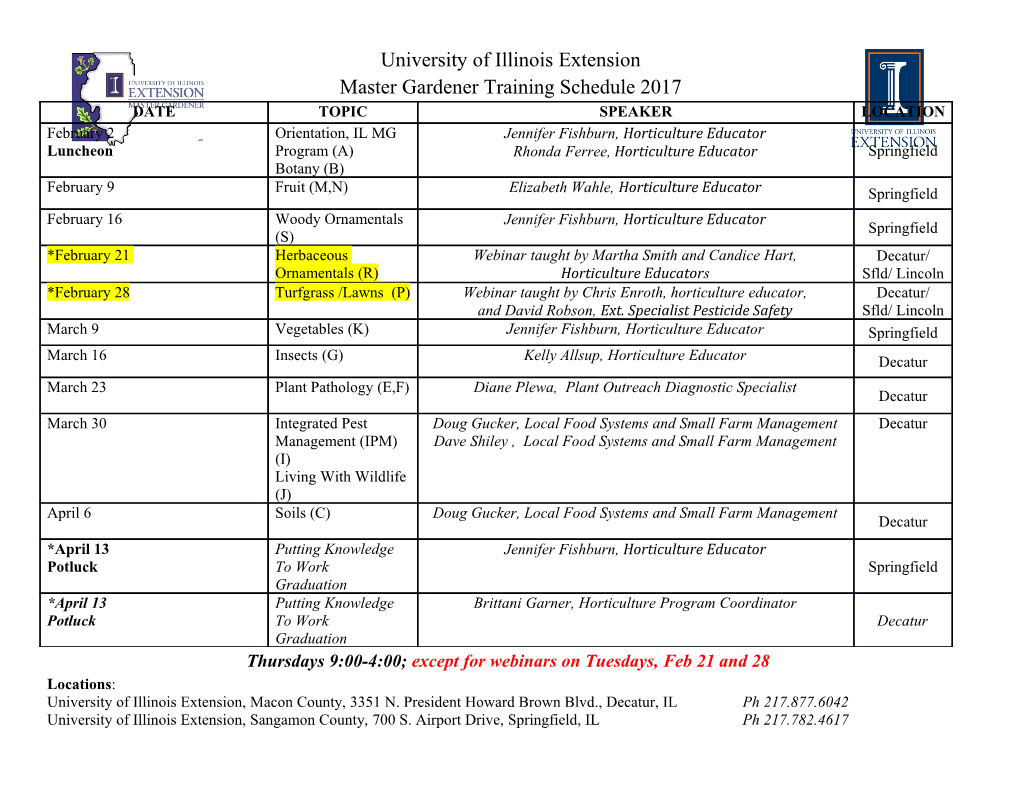
A different mirror.. can be controlled. Pulsed power output of layers are used to confine electrons and over 1 W has been demonstrated from a holes, while thicker layers serve as mirrors single array. Edge-emitters have delivered 10 or waveguides to confine photons. “Thin” is times that much, but their geometry restricts about 10 nm, and “thicker,” about 100 nm. them to one-dimensional arrays. After these layers are grown uniformly To be sure, engineering hurdles still loom across the full wafer, the next stage is to de- for surface-emitting lasers. The biggest is marcate individual laser devices with such the substantial elimination of the heat from standard fabrication processes as ion im- the light generation process. The other plantation or plasma etching. They may be emiconductor laser diode problems that must be resolved uiclude con- either separated for individual packaging or technology has at last gone trolling the light’s polarization and delivering left joined together to form an array. beyond the edge emission of the power in one mode. Rut since potential In surface-emitters, as with the edge- light. In that invention of the applications range over optical-fiber com- emitters, most of the pioneering work has early 196Os, photons shoot munications, printing and scanning, two-di- been done with heterostructures of indium out of one edge of the semi- mensional image recognition. and com- gallium arsenide and aluminum gallium ar- conductor wafer after re- puting, the debices are moving rapidly from senide alloys. Those 111-V materials are bounding off mirrors that research into manufacturing. ideal for complex surface-emitter devices. have been literally cleaved ATOMIC LAYERING. The surface-emitting The ciystal lattice of AlGaAs matches the out of the ci-ystalline substrate. In the new laser’s entire structure-mirrors and all- spacing of the lattice of gallium arsenide surface-emitting laser, though, photons is built up by “spray painting” crystalline substrates, so it can he grown epitaxially on bounce vertically between mirrors grown layers onto a substrate with atomic pre- GaAs wafers without fear of crystal defects into the structure, and then shoot straight cision. By means of techniques such as mol- and dislocations.Although InGaAs materials up (or down) from the wafer’s surface. ecular beam epitaxy and metal-organic are not naturally lattice-matched, they can ‘Those differences seem simple, but their po- vapor phase epitaxy, hundreds of layers of be grown on GaAs substrates if the layers tential consequences for manufacturing effi- semiconductor materials can he grown one are kept thin-and the elastic strain im- ciency and new applications are tremendous. on top of the other. By mixing and matching parted to the thin layers has beneficial elec- Most critically, laser devices that emit the tnaterials to create “designer” alloys, it tronic properties. With in situ diagnostics, light from their upper surface can be fah- is possible to grow a crystalline structure tolerances can be tightly controlled, and ricated side by side on a wafer in vast with all the electrical and optical properties processing technologies such as ion implan- numbers. Tens of millions can fit on a 100- desired for its various parts. tation and etching are well understood. millimeter-diameter wafer. Packing them in This method of tailoring semiconductor Finally, 111-V heterostructures give laser so densely enhances manufacturing effi- structures is called handgap engineering diodes their lowest lasing thresholds and ciency. Even more important, the way they [see “Quantum-tailored solid-state devices,” hest temperature characteristics. are made means they can be integrated on by Titnothy J. Drummond, Paul L. Gourley, STRUCTURAL DIFFERENCE. In the surface- chip with transistors and other devices. and ’Thomas E. Zipperian, IEEE Spectrum,, emitter, the semiconductor laser structure There is no need to wire each of them indi- June 1988, pp. 33-371. In essence, thin is swiveled by 90 degrees from the orien- vidually to a circuit, as is done with edge- emitters, and they can even be optically Index of refraction: the ratio of the speed of linked to overhead elements. ~ Defining terms Coupling efficiency also benefits from a ~ light in a vacuum to its speed in a material surface-emitting geometry. The beam of Band gap energy: the minimum energy longitudinal optical modes: discrete optical light that issues from an edge-emitter, typ- required to break a valence electron from a crys- resonances occurring in a semiconductor laser ically through a 1-by-2-pm aperture, is tal bond and set it loose in the crystal lattice as a when twice the cavity length (distance between usually both elliptical and divergent-not at mobile carrier. mirrors) corresponds to an exact multiple of the all the round, collimated beam that couples Edge-emitting laser: the conventional semi- photon wavelength its entire energy into an optical fiber. In conductor laser, in which the gain medium is Quantum well: a thin layer of material of com- contrast, the surface-emitter aperture can grown epitaxially on a substrate and the two mir- paratively narrow band gap sandwiched between he shaped to give the beam the ideal rors are formed by cleaving the resulting structure wider-band-gap layers for the purpose of trap- ~ circular cross section and its diameter can to expose reflective crystal facets. Light generated ping mobile carriers and confining them quantum- be made large enough, at 5 pm, to minimize in the gain medium bounces horizontally between mechanically i the divergence of the light rays. the facet mirrors (there is usually some lateral Vertical-cavity surface-emitting laser: a ~ Last, if left attached together on the wafer, confinement), and some leaks out through one solid-state laser in which the two mirrors as well ’ surface-emitting lasers can form a two-di- mirror to become the laser beam. as the intervening gain region are grown epitaxi- ~ mensional array whose power and direction Epitaxy: the growth of crystal by depositing ally on a semiconductor substrate Light gener- atoms on a substrate a single layer at a time by ated in the gain region bounces vertically ~ Paul L Gourley, Kevin L Lear, arid techniques employing molecular beams or between the mirrors, and some leaks through the Richard P Schneider Jr gaseous chemicals, top surface mirror to form the emitted beam , Sandia National Laboratories 001 8-923.i/94/S4.00 :‘1994lEEE 31 tation of a cleaved-cavity edge-emitter. The laser light does not travel horizontally within a single layer inside the wafer, but instead bounces vertically through the epi- taxial layers between mirrors grown above and below the active layer. Because the active layer is only 10 pm thick, the length of the cavity between the mirrors is less than 10 ym-extremely short in com- parison with the 100 pm or more of the edge-emitter’s cavity. The mirrors in a surface-emitter are grown into the laser structure itself. Each is composed of paired layers of two dif- ferent materials, such as GaAs and AIAs: In this scanning electron micrograph, the “checkerboard”is in ac- one material has a high index of refraction tuality a two-dimensional phased-locked array of vertical-cavity and the other a low index. (The index of re- surface-emitting lasers. Molecular beam epitaxy was employed to fraction is the ratio of the speed of light in a grow the semiconductor wafer, complete with mirrors [light and vacuum to the speed of light in the ma- dark stripes], and the result was topped by a thick phase-shift layer terial.) Because the light waves from suc- [solid light layerl. Then reactive ion beam etching was used to cessive layers interfere constructively, to- define each laser individually as a square, measuring 5 ,um on a gether, the pairs of layers can reflect more side, and the thick phase-shift layer was etched off the top of every than 99 percent of the photons at the laser’s other laser in the array. The inset is an optical micrograph of light emission wavelength. emitted from the operating array, The mirrors are known as quarter-wave stacks because each layer’s thickness is equal tiplies rapidly, and some of the photons leak While he!ium-neon gas lasers of the type to one-quarter of the wavelength of the light out through the circular aperture in the used in supermarket bar-code scanners are inside the material. The wavelength there is contact on one mirror, producing an intense approximately 0.01 percent efficient, com- shorter than it is in a vacuum by a ratio equal beam of coherent light. mercial laser diodes are 30 percent efficient to the refractive index. For example, the re A COMPARATIVE CINCH. With today’s precise or better. fractive indices of GaAs and AlAs are 3.5 and epitaxial technology, surface-emitters are One serious obstacle to high efficiency in 2.9, respectively, at the emission wavelength expected to be much faster and simpler to surface-emitters, however, is high series re- of 980 nm, so that the respective layers need make in high volume than conventional sistance to the charge carriers (electrons to be 70 nm and 84 nm thick to create an ef- edge-emitting lasers can be. They need less and holes) transported through the laser fective mirror. special handling, above all because the mirrors. The high resistance reduces the On the top surface of the surface-emitter mirrors are an integral part of the laser’s efiiciency and generates unwanted and the underside of the substrate, metal is structure. (In contrast, the cleaved-facet heat, which limits the number of devices deposited to form electronic contacts.
Details
-
File Typepdf
-
Upload Time-
-
Content LanguagesEnglish
-
Upload UserAnonymous/Not logged-in
-
File Pages5 Page
-
File Size-