm. The Vee converting a Ford 2.5L Duratec V6 to a 2.0L for Touring angle is 60°. The engine is a 4 valve per cylinder, with 4 Car Championship competition. This paper will consider chain driven overhead cams. The oiling system is dry rules, (1,2) packaging and component design. The com- sump type. puter modeling of the engine was conducted using Ford’s 1 FOCAL POINTS MANDY INTAKE/EXHAUST FLOW SIMULATION-POWER OUTPUT 89MM BORE The following rules as taken from the Sanctioning Body 300 were to become the focus of the overall study. 250 1. Engine must be same make as the car (block and head). 200 2. Maximum capacity 2.0 liters. 150 3. The position and axis of the ports must remain as per BRAKE H-P original production. 100 4. The axis and angle of the valves must remain as per 50 original production. START FINAL 5. Port sizes may change, but the port centers at the 0 4500 5000 5500 6000 6500 7000 7500 8000 8500 9000 9500 manifold must remain the same +/- 2mm. RPM 6. Camshaft position and number must remain the Figure 2. same as per production, otherwise open. 7. 8500 rpm limited engine speed. PHASE 1 AIRFLOW vs. TARGET AIRFLOW @ 10" H20 Of these rules listed the most challenging was #4. The included valve angle of the Duratec engine is 50°. The 160 valve spacing is 38 mm. In addition to the rules the 140 benchmarked engine was 11.3 kg. lighter than the 120 Duratec. The first cut at the Duratec (with alternator) weighed 137 kg. 100 80 CFM APPROACH FOR PHASE I 60 Target Intake Airflow @ 10" H20 Phase 1 Average Intake Airflow @ 10" H20 The Production Ford Duratec V-6 engines come in two 40 Target Exhaust Airflow @ 10" H20 Phase 1 Average Exhaust Airflow @ 10" H20 displacements 2.5 liters and 3.0 liters, with bore sizes of 20 82.4 and 89.0 mm respectively. Ford’s CAE tools 0 MANDY (4) with its coupled dynamic optimizer (5) was 0 2 4 6 8 10 12 Lift in mm used to determine best bore size. However, the optimiza- tion showed no significant increase in peak power, and Figure 3. the optimizer would not move in any direction to improve the performance (Figure 2). The reason for this is the low Compression ratio was calculated at 11.15:1, due to mean piston speed 15.13m/s with the 89 mm bore, and chamber geometry the piston dome volume was maxi- the port velocities were too low. This meant that the mized at 12.2 ccs. This volume was achieved while response surface was very flat so that the program did maintaining a minimum piston to valve clearance of 1.5 not find any real direction to move to improve the perfor- mm. The shape and surfaces were irregular, and there- mance. Consequently, a bore size of 82.4 mm, the size fore, not optimum for both spark sensitivity or flame of the 2.5 liter V-6 Duratec engine, was chosen as the travel. Combustion chamber shape for Phase I was mean piston speed was 17.68m/s. Not very high, but still asymmetrical, this due to the stock 2.5 Duratec chamber. better than that with the 89 mm bore. Once the bore size Chamber volume for Phase 1 was 41.5 ccs. was decided, the corresponding stroke was calculated to Camshaft choice was based on competitive Benchmark achieve the proper 2.0 liter displacement. engine profiles (which operate a bucket style system). Cylinder head work concentrated on increasing air flow These profiles were converted into roller follower geome- (Figure 3). Baseline air flow tests were conducted at two try. The camshaft was a single pattern grind for both the different differential pressures 10” and 28” H20. Intake intake and exhaust. Roller finger followers were and exhaust port air flow targets were based on air flow machined out of billet to increase stiffness, durability, and information from the benchmark engine and MANDY pre- retained the ratio of 2:1.
Details
-
File Typepdf
-
Upload Time-
-
Content LanguagesEnglish
-
Upload UserAnonymous/Not logged-in
-
File Pages10 Page
-
File Size-